“Kawasaki-Unimate”, Japan’s first domestically manufactured industrial robot
Industrial robots have strongly supported businesses in Japan. Although today it becomes common for many companies to implement robot systems, the road to widespread adoption was by no means a smooth one. As a matter of fact, the first industrial robot domestically manufactured in Japan was the Kawasaki-Unimate launched by Kawasaki Heavy Industries, or Kawasaki, in 1969. This article will introduce some of the stories behind the development of this home-grown Unimate.
An industrial robot is a machine with multiple, freely-moveable, operable joints capable of performing tasks such as welding and handling heavy objects. Once movements are configured through teaching and programming, industrial robots can continue their operations accurately for hours on end, making them essential to manufacturing sites these days. For more information about the types and mechanisms of industrial robots, have a look at some related articles:
What Kinds of Industrial Robots Are There? A Guide on the Features of the Major 6 Types
How Are Industrial Robots Built? A Guide on the Components and the Movement of Robot Arms
The history of industrial robots began in the 1950s. American engineer G. C. Devol, Jr. came up with the basic concept of industrial robots—automating repetitions of simple tasks—and applied for a patent in 1954. Then, J. F. Engelberger, an entrepreneur who paid a great deal of attention to this concept, established the venture company Unimation, Inc. The Unimate, developed by the company, became the world’s first industrial robot and for this achievement, Engelberger came to be known as “the father of robotics”.
Kawasaki signed a technical license agreement with Unimation in 1968. Following this, Kawasaki sent its engineers to the United States, tasking them with acquiring technical knowledge and importing sample machines back to its factory in Japan for continual research and development, a process which would eventually commence the domestic manufacturing of the Unimate. One year later, in 1969, the first industrial robot domestically manufactured in Japan was completed. This is where the history of Kawasaki Robots begins.
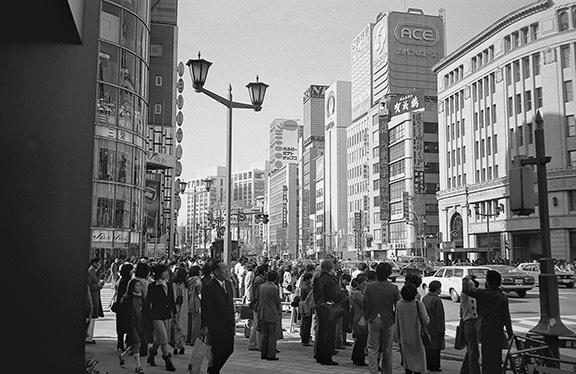
During this time, Japan found itself in a period of rapid economic growth. It was a time when labor shortage became a major social issue and people from rural areas were making their way to the city en masse to work. Young workers of these groups were appreciated and called “golden eggs”.
The name “Unimate” means “working mate with universal capability”. Taking a look at a brochure from back then shows how it was introduced with the concept of being “a new type of worker that would solve labor shortage issues”, an indication of the high expectations for robots to save manpower. While the cause of labor shortage today, namely an aging population, is different from what it was back then, the roles which society expects industrial robots to play are identical.

The Unimate reaches further as the automotive industry grows
The first-generation “Kawasaki-Unimate 2000”, however, was not sufficient as a high-performance working mate. It was hefty, weighing in at 1.6 tons and measuring 1.6 x 1.2 x 1.3 meters, but its payload was only 12kg. Yet it cost 12 million yen which is equivalent to approximately 80 million yen in today’s currency; it was a very expensive device considering the average initial monthly salary for university graduates was 30,000 yen.
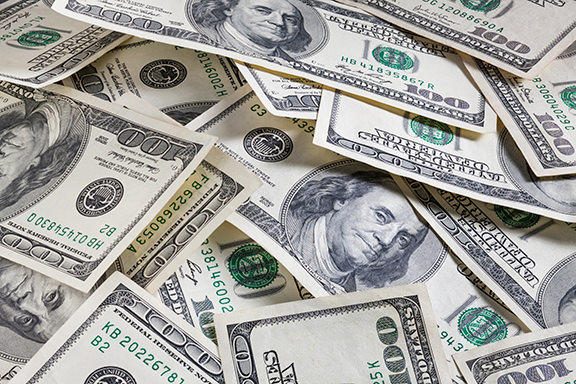
It was the automotive industry that expressed a particularly strong interest in these robots, these pricey machines that had no proven precedent case study of working inside the manufacturing industry. In the most advanced car factories of the day, some manufacturing processes were already automated with dedicated devices. However, whenever the occasion called for a model change, production lines had to be reestablished from scratch, costing both time and money. But with the use of highly versatile robots, all that would change as they could instantly adapt to the model changes by simply having new processes taught to them.
Japan during this period saw a sharp rise in car sales thanks to the effects of rapid motorization; it was becoming more common for a household to own a personal-use car. In order to increase production volume, improving productivity with robots was inevitable.
