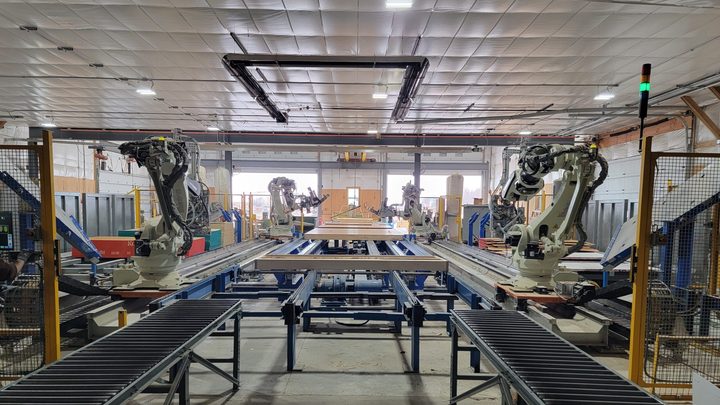
- AplicaçãoMontagem, Manuseamento de materiais
- Série de RobôBX/BT series
Sistema concebido por:
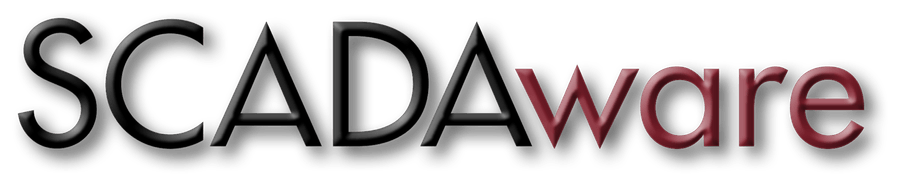
VISÃO GERAL
Recentemente, as casas pré-fabricadas tornaram-se mais acessíveis. Este crescimento levou a um aumento da procura de casas que podem ser fabricadas de forma rápida e económica e montadas no local. No entanto, essa acessibilidade traduz-se em margens mais reduzidas para os fabricantes de componentes de construção, especialmente quando concorrem entre si para os mesmos projectos. Como muitos no sector aprenderam, quanto mais automatizado for o seu processo de fabrico, mais competitivos se tornam na mesa de licitação.
O construtor Rehkemper & Son contactou o integrador SCADAware da Kawasaki para ajudar a automatizar o seu processo de montagem de casas pré-fabricadas. Para além de aumentar a sua vantagem competitiva, também queriam minimizar a sua dependência do trabalho humano devido à escassez. Depois de analisar os processos manuais da Rehkemper, a SCADAware concebeu um sistema único para automatizar grande parte do processo de montagem de paredes pré-fabricadas utilizando software personalizado, robots Kawasaki e calhas Güdel.
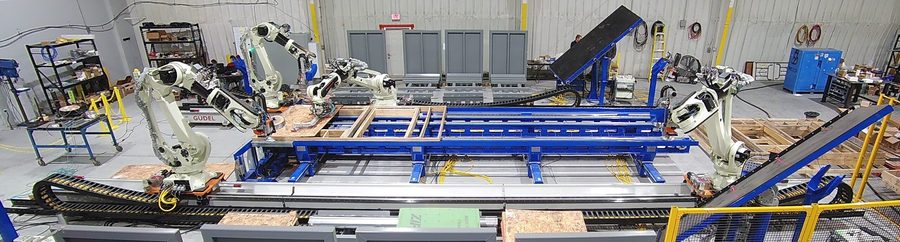
DESAFIOS
Material pesado, aplicação de alta precisão
No processo da Rehkemper, o revestimento de OSB (oriented strand board) é colado às paredes pré-fabricadas. O OSB apresenta-se em painéis de madeira prensada grandes e pesados que podem ser difíceis de manobrar. Precisavam de uma solução robótica que pudesse colocar com precisão os pregos para fixar as placas às vigas de madeira e às vigas escondidas por baixo. O que tornou esta tarefa tão difícil foi o facto de, em comparação com outros materiais de construção, a madeira ser notoriamente imprecisa.
“As tábuas de madeira estão muitas vezes deformadas; e quando se coloca OSB, já não se consegue ver onde se encontra a viga. Se o prego só retém ar, então estamos em apuros”, diz Rick Caldwell, presidente da SCADAware
SOLUÇÃO
- Quatro robots Kawasaki BX250L montados em calhas Güdel TrackMotion Floor-3
- Os robôs fixam os incómodos painéis OSB às estruturas das paredes e cortam as janelas e portas nos painéis
- O software SCADAware personalizado dita os cortes para os robots
A montagem em fábrica de casas pré-fabricadas é efectuada em duas fases. Em primeiro lugar, as vigas de madeira são serradas e montadas para formar o esqueleto das paredes, o telhado e as treliças do chão. A fase seguinte consiste em aplicar o revestimento de OSB nas paredes pré-moldadas, pregar os painéis à estrutura e abrir buracos para as janelas e portas. As peças componentes são depois enviadas para o local de construção, onde são montadas numa estrutura de pé.
Os engenheiros da SCADAware criaram um software personalizado que analisa a versão eletrónica do desenho da parede e indica ao robô onde pregar e cortar. O sistema utiliza uma mesa grande, ajustável e motorizada para acomodar paredes emolduradas com 8 a 14′ de altura e até 20′ de largura. As paredes individuais são transportadas para a mesa do SCADAware, onde são esquadrejadas contra um batente fixo na extremidade mais distante. As extremidades ajustáveis da mesa juntam-se para alinhar a estrutura de cima para baixo.
