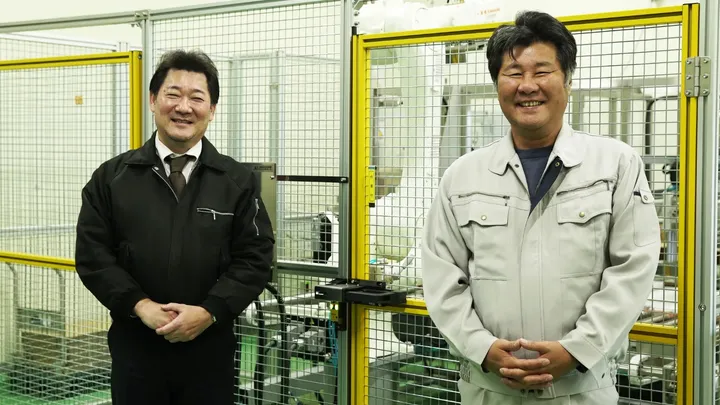
Marumi Foods Co., Ltd.
Robot user: Marumi Foods Co., Ltd.
System integrator: K’s Beltech Co., Ltd.
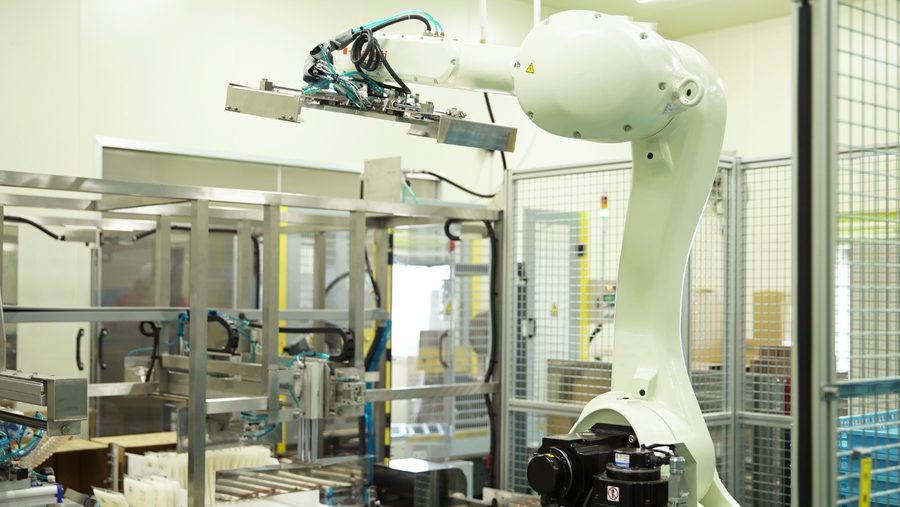
Fresh grated radish made from the whole radish procured from local contracted farmers.
This is freshly packed and sold by Marumi Foods Co., Ltd.
The radishes processed in one day is three to four tons.
The processed grated radish is packed and then rapidly frozen at -35℃, making the products cold, heavy and slippery. The work to pack the items in the cardboard boxes for shipping required a lot of human labor, and was also work that placed quite a burden on the workers.
Labor-saving for the process was achieved by an automation system using a vertical articulated robot.
Introduction background/issues:
The packing of frozen foods in boxes required manual labor and time
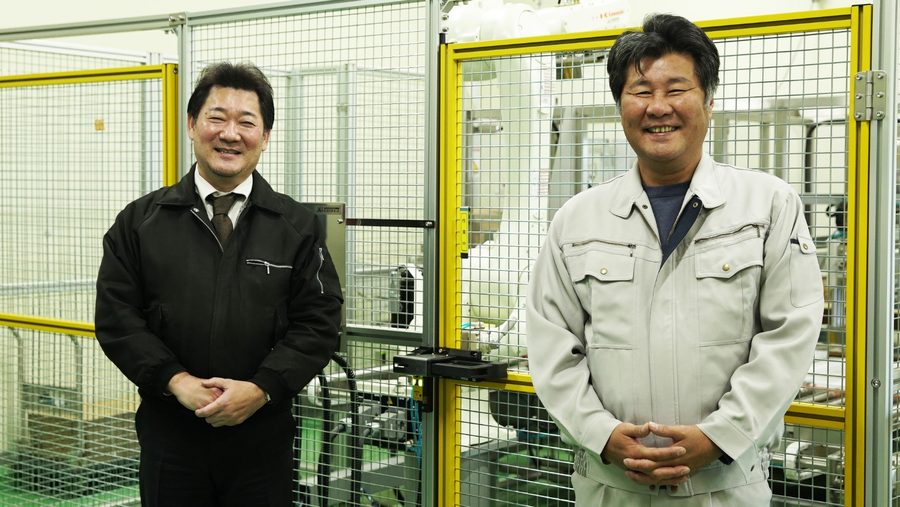
This robot system to automated box packing was created in close cooperation with Mr. Katsunari Satozono (photograph left), Representative Director of K’s Beltech, Co., Ltd., which has a history of over 50 years as food professionals.
