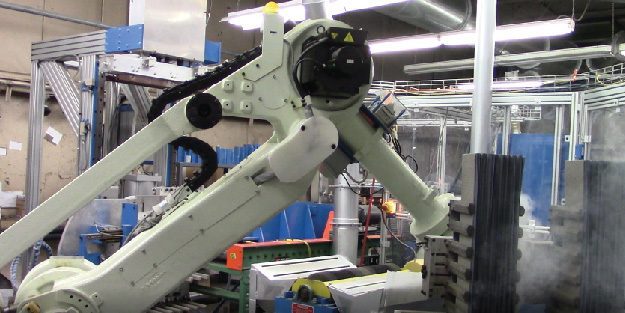
- IndústriasEletrónica
- AplicaçãoMontagem, Manutenção de máquinas
- Série de RobôZX series
VISÃO GERAL
Os fabricantes utilizam a automatização para levar as suas operações para o nível seguinte. Quer se trate de aumentar o rendimento ou de diminuir os custos de mão de obra, a automatização robótica dá às empresas de todas as dimensões a oportunidade de expandir o seu negócio. Podem também eliminar pontos problemáticos nos seus processos, o que, muitas vezes, tem um efeito cascata de benefícios imprevistos em toda a organização.
A Battery Builders, LLC. (BBI), é um fabricante de baterias industriais de chumbo-ácido sediado em Naperville, IL. Quando decidiram atualizar as suas instalações, parecia óbvio incluir a sua máquina COS (Cast-On-Strap) de seis estações na atualização. Eles trabalharam com o integrador robótico MAC Engineering de Benton Harbor, MI para instalar um robô Kawasaki de grande carga útil dentro de uma célula robótica de 6 estações. Quase imediatamente após a instalação, a Battery Builders viu um produto mais consistente – um benefício imprevisto que teve um enorme impacto no seu negócio.
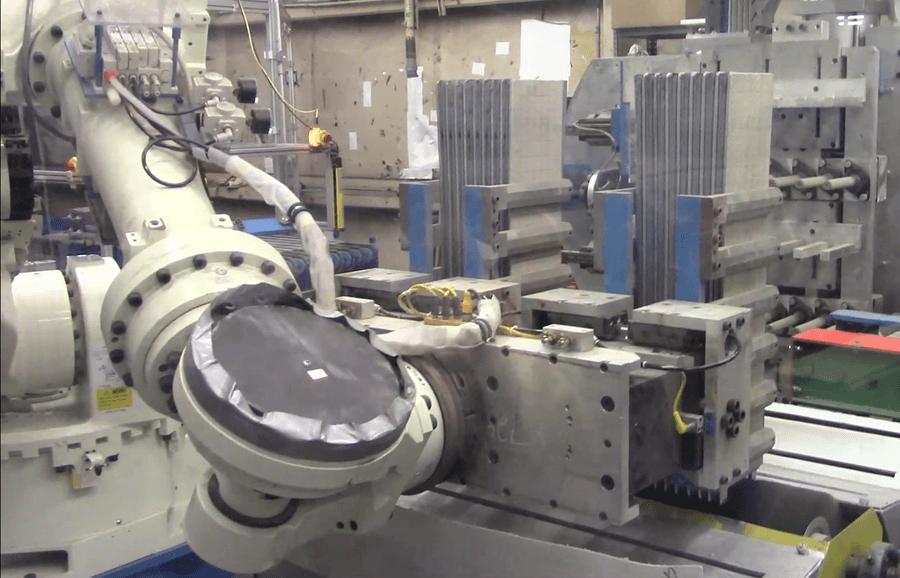
DESAFIOS
- Necessidade de um robot preciso e versátil para trabalhar com vários tipos de máquinas
- Diminuir o número de operadores necessários
- Necessidade de aumentar o rendimento e a qualidade do produto
O robot tinha de ter uma carga útil elevada e uma elevada repetibilidade para levantar e alinhar as placas da bateria com precisão. A BBI também precisava de poder confiar no seu robô e no equipamento periférico para cumprir os objectivos de produção. A empresa propôs-se a processar 1.000 células de bateria por dia – mais do dobro da sua produção diária – utilizando menos mão de obra.
Top of Mind: Fiabilidade
A BBI era afetada por avarias frequentes da sua máquina COS de funcionamento manual, que possuía há mais de 25 anos. A máquina antiquada estava a causar atrasos dispendiosos na produção – a BBI tinha quatro a cinco horas de inatividade por semana.
Riscos de saúde e segurança
O manuseamento manual de placas de bateria gera mais pó de chumbo no ar do que um processo automatizado, o que representa um maior risco de exposição. A máquina mais antiga também exigia que os funcionários levantassem cargas mais pesadas, resultando num maior risco de lesões. Para a BBI, era importante ver o impacto positivo da automatização refletido no seu ambiente de trabalho – e não apenas no seu resultado final.
Um robô, seis estações
A BBI tinha de instalar um robot suficientemente preciso para alinhar consistentemente 300 lbs. de placas de bateria até 500 vezes por dia. O robô também tinha de ser capaz de escovar os conectores das extremidades das baterias, mergulhá-las em chumbo fundido e embalá-las num frasco de plástico, entre outras tarefas. Para realizar esta lista diversificada de tarefas pormenorizadas, era necessário um robô versátil.
