Due to the spread of COVID-19, the logistics industry has seen an explosive increase in the volume of goods handled, and automation in this industry is advancing rapidly with a focus on warehouses. By combining the versatility of robot arms with the mobility of trackless unmanned transport vehicles, Kawasaki can offer measures for the automation and optimization of logistics processes that involve automated warehouses including product receiving and shipping.
Taking on the challenge of the “barriers to warehouse entry and shipment”
in logistics automation
In recent years, factors such as the expansion of the EC market have led to increasingly serious labor shortages in the logistics industry. Logistics labor saving and automation are urgent tasks.
When we talk about logistics labor saving and automation, we tend to focus on transportation and delivery. However, in the series of logistics processes between the supplier, distribution center, and end user, it is actually the processes for warehouse receiving and shipment that require a lot of labor.
Kawasaki is aiming to automate logistics by providing solutions that achieve warehouse labor saving and automation in conjunction with near-future mobility.
Bottlenecks in warehouse automation
In recent years, “automated warehouses” have meant that automation has proceeded rapidly inside warehouses, in the processes from the incoming goods inspections to shipment goods inspections. However, the processes that occur before and after that are still being performed by human workers. These are the unloading, picking and palletizing processes.
Kawasaki’s logistics solutions
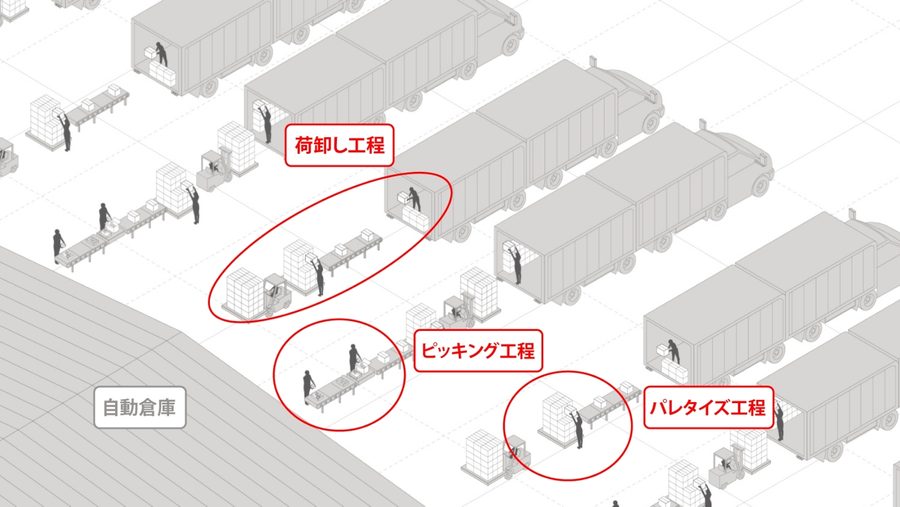
01. Automation of the unloading process
Problems in the conventional unloading process
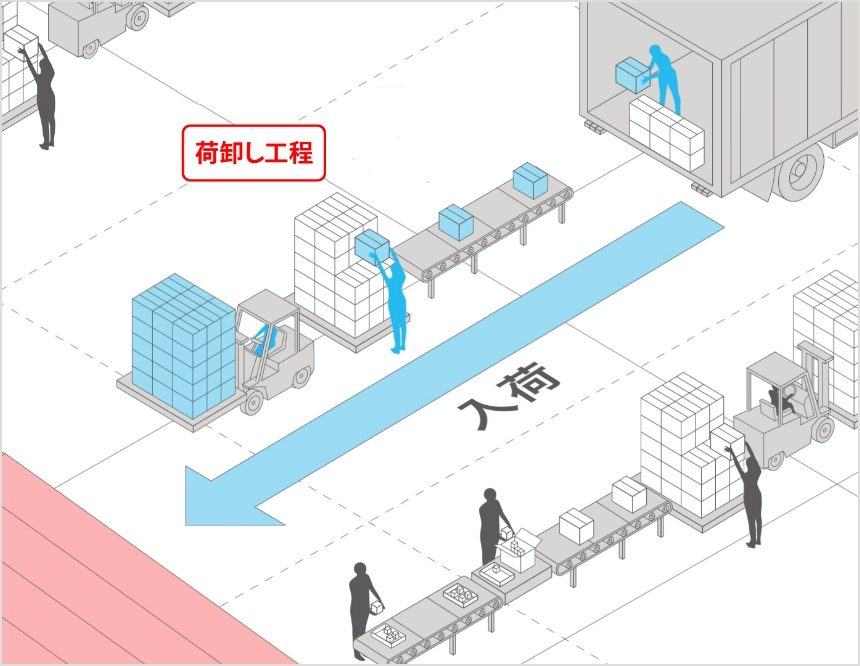
In the unloading process, it is necessary to unload the cargo from a container that has been brought in on a trailer and to restack it. So, why hasn’t this process been automated? The problem has been with how the cargo is loaded in the container.
