Advanced manufacturing technologies and skills: they make a cornerstone of a country. Due to the aging society, skill transfer of expert technicians who are responsible for these advancements may be at risk in the near future ———— Currently, many companies in the manufacturing industry are raising a red flag to this problem. And it is a problem not only for Japan but for many developed countries treading on the border of the 100-year-life era.
In this light, a new robot system that shows promise in solving the problem of skill transfer has been unveiled. Kawasaki put on display its new robot system during the International Robot Exhibition (iREX) 2017 (Nov. 29–Dec. 2 at Tokyo Big Site) and they named this system the “Successor.” What kind of a robot system is it?
Realizing a world where robots become the “disciple” of a craftsman
Kawasaki is a leading manufacturer that originally began producing the first domestic industrial robots in 1969. Now, their market share in the industrial robot business ranks in the top five worldwide. Mr. Yasuhiko Hashimoto, the Managing Executive Officer at Kawasaki, General Manager of the Robot Division, and also the person in charge of the development of the Successor, talks about his motivation for taking on the challenge of developing the system.
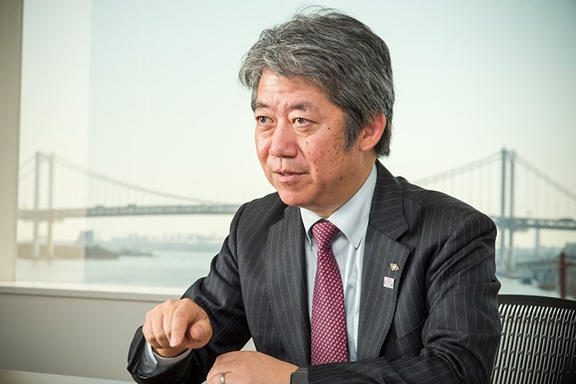
“The Successor allows for streamlining workflow in fields that were previously difficult to automate through the use of robots. It also realizes passing on the precious skills of the master craftsmen who have supported Japan’s culture of manufacturing to later generations. The system can also contribute to securing labor force by utilizing robots. The name, the “Successor”, stands for three meanings; a robot ‘inherits skills’, and those ‘skills are conveyed’ to young technicians through the robot, and finally, it broadens the scope of robot application, ‘spreading new concepts to the world.’”
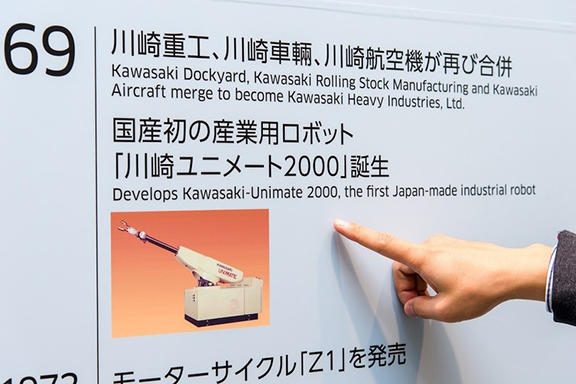
The innovative solution the Successor enables a worker to personally operate the robotic arm remotely using a dedicated operation device (similar to a controller). The shape of the device differs depending on applications and just by performing actual factory work using the controller, the robot learns of the subtle nuances in the human’s movements during the task and reproduces those movements. The sensory feedback capability lets users feel the weight and vibrations of the work being done through the robot arm as if the work was actually being done by hand.This remote-control device can also, through the camera and microphone—serving as the craftsman’s eyes and ears— comprehensively capture information, record the state of having correctly completed work, and reproduce the entire process.
