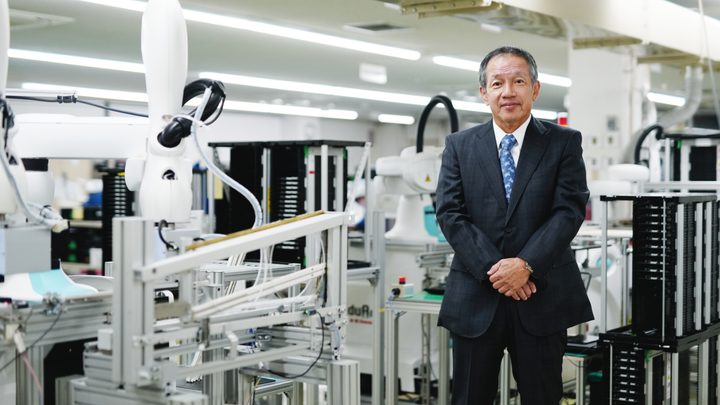
- IndustriesElectronics
- ApplicationsAssembly
- Robot SeriesRS series, duAro series
Robot user: Toyo Electric Corporation
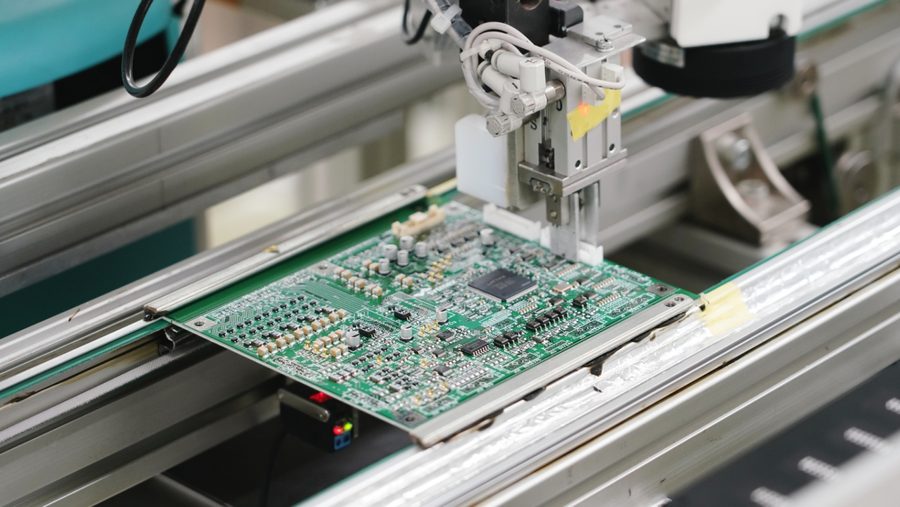
It was in 1969 when the Kawasaki-Unimate 2000 was announced as Japan’s first industrial robot.
In that same year, Toyo Electric Corporation was established, with the assembly and manufacturing of electrical components for industrial robots as a pillar of its business.
From the early days of industrial robots, they have been electronics experts who have worked on the harnesses and printed circuit boards that could be described as the robot veins and nerves. The company uses its extensive knowledge of robotics to construct unique automation systems.
Introduction background/issues:
A collaborative type robot that is ideal for the assembly processes for lightweight and delicate electrical components
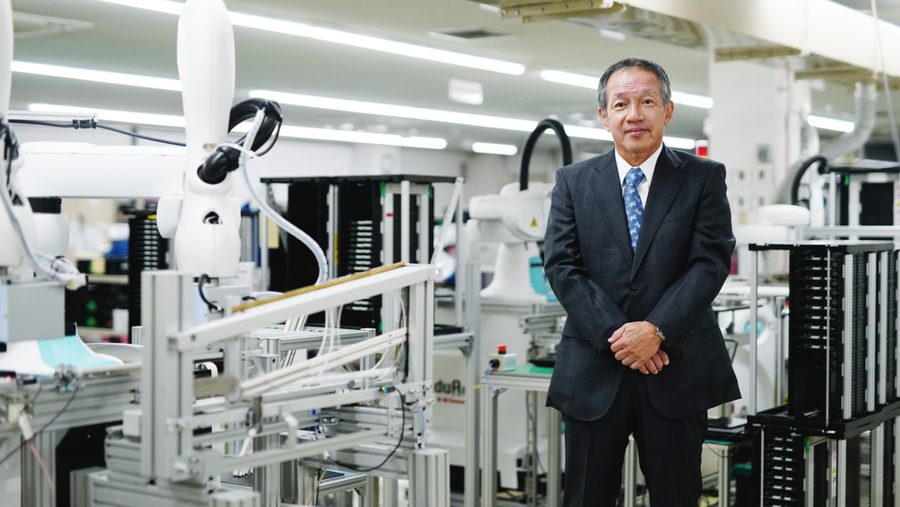
The President of the company, Osamu Ikushima, says that, “It is precisely because we have a thorough knowledge of robots that we ought to take the initiative and use them.”
