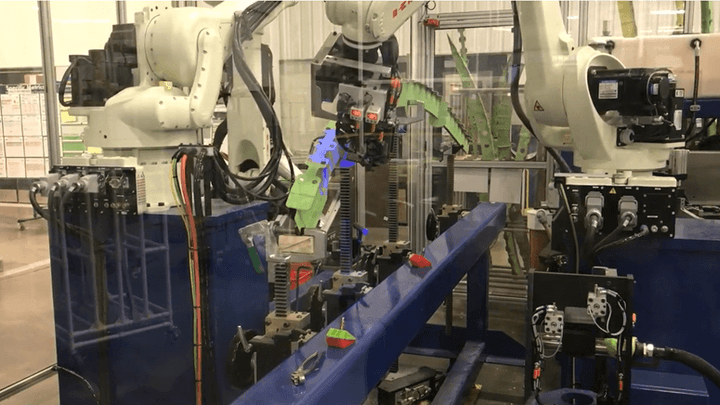
- IndústriasAeroespacial
- AplicaçãoMontagem, Selagem / Distribuição
- Série de RobôR series
Sistema concebido por:
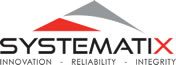
VISÃO GERAL
Ao contrário de muitos dos sectores de produção actuais, a indústria aeroespacial tende a manter-se afastada da automação. Os braços robóticos são uma visão rara nesta indústria devido aos baixos volumes de produção e às peças altamente especializadas. Apesar disso, o fornecedor de peças aeroespaciais associou-se ao integrador SYSTEMATIX, com sede no Ontário, para conceber uma célula de montagem robótica complexa guiada por visão para a instalação de placas de porca.
As placas de porca são uma peça irregular com mais de 200 variações utilizadas para segurar o revestimento exterior do avião à estrutura. Embora esta aplicação complexa não pareça necessariamente um candidato ideal para a automatização, a SYSTEMATIX pensou de forma diferente. Os robots Kawasaki repetíveis e os produtos de montagem guiados por visão 3D reduziram os tempos de ciclo, aumentaram a consistência do produto e reduziram a mão de obra.
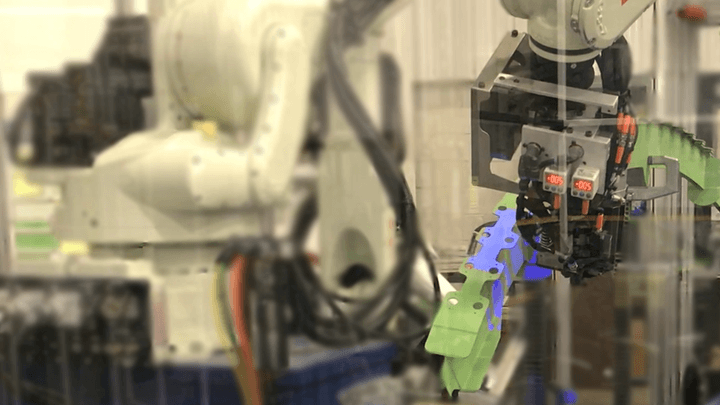
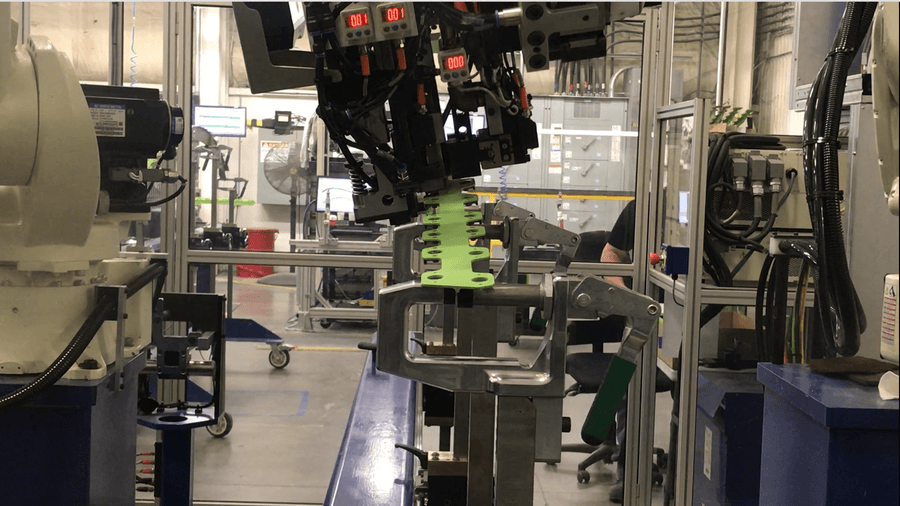
DESAFIOS
Uma aplicação difícil e fastidiosa
Foram várias as razões que levaram o cliente a escolher o processo de automatização da instalação de placas de porcas. Para cumprir os rigorosos requisitos de qualidade, todos os funcionários tinham de receber formação intensiva e certificação para cada peça. Tinham também de documentar o seu trabalho em tempo real. Este facto, combinado com a natureza monótona do processo de instalação de placas de porcas, criou problemas de retenção para o fabricante.
Controlo de qualidade
Devido ao papel integral que a placa de porca desempenha na construção de aeronaves, as alturas dos rebites da placa de porca têm de ser exactas. Antes da automatização, os operadores humanos tinham de raspar os rebites até à altura exacta necessária – um processo fastidioso e sensível ao tempo.
