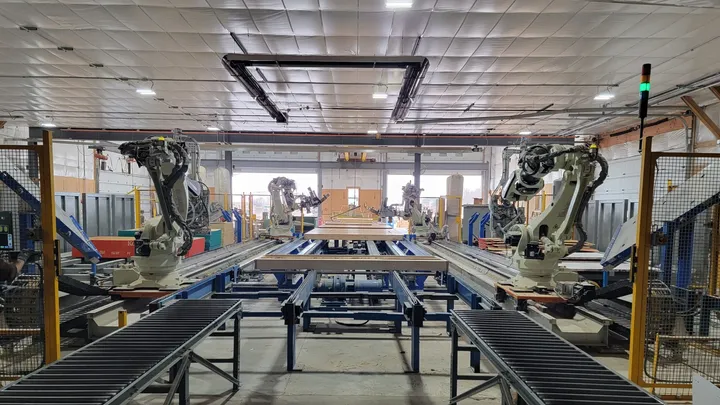
- ApplicazioniAssemblaggio, Movimentazione dei materiali
- Serie robotserie BX/BT
System designed by:
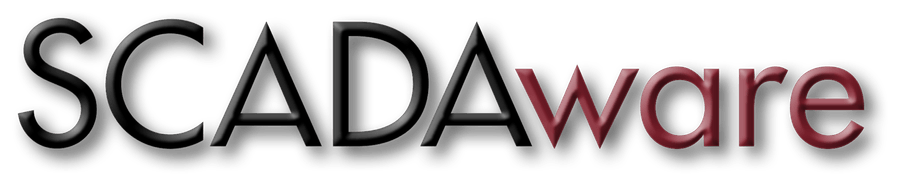
OVERVIEW
Prefabricated homes have recently grown in affordability. This growth has led to increased demand for homes that can be manufactured quickly and inexpensively and assembled on-site. However, that affordability translates to thinner margins for building component manufacturers, especially when they are bidding against each other for the same projects. As many in the industry have learned, the more automated their manufacturing process, the more competitive they become at the bidding table.
Builder Rehkemper & Son contacted Kawasaki integrator SCADAware to help automate their prefabricated home assembly process. In addition to sharpening their competitive edge, they also wanted to minimize their reliance on human labor due to shortages. After reviewing Rehkemper’s manual processes, SCADAware designed a one-of-a-kind system for automating much of the prefabricated wall assembly process using custom software, Kawasaki robots and Güdel rails.
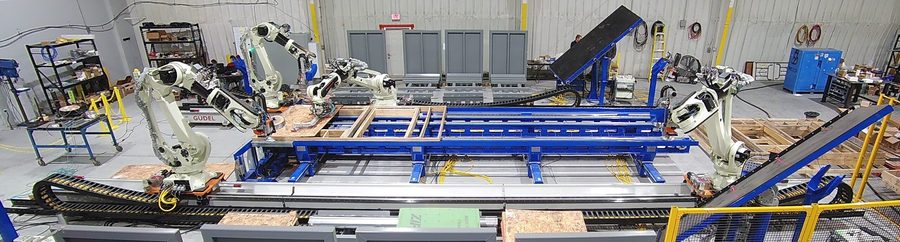
CHALLENGES
Cumbersome material, high precision application
In Rehkemper’s process, oriented strand board (OSB) sheathing is adhered to the prefabricated walls. OSB comes in large, heavy, pressed-wood panels that can be difficult to maneuver. They needed a robotic solution that could accurately place nails to affix the boards to the wooden studs and beams hidden underneath. What made this task so difficult is that, compared to other building materials, wood is notoriously imprecise.
“Wooden boards are often warped; and once you lay OSB down, you can no longer see the where the stud is located. If the nail only holds air, then we’re in trouble,” says Rick Caldwell, president of SCADAware
SOLUTION
- Four Kawasaki BX250L robots mounted to Güdel TrackMotion Floor-3 rails
- Robots attach cumbersome OSB panels to wall frames and carve windows and doors into panels
- Custom SCADAware software dictates cuts for robots
Factory assembly of prefabricated homes is done in two stages. First, wooden studs and beams are sawn and assembled to form the skeletal walls, roof, and floor trusses. The next phase involves applying OSB sheathing to pre-framed walls, nailing the panels to the framework, and carving out holes for windows and doors. The component parts are then shipped to the building site, where they are assembled into a standing structure.
SCADAware engineers wrote custom software that looks at the electronic version of the design of the wall and shows the robot where to nail and cut. The system employs a large, adjustable, motorized table to accommodate framed walls measuring 8 – 14’ high and up to 20’ wide. Single walls are conveyed onto SCADAware’s table, where they are squared against a fixed end stop at the far end. The table’s adjustable edges come together to align the frame top to bottom.
