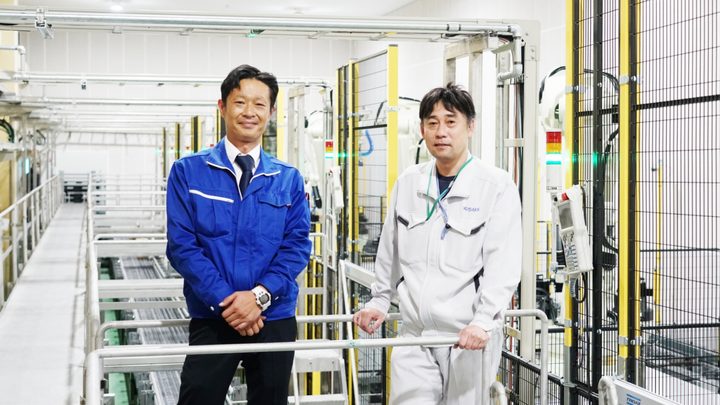
- BrancherMad og drikke, Logistik
- AnsøgningerPalletering
- Robot SerieCP-serien
Robot user: Kasugai Seika Co., Ltd.
System integrator: Ryowa Electric Co., Ltd.
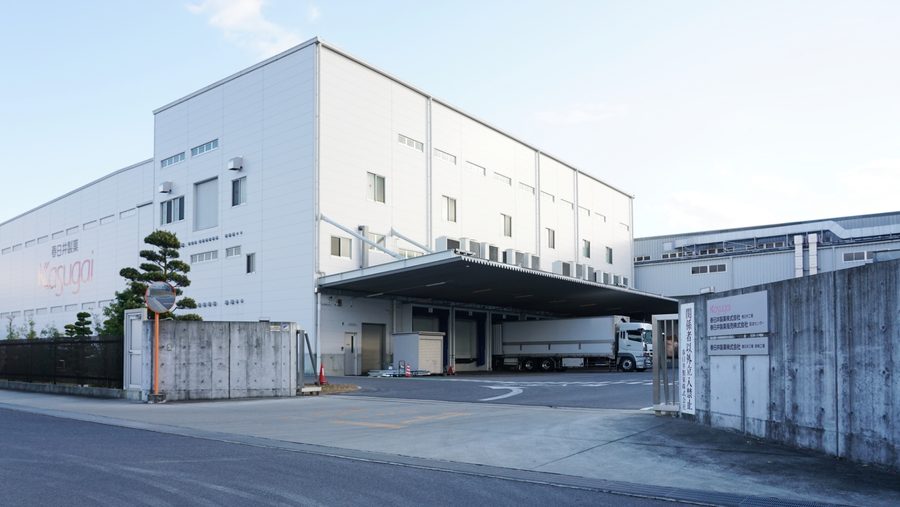
春日井製菓株式会社は、1928(昭和3)年に愛知県名古屋市で創業した老舗の菓子メーカーです。「おいしくて、安心して多くの人々に愛され続けるお菓子」を届け続けて90年余り。同社工場からは豆菓子、金平糖、グミ、キャンディ、ラムネなど幅広い年齢層に愛される菓子が毎日送り出されています。その出荷プロセスをより効率的で正確なものとするべく、ロボットを使った自動パレタイズシステムの導入が進められています。
Introduction background/issues:
Integration of the automation system from the production area to logistics
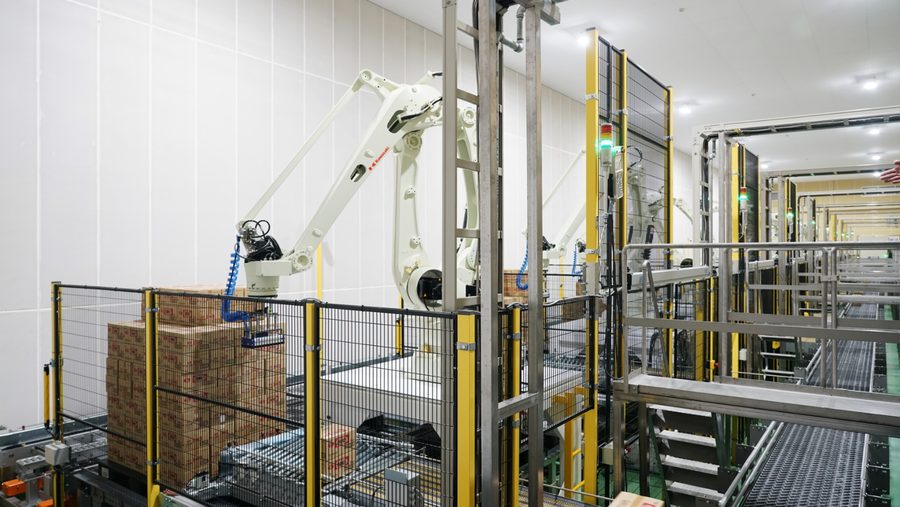
After stacking cardboard boxes to the specification, they are wrapped with film on a stretch wrapping machine to prevent the load collapsing and then carried into the automated warehouse.
