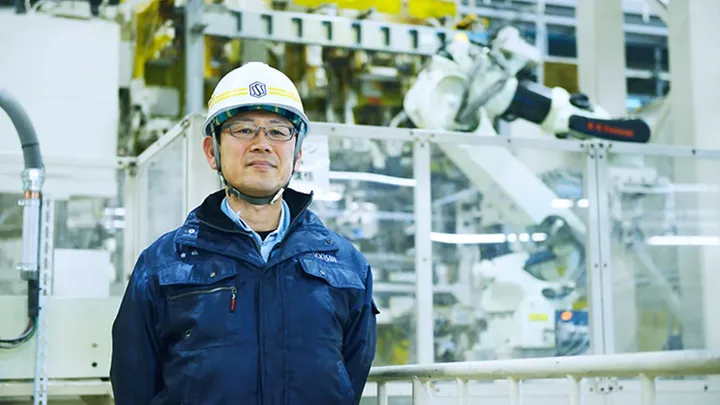
Sekisui Heim is the world’s first company to construct houses using the Unit Construction Method. The company’s production process has been and still is a continually evolving pursuit of quality and efficiency, and in its Kyushu factory, “robotic house construction” utilizing industrial robots is happening.
The Kyushu factory is located in Tosu City, Saga Prefecture in Japan and robots are implemented on the housing unit assembly line. These are industrial robots built by Kawasaki Heavy Industries, or Kawasaki. The intention behind this application of robots was to realize strict quality control and to deal with aging factory workers and labor shortage.
There are numerous options for bespoke houses when it comes to room layout and exterior design, depending on the customer’s lifestyle and personal tastes.
“Factory-automating all of that must have been very challenging…” With that thought in mind, we toured the Kyushu factory while interviewing with Mr. Satoshi Kurahashi, the Engineering Division manager and Construction Division manager of Kyushu Sekisui Heim Industry Co., Ltd., who, from the very beginning, led the project of establishing a factory with active robot workers.
At the factory, robots play a role assembling unit frames
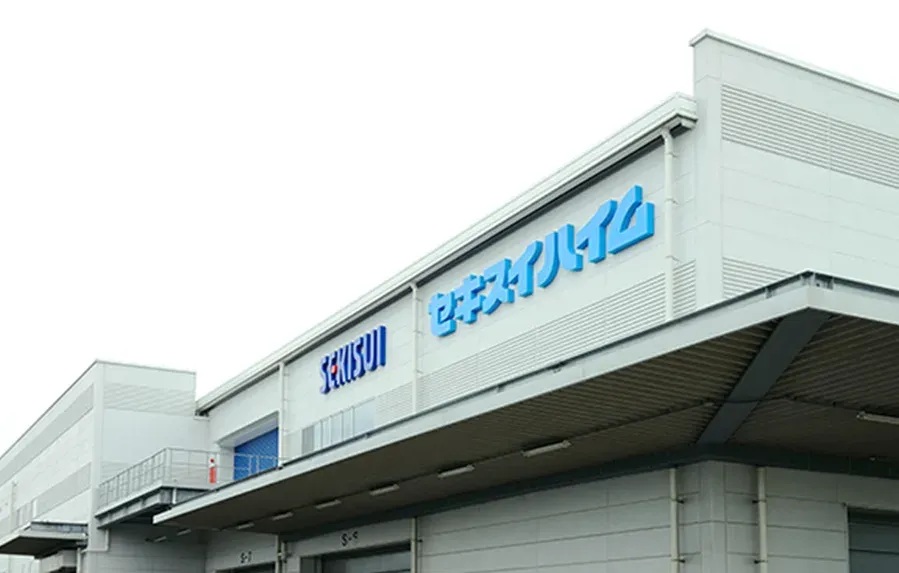
The Kyushu factory is approximately 77,000 square meters. On this site with an area equivalent to one-and-a-half times the Tokyo Dome where it can hold 55,000 people, sits the Heim Production Building, where “houses are assembled by robots”.
The Unit Construction Method, a method in which factories manufacture box units, and builders on the actual housing site assemble these units, has been in use at Sekisui Heim since 1971. At this factory, fully completed housing units—with frames assembled, and exterior and interior walls, floors, stairs, windows and sashes all installed—are built and shipped out. Just joining these units together is all that is required at each housing site. Thanks to this method, the work at housing sites can be finished in a day. There are no unassembled units left out in bad weather, leading to a guaranteed quality product.
