What is “duAro”, the collaborative robot developed by Kawasaki?
Kawasaki Heavy Industries, or Kawasaki, has developed a large number of industrial robots since the launching of its first domestically manufactured industrial robot, the Kawasaki Unimate 2000 in 1969. Such Kawasaki, a pioneer in industrial robots in Japan, released the dual-arm SCARA robot* “duAro”, in June 2015. duAro is the result of the pursuit of the ultimate user-/human-friendly robot.
(*Robot arms moving horizontally.)
Mr. Shogo Hasegawa from Kawasaki was involved in the project since its conception and took part in its development. He will tell us the secrets behind the birth of duAro. Through his account, you will see the extraordinary philosophy of a company which has been pushing the boundaries of the industrial robot field in Japan for more than 50 years.
Companies’ needs and transformation in the development process
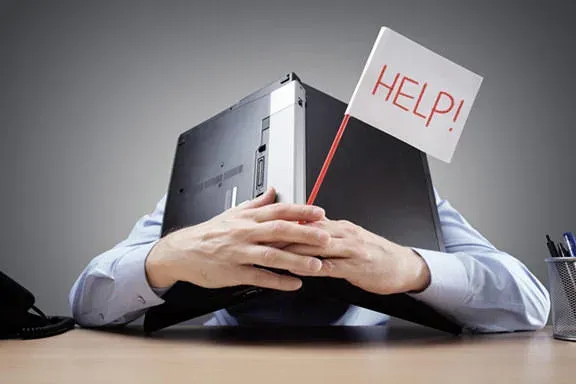
“So far, based on the technology and expertise we accumulated throughout the years, our company has been developing products in a product-oriented manner; however, due to social changes – such as chronic labor shortage – the company started shifting to be more market-oriented in order to fulfill the customers’ real needs. As a result, some changes occurred in our development department, and the system implementation department started to become the center for the new product development” describes Mr. Hasegawa.
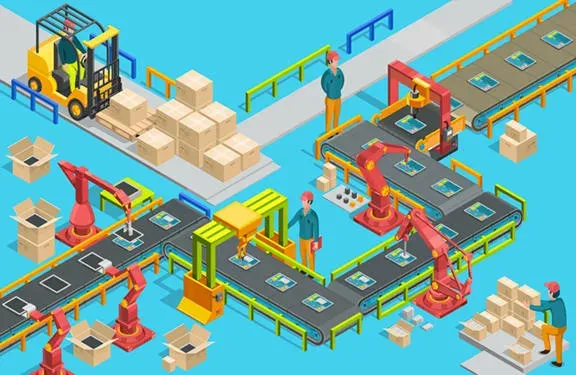
The transformation of the development process was one of the biggest factors that led to duAro’s creation.
He explains, “Back then, I was in charge of developing a new small-size low-cost product, very different from duAro, but I couldn’t think of any good ideas, and the project was not going very well. I first directly got involved with duAro when an electronic parts manufacturer asked me for implementing Kawasaki robots to their factory.”
The first thing Mr. Hasegawa did after the client’s requirement was to visit their manufacturing site where they wanted the robot to conduct a thorough assessment of their needs. Based on the information he gathered, he carefully examined “what kind of robot could meet that company’s demands.” He says, however, there were too many obstacles in order to use the conventional robots they had available at that time.
Issues hindering the use of conventional industrial robots
“The client told me they would use the robot for manufacturing products that are newly released to the public on a three-month basis. Conventional general-purpose robots are suitable for the mass production of big things, for long life cycle products such as those of automobiles; they are not suitable for manufacturing products that change over a short span of time,” explains Mr. Hasegawa.
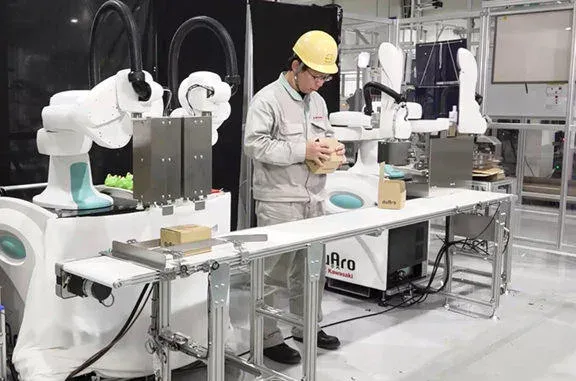
“One of the reason” – he continues – “is that it usually takes around half a year to implement robots and to start operation. In order to set up a production line, space for robots needs to be secured and there needs to be safety fences separating humans and robots. This means that the factory workflow may have to be rearranged. So it could cost a considerable amount of money and time not only on the robots, but also on adjusting and implementing a new process that covers the period until the robot is in operation. For instance, let’s suppose a customer wants to install one single robot; based on our calculation, the cost for the robot peripheral integration alone (i.e. installation and setup necessary for its operation) is three times that of the robot itself. Consequently, robot implementation could be quite difficult in cases of short life cycle products with frequent model changes. This happens because we can’t counterbalance the cost and speed of implementation due to the fact that it is necessary to modify the robot’s operating environment to match the product changes every time they take place.”
