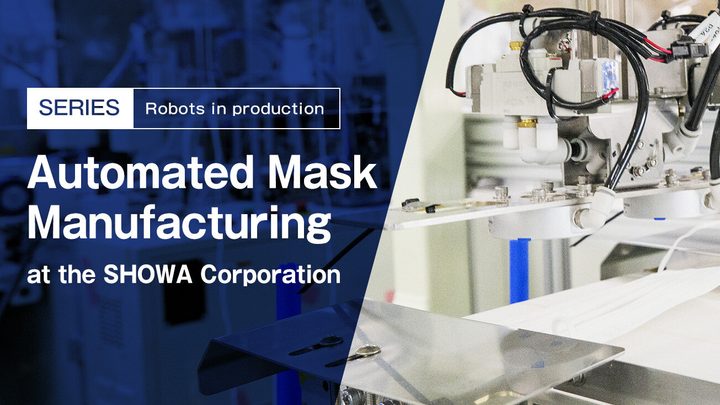
- BranchenBiowissenschaften
- AnwendungenMaterialhandhabung
- SerieYF-Serie
Die Showa Corporation, die sich eigentlich mit der Entwicklung und dem Vertrieb von Industriewaschmaschinen sowie Maschinen für das gewerbliche Waschen von Lebensmitteln befasst, hat im März 2020 als Maßnahme gegen das hochansteckende Coronavirus mit der Herstellung von Schutzmasken begonnen. Bewältigen konnte Showa diese neue Herausforderung nicht zuletzt dank der robotergestützten Automatisierung.
Problem: Unproduktive Abläufe und häufiges Auftreten von Mängeln aufgrund von Handarbeit
Bei Aufnahme der Produktion wurden viele Arbeitsabläufe von Hand durchgeführt, sodass es eine lange Vorlaufzeit und eine steigende Anzahl an unfertigen Produkten gab. Außerdem traten häufig Mängel auf. Zu diesem Zeitpunkt betrug die Produktionskapazität 1,5 Mio. Masken pro Monat. Innerhalb eines Monats wurden jedoch deutlich mehr als 2 Mio. Masken bestellt, sodass das Produktionssystem drastisch überarbeitet werden musste.
Lösung: Vollständige Automatisierung des Prozesses von der Herstellung der Masken über die Überprüfung und die Verpackung der einzelnen Masken bis hin zur Verpackung in Kartons
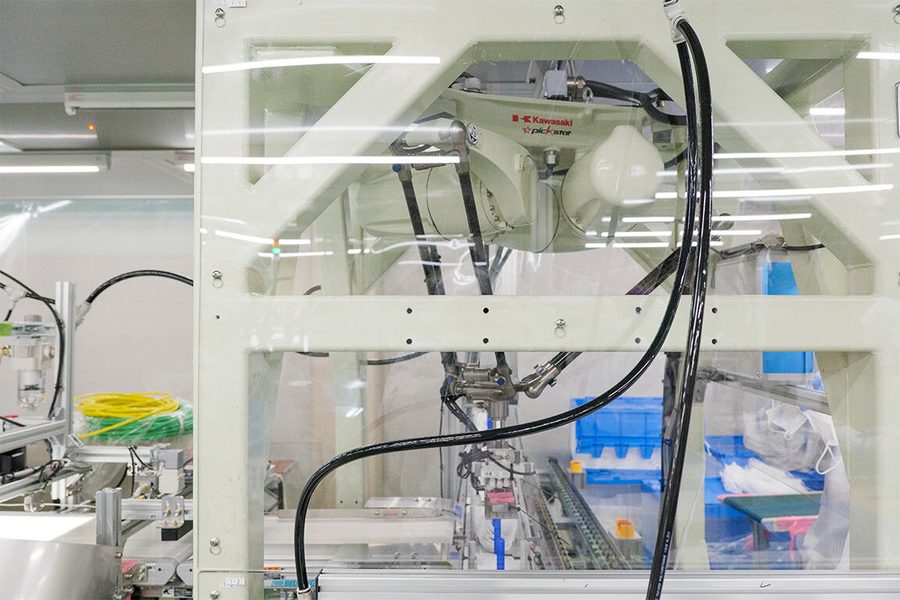
Zur Erhöhung der Produktionskapazität musste der gesamte Prozess von der Herstellung der Masken über die Überprüfung und die Verpackung der einzelnen Masken bis hin zur Verpackung in Kartons mit so wenigen menschlichen Eingriffen wie möglich vollständig automatisiert werden.