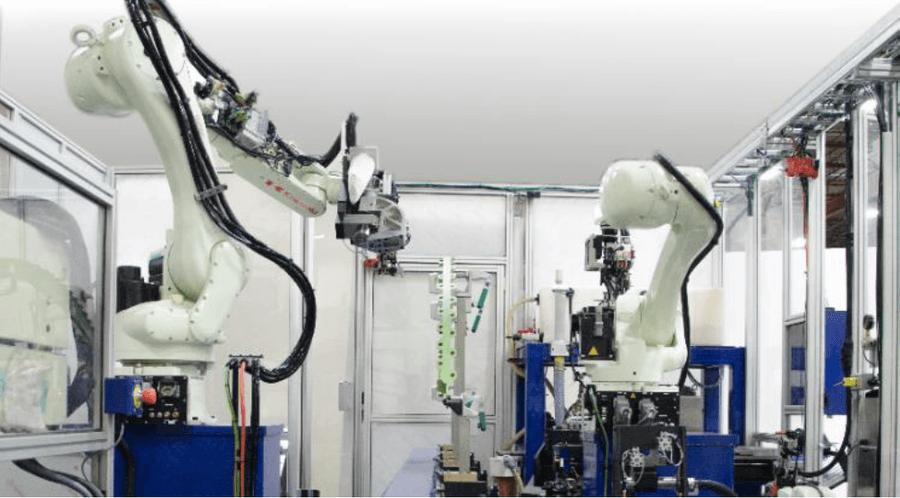
SOLUÇÕES
- Três modelos diferentes de robots da série R da Kawasaki instalados na célula de montagem guiada por visão
- O software de imagem Matrox e os localizadores LMI identificam corretamente 225 tipos de peças
O processo
Em primeiro lugar, um Kawasaki RS080N determina a posição da peça através da leitura de três caraterísticas distintas da peça utilizando a visão 3D e ajustando-a em conformidade. Após o alinhamento, a ferramenta de fim-de-braço (EOAT) da cabeça de perfuração do robot agarra a peça, perfura e rebaixa dois furos de rebite para a instalação da placa de porca.
Em seguida, o RS080N roda o braço para retirar os rebites corretos de entre quatro comprimentos possíveis e num de dois passos específicos, a partir da ferramenta de deslizamento de rebites. Enquanto o RS080N recupera os rebites, o robô RS010L apanha uma placa de porcas e utiliza câmaras de visão para verificar se está correta de entre 28 tipos possíveis. A partir daqui, o robot coloca o rebite na ferramenta de localização da placa de porca. As câmaras efectuam uma verificação de visão antes de colocar a placa de porca na ferramenta para garantir que está livre para receber uma nova placa de porca.
O robot coloca então a placa de porca numa mesa giratória para que o robot RS005N possa aplicar o selante – um requisito do cliente para garantir a resistência à corrosão. O robot RS005N efectua duas verificações de visão nesta fase do processo: uma antes da aplicação do selante e outra depois, para garantir uma aplicação correta.
A partir daqui, o prato giratório roda para que o RS010L possa recolher o pacote completo de ferramentas, que inclui a placa de porca e a ferramenta de colocação da placa de porca. O robot RS010L examina as três caraterísticas da peça para assegurar o alinhamento correto do plano de instalação. De seguida, agarra a peça na caraterística definida. Enquanto o robô RS010L mantém a peça no lugar, o robô RS080N entra na área e as duas cabeças casam-se. De seguida, a cabeça de aspiração de rebites do robot RS080N coloca rebites no interior da cabeça do robot RS010L, que instala os rebites na peça.
Após a instalação dos rebites, as cabeças dos robots separam-se. O RS010L liberta a peça em segurança e roda para deixar cair as ferramentas sujas, e o RS080N roda o EOAT para a posição correta para a cravação dos rebites, o que completa o processo de 39 segundos.
Visão, precisão e velocidade
Ao longo deste complexo processo, é provável que tenha notado um tema comum: a importância da visão 3D. O software de imagem Matrox e os localizadores LMI desempenham um papel vital na identificação de 225 estilos de peças e 28 configurações diferentes de placas de porca possíveis – todas elas podem ser instaladas em dois passos diferentes.
O fornecedor escolheu os robôs Kawasaki devido à linguagem de programação de arquitetura aberta e à capacidade de lidar com processos mais avançados. “Uma das razões pelas quais gosto da Kawasaki é a facilidade de trabalhar com os programas, especialmente com a linguagem AS”, afirmou o chefe de projeto P.J.. “É uma das razões pelas quais utilizamos a Kawasaki”.
Um dos aspectos únicos desta aplicação é a proximidade com que os robots trabalham em conjunto. As cabeças do RS080N e do RS010L têm de se ligar sem colidir – uma ação que é impossível sem robôs altamente repetíveis. A série R de robots de uso geral da Kawasaki cumpre este critério, com uma repetibilidade que varia entre ±0,02 mm e ±0,06 mm à medida que a carga útil aumenta (3 kg a 80 kg). “Os braços são muito robustos; não se deslocam”, afirmou P.J.. “Os braços têm de se deslocar para um posicionamento muito exato, e não tivemos um único problema com isso. São muito precisos”.
RESULTADOS
- Tempo de ciclo reduzido em 26 segundos
- 97% de consistência alcançada
- Número de operadores reduzido de três para um
- A célula cria uma peça totalmente concluída – não são necessárias estações de trabalho em curso
Desde a instalação, o fornecedor tem experimentado os benefícios da automação em primeira mão. Algumas das vantagens incluem tempos de ciclo drasticamente mais curtos, maior consistência do produto e menos mão de obra, o que os ajudou a atingir os objectivos de redução de custos e aumento da produção que definiram desde o início.
Mas quando lhes perguntaram onde viram a maior melhoria, P.J. citou a consistência sem hesitação. Depois de estar em produção há pouco mais de um ano, a célula praticamente eliminou as inconsistências das peças. Atingiram 97% de consistência – uma estatística que afecta grandemente os seus resultados através da poupança de custos e de tempo.