Reasons why industrial robots are chosen as the ticket for automation solutions
As the need for automation increases, industrial robots are attracting more attention as a solution for addressing labor shortages and expanding business opportunities. With their versatility and flexibility, industrial robots have the advantage of being easily deployable to sites where deploying a specialized machine is not ideal or where large-scale facility renovation is difficult.
In addition, by collaborating with a system integrator (SIer), a group of professionals specializing in deploying robotic systems, end-users can move through the steps from planning, testing, installation to operation with ease.
Moreover, in June 2021, Kawasaki Heavy Industries launched K-AddOn, a platform where users can easily find compatible peripheral equipment to build the desired system. The robot deployment requires connecting to peripheral equipment such as hands, various sensors, and vision. Our new open platform enables us to verify and certify these products for connectivity in advance. The end-users can reduce the verification cost of equipment connections required during deployment.
In addition, by letting the robot perform various tasks, the users can accumulate the training and performance data, including machining details. In addition to collecting its performance data, these data will be valuable in terms of training other robots, progress management, and traceability.
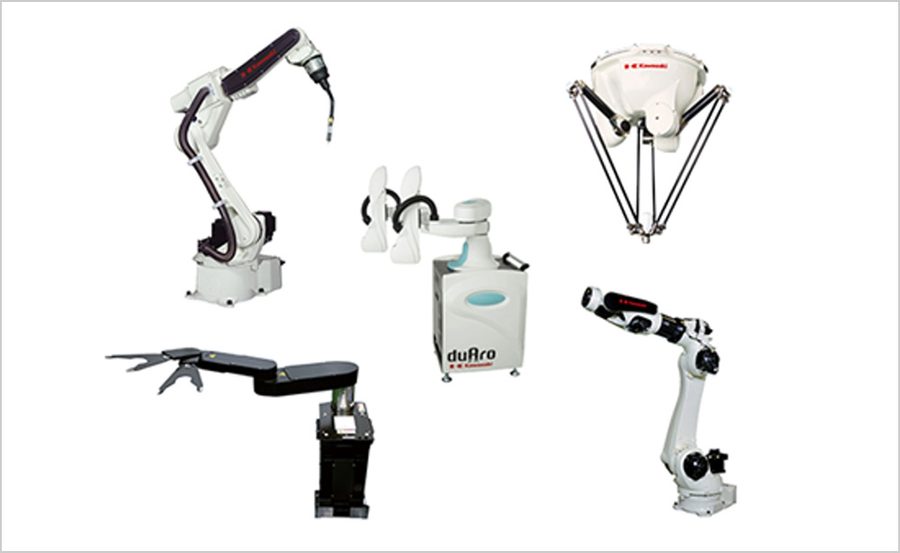

The types of robots can be generally categorized into industrial and non-industrial robots. The former is mainly used in manufacturing, logistics, agriculture, and animal husbandry. The latter refers to robots used in security, medical and health care, and space. The humanoid robot “Pepper” and cleaning robots are included in this category.
What is an industrial robot anyway?
The world’s first industrial robot was brought to life in the United States in 1962. The idea of “a robot that can flexibly respond to automation through teaching and playback” was proposed by American engineer George Charles Devol Jr. Devol met Joseph Frederick Engelberger, an entrepreneur and the man who would come to be known as “the father of robotics”, and succeeded in developing the first industrial robot named “the Unimate”, meaning “a workmate with universal capability”.
Kawasaki Heavy Industries was one of the first companies to sign a technical license agreement with Unimation, the manufacturer and seller of the Unimate. In 1969, the Kawasaki-Unimate 2000, Japan’s first industrial robot, was launched, mobilizing all of its technological capabilities for domestic production. Since then, the development of industrial robots for Japanese industries has accelerated, especially in the automotive industry. This is where the capabilities of Japanese manufacturers, who had acquired a high degree of skill in the fields of electrical equipment and precision machinery, reached their pinnacle. Japan rose to become the world’s top robotics powerhouse.