Choshi City in Chiba Prefecture is blessed with a warm and humid climate all year round, so there is a lot of cultivation of vegetables grown outdoors.
Of the crops that this land produces, it is radish that has the greatest production in the prefecture.
Marumi Foods Co., Ltd., sells frozen grated radish that seals in the deliciousness of those radishes at an extremely low temperature.
The radishes are brought in by local farmers with their leaves and tails removed. After peeling, sterilization, chopping and grating, the product is placed in pillow-packaging and rapidly frozen.
All the processes after the inspections up to the packing in boxes are conducted as an integrated part of the manufacturing line in the company.
Of the series of process, box packaging of the products after the rapid freezing previously required a particularly large number of workers.
The frozen packs weighing 500 g per bag are cold, heavy, and slippery, so they are extremely difficult to handle and there was an issue that continuing the work for a long time was difficult.
Marumi Foods Representative Director Katsuya Miyauchi, who has been advancing the labor-saving using dedicated machinery for several years, explains that,
“When we think of 10 or 20 years into the future, factory automation will be essential.
It will be too late if we panic and install something later.
This is why we decided on the introduction of an automation system using a robot.” In addition to reducing the burden on the employees and improving the efficiency of the work, the increase in labor costs in the future was also taken into consideration, and the full-scale operation of a robot system for box packing automation was started from 2021.
Introduction effects/solutions:
Success in labor-saving with a robot playing two roles + an original system
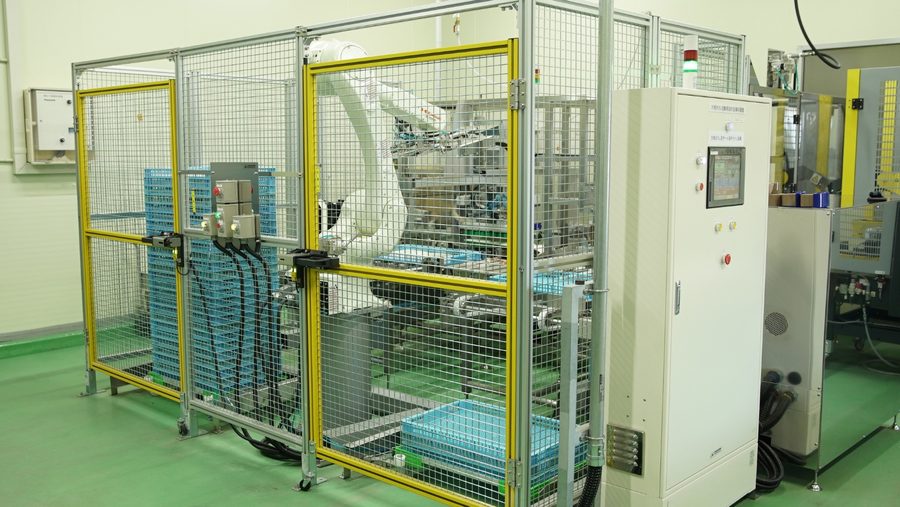
The robot unstacks the trays in order from the top and places them on a conveyer.
After a suction conveyance device lifts the products up, the robot stacks the empty tray in the stacking area on the right, from the bottom.
The robot arm is performing in the full range of its reach in the vertical direction.
The automation system for box packing of the products is composed of: (1) an RS020N vertically articulated robot responsible for the stacking/unstacking of the trays (containers), (2) a suction conveyance device, (3) a conveyer system, (4) a workpiece alignment and box packing mechanism, (5) a case former and (6) a case sealer.
It features compact design, where the whole system fits into a space of about four square meters.
The series of processes starts from the 30 stacked trays that are brought in from the freezer and placed in the unstacking area.
As the start button is pressed, the robot grasps the trays in order from the top and places them on a conveyor. The six packs placed in a tray are picked up by a suction conveyor. Then, the robot moves the empty trays to the stacking area.
During that time, the products that are supplied to the alignment and box packing area are packed into a cardboard box, 20 pack each. Finally, the boxes are sealed and moved to the shipping area.
It takes seven to eight minutes to process a rack stacked with 30 layers.
There are nine boxes containing 20 products completed per flow.
This robot system has reduced workers in the box packing process from four or five to one or two.
Also, there is no direct contact between workers and the frozen products, eliminating the risk of thawing products.