The way the production line is set up is said to be inspired by car factories. The industrial robots from Kawasaki are utilized on the unit assembly line, working on gable frame assembly, and overall assembly to connect the ceiling, floor and gable frames.
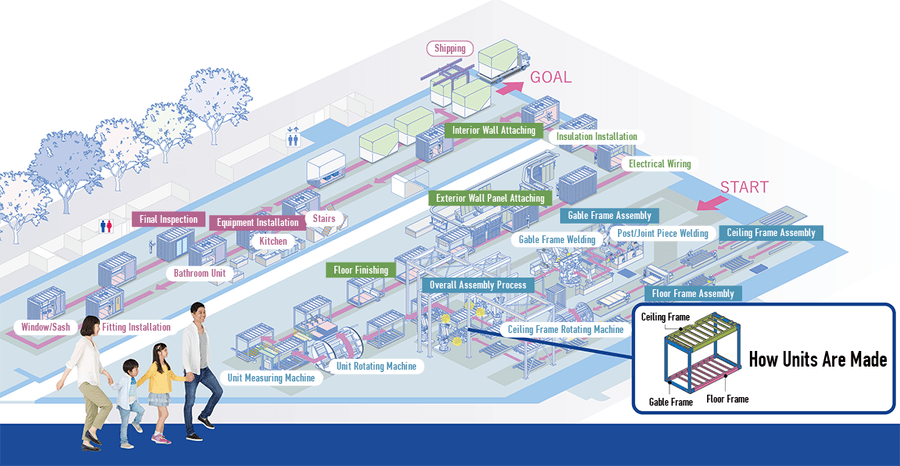
Taking a closer look at the robotic automation process, shows that it can be divided into 4 parts as illustrated below. Kawasaki robots are used in processes 02–04.
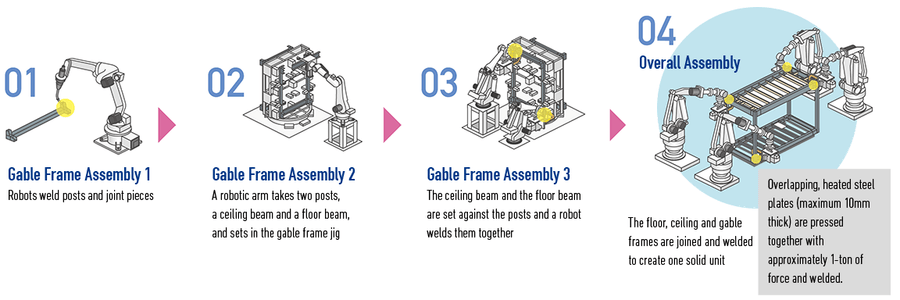
These processes used to be handled manually. So then, why are robots handling these tasks today? And what results have the application of robots brought? We interviewed Mr. Kurahashi, who was the driving force behind the introduction of robots into the factory.
Sekisui Heim’s house-building improved through robot implementation
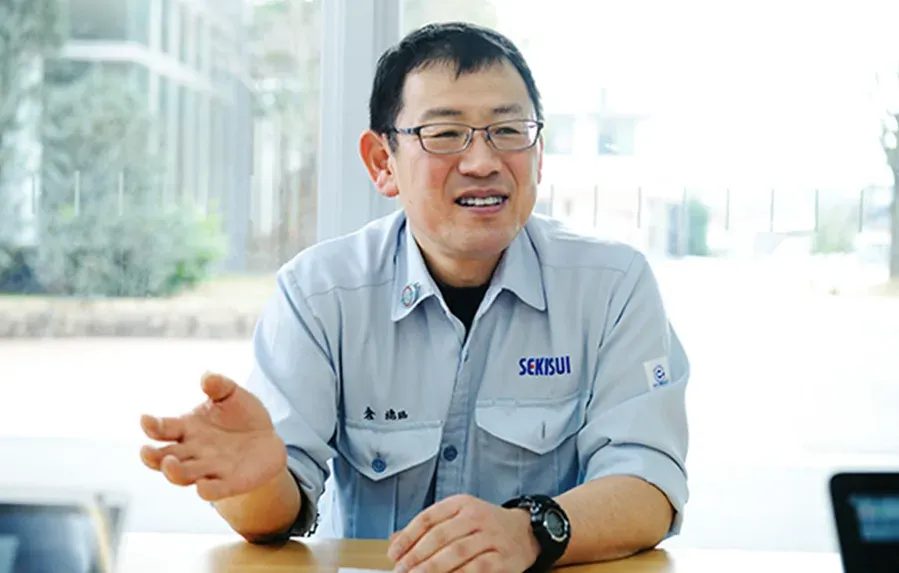
Mr. Satoshi Kurahashi, Engineering Division Manager and Construction Division Manager of Kyushu Sekisui Heim Industry Co.
