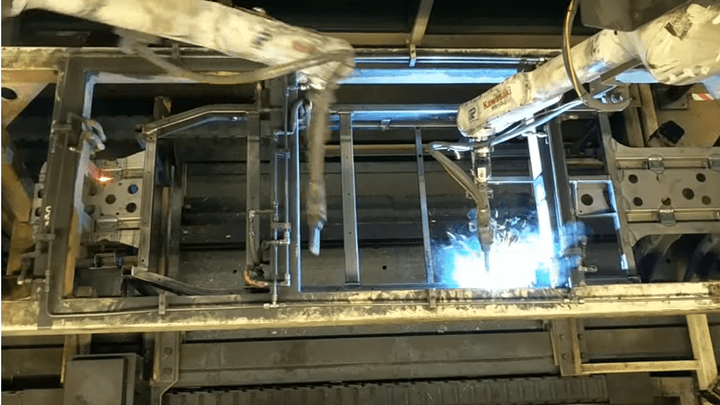
- IndústriasMaquinaria e fabrico de metais
- AplicaçãoSoldadura por arco
- Série de RobôR series
VISÃO GERAL
À medida que os soldadores de arco experientes se tornam escassos e a produção em massa aumenta a necessidade de consistência, muitas empresas ficam sem saber o que fazer. Precisam de soldar as suas peças, mas é difícil encontrar soldadores qualificados que possam produzir produtos de alta qualidade – quanto mais manter esse padrão de hora a hora. Atualmente, os avanços na soldadura por arco robotizada permitem às empresas experimentar a qualidade e a consistência de um soldador por arco especializado no seu melhor dia, em cada soldadura.
Em meados dos anos 80, a Kawasaki Motors Manufacturing Corp, EUA (KMM) instalou os seus primeiros robots Kawasaki para soldar os quadros dos seus veículos todo-o-terreno (ATV) e dos veículos de quatro rodas Mule e Teryx. Trinta anos mais tarde, o fabricante utiliza 71 robots de soldadura por arco Kawasaki, e esse número aumentará para 84 em junho de 2019.
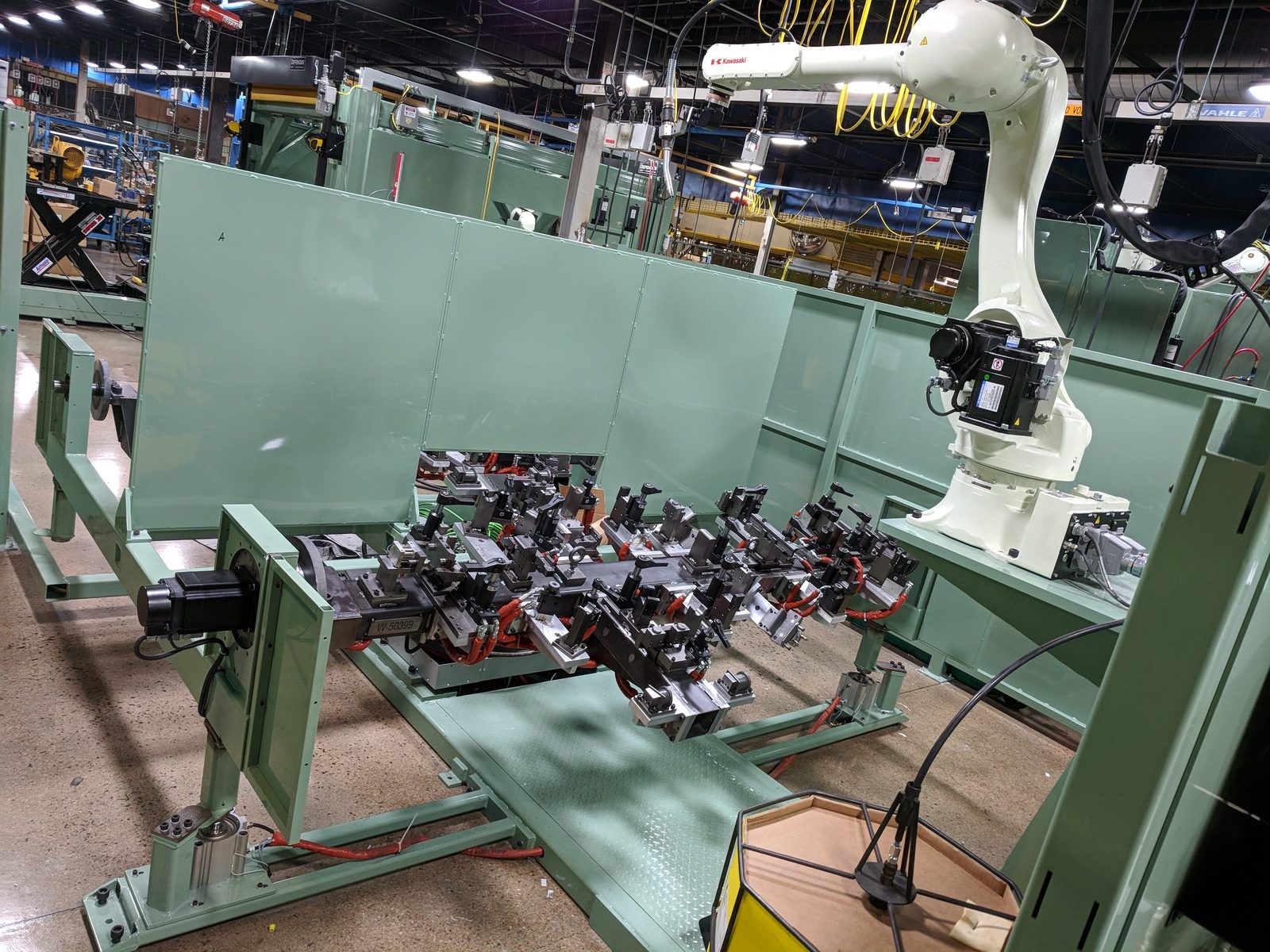
DESAFIOS
A KMM não precisava de automação para aumentar o seu volume de produção. No entanto, necessitava de soldadura por arco robotizada para manter a sua taxa de produção atual e, ao mesmo tempo, fornecer uma estrutura mais repetível. Eles também precisavam de uma solução versátil que pudesse soldar uma variedade de peças.
