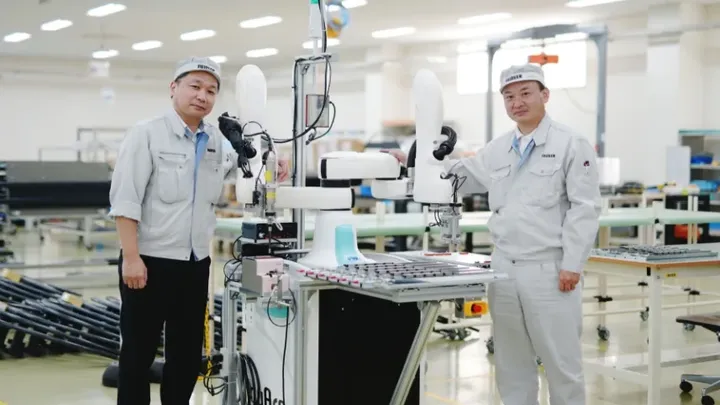
Robot user: FUJISEN Technical Industry Co., Ltd.
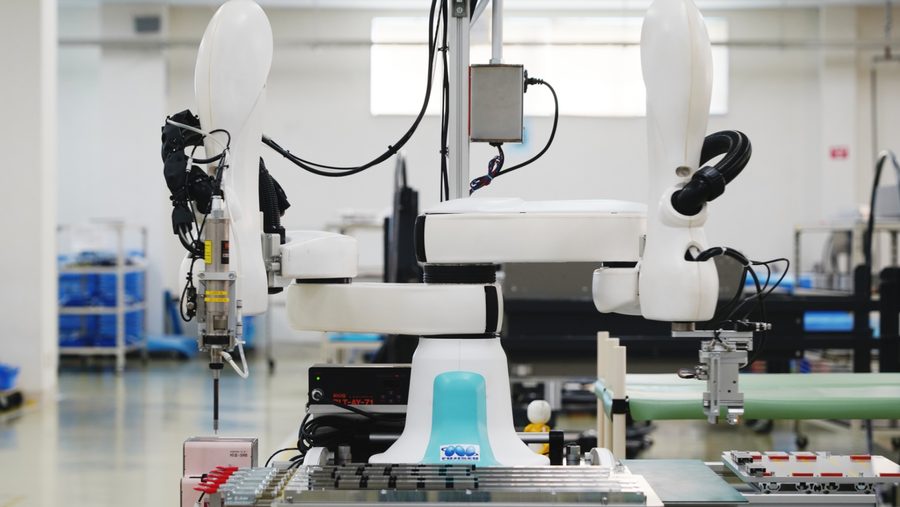
FUJISEN Technical Industry Co., Ltd. (Headquarters: Ashikaga City, Tochigi Prefecture, President Fujio Kinoshita) performs development and design and component processing and assembly for industrial devices such as semiconductor manufacturing equipment. It installed the “duAro” robot from Kawasaki to solve the labor shortage that had long been a problem for the screw tightening process inside semiconductor testing equipment, and to stabilize the work quality.
When an automation system using a robot is introduced, a system integrator usually performs the system setup. However, FUJISEN performed in-house system integration, including the production of peripheral devices.
Based on that experience, the company is now aiming for external sales of the automation system for screw tightening using robots.
Introduction background/issues:
The introduction of robots solved the difficulties in hiring skilled workers and maintaining high work quality
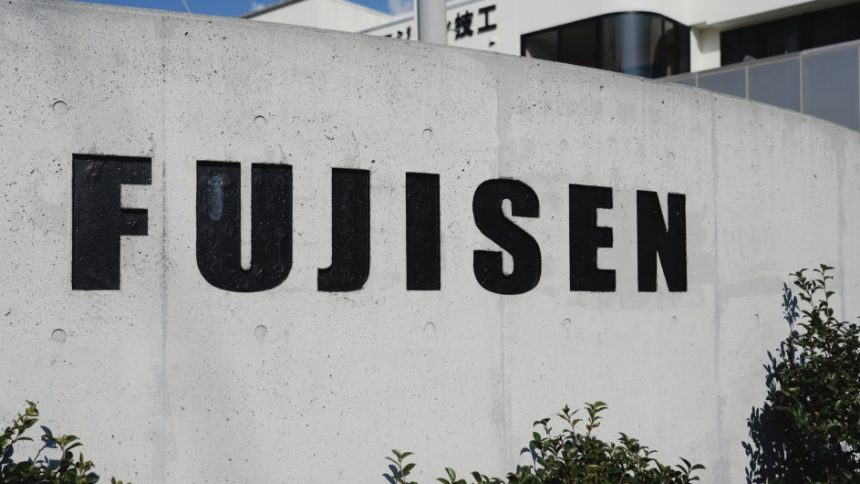
FUJISEN was established in 1987 as a metal processing company.