Toyo Electric has a history of over half a century as a specialized manufacturer of electronics, and has been involved in the production of electrical equipment for industrial robots since the 1960s, which can be described as the starting point for industrial robots.
President Osamu Ikushima explains that, “At the beginning, the majority of the electrical equipment related parts of the Kawasaki-Unimate were produced by us.
Our staffs went to Kawasaki’s robot factory and helped with things like the harness wiring. We were also engaged in the installation work for other companies installing the robots.”
Electrical items for Kawasaki account for 70% of Toyo Electric sales. Half of those items are used on industrial robots and the other half are used in precision machinery.
The company also has a business relationship with Sysmex Corporation, which boasts the top share globally in the three sectors of hematology inspections of the components in blood (blood cell counts), blood coagulation, and urine analysis (urinary sediment). That relationship has continued from the time when Sysmex was known as Toa Medical Electronics Co., Ltd.
Furthermore, we also deliver components to Furuno Electric Co., Ltd., which has spurred a lot of innovation in the sector of electronic devices for ships.
Toyo Electric has been working on components for industrial robots for a very long time, but they found it hard to find processes within their own company where an industrial robot could be applied to the work.
President Ikushima explains that, “Our company handles things like wire harnesses and printed circuit boards, so we do not need a maximum payload of tens of kilograms.
In addition, we have a lot of employees working on the supplying and conveyance of workpieces, so having something enclosed in a safety fence does not suit our work environment.” However, the company has been associated with robots for more than 50 years.
“That was why we thought we understood everything about them, from their structures to their mechanisms.
So, we felt that we really must take the initiative and use robots.” Thus, what the experts in electrical equipment production focused on was the duAro collaborative type dual-arm SCARA robot from Kawasaki.
Introduction effects/solutions:
Harness assembly and printed circuit board mounting automated with duAro
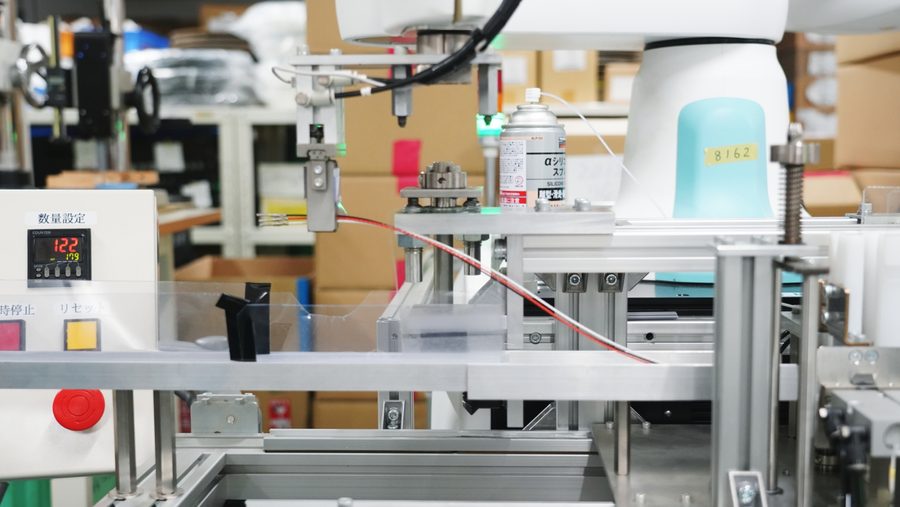
The use of duAro robots realized the automation of two processes at Toyo Electric: (1) harness assembly, and (2) printed circuit board mounting.
The development of the first process (1) required two years. The process is to pass multiple electric wires through a protective tube.
One duAro uses one of its arms to pick up one wire at a time from multiple magazines and set them in the prescribed location.