Industrial robots are roughly categorized into 6 types. The first type of industrial robot is a polar coordinate robot. This type was extensively developed in the early days. It features a centrally pivoting shaft like a gun turret and an extendable arm that rotates up and down. The Kawasaki-Unimate 2000, Japan’s first domestically manufactured industrial robot, also belongs to this type. Another type, a cylindrical coordinate robot, is similar to the polar coordinate type, which was also widely produced in the early days. This type of robot features a pivoting shaft and an extendable arm that moves vertically. Another type of robot is a cartesian coordinate robot. Cartesian coordinate robots perform movements in three dimensions, not by rotating, but by sliding on their three perpendicular axes (length x width x height). This type requires a larger installation area, but the mechanism is simple and easy to control.
The type of robot that is most widely used today is the vertically articulated robot. It features an arm with multiple joints (axes) like a human arm and a pivoting shaft, and is used in various applications such as welding, palletizing, and assembly. Another type is a selective compliance assembly robot arm (SCARA) robot that features a horizontal rotary shaft and a vertical linear shaft. The upward and downward moving tip moves horizontally, making it suitable for workbench tasks with a fixed height. A parallel link robot excels at high-speed work. The tip of the robot is controlled by multiple joints arranged in parallel, which enables high-speed and precise movement. This type of robot is used for picking lightweight workpieces flowing on a conveyor belt.
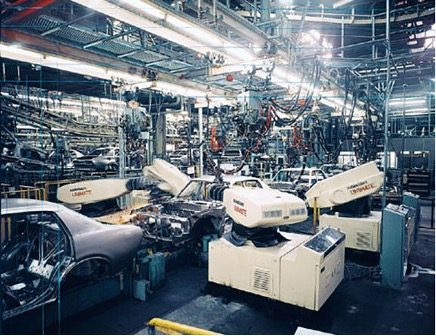
The Kawasaki-Unimate, the first domestically manufactured industrial robot by Kawasaki Heavy Industries. During Japan’s motorization trend, the automotive industry had particularly high expectations for these robots. They were first deployed in the welding process, which was considered to be demanding, dirty, and dangerous work.
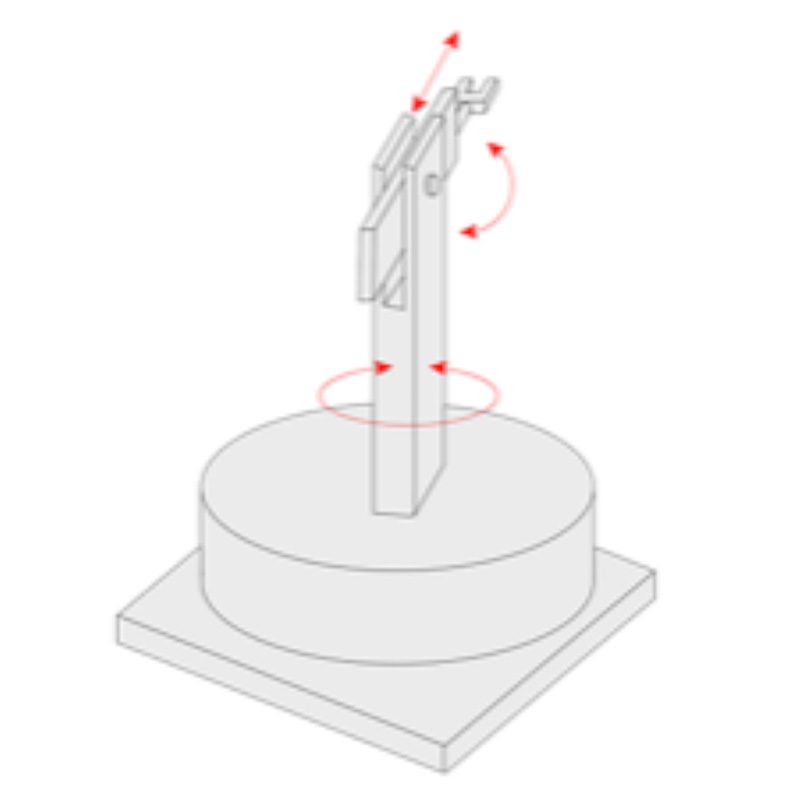
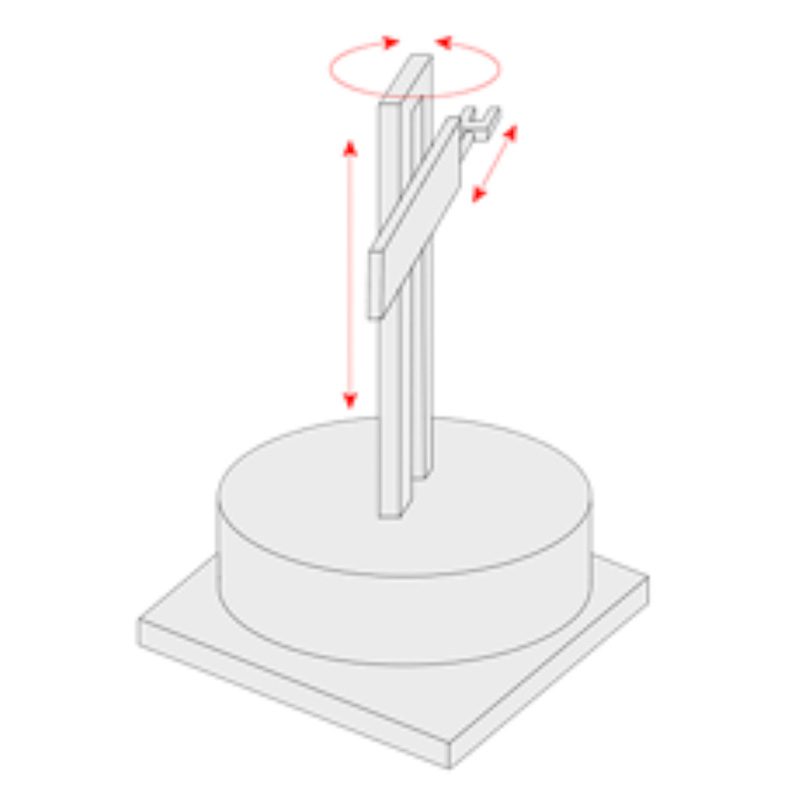
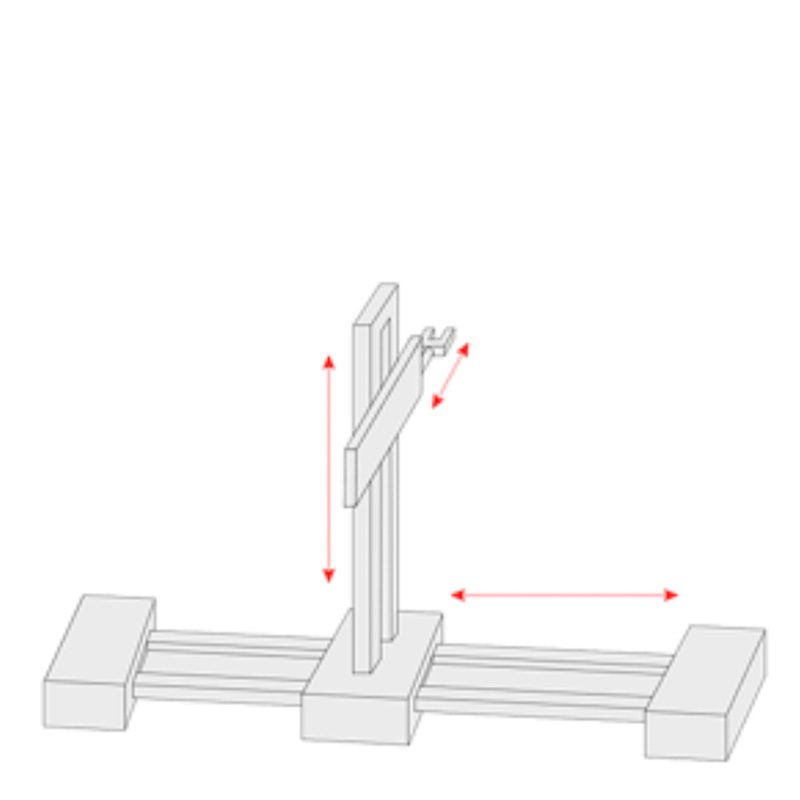
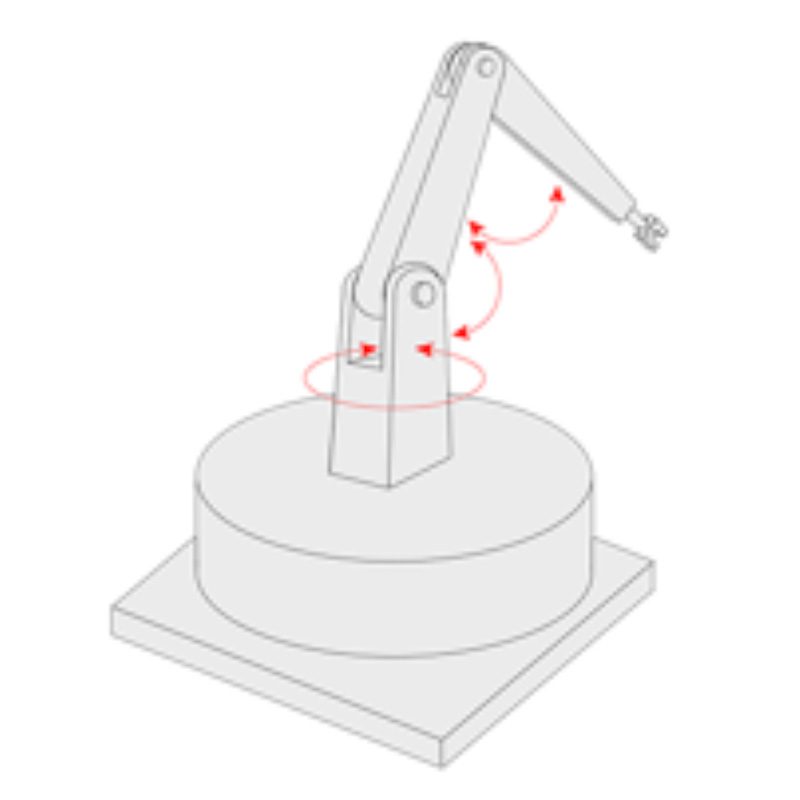