The Kasugai Factory is located near to the Manai Station on the Meitetsu Komaki Line. It is the main factory of Kasugai Seika, and accounts for around 80% of the total production of the company.
There are two factories A and B next to each other, with Factory A producing candy and Factory B producing gummy candy and pea and bean candy.
More than half of the employees of the company work at the Kasugai Factory, where the trend toward automation accelerated around ten years ago.
Automation using dedicated machinery for mostly packaging equipment was started from around 2010, when the new Factory B was planned to be built due to expanding the product items.
After that, when starting the reconstruction of the distribution center, there was an active discussion. “If we rebuild it, let’s make it something more efficient”, and the planning began.
Factory Manager Kohei Hatano of Kasugai Seika, Kasugai Factory B says that, “It was the time when automated warehouses were starting to spread, so we decided to introduce one too.”
In 2018, an automated warehouse was completed that manages the history of items entered and retrieved from the warehouse, and the inventory in a system, and performs the delivery of items to a cargo handling area where products sorted per delivery destination are temporarily stored.
In parallel with this, the carry-in flow for the products stored in that automated warehouse was revised to integrate everything from the production area to the logistics.
Then, after a three-year preparation period, the automated palletizing system using a robot started operations from March 2020.
Introduction effects/solutions:
Flexible response to increases/decreases and changes in the various products handled
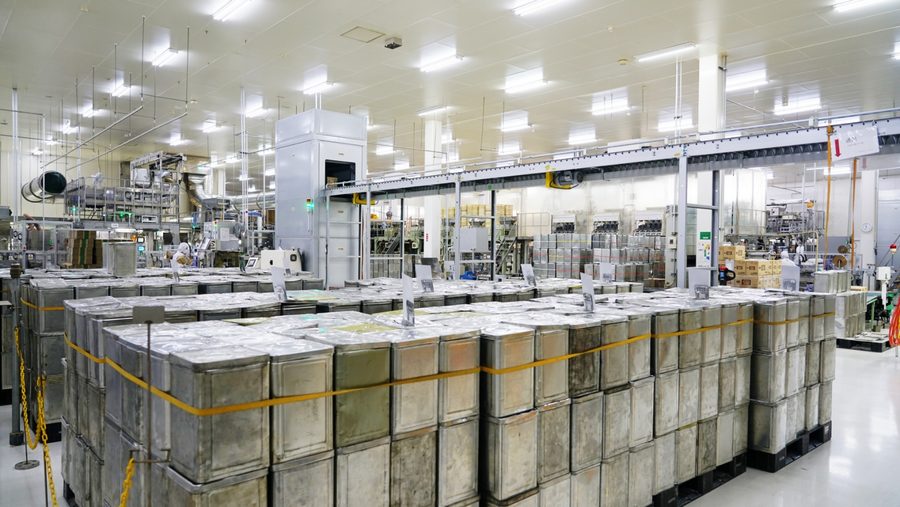
The cardboard boxes filled with confectionery are placed on an elevator and transported to the neighboring palletizing area by a conveyor.
The total coordination of the automated palletizing system was performed by Ryowa Electric Co., Ltd., the system integrator.
The robots installed were the Kawasaki palletizing robots CP180L’s.
This full automation is achieve by the following processes: the products packed in cardboard boxes in the production area are transported to the palletizing area on a belt conveyor, the cardboard boxes are stacked flat on a pallet and are wrapped around by film to prevent the boxes from collapsing, then they are transferred into the automated warehouse.
The Kasugai Factory produces 14 different products.
Department Manager Shigetaka Nakamura of the Production Engineering Department at Kasugai Seika says that, “Of those products, we decided to start from the three pea and bean candies that are the main products of our company.
At the present, each product is allotted to one of three palletizing robots.”