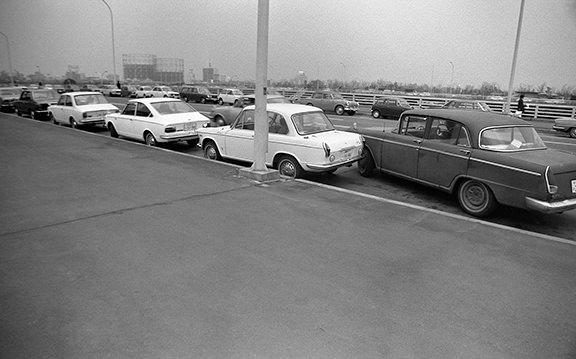
Car manufacturers began their robotic transition by first focusing on automating spot welding lines, a process which required a great deal of manpower. Completing one single automobile requires an average of 4,000 pressed parts to be spot welded, so there were expectations that if this process could be automated it would significantly increase productivity.
However, the first Kawasaki-Unimate 2000, which was manufactured according to its American concept and specifications, needed work in order to fulfill the requirements of Japanese car manufacturers. So, Kawasaki attended to their requests and independently developed the “2630-type”, an upgraded Unimate with six degrees of freedom instead of the previous five and a payload increased from 12kg to 25kg. The 2630-type, literally the first domestically manufactured Unimate, was widely introduced in car factories and became a bestselling machine for years.
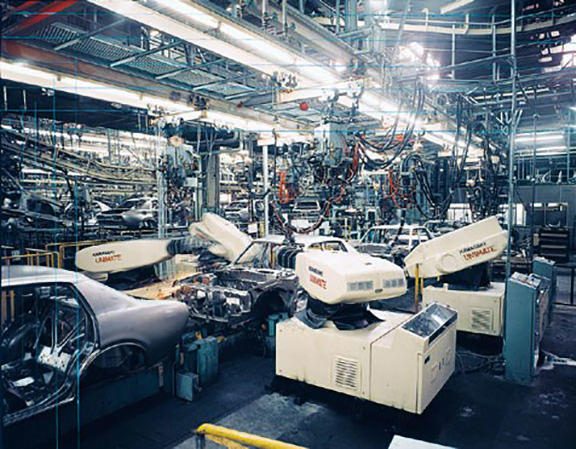
In this fashion, a collaborative relationship with car manufacturers expedited developments in industrial robots.
The achievement and legacy of the Unimate
It has been 50 years since the birth of Japan’s first domestically manufactured industrial robot, the Kawasaki-Unimate. Industrial robots began to steadily circulate when the automotive industry took the lead in utilizing them, and they have gone on to expand their playing field, moving into other industries such as the electrical and electronics industry and supporting manufacturing in Japan.
Not only did factory automation improve productivity, it also liberated workers from arduous jobs including spot welding and painting. Robots would be responsible for handling Japan’s so-called “3K” (kitsui, or “hard”; kitanai, or “dirty”; and kiken, or “dangerous”) jobs as well as simple repetitive tasks, allowing humans to concentrate on more sophisticated tasks that require decision-making.
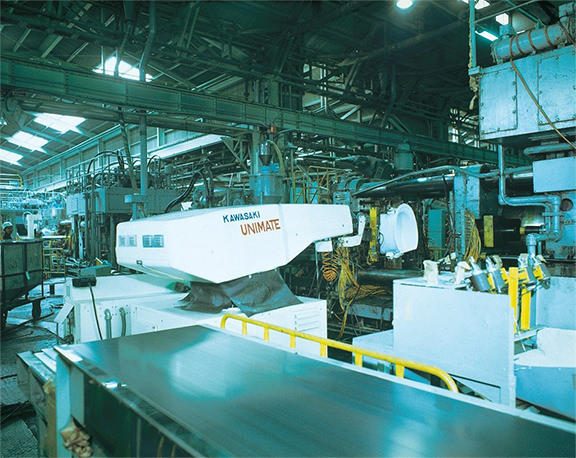
Today, five decades after the launch of the Kawasaki-Unimate, the range of robotic applications is still expanding. Robots are no longer confined to working within the walls of factories; they are being increasingly utilized in commercial facilities and at home as well.
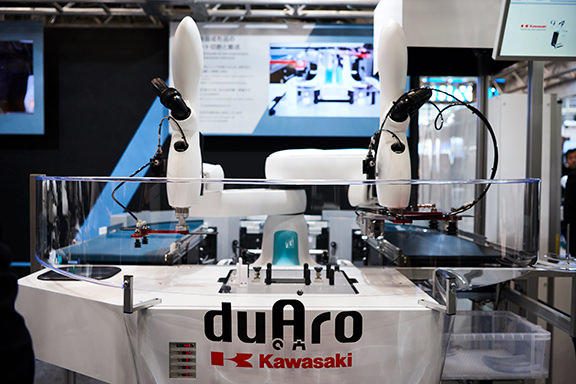
Robots have long been considered a supporter for humans. The concept behind the dual-arm SCARA robot, “duAro”, launched by Kawasaki in 2015 is for it to be “a robot capable of collaboratively working with humans”. The duAro can perform tasks which normally require both hands of a human, perform them right next to humans, and above all, work while posing less of a risk of harming humans. Similar to the way the Unimate set factory workers free from physically demanding jobs, Kawasaki Robots will continue to evolve, responding to the needs of society and to help humans and society.