昨今、製品品質に対するお客様の要求は製品の機能・性能のみならず,キズの無い美しい表面が求められるなど、外観意匠品質に対する要求が増えてきています。
塗装面の外観検査は目視検査が主流で、検査員は微細で様々な欠陥を感覚や経験に基づく官能的な評価で判断しているため、技能、ノウハウ、さらに高い集中力を必要とし、属人的な作業が製品の外観意匠品質のバラツキにつながってしまいます。こうした中、近年の労働人口の減少、特に熟練作業者の減少や労働者の安定確保の困難を背景に、塗装面の外観検査の自動化・脱技能化のニーズが高まりを見せています。
そこで、塗装面の外観検査を例に川崎重工が開発した汎用ロボットを使った自動外観検査システムについて紹介します。
外観検査の取り巻く環境
塗装面の外観を検査する自動機の仕組みとして、被検査対象面へ照明を照射した時の反射の違いをエリアカメラで撮像し、画像データから良品と不良品の識別する手法が一般的とされています。近年、光学機器の性能や、撮像した画像の処理技術などの進歩により、外観検査の領域において、より高度な適用への展開が期待されています。
撮像方法の進歩
カメラやレンズの光学系は解像度が向上し、撮影に必要な照明についても小型化や、撮影時に特殊な発光パターンを使うことで、今まで目視でしか判断ができなかった塗装表面の微細な凹凸も画像上に映し出すことが可能となり、また、機器の低価格化も進んでいます。
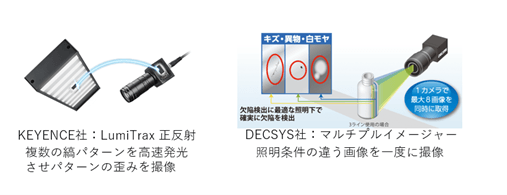
画像処理技術の進歩
画像処理技術においてもGPUが高性能化し、処理の並列実行が可能になったことで、より解像度が高く、フレームサイズの大きい画像を高速処理でき、リアルタイムに検査結果の判定をおこなうことが可能になりました。また、従来のルールベースによる判断では難しかった非定型なものも、AI技術により大量の学習データもとに高速に判断できるようになりました。
川崎重工の走査型外観検査システムにおけるソリューションと効果
光学系・画像処理の進歩にともない、より高度な適用への自動化が増加する中、曲面を有する塗装部品の外観検査の自動化は、まだ進んでいません。特に自動車の外装部品で図1のようなライン工程では、検査員を複数名配置し、決められたタクトタイムで生産する必要があり、検査員の代替になるためには、複雑形状の被検査対象面から短時間に不良を見つけ出す必要があります。
そこで川崎重工は曲面を有する塗装部品に対して、曲面に沿った動きをさせることができる汎用ロボットと、高解像度で撮像できるラインスキャンカメラを組み合わせることで、複雑形状に対して高速で高精度な検査の自動化を可能にしました。
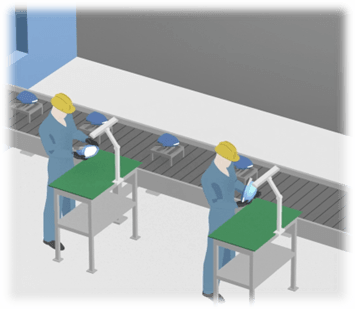
移動量パルス出力機能
