What kind of operations are robots capable of?
Today industrial robots are often featured on TV and other media, and the opportunity to see industrial robots is gradually increasing. However, we guess that most of you have not yet seen the real performance at actual workplaces. Although Japan has become the so-called “Robot Kingdom”, such an opportunity is still limited in everyday life unless one has worked at factories equipped with robots.
This article introduces the inside of the Robot Showroom of Kawasaki Heavy Industries, or Kawasaki, in the Nishi-Kobe Works. The Showroom exhibits how industrial robots are working in actual workplaces. Now let’s take a look at their performances.
Sneaking in the private showroom
The Kawasaki Nishi-Kobe Works is located in the West part of Kobe City, Hyogo. In addition to hydraulic components and hydraulic marine machinery, robots are manufactured there. Kawasaki’s large showroom of robots is located in the robot production site, and the showroom staff will guide visitors to show a variety of industrial robots.
*This facility is for the companies who consider the implementation of robots, and it is not open to the public.
Once the visitors enter this robot production site, there is a full view of the showroom on the mezzanine level. The view of a number of large robots – more than 3 meters long with the fully stretched arm – that are simultaneously in operation is quite extraordinary.
Aligning robots closely with each other to minimize the space – The assembling line of automobile bodies
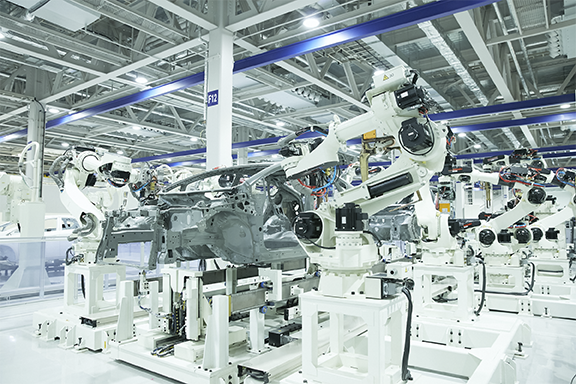
The most advanced fields in terms of the utilization of industrial robots are automobile factories. The first section that welcomes the visitors is the assembling line for automobile bodies.
At this section, the B and CX series, the main robots for spot welding, are in action.
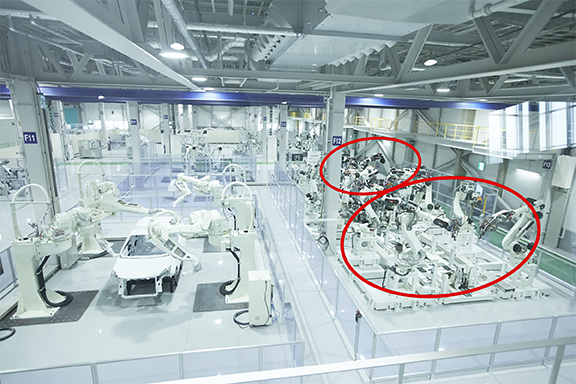
The B and CX series robots are on the right side of the above photo. The robots marked with a red circle respectively handle a vehicle body. The robots are uniquely and closely positioned in a limited space: 2 robots each on right and left side, total 4 robots at the front and 6 robots each on right and left, total 12 robots at the back.
The 4 robots at the front are the CX series. They are manufactured in a factory in Suzhou, China where robots manufacture robots. For its light-weight arm powered by the advanced anti-vibration control system, the robots can move their arm at a high-speed from one place to another regardless of the distance.
The 12 robots at the back are the B series. There is a space inside the arm to store cables without interfering each other. Because the base is designed small, a number of robots can be installed closely with each other in a limited space. It shortens the production line to one third and significantly reduces the cost for space and establishing the peripherals. As seen from this case, various cost-cutting efforts are made in the design of robots’ structures and production lines.
Welding technology is improving
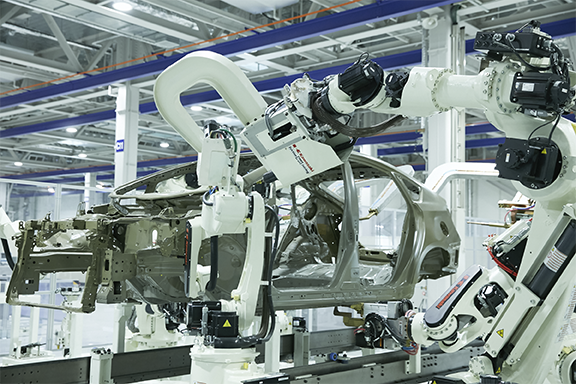
In the automobile production processes, welding is applied to thousands of points during assembling the body, and therefore the welding is a very important process. Have you ever heard of the Friction Spot Joining (FSJ) which Kawasaki developed for this process? FSJ is a process that uses force and high-speed rotation of a FSJ gun to generate friction heat and then joins softened materials. It is an ideal method for joining aluminum alloys and the like that is often used for hoods at automobile factories. This robot operating FSJ is also the CX series introduced at the previous body assembling line.