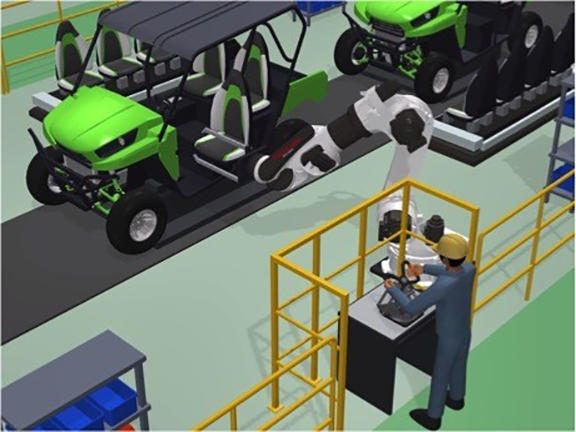
“It may not be common knowledge, but even to this day, robots are not suited to do a number of tasks. For example, the process of equipping a car seat to a car. Since there are subtle variations to the mounting position depending on the vehicle, humans determine the correct position using the feeling from their palms, and only then the car seat can be equipped.
Although it may be easy for human beings, it is a different story for robots that specialize in accurately repeating the same preset tasks. Robots are usually unable to deal with tasks that required judgment at various situations every time. When using the Successor, as the humans repeat tasks, it accumulates data such as positioning, speed, and acceleration. By analyzing these data, the robot is able to learn the ‘tricks of the trade.’”(Yasuhiko Hashimoto)
The unresolved problem of tasks industrial robots cannot perform
Why were these tasks only doable by humans?
Conventionally, when making a robot do a certain task, the common practice was to have specialist engineers observe a human’s complex movements and program these observations into the robot. With this method, it was difficult to reproduce processes which called for craftsmen to rely on their sense of touch or hearing, or other processes dependent on the combination of multiple senses in order to successfully complete the work. Additionally, there was also the problem of programming requiring a certain amount of time and cost, making it infeasible to use robots for small-scale production (having humans do the work costs less).
The Successor will allow the robot to learn and reproduce the movements of humans, so no engineer is necessary to program the robot. Mr. Hashimoto says that this would make it possible for robotization to expand even in fields where robotization was considered difficult, such as the production of small quantities of a large variety of goods in SMEs, or the production of custom-made products with differing product specifications.
The Successor’s characteristic remote operation feature will bring various benefits to industrial workplaces, one of which is a worker’s liberation from harsh environments. Since the worker can operate the robot through the remote-control device, there is no need to stay around the robot. As a result, coordinated work between large robots and humans can be carried out safely. In addition, tasks that require working in harsh environments such as those with dust and high temperatures, or handling heavy loads can be drastically reduced.
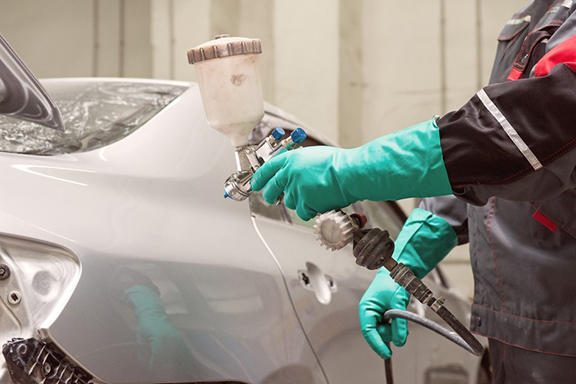
Furthermore, if a robot can learn how humans work and extend the gamut of its automatic operation capabilities, then the range of operations by humans will decrease. Consequently, one technician can then supervise and operate multiple robots at the same time, which dramatically increases the efficiency of production per capita.
Revisiting the scope of work that robots cannot do
Why only now, in 2017, is the practicality of the Successor being put to use? It is not strange to think that the idea of combining remote operation with robot automation would have come about even earlier.
Mr. Hashimoto smiles bitterly at this question. “This is the Columbus egg of the industrial robot world.” At Kawasaki, the so-called master/slave control technology meaning a robot moves based on unidirectional communication from a master, has been in development since the 1980s, while work was also being done in tandem on automation technology. However, Mr. Hashimoto analyzes that perhaps combining these individual technologies and coming up with the idea to realize “automation and learning of craftsman skills” were not so prevalent in the industrial robot world.