So, how did Kawasaki’s duAro find the solution to those problems left unsolved by conventional industrial robots?
duAro’s coexistence with people
Mr. Hasegawa says the answer to that question is duAro’s major feature: coexistence.

“When we started developing duAro, we brought up the concept of “human-friendly robot”. At factories where robots are not employed, no matter which production site you go to, people still work as they did in the past. However, if duAro could perform tasks occupying the same amount of space as one employee, then we would be able to implement it without having to rearrange neither the workflow nor the production line. By enabling to have a robot side by side with a worker, we cleared the two biggest obstacles for implementation in our way: time and cost.”
There were even some secrets in the very own dual-arm SCARA structure chosen for creating the human-friendly robot:
“We realized that almost every work was a combination of horizontal tasks when observing the production site. Based on that, we eliminated vertical tasks and opted for a SCARA type robot due to its ability to perform simple horizontal movements. duAro is a dual-arm robot and its arms come out from one single axis. duAro has two arms because it is made to cover the work of a person performing tasks with two arms. Moreover, having the two arms from a single axis makes them less prone to interfere with each other and allows duAro to perform coordinated movements** which are quite difficult for conventional SCARA robots. Naturally, we paid close attention to duAro’s design in order to ensure its safety since it was going to be used in the same place where people work: the arms are covered with a urethane cushion as not to hurt the person working next to it in case of contact.”
(**Two or more robots recognize each other’s relative position and work together to perform an action.)
Development of an application that allow on-site staff to directly operate robots
Mr. Hasegawa comments that, in addition to safety, they also made intense effort to make duAro easy to use.
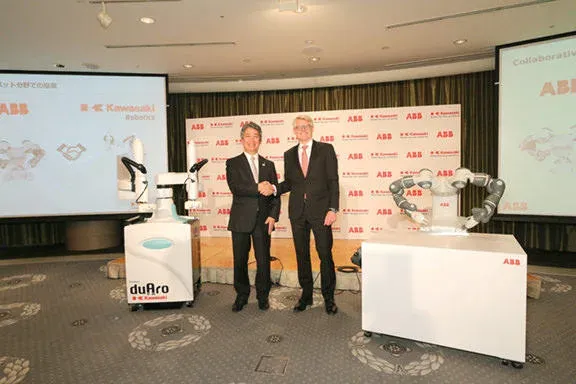
“For short life cycle products, programming to robots has to be done every time product models change and this process becomes a burden. And, until now, the programming needs to be conducted by a specialist engineer to handle even the smallest of changes. However, along with duAro’s development, we also developed an application that enables any person to easily program tasks to duAro. Not only can you use a conventional teaching pendant, which requires specialized technical background, but you can also perform teaching operations via a tablet device. Additionally, duAro is also equipped with a direct teaching function in which the robot memorizes movements that the person directly move its arms. The fact that duAro is a SCARA robot with just a few axes (only for horizontal movement) is a helping factor for such function.”
“We applied ourselves to make duAro easier to implement in other ways too. duAro has an integrated controller*** mounted on a wheeled base which allows a single person to carry the robot on any flat surface.”
(*** Industrial robots usually need a separate controller to run.)
Through this process of trying to pursuit a user-friendly robot, duAro solved the issues of previous industrial robots and came to be the right product to answer the client’s need.
duAro’s outlook and Kawasaki’s vision
“Currently, we are conducting further development in order to make duAro even easier to implement in various companies. First, we are increasing the variation of arms. duAro will thus be able to perform tasks other than horizontal ones and tackle the demands of a wide range of areas. Second, we are adding new functions such as voice recognition. By adding a voice command function which recognizes voiceprint, workers will be able to tell the robot when to start and shut off using just their voice. We will continue on developing products tailored to our customers’ needs.”
Mr. Hasegawa described to us a future where more and more production sites will have robots working side by side with people. As if bringing this future closer, in November 2017, Kawasaki announced in a press release that it will join forces with industrial robot manufacturer ABB in the field of collaborative robots. Mr. Hasegawa commented on the sequence of events that led to the cooperation deal with the long-established Swiss company.

“With the increase of companies implementing and using robots, we will need to improve the safety and operability of our products even more. From now on, instead of working alone, it is important for companies of our field to cooperate with each other and establish standards for difficult technical requirement imposed by customers. I hope we can make good use of this collaborative endeavor to drive forward the production of robots that are even easier to use, and easier to implement. Kawasaki is keen to jointly work on this field not only with ABB but also with the entire industry, to develop robots that are safe and easy to operate for customers, and by disseminating their use, we can contribute to securing the labor force which will support Japan in the future.”