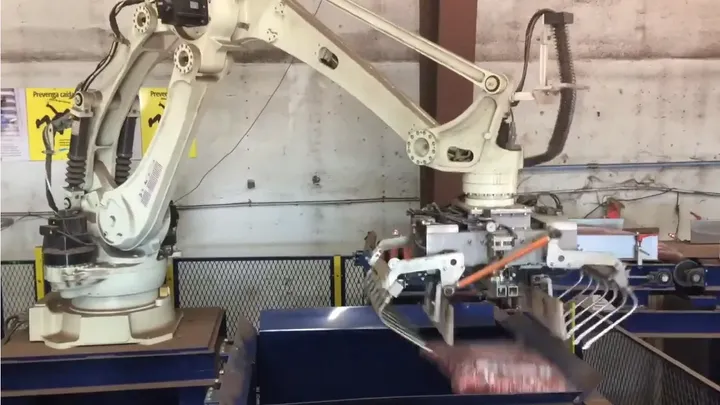
- IndustriesLogistics
- ApplicationsPalletizing
- Robot SeriesCP series
System designed by:
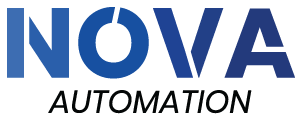
OVERVIEW
In most factories, end-of-line processes are sought-after candidates for automation. The combination of ergonomically challenging tasks and simple, repetitive movements make them tedious for workers and, oftentimes, easy to program. These factors also can lead to costly labor shortages.
However, in the landscaping industry, palletizing bags of soil and mulch has always been a relatively difficult process to automate. Dropping lightweight, oversize plastic bags onto a pallet securely and without overhang has proven to be a challenge for robots and human workers to do with precision – especially after performing hours of manual labor.
To solve this problem, Denver-based integrator NOVA Automation designed an automated system that allows manufacturers of landscaping materials to avoid pallet overhang and redeploy workers to more human-friendly jobs, while providing a consistent and reliable palletizing process amidst a labor shortage.
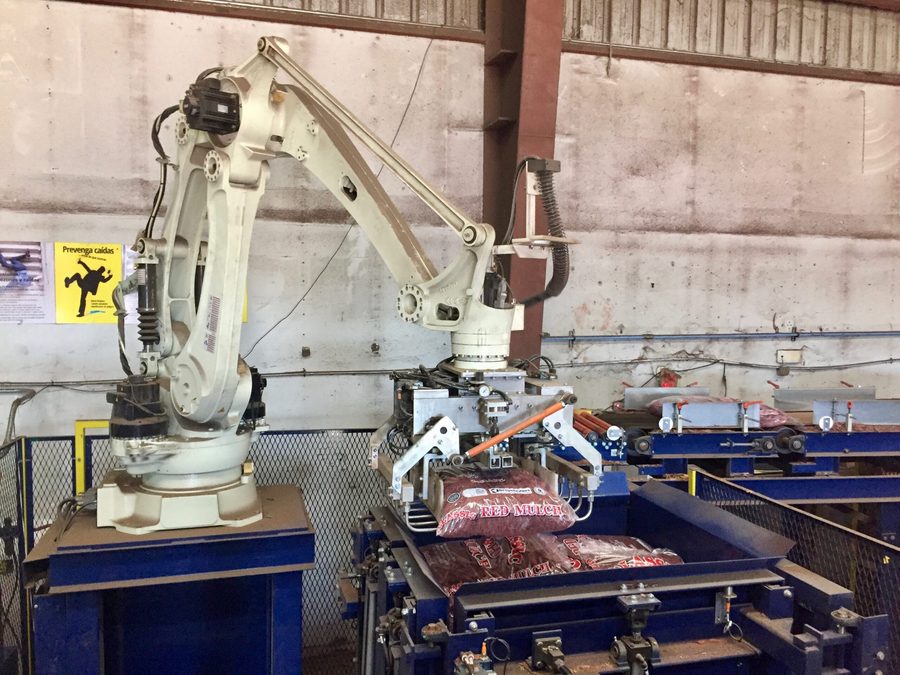
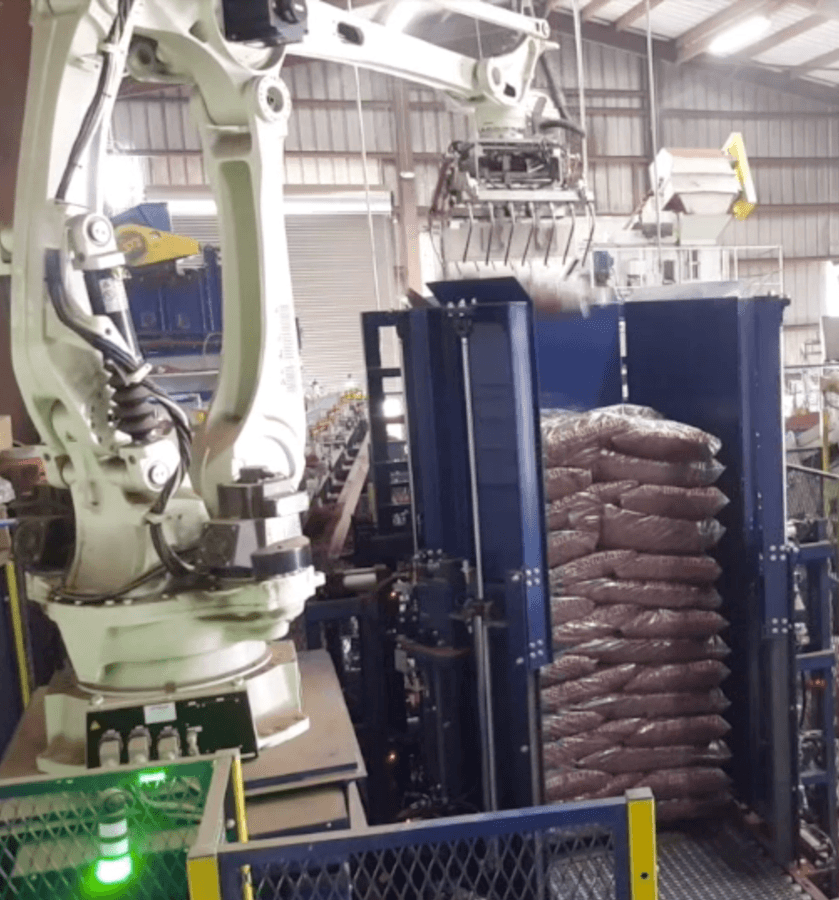
CHALLENGES
- Eliminate pallet overhang
- Achieve consistent palletizing rate
- Redeploy employees to more human-friendly roles
In order to keep shipping costs down, the manufacturer had to fill delivery trucks from floor to ceiling with eight-foot tall pallets. For human workers to achieve this kind of pallet height, they had to drop the bags onto the pallet from over the top of the eight-foot manual stacking box, which would keep the bags from slipping off the pallet. It was impossible to follow a specific pattern because the bags were dropped, resulting in unstable, irregular pallets.
Stacking oversize plastic bags of landscaping material is not an ergonomically friendly task for human workers. Fatigue naturally sets in after doing manual labor over the course of an eight-hour shift, and doing this type of repetitive motion for extended periods poses a clear risk for injury. The strenuous nature of this task led to low employee retention, which resulted in inconsistent palletizing rates and idle machines.
“It’s not easy to stack 8-9,000 bags per day,” said Harvey Schneider, owner of Florida Wood Recycling (FWR), a manufacturer that uses NOVA Automation’s solution every day in their facility. “It’s a tough job, so it was hard to keep workers in that job.”