Inside the container, various boxes of different shapes and sizes are stacked in a way that will prevent the load from collapsing. This made it difficult for machinery to grasp the boxes and restack them.
Up until now, it has been necessary for human workers to go inside the container to pick up and load the cargo onto a belt conveyor that carried the cargo out, or to restack the cargo on a pallet for it to be carried out by a forklift truck.
Kawasaki’s proposed solution for the unloading process
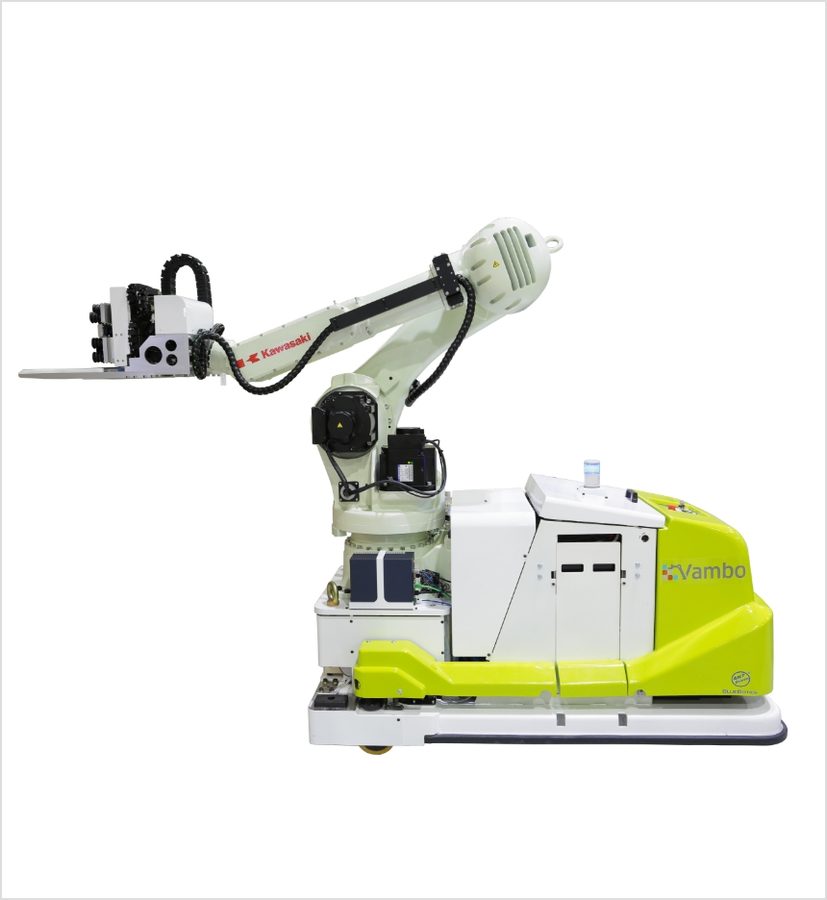
Vambo devanning robot
An unloading/loading robot which combines a robot arm and an unmanned vehicle (AGV). It features a vertical articulated robot arm with a wide operating range and a large weight capacity, a vision sensor that recognizes mixed load cases, and a trackless unmanned vehicle (AGV) that transports the robot arm to the working position in a container of a transport truck.
Automation of the unloading process by Kawasaki
When the Vambo moves into the container, a vision sensor detects the shape of the boxes. It performs picking on boxes of various shapes and sizes with a hand shaped like a dustpan and a robot arm. The boxes can then be placed on a belt conveyor. A palletizing robot then waits at the end of the belt conveyor and transfers the cargo that is unloaded from the container to a pallet for a forklift truck, which completes the unloading. Kawasaki can automate all of these tasks.