Representative Director Katsunari Satozono of K’s Beltech which designed this automation system, says that, “The cost and space were suppressed by having a single robot perform two roles of unstacking and stacking.”
K’s Beltech, Co., Ltd. is a pioneering company that was the first in the world to work on the wire belt for food conveyance that is commonly called a choconet conveyor.
They have been involved in the construction of automation systems for food production lines for more than 50 years as food professional.
“The case former and case sealer used in this system are commercially available machinery, but the other peripheral equipment is mainly originals devices.” (Mr. Satozono)
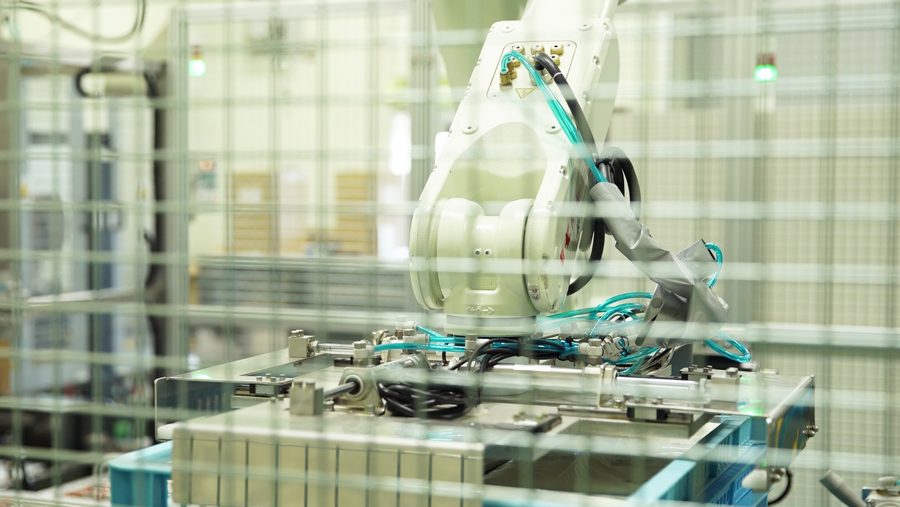
Even if there are less than 30 trays stacked, the robot can search for the position of the uppermost level and start the work.
Mr. Satozono explains that, “Soon after the products come out from the freezing room, their condition and shapes change every moment.” The workpieces are delicate, so elaborate inventive ideas have been incorporated throughout the system.
The robot hand where the bracket to grip the trays is attached has a proximity sensor, so it can start the unstacking work from where it detects the height of the stack (= the start point), regardless of whether there are 30 trays or 20 trays stacked.
The cold workpieces can sometimes adhere to the plastic trays, so when the tray is placed in the suction area, it is deliberately dropped from a small height to apply an impact so that the workpieces will more easily separate from the tray.
As Mr. Satozono says, “With suction to hold a workpiece that is at -30℃ to -40℃, there may be an effect on the vacuum part, or the pad may become too cold and fail.” To make it possible to handle frozen products reliably and continuously, he says that they found the optimal solutions after building an ejector into the hand and closely examining things like the pressure and the material and shape of the pad.
The surfaces of the packs filled with grated radish all have slight irregularities, so the seemingly simple work of aligning and placing them in the boxes also required inventive ideas.
The workpieces are rough and as hard as stone. When multiple of them are clamped from both side and lifted up, they may slip and fall down.
For this reason, this system employs a unique mechanism. The cardboard box is first fallen over on its side. The products are then pushed with a cylinder and packed in the box by sliding them from the side. The box is then raised upright again and sealed.
Mr. Satozono explains that, “We believe in ‘Simple is best’.
It is possible to make as complicated a system as you want, but the more equipment there is, the more the risk of failure increases.
Considering hygiene, a simple system is ideal, too.”