It went on to start total engineering with a focus on the manufacturing industry, including with the design and development of industrial devices, component procurement and assembly.
It currently has a sheet metal plant and a cutting plant that support various materials, and has around 120 employees.
The trigger for FUJISEN’s decision to automation using robots was a labor shortage.
The company had difficulty gathering employees to perform the assembly of semiconductor testing equipment and struggled with recruitment. They decided to automate the work with a robot.
Ikuyo Sato, General Manager of the Sales and Marketing Division of the company says that,
“The demand fluctuation in the semiconductor industry is very large, and those increases and decreases in the demand cause fluctuations in the number of personnel required. Therefore it is difficult to keep necessary workers employed.”
“Even if we attempt to use temporary workers to secure the people at the times they are needed, when we check their skills to secure tightening quality, the pass rate is only about half.
When we considered a method to constantly secure workers who could satisfy the quality for this screw tightening work, we thought that a robot would be ideal,”
Screw tightening looks like simple work, but, as Keiji Akutsu, Manager of the Engineering Department of the company stressed, “When the accuracy of the screw tightening is poor and there is looseness, it may lead to the suspension of the plant operations being caused by damage to the machine.
Screw tightening is extremely important work.”
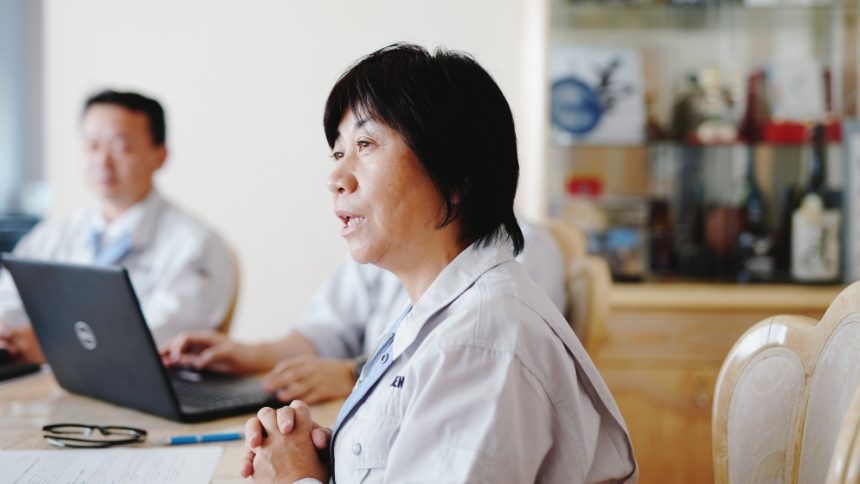
The judgment by the customer regarding screw tightening is very strict, and there are requirements for high precision and stable quality. However, when trying to recruit workers for a simple repetitive work, there are not many applicants. It is difficult to get the workers to continue working until they attain a certain level.
Chief Engineer Hideki Sakamura of the Engineering Department Production Engineering Section says, “Even though it is merely screw tightening, we had the issue of how we should manage the quality of the manual work.
In a situation where we couldn’t recruit the workers, we thought that it was necessary to have a robot, which would have stable quality.”