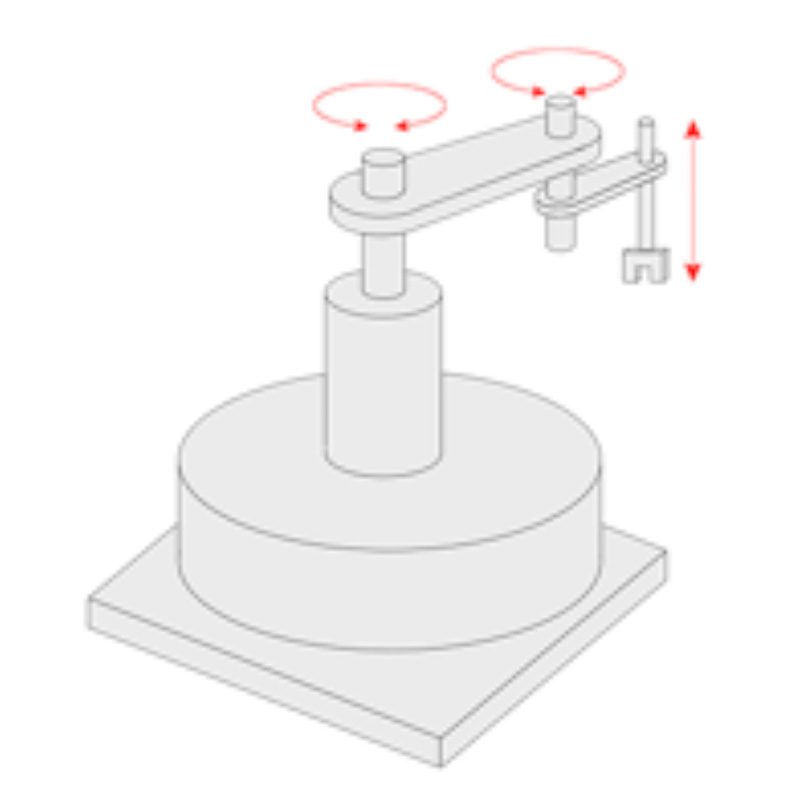
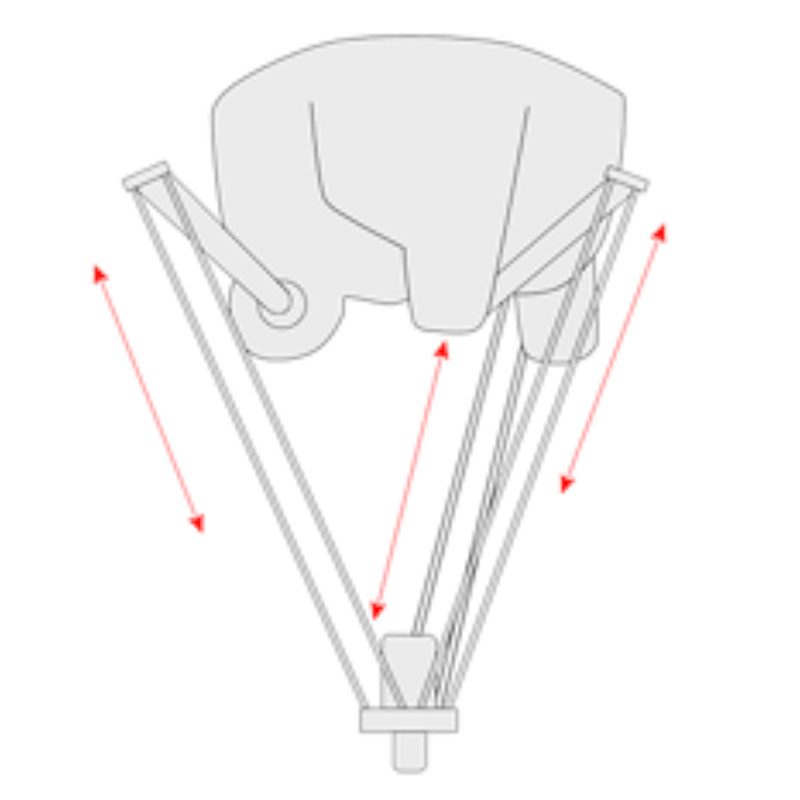
Industrial robots can be categorized into 6 main types. From left to right: Polar Coordinate Robot, Cylindrical Coordinate Robot, Cartesian Coordinate Robot, Vertically Articulated Robot, SCARA Robot, and Parallel Link Robot. The SCARA robot with twin arms is “duAro,” a Kawasaki Heavy Industries’ collaborative robot.
Industrial robots for a new era
Because they are fast and powerful, conventional industrial robots are required to be installed away from people and inside safety fences. On the other hand, collaborative robots, a new type of robot that has been attracting attention in recent years, can coexist with humans. These robots can be operated in a small space without the need for large safety fences, which enable applications in a variety of sites with less specialized equipment. For example, Kawasaki’s dual-arm SCARA robot “duAro” is a collaborative robot that only takes up the same amount of space as one human worker. Utilizing two arms, the robot can assemble a boxed lunch, wash dishes or package cosmetic items in the same way as a human worker does. Kawasaki is also developing an automatic waste sorting system for recycling sites using duAro.
Another new addition to the world of robotics is the remote collaboration system “Successor” developed by Kawasaki. The Successor can remotely control robots that are installed away from the operator via a controller unit. This innovation opens up the possibility of deploying robots to tasks that require human sensations, which had been considered difficult in the past. One of the Successor’s great advantages is that the robots can be directly taught the minute movements of a human without programming. This means that they can be used as a tool to pass on skills to the next generation, as the skills of an expert can be transferred to the robots, and later these robots can train new human workers. It also supports a multi-control function where one operator can operate multiple robots simultaneously. Operating multiple factories around the world from a single location using a high-speed communication network may become possible in the future. The system is a perfect solution for the coming smart factory era.