The processes up to (1) packaging, (2) packing in boxes, and (3) adhesion process (a process where two cardboard boxes are joined together with adhesive.
At Kasugai Seika, two boxes stacked together are called one case.) had already been automated using dedicated machinery.
In the introduction of this new automated system, belt conveyors connecting to the palletizing area were installed after step (3).
First, a QR code is printed on the case containing two boxes for product management by an industrial-use inkjet printer. It is then lifted up by a vertical conveyor and sent to one of the three belt conveyors to the neighboring palletizing area.
Three to four cases per minute are carried in.
At the joining point along the route, a sensor and stopper control are used to prevent the boxes colliding with each other.
In the palletizing area, the QR code for each case is read on the belt conveyor. Then, the system identifies which of the three palletizing robots the box should be sent to.
The belt conveyor leading to the palletizing robots has ball rollers and a sorter to slide the cargo in one direction.
When the cases get close to the draw-in route where the robot and pallet are located, the cases are sent from the belt conveyor to the automated palletizing system without slowdown.
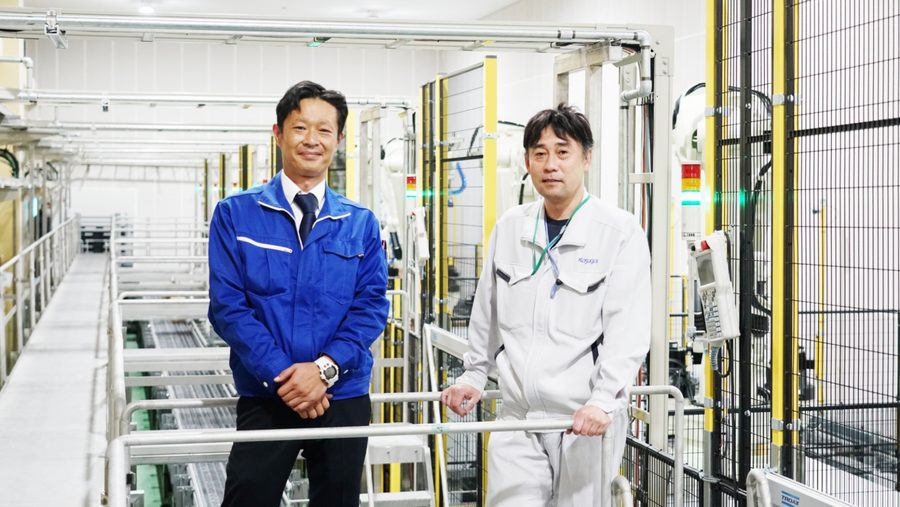
The cases carried into the palletizing system are checked again using the QR code to confirm that they have not been sent to the wrong location.
If they are correct, the CP180L robot performs flat stacking. This is the series of operation.
Division Manager Tadaaki Kuroiwa of the FA Robot System Division of Ryowa Electric explains that, “The robot hand is equipped with a vacuum gripper.
It has a check valve, so even if one of the vacuum pads does not contact the workpiece, the overall vacuum pressure is adjusted so that the workpiece can be firmly transported.
Therefore, even if the size of the case is different, it is not necessary to change the hand.”
The reason for selecting the CP180L was its processing speed.
Mr. Nakamura says that, “The most important thing is to be able to cope with our production speed.
At the time of the automation system design, the CP series palletizing robot had the fastest processing speed in the industry.”
At present, 1,700 cases come off each line per day and the three robots each stack around 20 pallets per day.
The application needs a short tact time and installation space is limited, so it was necessary to perform advance verification work carefully.
Mr. Kuroiwa explains that, “The Kawasaki robot simulation software K-ROSET was used to render the design drawings in 3D to reconstruct the workplace environment using a PC.
We thoroughly verified how much of the capability could be achieved.” The K-SPARC palletizing software was also used beside the K-ROSET software. With K-SPARC, it is easy to generate operation programs by simply selecting the workpieces, pallets and stacking patterns on a PC.
Nowadays, automation needs are diversifying and the number of product types to be handled could fluctuate always.
“An attractive aspect was that even when the box size or pattern changes, the user can easily change,” says Mr. Nakamura.