In this site, robots set the work object in position and then replace their robot hand (like our fingers) to a FSJ gun by themselves.
A robot rotates the FSJ gun at a high speed like a drill to generate friction heat and operates FSJ.
This method does not require the power cables, cooling hose pipes and high current which are required for traditional spot welding, and as a result significantly reduces the facility operation and running cost.
Automating hard labor with robots – Lifting up and down heavy objects up to 500 kg
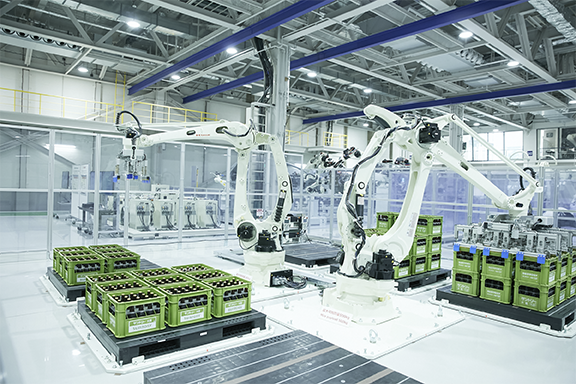
The robots which were carrying many beer cases at once are the CP series designed for palletizing. The operation speed may surprise you. The palletizing capacity for CP180L on the left is 2,050 cycles per hour and it is regarded as the fastest in the same class within the industry. In other words, the robot can move the range of 40cm-hign and 2m-wide holding a 130 kg object within 2 seconds. If humans do this work, it may end up hurting the back. Needless to say, it is a robot and there is no need to worry about it.
In this video, CP500L robots are palletizing 9 beer cases at a time.
The payload for CP500L is 500 kg. While CP180L can handle 3 beer cases, CP500L can handle 9 cases. The demonstration showed the CP series robots transferring beer cases. The robots are able to handle other various objects as well by using the hands specifically designed for the purpose.
Identifying and quickly sorting products without errors even for long hours
The Y series, the parallel link type, is a high-speed picking robot. In the demonstration, the robot used a vision camera to identify objects with images and then sorted them by shape (3 types: a circle, a triangle, and a square) or accurately sorted dice by a number appeared on the top. In the actual workplaces, the robot not only sorts several products but also eliminates defectives.
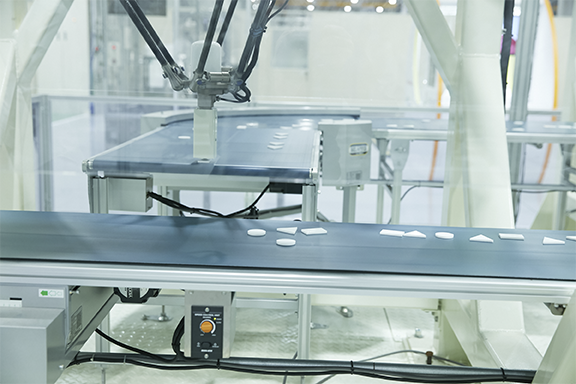
The robot aligns parts delivered on a conveyor belt by the shape.
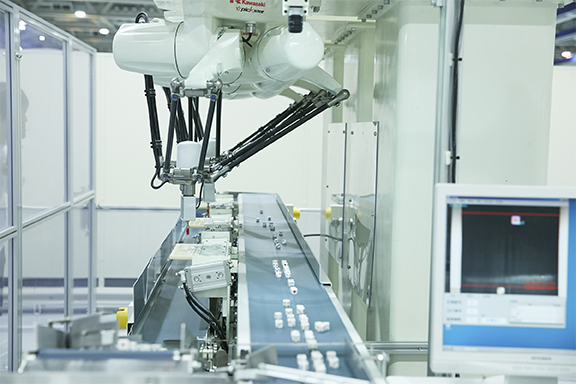
3 robots pick up a pair of dice with the number that each of them is assigned (there are three pairs: 1 and 2, 3 and 4, and 5 and 6).