The other arm transports the jig to the position specified for each model and then supplies the electric wires that have been prepared by the other arm onto the top of the jig all together.
The mechanism groups together the multiple electric wires that are to be sent into the flexible tube by passing them through a jig shaped like a funnel.
There are multiple sensors on the hand that reliably grasps one electric wire at a time from the multiple wires in a magazine. However, there is no complicated equipment such as a camera or image processing system.
By taking steps in the mechanical structure of the hand, such as in the selection of its materials and in its shape, it has been made possible to accurately handle the thin electric wires, which have elliptical shapes and are only around 1.4 mm in diameter.
Another characteristic is the simple structure, which prioritized “using the original functions of the main body of the robot as much as possible”.
The positioning of the workpieces is also handled with just the movement of the duAro, without adding control systems using servomotors or stepping motors.
In addition, spraying lubricant (silicon oil) on the tube is also the role of duAro.
Before the arm that places the tube moves onto the next task, it cleverly uses its “forearm” to push the nozzle on a spray can. In this way, the individual movements of the duAro are each utilized efficiently.
Furthermore, a compact vertically articulated robot is used in the process called the preliminary soldering that occurs in the processing before the tube insertion.
Kawasaki’s RS003N robot performs the series of task: Picking of an electric wire from a magazine -> stripping a part of the cover off one end of the cable -> twisting the core wires and applying flux -> performing preliminary soldering -> returning the wire to the magazine.
By locating these two processes of the preliminary soldering and tube passing next to each other, it became possible to operate almost completely without human workers, except for just the workpiece supply and discharge.
For the printed circuit board mounting in (2), three duAro units perform the work.
The first robot is responsible for everything from the connector selection to classification and packing in dedicated sticks.
The mechanism ensures that only normal items enter the stick with a combination of a vision system and sensors to check the polarity and pin height deviations, etc.
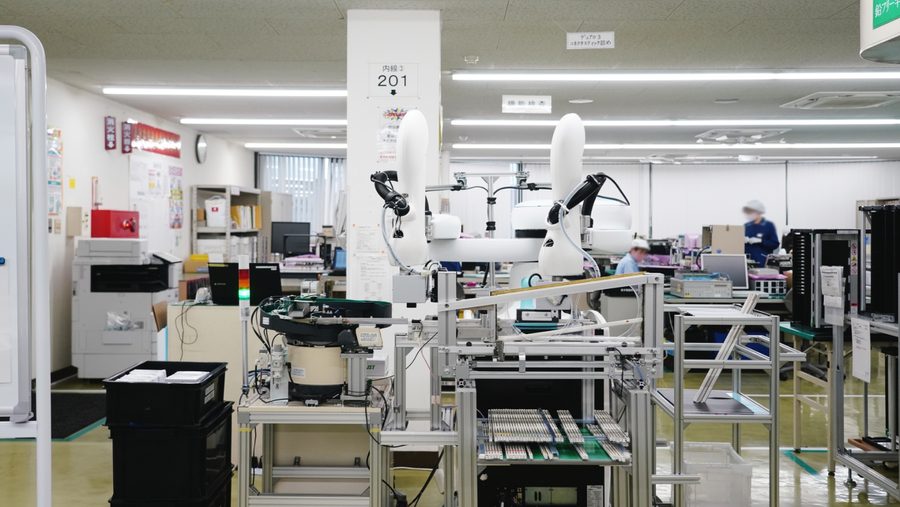
Here, the duAro mounts each connector at the designated hole position on the circuit board.
The Plant Manager of the Toyo Electric Akashi Plant 2 explains that, “The positional repeatability of duAro is ±0.05 mm.
Even so, if there is even just a small amount of position deviation in the instant when the hand grasps the connectors, then it will not be possible to place them correctly.” A deviation of just a few tenths of a millimeter means that the connectors will not enter the circuit board.
As countermeasures to this, a system was constructed where the workpiece is temporarily placed on a standard plate, and also a camera installed on the robot hand is used to further improve the accuracy.
In addition, the camera reads the marks on the circuit board side to detect the correct position and to conduct compensation while performing the mounting.
The circuit boards that had connectors mounted are stored in a rack and sent to the final soldering process.
The third duAro robot takes a circuit board from the rack and then waits for the completion of the work by dedicated soldering machinery called a desktop robot. When the soldering is complete, the duAro stores it in the rack for completed items.