This ensures the wooden stud nearest to the end stop is straight with its physical centerline aligned to within 1/16th of an inch or better of the digital design. There are servo-controlled fingers under the wall to straighten any warped studs. These fingers help align the next 3 studs by sliding up the table’s central rail and applying pressure to straighten each stud.
Meanwhile, two pairs of Kawasaki BX250L robots – each with a reach extending 2,812 millimeters, or just over 9 feet – are mounted on corresponding Güdel TrackMotion Floor-3 (TMF-3) units extending the length of the table on either side. Each Güdel track measures 15 meters and delivers a 12-meter working stroke, allowing all four robots to work together along the entire length of the table.
After the wall is in place, one of the rear robots next to the conveyor uses vacuum heads to pick up a 4 x 8-foot OSB panel and place it over the now straightened studs. Once the first panel is fully attached, the robots and fingers repeat the process until the wall is completely sheathed.
All four robots can easily switch tooling. As one set of robots carves windows and doors into the OSB panel, the other two remove the cut sheathing and transfer it to the scrap heap.
Robots = Reliability
Rehkemper’s process is extremely labor intensive, which made it difficult to find and retain employees. Automation can be the perfect solution for these situations, as manufacturers can rely on robots to work consistently while yielding a high quality product. Kawasaki robots are known in the industry for their reliability and flexibility. Offering a 250 kg payload, Kawasaki BX250L robots can easily lift large, cumbersome OSB walls with ease. Their patented hollow-arm structure provides easy installation, maintenance and minimized wear. Their extended reach, high speeds and advanced motion control technology reduce cycle times.
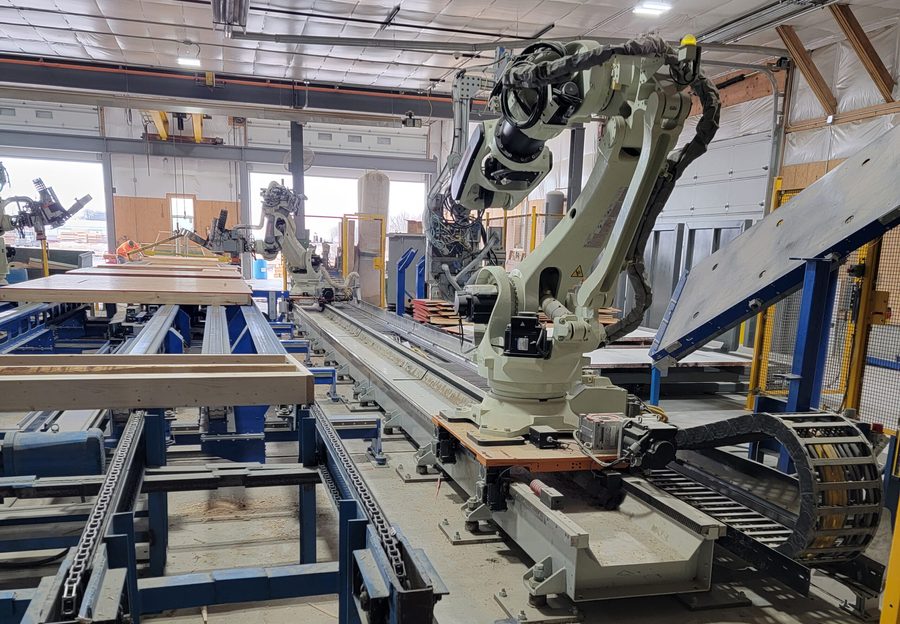
RESULTS
- Efficiency drastically increased
- Throughput increased by at least 25%
- Labor costs reduced
In simulations, the system has shown it can finish assembly of an 8 x 20’ wall in considerably less time than it would typically take two operators to complete — including placing and affixing OSB sheathing and cutting it to form windows and doors. With additional optimization, Caldwell believes the system can do even better.
“A big impetus behind Rehkemper reaching out to us was the difficulty they were having in hiring workers to do these sorts of jobs,” said Caldwell. “But our collective goal was also to help them to compete better and get the job done quicker for less of a cost.”
The speed, versatility, and precision enabled by Güdel’s rail promises to increase throughput by at least 25% with no loss in quality. The improved productivity and reduced labor costs enable contractors like Rehkemper & Son to save money and offer more competitive bids. Currently the track and robot system has increased the linear footage produced each day by 25% with no loss in quality; further adjustments are expected to increase efficiency to 35-40%. An additional benefit is minimizing their reliance on scarce human labor for this process, resulting in less downtime, more precision, and no injuries.