Uma solução para a escassez de mão de obra
Durante anos, a KMM travou uma batalha difícil contra a escassez de mão de obra na indústria da soldadura. Atualmente, 80% dos processos de soldadura por arco da KMM são automatizados com robôs Kawasaki e apenas 20% do trabalho tem de ser feito manualmente. Agora, os soldadores com formação podem fazer o trabalho adicional, que inclui a dupla verificação do trabalho do robot ou o acesso a áreas de difícil acesso.
Consistência e fiabilidade
Os padrões de qualidade dos produtos estão sempre a aumentar, e cumpri-los com métodos manuais é um desafio. A KMM efectua principalmente soldadura tubo-a-tubo, pelo que necessita de robôs altamente repetíveis para executar programas sem ter de ver o caminho. Para satisfazer esta necessidade, os robots Kawasaki RS010L têm uma repetibilidade de ±0,05 mm, o que resulta num produto altamente consistente. “Os robôs Kawasaki são, de longe, os mais fiáveis que já vimos no mercado”, afirmou Gordon.

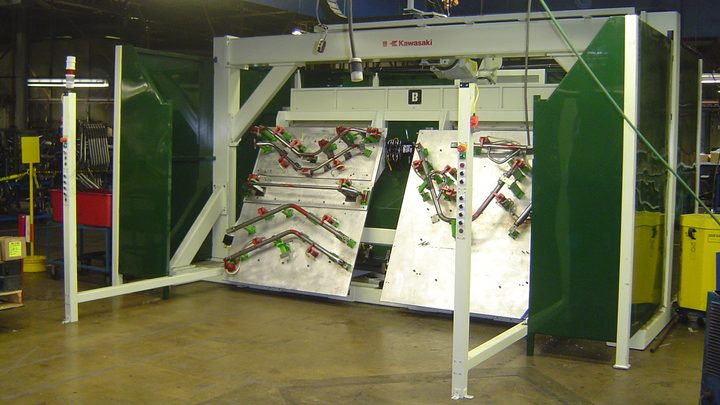
SOLUÇÃO
- Quatro células de soldadura por arco robotizadas especializadas na soldadura de diferentes peças
- Uma célula “Battle Bot” que solda toda a estrutura do ATV ou do veículo de quatro rodas
- Uma célula “Kneeling Easel” que solda estruturas de cabina pesadas
A KMM precisava de uma solução flexível para soldar muitas peças à medida que as necessidades de produção e as linhas de produtos evoluíam. Para o efeito, a KMM desenvolveu cinco células utilizando robôs Kawasaki das séries R e F para soldar diferentes componentes das estruturas dos ATV e dos veículos de quatro rodas. Quatro das cinco células (Tipo 1, Tipo 2, Tipo 3 e Células de cavalete ajoelhado) soldam peças de diferentes tamanhos. Depois de concluídas, estas peças são introduzidas na célula “Battle Bot”, que solda toda a carroçaria do veículo.
A célula Tipo 1 solda peças pequenas, como braços de suspensão. A célula Tipo 2 utiliza uma Kawasaki RS010L para soldar peças de tamanho médio, como bancos ou protecções frontais, à medida que rodam numa mesa de soldadura ligada a um dispositivo de troca rápida. A seguir, a célula Tipo 3 tem uma área de trabalho de 108′ x 52′, tornando-a ideal para a soldadura de peças longas. Por último, a KMM desenvolveu a célula de cavalete ajoelhado para soldar grandes estruturas de cabina de 1,5 m por 1,5 m, cuja forma incómoda constituía um desafio ergonómico para os soldadores humanos.
RESULTADOS
- 80% de toda a soldadura por arco é feita pelos robots Kawasaki
- As soldaduras manuais são necessárias apenas para 20% do trabalho
- Os soldadores humanos verificam o trabalho dos robots ou soldam áreas de difícil acesso
- As inconsistências do produto foram eliminadas devido à flexibilidade e aos elevados níveis de repetibilidade dos robots
Ao longo de 30 anos de soldadura por arco robotizada, a KMM assistiu a uma diminuição drástica da distorção do chassis e a um aumento da consistência. A dependência da empresa em relação à soldadura manual diminuiu, pelo que pode dedicar mais tempo ao fabrico. A KMM continua a adicionar robots de soldadura por arco da Kawasaki para fabricar milhares de chassis de veículos todo-o-terreno ATV, Mule e Teryx.