Future prospects and plans:New factory in anticipation of full automation
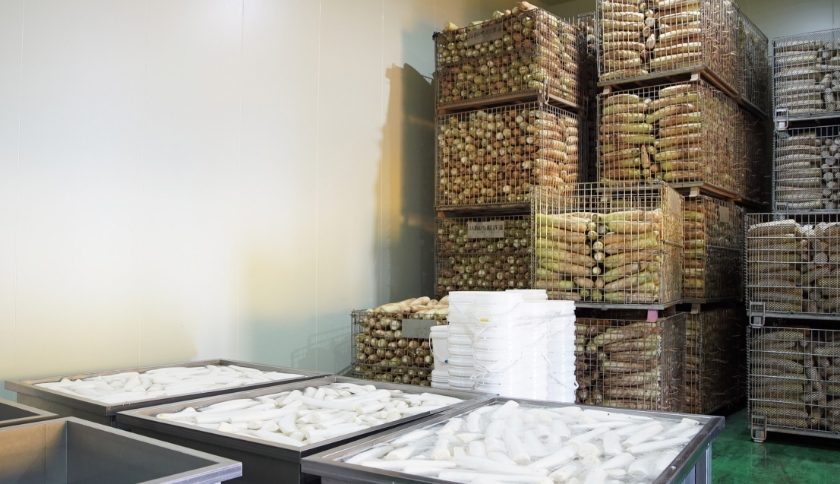
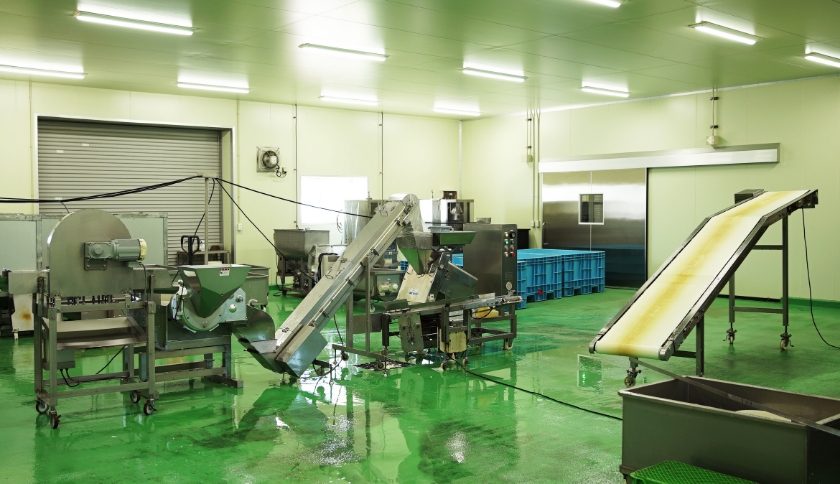
▲When building a new factory, automaony
tion equipment was introduced for each process of the peeling, cutting and grating of radish.
For full automation in the future, the factory has a single line of flow connecting all the processes of ingredient acceptance, storage, processing, freezing and shipping.
Marumi Foods built the current factory in 2018 with a view to full automation.
Automation is already being advanced with the introduction of dedicated machinery for each process such as the radish peeling, cutting, grating, filling and packaging. However, there are still quite a few sections that rely on work by people, including the supply of materials to the machinery and the transfers between processes.
Mr. Satozono describes the prospects for the automation of the entire factory that, “We want to automate the sections connecting each process, from A to B, B to C, and so on.
We are also considering the use of robots for the palletizing after the box packing.”

President Miyauchi says that using robots was his own strong desire.
Mr. Satozono explains, “We have always used food machinery and packaging equipment.
With each individual dedicated machine, it is only possible to reach semi-automation. If a robot is used, then full automation will be possible.
A robot can also be used in various applications by changing its hands and programs.
Investing in robots is not only for the present, but also for the future, as yet unseen, opportunities.
However, the introduction of robots does require assistance from people.
It is our job to create the conditions and environment so that the robot is able to achieve 100% of its performance.”
President Miyauchi explains the relationship between the user, the system integrator (SIer) and the robot manufacturer as follows.
“If the robot is the engine, then the SIer is the party that makes it move, in other words, the party that gives it the chassis. We, the users, are the drivers.
It is an analogy to building automated systems.
Drivers all have their own idiosyncrasies.
I think it is the SIer who is able to create something that fits perfectly to those idiosyncrasies.”
With this explanation, President Miyauchi has a strong belief in the power of robots.
“Robots have an image of being something in large, state-of-the-art factories such as in the assembly of automobiles and manufacturing of semiconductors.
But there will surely be a day when robots also come to small factories such as ours.
This is what I believed.
Due to the nature of a workplace that handles foods, automation not only leads to labor-saving, it also contributes in terms of hygiene.
If we think about 20 years into the future, I believe that this is the minimum level of equipment that we should be preparing.” — The versatility of robots is being utilized to expand the venues for their utilization into various workplaces.
― Company information Company name: Marumi Foods Co., Ltd. Representative: Representative Director Katsuya Miyauchi Established: August 1989 Capital: 3 million yen Core business: Vegetable processing and sales, environmental business through renewable energy power generation Place of business: Head Office: 1323 Tokoyoda-cho, Choshi-City, Chiba Website: https://marumifood.amebaownd.com/ ― Robots installed Model RS20N: A six-axis vertically articulated robot that can be applied to a wide range of applications such as assembly, material handling and sealing Features: Compact and slim, but has a high rigidity arm, a wide motion range in its class, high dust- and water-proof performance Payload: 20kg Axes: 6 Positional repeatability: ±0.05mm Maximum reach: 1725mm