02. Automation of the picking process
Problems in the conventional picking process
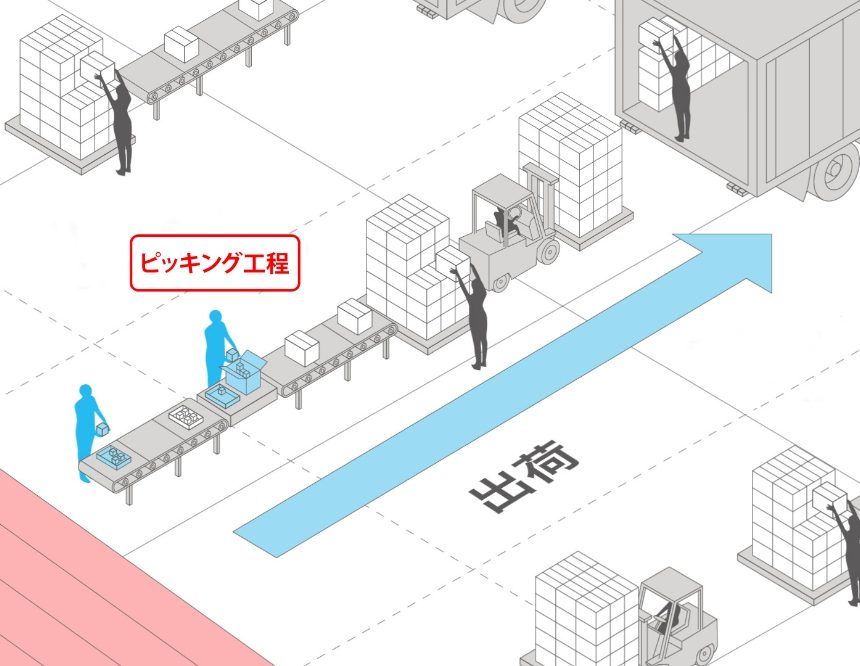
After the inspection of the items for shipping by the “automated warehouse,” the items are placed in a plastic container and delivered out. At present the automation is only up until this point. Human workers have been performing the work to remove the items from the plastic containers and repack them according to the destination, and the work to assemble and pack the boxes for shipping.
Kawasaki’s proposed solution for the picking process
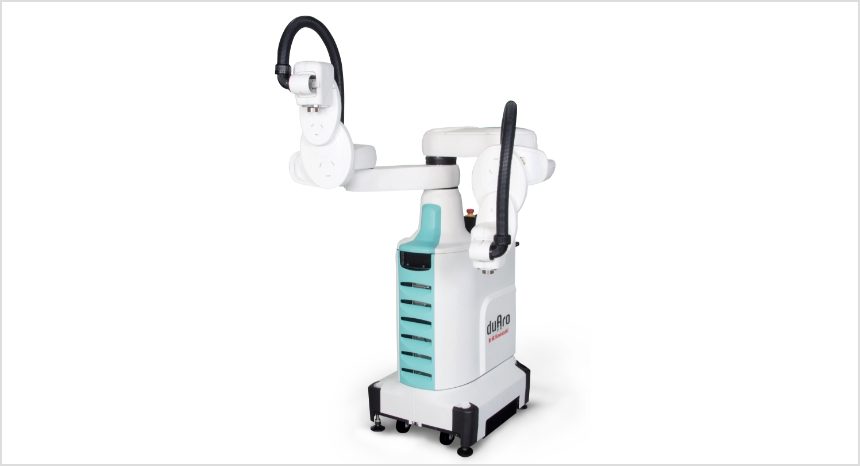
duAro2 dual-arm SCARA robot
A dual-arm SCARA robot that can co-exist and perform collaborative work in the same space as humans. It can work in a compact installation space equivalent to that for one person, and its cart with casters and a built-in controller can be easily moved and installed. By utilizing both arms, it is possible to perform picking and repacking work on packages of various shapes and sizes.
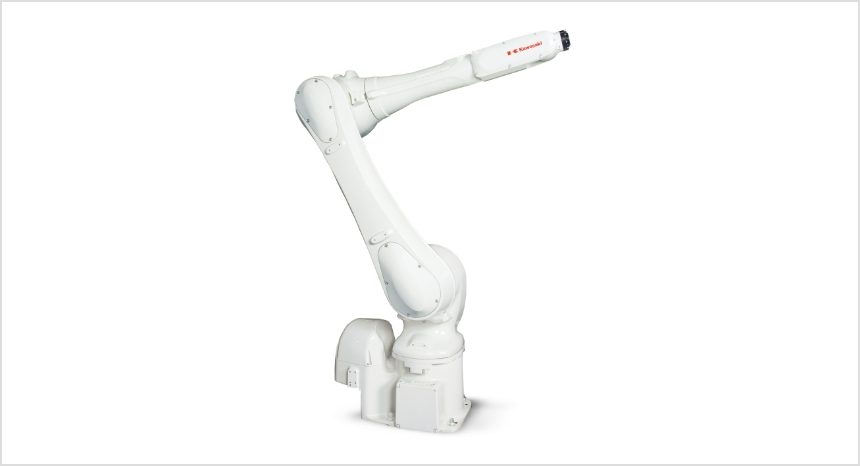
RS013N six-axis vertical articulated robot
The RS013N is characterized by the three-dimensional movement of a vertical articulated robot.
Automation of the picking process by Kawasaki. Cargo packed in plastic containers after the completion of the shipping item inspection. The RS013N assembles boxes, and duAro2 performs the packing from the plastic containers into the boxes. This automates the picking and packing processes that have previously been done manually.
