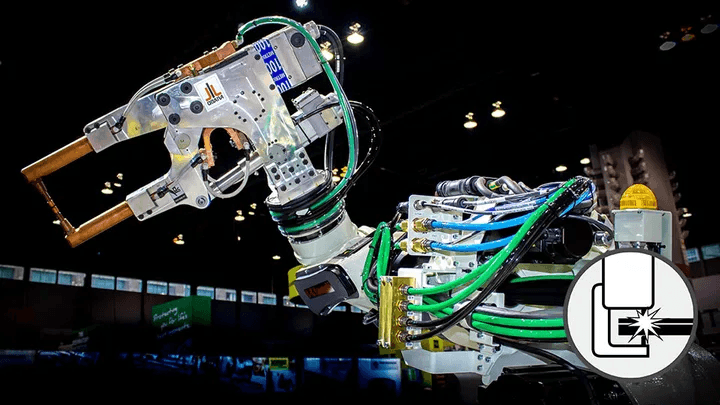
NEDSÆTNING AF CYKLETID MED 20% MED STØRRE STEDKONTROL
Spot welding is a resistance welding process that uses large electrical current to join two or more sheets of metal in a single location. Spot welding technology has evolved through its extensive use in automobile manufacturing using articulated robots. Kawasaki is pushing the envelope by developing spot welding automation that offers through arm cable routing, reduces cycle time, allows greater control, and reduces cost.
Kawasaki robots use an additional servo motor with a high resolution encoder to precisely control the motion of a spot welding gun. The Kawasaki spot welding software accurately controls the position, acceleration, and force of the gun. The position control and force calibration allow for different thicknesses and types of material to be welded. Kawasaki's advanced servo gun software optimizes the gun motion profile which results in an average cycle time reduction of 20%.
Kawasaki's experience with industry-leading spot welding technology can help you increase product quality, reduce production cycle time, or design and build a custom turnkey spot welding solution.
Robotter til Punkt svejsning
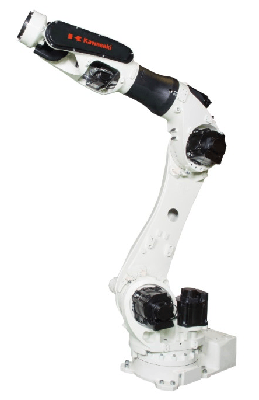
Store robotter op til 300 kg nyttelast
Store almene robotter med en nyttelastkapacitet fra 100 til 300 kg.