Future prospects and plans:
Anticipating the future with eight palletizing robots
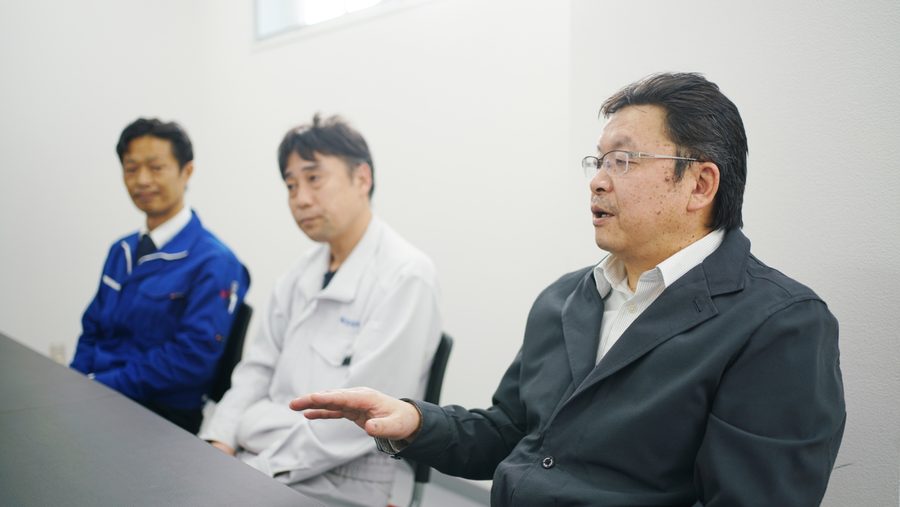
According to Factory Manager Kohei Hatano (photograph right), who heads the Factory B at the Kasugai Factory, “When we mechanized, at the beginning there were concerned comments from the employees.
They thought that a failure may occur, and they worried that there might be a lot for them to learn. However, in the end, everyone changed their feeling to positive for the installation.”
Regarding the results of the palletizing automation system installation, Mr. Hatano says that, “As expected, the physical burden has been reduced on the line where the pallet stacking work has been eliminated.
No human intervention is needed from the production area to the logistics, so human error has also been eliminated.”
At present the application is only for three product items, but in the future, Mr. Nakamura explains that, “The goal is to automate the palletizing for all the products produced in Factories A and B.
To approach that final goal, we have planned construction work split into three phases, with the work this time being Phase 1.
We are planning to start Phase 2 next year.”
The goal is to automate all the 14 lines including the 11 lines in Factory A. In anticipation of this, in addition to the three robots in operation in the palletizing area, there are also five more CP180L units already in “stand-by”.
Mr. Kuroiwa from Ryowa Electric explains that, “In the end, what is important in our work is to respond flexibly and think how we can make an original system that will be as easy as possible for the users to use.”
He says that more than anything else, it is vital to gain thorough knowledge of the user’s workplace and ways of working, and that, “If we had not understood the production management of Kasugai Seika, then it would have been impossible to realize the system created.”
“When you actually use a robot, there are some robot functions that are difficult.
The role of the system integrator is to coordinate so that they can be used as simply as possible by the customer.
The more robots become complex and the more things they become able to do, the more work there is for us.
We make an effort to create a system that will be easy for the customer to handle and want many more people, in as many companies as possible, to use robots.”
― Company information Company name: Kasugai Seika Co., Ltd. Representative: President and Representative Director Daisuke Kasugai Established: April 1948 Capital: 100 million yen Core business: Manufacturing and sales of confectionery Employees: 580 Places of business: Headquarters: 1-3-14 Hananoki, Nishi-ku, Nagoya-City, Aichi Prefecture Headoffice Factory: 1-5-2 Hananoki, Nishi-ku, Nagoya-City, Aichi Prefecture Kasatorikita Factory: 4-106 Kasatori-cho, Nishi-ku, Nagoya-City, Aichi Prefecture Kasatori Factory: 2-121 Kasatori-cho, Nishi-ku, Nagoya-City, Aichi Prefecture Kasugai Factory: 656-2 , Tenjinmae, Ushiyama-cho, Kasugai-City, Aichi Prefecture Aioi Factory: 5377-15 Aioi, Aioi-City, Hyogo Prefecture Website: https://www.kasugai.co.jp ― Robots installed Model CP180L: A high-speed palletizing robot that boasts the fastest processing capacity in the industry. Realizes energy-saving with the first standard installation of a power regeneration function in the industry. Features: Powerful drive system that realizes high speed operation, energy-saving design using the power regeneration function Payload: 180kg Axes: 4 Positional repeatability: ±0.5mm Maximum reach: 3255mm Operation speed: times/hour* *Operation patter of 400 mm upward, 2000mm horizontal and 400mm downard movements.