03. Automation of the palletizing process
Problems in the conventional palletizing process
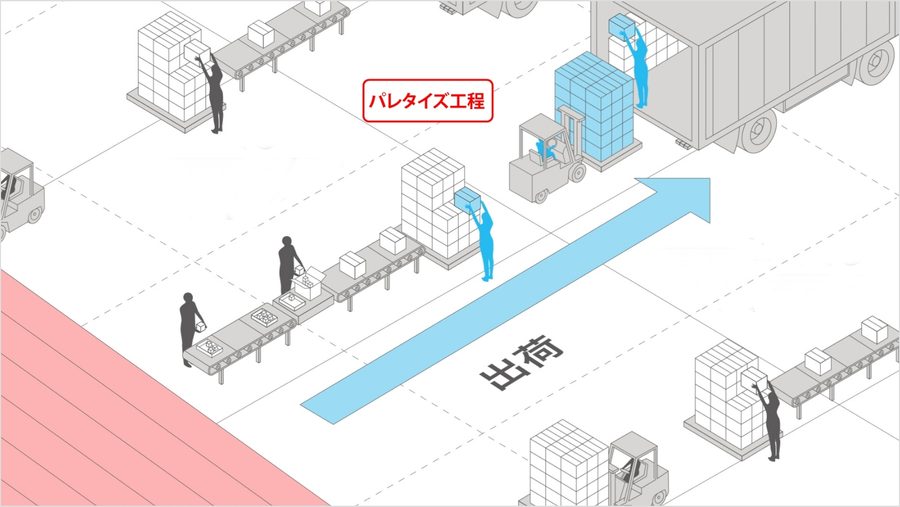
The final process is work called palletizing, in which the boxes filled with cargo are loaded onto pallets. The loading must be quick, stable and withstand the pressure, and performing the work manually is a heavy burden.
Kawasaki’s proposed solution for the palletizing process
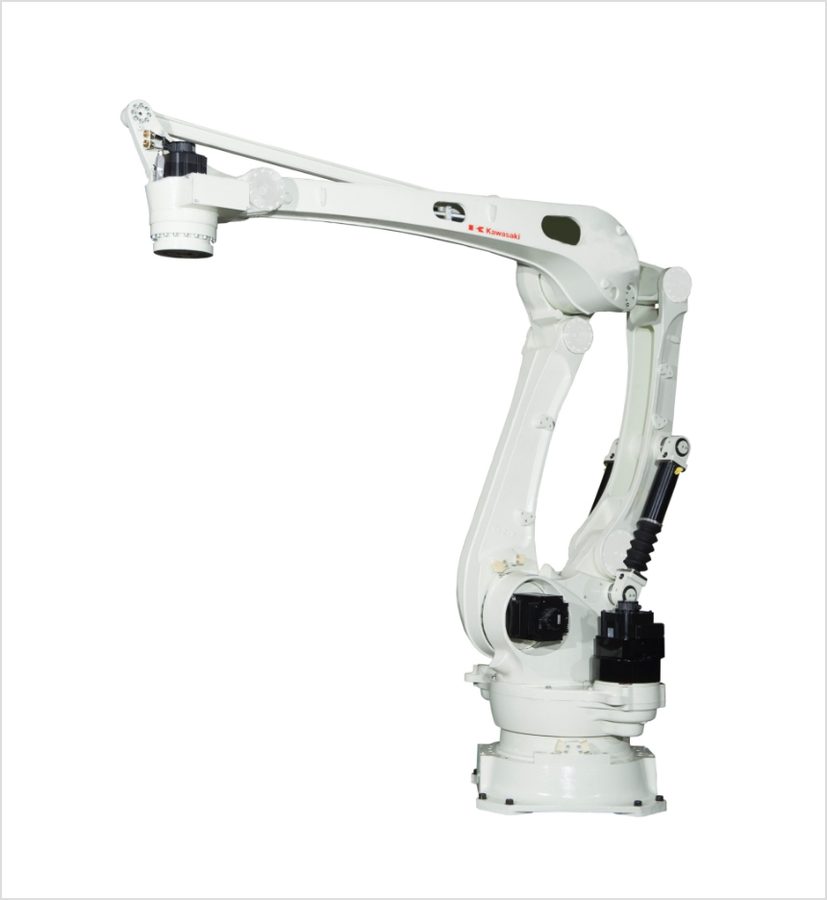
CP180L palletizing robot
This high-speed palletizing robot from Kawasaki boasts the industry’s fastest processing capacity. It supports the diverse needs of various industries, such as food, pharmaceuticals, and printed materials, as well as the production of diverse products in small quantities.
Automation of the palletizing process proposed by Kawasaki
The boxes brought on a conveyor are aligned in their designated positions by the RS series robot arm. The palletizing robot then quickly and accurately grasps the aligned boxes and stacks them appropriately on the pallet.
The “unloading,” “picking,” and “palletizing” processes in logistics have so far required a large number of human workers. Kawasaki will contribute to improved efficiency in supply chains by working on “automation and labor-saving” in these processes.