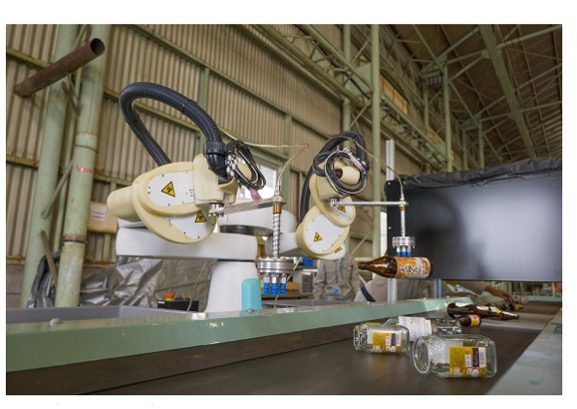
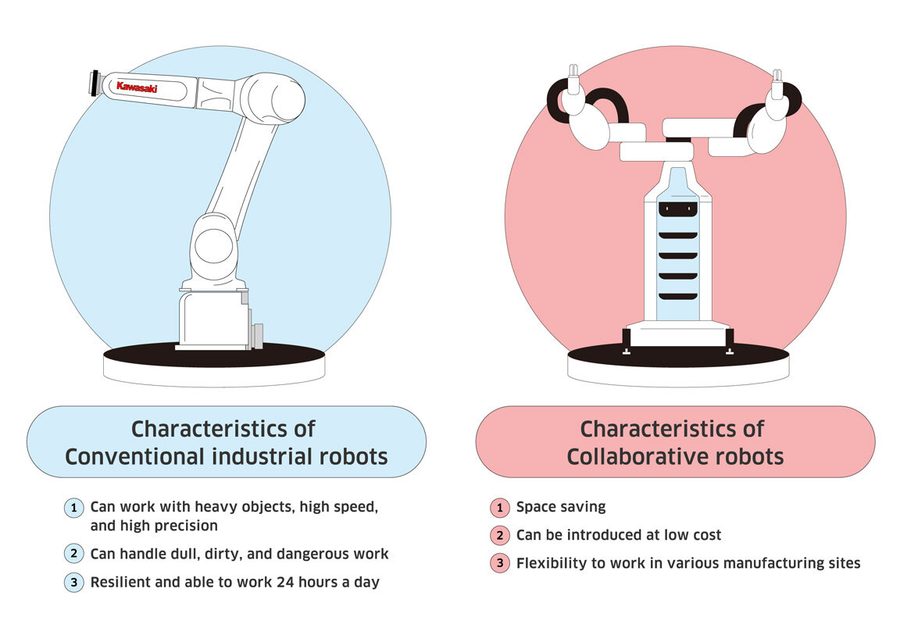
Unlike conventional industrial robots, which require safety fences, collaborative robots can work side-by-side with human workers. Kawasaki Heavy Industries has developed a resource waste sorting support system using the collaborative robot, duAro. With a space-saving design that only takes up the space of a single person and its dual-arm, duAro can perform sorting on the conveyor alongside humans.
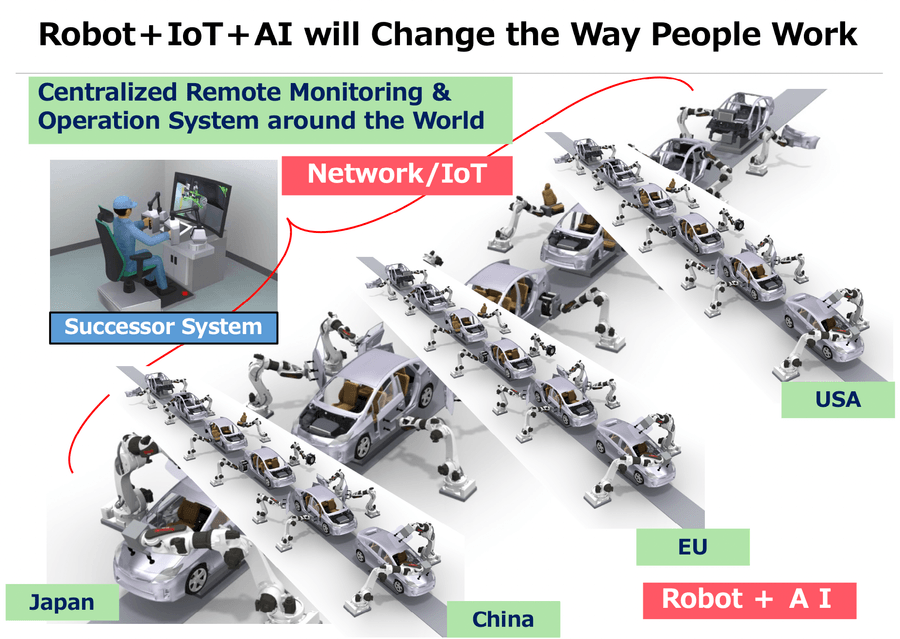
The Successor is a remote collaboration system that can remotely control robots via a controller unit called Communicator. In the future, an operator in the office may be able to use the system and the high-speed communication network to carry out work at remote factories. Its development is underway with such applications in mind.