Since the Successor is built upon existing technology, its development to practical usage took an exceptionally short period of less than two years. A big part of this is the fact that Kawasaki had the master/slave technology, the automation technology, as well as the AI. “We already possessed the component technologies and knew them well.” (Mr. Hashimoto)
“Behind the decision to come out with the approach for the Successor to ‘reproduce the skills of expert technicians,’ now was the will of the company to promote the implementation of robots even in areas where it had been difficult in the past.
According to statistical data, the number of industrial robots used per 10,000 employees in the manufacturing industry is about 300 in Japan. Even in Korea, where they are most advanced in the world in this field, it is about 600 units (Source: the International Federation of Robotics). As for the automation of the manufacturing industry, I believe there are many more areas still left behind. With the Successor, we believe that we can raise this number to a standard of 1000, or even 2000 units.” (Mr. Hashimoto)
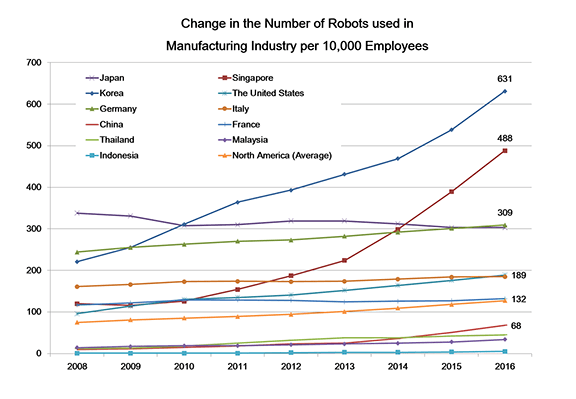
Successor opens the door to the near future where humans and industrial robots “collaborate”
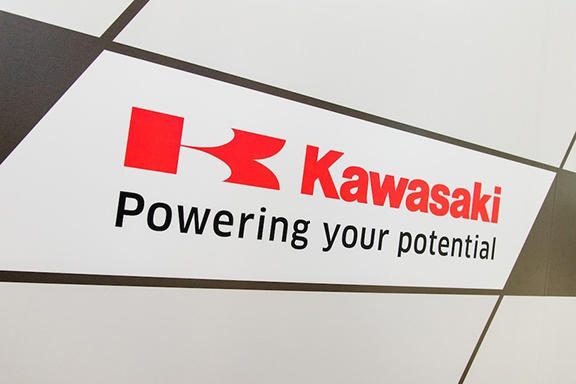
With the implementation of machine learning technology of AI into the Successor’s system, Kawasaki is confident of realizing that robots automatically learn through repetitions of workers’ remote-operated tasks and enabling them to acquire skills.
If the Successor can “master” techniques through AI, a robot will be able to distinguish between correctly completed work and failed work, just like its human parent. Then, when comes time for the human to become the disciple, they will be able to “learn” the correct methods from the Successor. With the Successor as the intermediary, some form of skill transfer will become a reality. It may sound like an event from a science fiction world, but this is a real use case, a future robot industrial society that Kawasaki envisions.
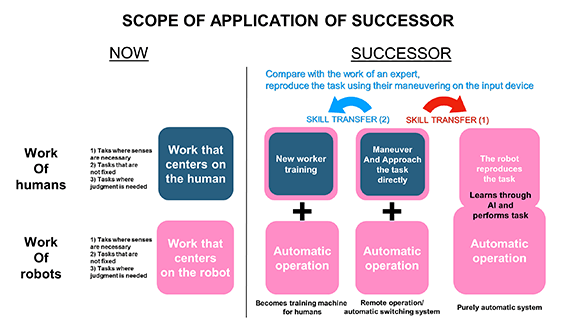
The sales of the Successor will be limited to selected customers in 2018. The release to the general market is targeted at 2019. Other details such as the price are to be determined.
(Text: Hajime Kato; Photos: Kiyotaka Okada)
Read the original article on BUSINESS INSIDER JAPAN 11.29.2017 * Available in Japanese.