従来からラインスキャンカメラを使い、ロボットあるいは製品を動かして曲面の表面状態を走査撮影する技術は存在していましたが、多くの場合はラインスキャンカメラの撮影タイミングをカメラ制御装置の内部タイマーをつかい固定タイミングに制御していたため、ロボットあるいは部品移動装置は一定速度で走査することが必然とされていました。このような走査方式の場合、取得画像の距離精度を確保するためには、走査動作が直線状に限定されるか、あるいは低速固定速度での動作に限定され、設定走査速度に到達するまでに助走区間が必要になるなど、複雑形状部品の検査においては適用困難な面がありました。
そこで、川崎重工は複雑な曲面に沿って高速走査撮影を可能とするため、新機能として「ツール先端移動量パルス出力機能」を開発しました。この「ツール先端移動量パルス出力機能」とは、図2に示す外観検査システムにおいて、ロボットアームに取り付けたツール先端(カメラ焦点位置)の移動量に応じて、ロボットコントローラから自動的に撮影トリガーにあたるパルス信号が出力する機能です。
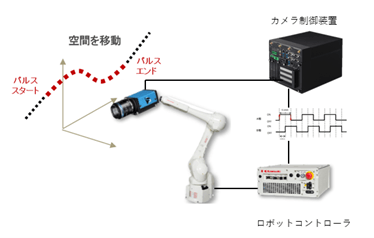
あらかじめ、1パルス当たりのツール先端移動量を設定しておくことで、ロボットのツール先端の移動量に応じて、一定距離ピッチ撮影となるようにカメラ制御装置へ撮影指令トリガーを出力することが可能となります。図3は従来の撮像手法とツール先端移動量パルス出力機能で縞パターンを撮像した結果を比較です。従来撮像手法では、ロボットの動作速度が変わると縞パターンの間隔が伸びることに対して、ツール先端移動量パルス出力機能では、速度が変化しても縞パターンに伸び縮みがなく一定ピッチで撮像ができていることがわかります。例えば、1パルス当たりのツール先端移動量を0.1mmピッチに設定することで、塗装面においても約φ0.3mmのブツ、ハジキ、素地に発生する不良などを検出することができます。(図4参照)
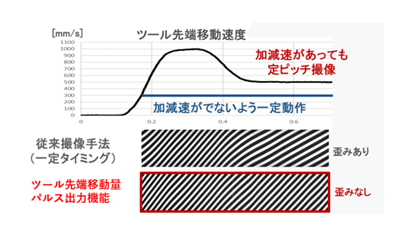
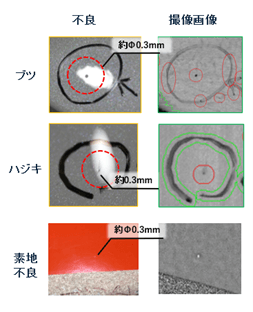
エリアカメラでは広範囲の対象を一度に撮像できますが、曲面を有する製品においては、撮像範囲が限られてしまいます。その分、図5のように製品を多くの撮像する必要があるが、「ツール先端移動量パルス出力機能」とラインスキャンカメラを組み合わせると、曲面に沿うような動きのみで撮像ができるため、撮像にかかる検査時間も短縮でき、撮像枚数を大幅に削減できるため画像処理に必要な時間も短縮できます。過去にエリアカメラに比べて全面検査時間を約1/10短縮することにも成功しました。
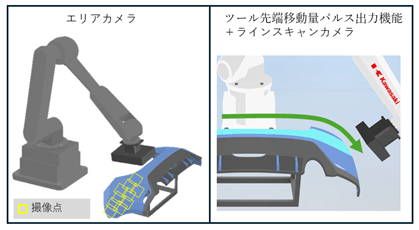
このパルス出力機能は、カメラをロボットが把持するだけではなく、図6のように製品を把持したロボットにも対応しています。そのため、固定されたカメラに対して製品をカメラ焦点位置の前で回転動作させて検査できるため、ロボットの動作を小さくでき、小型ロボットを採用することで、小スペースで導入ができます。
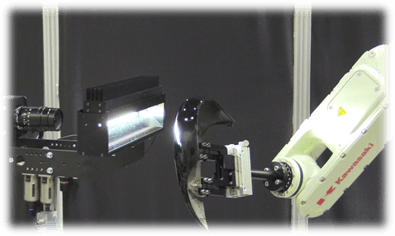
システム立上げを容易する検査パスシミュレーション(SLiM)