Introduction effects/solutions:
The deciding factor for the duAro installation was the two arms that can do the same work as a human
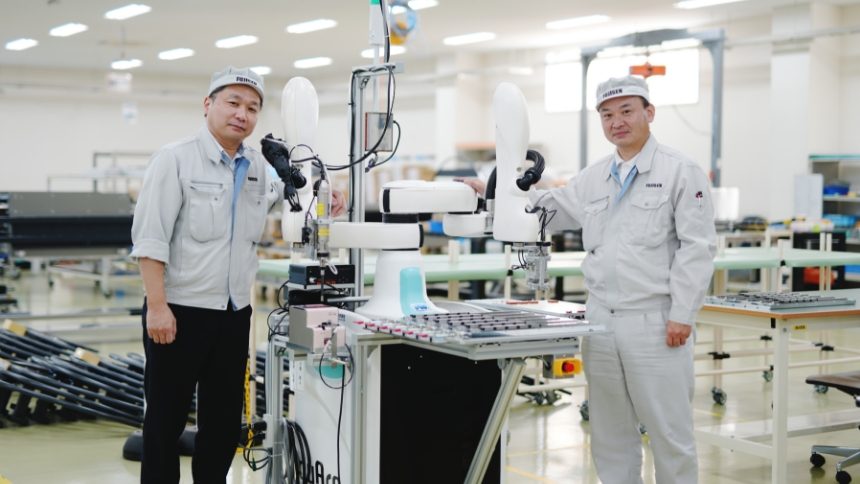
duAro is a collaborative robot with two SCARA arms that move horizontally and vertically.
It was launched in June 2015 and features a compact, movable and safe arms.
Unlike conventional industrial robots, where it is necessary to separate the robot and humans for safety, the duAro can work in the same space as humans.
The programming is performed using a commercially-available tablet, with a feeling that is close to a smartphone app.
Regarding the choice of duAro from among the many robots available, Department Manager Akutsu explained that, “We looked for robots from various manufacturers, but the fact that duAro has two arms and can do the same sort of work as a human was the deciding factor.
For introduction to a process that people use two hands to perform, we couldn’t imagine anything other than a dual-arm robot that could move in a way similar to humans.”
In the assembly and wiring plant for semiconductor testing equipment, one of the arms of duAro carries in a plate type member called an “LM guide” and places it in the prescribed position, and then the other arm performs the work to grasp a screw, insert it into a hole and tighten it.
The LM guide is a rail which guides the straight line movement of the equipment.
One process involves the tightening of screws for six LM guides.
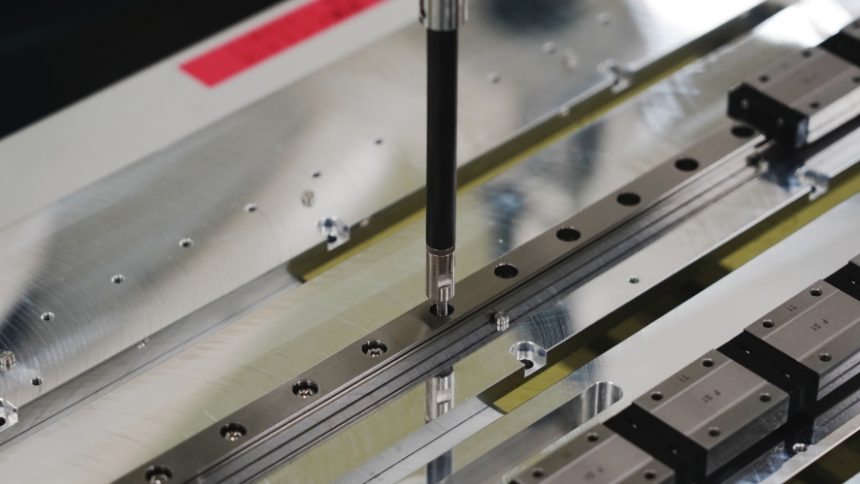
According to Department Manager Akutsu, the use of duAro to automate the screw tightening work increased the precision and also halved the work time for the single process compared with manual work.
By using a robot for the LM guide screw tightening, the personnel who had previously been responsible for screw tightening work could be reassigned to other work. Therefore, when considered for the plant as a whole, it realized improved production process efficiency and the optimization of personnel allocation.
Furthermore, by having a robot perform the work, it is possible to record all of the series of operations in the screw tightening work, with detail data for the number of rotation and torque for each screw.
There has not been a single failure since the duAro began the screw tightening work. Another merit for the robot is its traceability. Even if a failure should occur, it is possible to check all the records of the robot operations.
Chief Engineer Sakamura added that, “Another reason for selecting duAro was that the training center was close to our plant.”
There are nine Kawasaki robot service centers in Japan and one of those, the Kanto Service Center is located here in Ashikaga City.
Future prospects and plans:
The plan for the second robot is to be able to support various applications, and sell the systems externally using the experience we have acquired.