Isto assegura que o perno de madeira mais próximo do batente final está direito e que a sua linha central física está alinhada com 1/16 de polegada ou mais do desenho digital. Existem dedos servo-controlados por baixo da parede para endireitar quaisquer vigas deformadas. Estes dedos ajudam a alinhar os 3 pinos seguintes, deslizando pela calha central da mesa e aplicando pressão para endireitar cada pino.
Entretanto, dois pares de robots Kawasaki BX250L – cada um com um alcance de 2.812 milímetros, ou seja, pouco mais de 9 pés – estão montados em unidades Güdel TrackMotion Floor-3 (TMF-3) correspondentes que se estendem ao longo do comprimento da mesa em ambos os lados. Cada esteira Güdel mede 15 metros e oferece um curso de trabalho de 12 metros, permitindo que os quatro robôs trabalhem juntos ao longo de todo o comprimento da mesa.
Depois de a parede estar no lugar, um dos robots traseiros junto ao transportador utiliza cabeças de vácuo para apanhar um painel OSB de 4 x 8 pés e colocá-lo sobre as vigas agora endireitadas. Assim que o primeiro painel estiver completamente fixo, os robots e os dedos repetem o processo até que a parede esteja completamente revestida.
Os quatro robots podem mudar facilmente de ferramenta. Enquanto um conjunto de robôs esculpe janelas e portas no painel OSB, os outros dois removem o revestimento cortado e transferem-no para a pilha de resíduos.
Robôs = Fiabilidade
O processo da Rehkemper é extremamente intensivo em termos de mão de obra, o que dificultou a procura e a retenção de funcionários. A automatização pode ser a solução perfeita para estas situações, uma vez que os fabricantes podem confiar nos robots para trabalharem de forma consistente e produzirem um produto de elevada qualidade. Os robôs Kawasaki são conhecidos na indústria pela sua fiabilidade e flexibilidade. Com uma carga útil de 250 kg, os robots BX250L da Kawasaki conseguem levantar facilmente paredes OSB grandes e pesadas. A sua estrutura patenteada de braço oco proporciona uma instalação fácil, manutenção e desgaste minimizado. O seu alcance alargado, as velocidades elevadas e a tecnologia avançada de controlo de movimentos reduzem os tempos de ciclo.
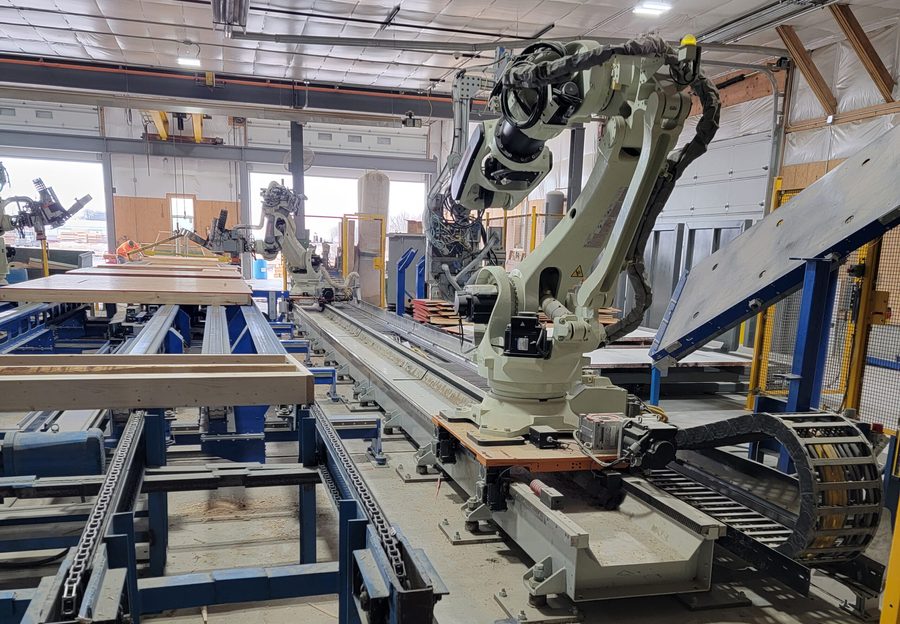
RESULTADOS
- A eficiência aumentou drasticamente
- Aumento do rendimento em pelo menos 25%
- Redução dos custos de mão de obra
Em simulações, o sistema demonstrou que pode concluir a montagem de uma parede de 8 x 20′ em consideravelmente menos tempo do que normalmente levaria dois operadores a concluir – incluindo a colocação e fixação de revestimento OSB e o corte para formar janelas e portas. Com uma otimização adicional, Caldwell acredita que o sistema pode fazer ainda melhor.
“Um grande impulso que levou a Rehkemper a contactar-nos foi a dificuldade que estavam a ter em contratar trabalhadores para fazer este tipo de trabalhos”, disse Caldwell. “Mas o nosso objetivo coletivo era também ajudá-los a competir melhor e a realizar o trabalho mais rapidamente e com menos custos.”
A velocidade, versatilidade e precisão permitidas pelo carril da Güdel prometem aumentar o rendimento em pelo menos 25% sem perda de qualidade. O aumento da produtividade e a redução dos custos de mão de obra permitem que empreiteiros como a Rehkemper & Son poupem dinheiro e ofereçam propostas mais competitivas. Atualmente, o sistema de carris e robôs aumentou a metragem linear produzida por dia em 25%, sem perda de qualidade; espera-se que novos ajustes aumentem a eficiência para 35-40%. Um benefício adicional é a minimização da dependência de mão de obra humana escassa para este processo, resultando em menos tempo de inatividade, maior precisão e ausência de lesões.