外観検査用ロボットを導入するにあたり、不良の検出能力に加え、指定タクトタイム内で短時間に検査を完了させるための適切な検査パス、ロボットの教示点を作成する必要があります。塗装表面の外観検査では、照明・カメラが被検査対象面に対して一定の角度に対峙する必要があり、当社では適切な教示点を判断するため、オフラインでも照明の反射が確認できるアプリケーションソフトSLiM(スリム)を開発しました。SLiMでは製品や、光学機器の3Dモデルとロボットの教示点を用意するだけで、各教示点を通る動作時にカメラで撮像できる照明範囲をワークモデルに図7の右下ように着色するように表示します。着色された結果を確認することで検査対象面の中に検査範囲外があることがわかり、その位置のロボット教示点を修正することで、現場でしか確認できなかった、適切なロボットの教示点とサイクルタイムをオフラインで検証することができます。ロボットを導入する際の現場作業は、システムの立上げ、ロボット動作の作成、動作の微調整が主な作業にあたり、ロボット動作をSLiMで事前検証することで、製品の追加や、変更があった場合に現場でおこなう実機作業の大幅な時間の削減が期待できます。
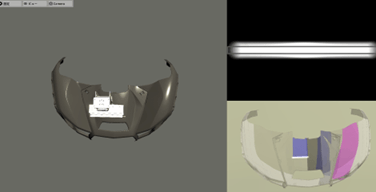
歩留まり改善に役立つ不良位置の表示機能
塗装製品の場合、検査時に検出した不良はほとんどが、手直し工程へ移されます。人が検査する場合は、不良の位置に付箋などの目印をつけ、後の工程に移されますが、ロボットで検査する場合も同じように、不良位置を後工程に示す必要があります。その手法の一つとして3Dモデル上に不良があった位置を示す手法を開発しました。「ツール先端移動量パルス出力機能」を使って撮像された画像は、一定距離ピッチで撮像されており、実物製品の大きさと一致します。そのため、ロボットの移動距離、その時の位置座標と撮像した画像上にある不良位置の距離(ピクセル数)を外部のパソコンで組みわせ、図8のように製品の3Dモデル上に重ね合わせることで不良位置を正確に示すことができます。
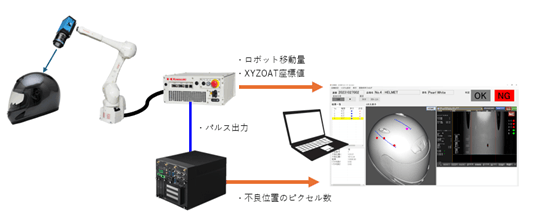
塗装品質を高めることは補修作業の低減や、生産性の向上につながります。特に不良情報は品質を向上させるために重要な情報です。ロボットで検査する場合は、不良情報は自動で蓄積され、分析に必要なデータを効率的に取得できます。また、図9に示すように工程、品種、塗色と不良の発生日時、生産に従事する作業者の情報を合わせて分析することにより、検査の前工程で発生する不良の原因特定までの時間が短縮され、歩留まりの改善が期待できます。
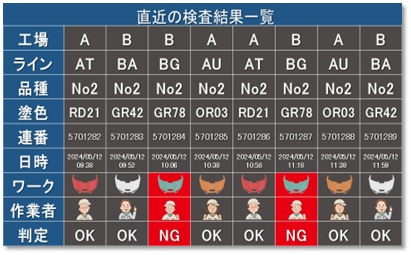
外観検査の自動化にともなう作業者の省人化に貢献
塗装面の外観検査は高い品質、不良種類の多さにより、未だ検査員による作業が主流ですが、光学系や画像処理技術の進歩により、着実に自動化に向けた技術が確立されてきています。今後も「ツール先端移動量出力機能」を基盤技術とした製品開発をおこない、塗装面に限らず、製品表面の外観検査の自動化にともなう作業者の省人化に貢献していきます。