Simplificar as operações e redistribuir os funcionários
Um dos principais objectivos do fabricante era aumentar a eficiência global da fábrica e aumentar o número de produção de células de bateria. O antigo processo COS que eles pretendiam automatizar exigia nove ou 10 funcionários para operar, e eles estavam a tentar diminuir esse número. A BBI também reconheceu que os seus funcionários poderiam ser mais úteis noutras áreas da fábrica.
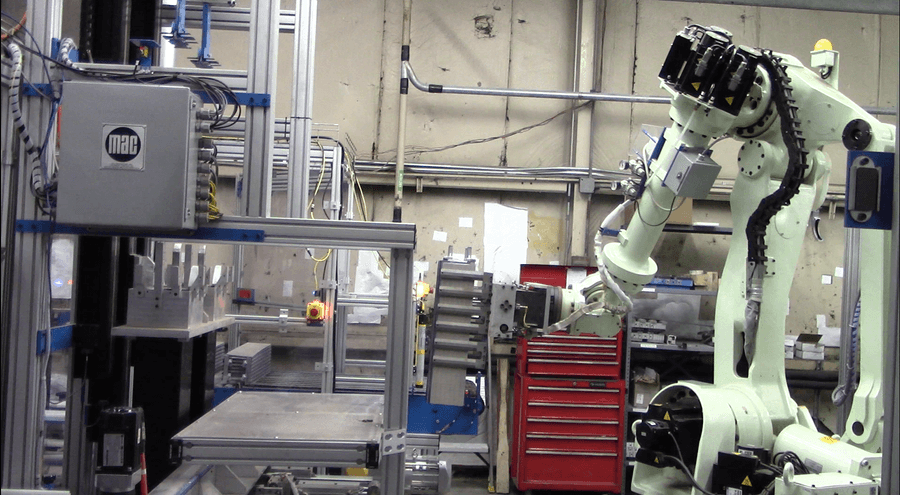
SOLUÇÃO
- Um robot move o produto através de todo o processo COS de seis estações
- O número de operadores necessários para gerir este processo diminuiu de sete para cinco
Quase imediatamente, a Battery Builders viu as vantagens do seu novo robot Kawasaki reflectidas na qualidade do seu produto final.
O número de trabalhadores necessários para executar este processo diminuiu de sete para cinco. O robot entra em ação depois de as placas de bateria terem sido colocadas manualmente no transportador para alinhar as placas e garantir que estão uniformes e niveladas. Durante este novo processo, os operadores já não têm de levantar as placas do chão. Movem as placas lateralmente para um transportador, o que é um movimento mais ergonómico.
O robot recolhe as placas e passa-as por uma escova de cerdas para remover quaisquer detritos dos conectores das extremidades. De seguida, o robô passa o produto por um processo de fluxo. Os conectores de extremidade são mergulhados em estanho e novamente em chumbo fundido. Por último, vem o processo de encaixe, em que o robô coloca as placas da bateria na respectiva caixa de plástico.
Os robots ZX300S da Kawasaki podem transportar cargas úteis até 300 kg. Combinam um braço de longo alcance com uma quantidade mínima de espaço morto para uma ampla área de trabalho. Têm também uma elevada repetibilidade de ±0,3 mm, o que os torna ideais para aplicações que requerem precisão e elevação pesada. Quando combinadas, estas caraterísticas criaram a solução perfeita para a BBI, que necessitava de um robot para alcançar máquinas em alturas variáveis.
Os mais recentes robots de grande carga útil da Kawasaki, a série BX, têm uma repetibilidade ainda maior, variando entre ±0,06 e ±0,08 mm. Possuem uma estrutura de braço oca, que permite a preparação interna do robot. Esta caraterística permite uma instalação e manutenção fáceis e um desgaste minimizado.
RESULTADOS
- Um robô de grande carga útil cobre o processo COS de seis estações
- Diminuição do risco de exposição dos trabalhadores a poeiras de chumbo em suspensão no ar
- A qualidade e a consistência do produto aumentaram significativamente
- O rendimento aumentará em 150%
Para a BBI, trabalhar com o seu novo robot tem sido fácil. “A parte robótica deste processo foi muito fácil. Instalar o robô não foi um problema, foi muito simples, e aprender a trabalhar com ele não foi muito complexo,” disse o Diretor Assistente da BBI.
Desde que substituiu a máquina COS, a BBI registou uma melhor qualidade do produto utilizando menos horas de trabalho, ao mesmo tempo que criou um ambiente de trabalho mais seguro. Os funcionários que operavam a máquina antiga estão agora a trabalhar no departamento de montagem de baterias, o que permite à BBI dedicar mais horas-homem às fases finais da montagem de baterias. Estas mudanças acabam por melhorar a qualidade das suas baterias. Quando toda a integração estiver concluída, será possível aumentar a produção de 400 para 1000 células de bateria por dia – mais do dobro da produção registada antes da automatização.