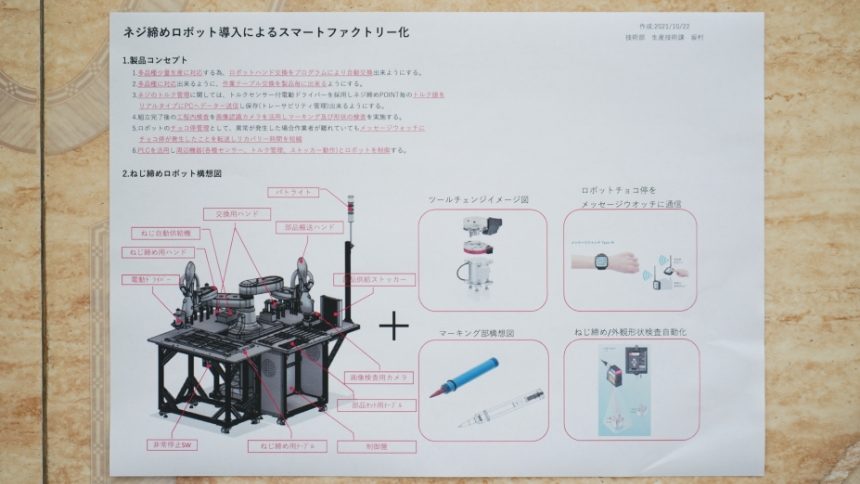
FUJISEN is planning to install its second duAro, with a target of spring 2022.
Unlike the first robot, which is specifically for screw tightening, the plan is that the second robot will be given versatility by making tool changing possible, and will automate various work processes.
Department Manager Akutsu says that, “We want to avoid it becoming a dedicated machine and want to improve work efficiency as far as possible.”
We will make it possible for the robot hands installed on the tip of the arms to be automatically changed by the program, to support the production of a large number of varieties in small quantities, and we will make it possible to change the work table for each different product.
Furthermore, we plan the utilization of an image recognition camera for inspections after assembly, and adding a function so that notification can be sent to the message watch of a worker in a different location whenever a momentary stop occurs (when there is a sudden temporary stop due to catching or clogging, etc.).
External sales of automation systems will be developed by utilizing the know-how accumulated through the installation of duAro at the company.
Division General Manager Sato explains the meaning of this as, “We want to support the solution of the problems of small- and medium-sized manufacturing businesses that are struggling with labor shortages.”
duAro can be used to replace repetitive work such as putting products in cardboard boxes and assembling components.
Department Manager Akutsu explains that, “We want to sell it as a robot system that can automate a specific process such as crimping, packaging, or assembly.”
“For example, when employing people for the 24-hour operation of a plant, if we think of one person working for eight hours, then it becomes necessary to employ at least three people.
duAro is not particularly expensive, so if we think about 24 hour operation, it does not take that long to recover the cost,” explains Department Manager Akutsu.
FUJISEN has an in-house design department, so it can plan and manufacture the incidental equipment that becomes necessary when constructing a robot automation system.
The policy is to begin the external sales of robot systems based on duAro within 2022.
Department Manager Akutsu rates the duAro very highly, saying that, “We are only considering duAro for the robot to be used in the automation systems we will sell externally.”
― Company information Company name: FUJISEN Technical Industry Co., Ltd. Representative: Representative Director Fujio Kinoshita Established: July 1987 Capital: 90 million yen Core business: Industrial devices such as electrical devices, semiconductor manufacturing equipment, adjustment labor-saving equipment, measurement devices, etc. (1) Development and design, (2) Precision plate metal components, (3) Mechanical component processing, (4) Assembly and wiring Employees: 120 Places of business: Head office: Ashikaga Plant, Cutting Plant: 400-6 Minamiomachi, Ashikaga-City, Tochigi Sheet Metal Plant: 685 Higashi-shinmachi, Ota-shi, Gunma Proactive Co., Ltd. (Manufacturing): 400-6 Minamiomachi, Ashikaga-shi, Tochigi Proactive Co., Ltd. (Worker dispatch business): 905-17 Tanaka-cho, Ashikaga-shi, Tochigi Website: http://www.fujisen.co.jp/ ― Robots installed Model duAro1: The first dual-arm SCARA robot with a collaborative concept Features: Compact, simple teaching, easy installation and high level safety Max. payload: 2 kg on each arm (4 kg with two arms) Axes: 4 axes on each arm Positional repeatability: ±0.05 mm