Der Prozess umfasst das Zuschneiden, Aufschichten und Falten des Vliesstoffes, das Anbringen des Nasendrahts und der Ohrlaschen, das Prüfen auf Mängel und Defekte mittels Kamera, das Verpacken der einzelnen Masken in Kunststofffolie und das anschließende Verpacken der Chargen in Kartons. Durch die Automatisierung dieser Abfolge von Arbeitsschritten, für die vorher etwa 50 Mitarbeitende benötigt wurden, konnte die Anzahl der benötigten Arbeitskräfte deutlich reduziert werden. Außerdem konnte die monatliche Produktionsmenge auf 2 bis 3 Mio. Masken pro Monat angehoben werden. Anschließend hat man sich darauf konzentriert, verschiedene Details zu verfeinern, wodurch inzwischen eine Maximalkapazität von 9 Mio. Masken pro Monat erreicht werden konnte.
An der Produktionslinie sind auch die für ihr hohes Arbeitstempo bekannten Pick-and-Place-Roboter der Y-Serie von Kawasaki Heavy Industries 24 Stunden am Tag im Einsatz. Dadurch konnte die Anzahl der für den Transport der Produkte benötigten Mitarbeitenden von vormals zehn auf einen Mitarbeitenden reduziert werden. Dies hat stark zur Rationalisierung beigetragen. Roboter mit Parallelkinematik sind mit schmalen Greifarmen ausgestattet, die an Greifautomaten erinnern, wie man sie beispielsweise von Jahrmärkten kennt. Sie sind speziell darauf ausgelegt, Teile schnell und präzise zu transportieren, und werden in großer Zahl in der Lebensmittelindustrie eingesetzt. Daher eignen sie sich sehr gut für die Maskenherstellung, bei der vor allem Geschwindigkeit und Präzision gefragt sind.
Das sagen unsere Kunden
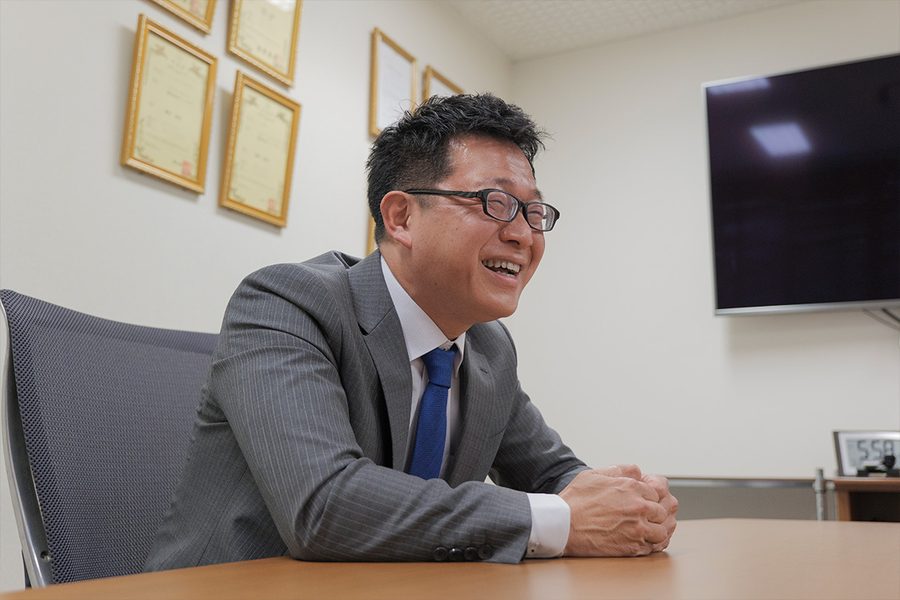
Bei der Entwicklung unserer Waschmaschinen und Kochroboter befanden sich meist Knickarmroboter, darunter auch der duAro im Einsatz. Bei der Maskenproduktion war jedoch vor allem Geschwindigkeit gefragt. In Anbetracht der Anforderungen war klar, dass sich Roboter mit Parallelkinematik hierfür besonders eignen.
Beispielvideo aus der Praxis
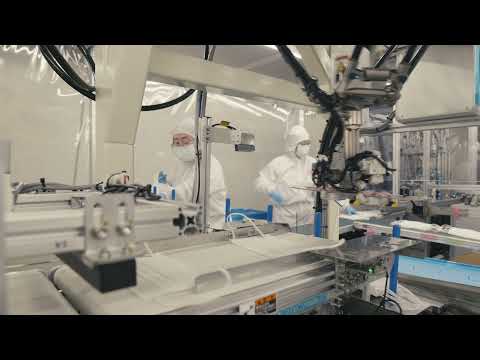
Ein Pick-and-Place-Roboter bei der Arbeit