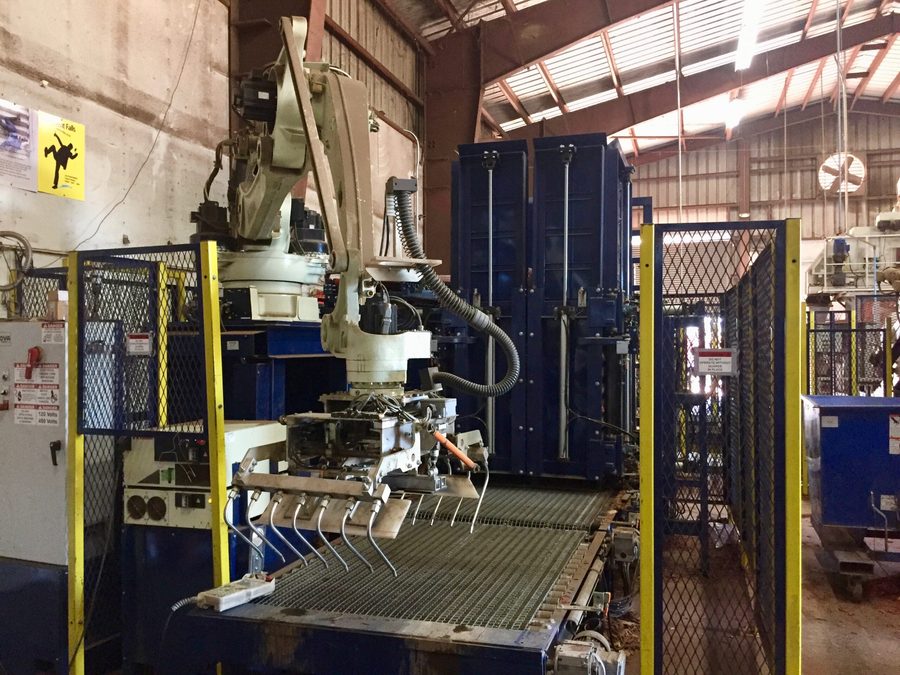
SOLUTION
- Fully automated end-of-line solution installed at Florida Wood Recycling (FWR)
- System uses a Kawasaki CP300L high-speed palletizing robot and an Automated Palletizing Stack Box, designed by NOVA Automation
To solve these industry-wide issues, NOVA designed a fully automated palletizing cell that they were able to install in FWR’s facility. The integrator automated the manual stacking box concept for use with a CP300L palletizer, and other end-of-line equipment.
To start, a volumetric feeder and form fill and seal machine fills bags with identical amounts of product. Once filled, the bags are sealed using hot air, and enter a conveyor system. A product conditioning conveyor flattens the bags for easy stacking, and then a pacing conveyor delivers them to the picking location for the CP300L robot.
NOVA’s patent-pending Automated Palletizing Stack Box begins below the pallet, which sits on a conveyor, and the box rises roughly four feet while the product accumulates on the infeed conveyor. The robot stacks bags individually on the pallet, following a programmed pattern. Once the bags reach the top of the box, it rises four more feet to the full pallet height and the robot continues to stack. The finished product is a stable pallet with no overhang, ready for plastic wrapping and truck loading.
The power, reliability, and industry-leading speed of Kawasaki’s CP300L robot made it the perfect candidate for FWR’s application. CP series robots drive the flexible automation of end-of-line and distribution processes in a wide range of industries, and support the highest production line efficiencies. With the lightest maximum payload capacity, the CP300L model’s throughput is the highest of the CP series palletizing robots.
Repeated positive experiences with Kawasaki also played a role in NOVA’s choice.
“We want a partner and not just a supplier. Kawasaki Robotics has been that partner we were looking for, and the collaboration gets stronger every day,” said Paul Wegman, NOVA Automation CEO. “Combine this with Kawasaki’s support, service, and a fantastic product line, and we could not be more pleased with our relationship.”
RESULTS
- CP300L robot runs up to 18 hours/day, palletizing at a rate of up to 22 bags/minute and realized output of 18 bags/minute.
- Employees redeployed to other roles in facility
- Customer maximized pallet height, resulting in more efficient shipping
- Automated Palletizing Stack Box eliminates overhang and allows for extended pallet stacking
FWR currently has one automated palletizing line and two still operated by human workers. Because of the success his company has experienced, Schneider is considering automating another line by the end of the year.
FWR’s CP300L robot is currently running at least 9 hours per day. During their busy springtime season, it runs up to 18 hours per day. It is able to palletize at a rate of up to 22 bags per minute with an average output of 18 bags per minute. This is roughly the same rate as two human workers combined.
Prior to automation, the bag stacking process required two workers to do strenuous, repetitive motions for an entire shift. Now, these workers are hard at work in another area of FWR’s facility, where their skills are better utilized. The robot is reliable and consistent, and FWR no longer has to pay overtime, or halt production if an employee doesn’t come to work. They also avoid having to pay workers in the case of a malfunction.
“Before automation, if one of our other machines went down, we’d have to pay someone to be idle while the other machine got up and running,” Schneider said.
Although it’s relatively new to the soil and mulch industry, end-of-line automation is an established concept supported by hundreds of positive examples. For NOVA Automation, FWR’s application is one of many successful robotic palletizing applications they have facilitated over more than 25 years of business.
“This has been proven before; (automated palletizing) isn’t new. Every application is different, but it’s not a brand new idea,” said Voit Karpala, NOVA Director of Engineering. “The technology has evolved, so palletizing is an ideal application for robots.”