——Could you explain the reasoning behind introducing robots?
Welder shortage was a serious issue for us. Before automating our spot-welding process, three welders were required. But as they aged, securing welders on a stable basis became difficult. Due to the lack of workers, if someone was off sick, our production and quality would not be guaranteed. Therefore, when the factory was due for a renewal, we decided on the installation of robots.
——What sorts of changes have you seen as a result of deploying robots?
First of all, productivity improved. The factory renewal we’ve undergone has led to an increase in the number of units we are able to produce per day from 55 units to 65 units. Even in factories without robots, the process for constructing houses is the same as it is at the Kyushu factory, and generally, there is an average of 11 to 12 units produced per factory. While factory automation through the application of robots or other methods has cut down the number of workers required for unit assembly by 20 compared to before, we’ve relocated staff replaced by robots to take on tasks which require human hands. In other words, the manpower saved by the streamlining has shifted over to other value-adding tasks.
——Why did Sekisui Heim choose to partner up with Kawasaki?
When we first started conceptualizing this robotic house-building system, we contacted several companies but no one took us seriously since the concept sounded like a dream at that time. No one except Kawasaki. Kawasaki went as far as to simulate the concept and worked with us to the point where we confirmed that it was a technically feasible plan.
Kawasaki was great because they stuck with us and listened to our science fiction-like story. Ordinary companies would first tell us the reasons why they couldn’t take our request.
——How were the robots eventually introduced into the Kyushu factory?
When this project first started out, we had housing business in Thailand and established a joint company with local companies. A new factory was planned for construction, so we took the opportunity to develop component technologies required for factory automation at the new Thailand factory.
The new factory in Thailand was completed in 2013. Since the technologies developed in Thailand were brought as-is to our Kyushu factory, production lines for both factories are quite similar. We call them brother factories, with the Thailand factory being the older brother and the Kyushu factory the younger one.
It took 10 years to embody the concept, but the number of skilled workers will continue to dramatically decrease. In order for us to survive as a house manufacturer, I think the Unit Construction Method is the only way to go. Just for reference, the amount of money we’ve invested into this robot implementation can be paid off within three years, according to our calculations.
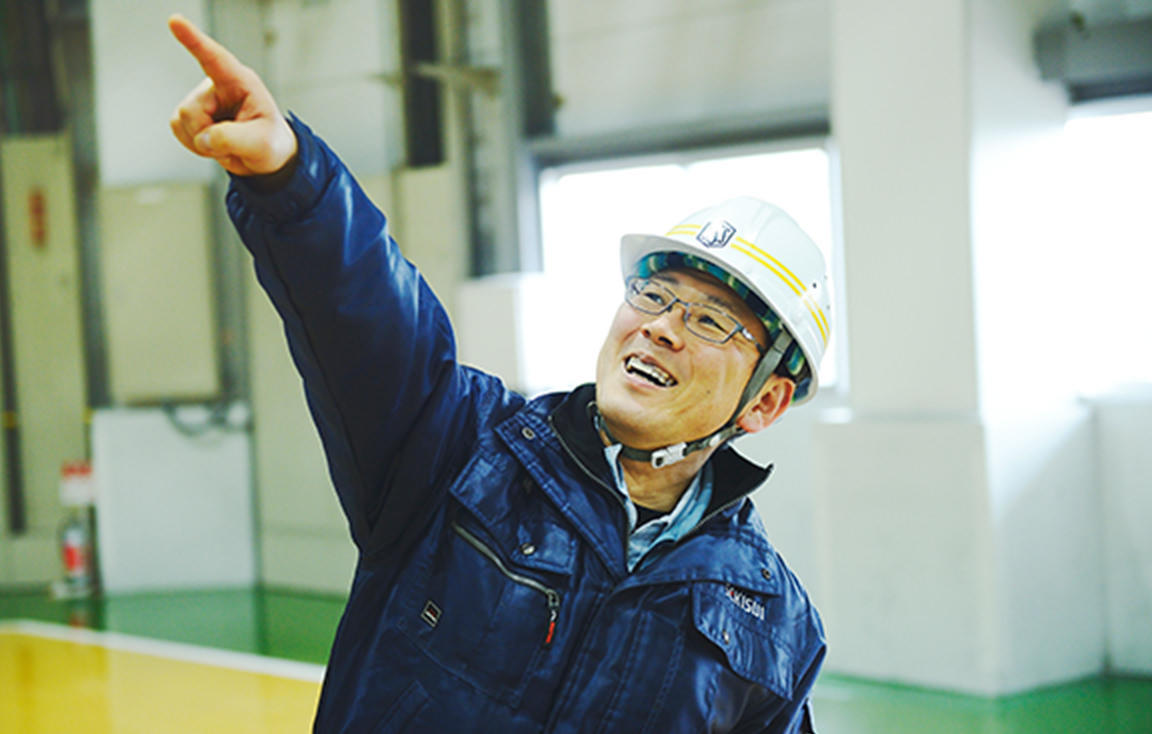
——How far do you think factory automation can go with robots in the near future?