These parallel link type robots are suitable for operations lining small objects at high-speed. If humans quickly handle simple work, there may be careless mistakes. However, robots have unlimited power of concentration. The current Y series robots are widely used in the food, pharmaceutical and cosmetics industries.
Robots collaborating with each other to elaborately paint
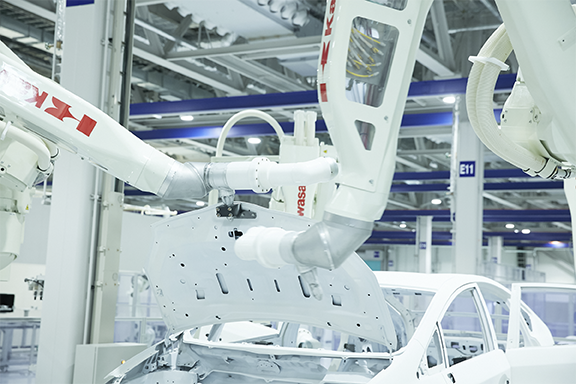
In this booth, the K series robots specializing in painting were in operation. There are 2 processes to paint an automobile body: one for outside and another for inside. We saw one robot with a tool attached on its arm opened and closed the door and hood of the car, while another robot painted the exterior and the interior of the car body. Two robots worked in a coordinated manner and the majority of the painting process was done only by the robots. The K series has been implemented in actual automobile factories in the same way as it is displayed in this showroom.
The robot at the front opens the rear door and another robot at the back paints the inside of the car body.
Co-existing with humans – Dual-arm SCARA robot “duAro” demonstrating its cooking skill
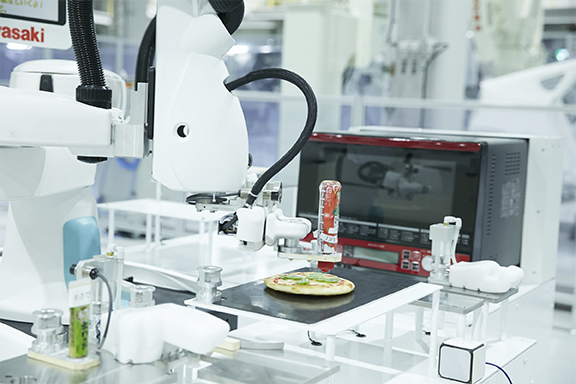
The last booth introduced the dual-arm SCARA robot “duAro” . The duAro is very different from other robots introduced so far since it was designed and developed to safely collaborate with humans in operations. As its motor output is controlled and reduced, safety barriers are not required. The collision detection function of duAro suspends the robot operation immediately when the robot contacts with humans. Also as its arm is made with soft material, it will not hurt humans even by accidentally bumping to them. Because there are casters at the bottom, it requires only one person to move duAro. It needs only power and a small-sized air compressor for its operation, allowing us to consider the implementation in a limited space.
No safety fences around duAro
At the showroom, the robot demonstrated the movement of making sushi and baking pizza. The unique function of this dual-arm robot is its two-hand operation. The automation using robots is developing in the food industry and it will not be long before robots appear in supermarkets and restaurants in the neighbourhood.
The duAro is rhythmically making sushi.
Kawasaki’s Tokyo Showroom is open to the public
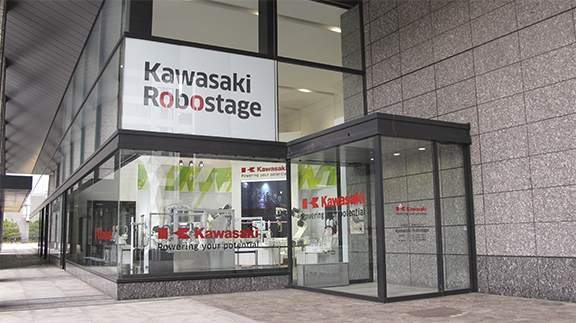
Various areas have started using robots. Not only automobile and electrical & electronic industries which have traditionally used robots, but also other industries have started using robots. The introduction of new robots designed to co-exist with humans will boost the use of robots in commercial facilities as well as at home.
As already mentioned, the Showroom in the Nishi-Kobe Works is not open to the public. The one open to everyone is “Kawasaki Robostage”, located in Odaiba, Tokyo. The visitors can see the latest robots and experience robot attractions there. No reservation is required and its admission is free. Please come and explore the real industrial robots!
Kawasaki Robostage
https://robotics.kawasaki.com/ja1/robostage/en.html