The soldering work used to be automated by the desktop robot, but supplying, discharging and storing of the circuit boards were performed by human workers.
The soldering takes about three minutes, so workers could be doing something else during that time, but they had to interrupt that other work at the timing of the supply and discharge.
By introducing a robot here, it was possible to realize a smooth work process.
Future prospects and plans:
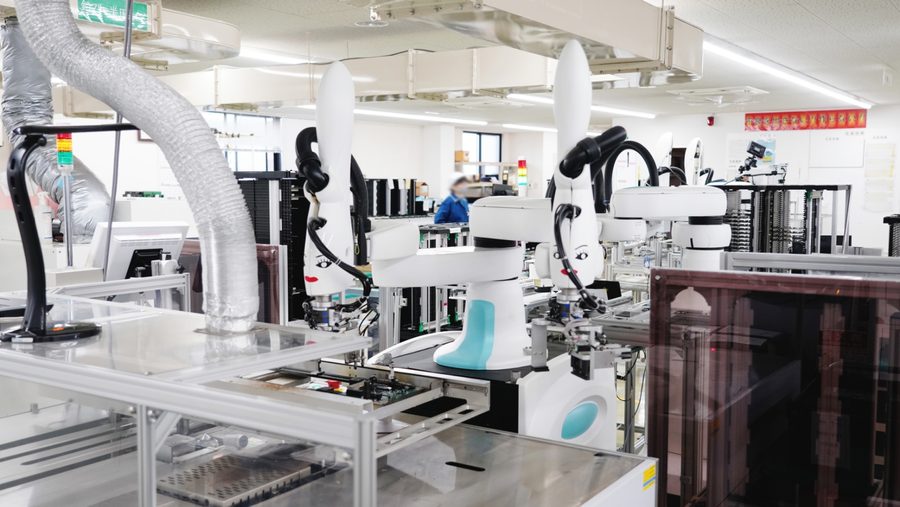
The fact that the robot has a “face” on the arm shows that the duAro is popular with the employees.
Since the Kawasaki-Unimate, Toyo Electric has been involved in the creation of electrical components and circuit boards for industrial robots for many years. They have accumulated a wealth of knowledge related to industrial robots over more than 50 years.
For the automation, in addition to the selection of the robot, a great strength of the company is that it is also able to conduct all of the peripheral equipment design, prototyping and system setup in-house.
President Ikushima explains that, “When we think about changing the specifications or expanding the work, if we have done it all by ourselves from the start, then we will be able to quickly correct the program or reconstruct the mechanisms.
That trial and error, and building up of knowledge, will go on to become an asset of the company.”

President Ikushima says that, “Continue introducing more and more robots, and have them operate.
This is what I have told the employees.”
“Our work requires a certain level of proficiency.
It is only because we have people who have those skills that the quality is maintained and the manufacturing can be achieved efficiently. On the other hand, it is necessary to increase the work that can be automated in preparation for the coming aging society.” Actually, for the circuit board mounting, further development is underway to introduce duAro for transfer of the filled sticks to the circuit board mounting process, which is currently being performed by workers.
“Currently we have two plants, Plant 1 and 2. I hope that we will be able to add a new robot to each plant every year.”
― Company information Company name: Toyo Electric Corporation Representative: President and Representative Director Osamu Ikushima Established: February 1969 Capital: 50 million yen Core business: Manufacturing and assembly of electrical components (printed circuit boards, controller cabinets, harnesses, etc.) for industrial robots Employees: 65 Places of business: Head office: 3-2-18 Shinohara Honmachi, Nada-ku, Kobe-shi, Hyogo Akashi Plant 1: 1675-1 Eigashima, Okubo-cho, Akashi-shi, Hyogo Akashi Plant 2: 540-1 Nishiwaki, Okubo-cho, Akashi City, Hyogo Website http://www.toyo-ele.co.jp ― Robots installed Model duAro1: The first dual-arm SCARA robot with a collaborative concept Features: compact, simple teaching, easy installation, high level safety Max. payload: 2 kg on each arm (4 kg with two arms) Axes: 4 axes on each arm Positional repeatability: ±0.05mm Model name : duAro1: RS003N, a compact vertically articulated robot designed to move faster, more widely and more precisely, and to be more compact Features: Compact design, lightweight design, wide working range Payload: 3kg Axes: 6 Positional repeatability: ±0.02mm