My wish is that it further reduces necessary manpower and makes the building operation easier. Although we passed on it for this factory, automating the welding of floor frames is also possible. Research and development of other component technologies is ongoing and I think making screwing automated is possible as well.
On the other hand, automating the handling of exterior walls is difficult. The amount of variation that can come from customers’ orders is almost infinite, making it very challenging.
The most crucial part of implementing robots was securing the precision of units. I believe that the fundamental first phase has been set with this operation, and I’d like to see young people being nurtured and moving on to the second and third phases.
——Did putting robots to work have any other effect apart from the improvement in productivity?
We have seen a rise in awareness of our company thanks to increased media coverage. The number of school trip visits to our factory has gone up as well, and we’ve received comments like, “It’s so amazing to see moving robots,” or, “The workers are cool!” Those comments by students make our factory staff very happy.
Some staff members even voiced that they have “grown to become proud of working at this factory”.
It has also brought positive influence on our sales. With this renewal, we’ve created a factory visitation route and proactively invite customers who come to see the model houses to visit the factory. Having customers see how the robots construct houses certainly seems to make them more comfortable in their decision to make a purchase.
――Thank you very much for these valuable stories.
Now, here are some reports on how the robots operate in the factory after taking the factory tour.
Gable Frame Assembly—Robots can effortlessly handle materials up to a maximum weight of 200kg
Kawasaki’s large BX200L robot carries four pieces of steel—previously welded posts and beams—and sets them up on the machine laid out like a frame-like configuration. It handles materials up to a maximum weight of 200kg precisely, within a 0.2mm margin of error.
And like a hidden door inside a Ninja house, the machine turns around, where two waiting extra-large MX420L robots spot-weld the corners. Special spot-welding guns are attached to these robots to allow them to weld steel plates, some of which can be as thick as 10mm. Each corner is welded with between 8 and 12 points.
Overall Assembly—Four robots assemble and weld frames to make a solid unit
The overall assembly involves assembling four frames to make a single unit. Four MX420L robots have been installed for this process, too.
The four robots handle the ceiling, floor and gable frames brought over. 10 to 14 points on each corner are welded with temperatures between 1,500℃ and 1,600℃.
The unit acting as the first floor needs to be stronger than the third-floor unit. In other words, the strength of the welds varies depending on the unit and therefore, these robots work with utilizing over 30 different welding programs.
Solving onsite issues through the application of robots
Taking a tour of the factory and witnessing robots actually working showed how the company understands tasks which are difficult for humans but not for robots, and judiciously allocates work between humans and robots.
Sekisui Heim continues to pursue the highest level of quality, having successfully realized a concept others thought sounded like a far-fetched dream at the beginning.
By assigning tasks better handled by humans to humans and leaving other automatable tasks up to robots, the company has made it possible to create a win-win relationship for both their consumers and workers.
Today, apart from the housing industry, there are growing needs in industries that traditionally have not utilized industrial robots such as food and cosmetics. There may be a day when robots step into workplaces where people would have never imagined robots being in the picture.
This article is supported by Sekisui Heim Kyusyu Corporation.