航空宇宙産業は他の産業と異なり、製造現場での自動化が進みづらいと言われています。少量多品種生産のため、ロボット導入が容易でないのがその主な原因です。今回ご紹介する航空機部品メーカーは、カナダのオンタリオ州にあるカワサキロボットの認定SIer(システム・インテグレータ)のSYSTEMATIX社と協力して、ロボットと3Dビジョンを利用したナットプレート組立セルの自動化に成功しました。
ナットプレートは航空機の胴体をフレームに固定するための重要部品です。200種以上の異なる部品があるため、自動化は難しいと考えられていましたが、SYSTEMATIX社はその課題を解決しました。カワサキロボットと3Dビジョンを使用した組立作業の自動化を導入した結果、サイクルタイムの短縮・製品品質の向上・工数の低減を実現しました。
この自動化において成功の鍵となった3Dビジョンは、28種類/225形状のナットプレートを認識できます。川崎重工のRシリーズロボット「RS010L」と「RS080N」は部品先端部のリベット接合を行います。
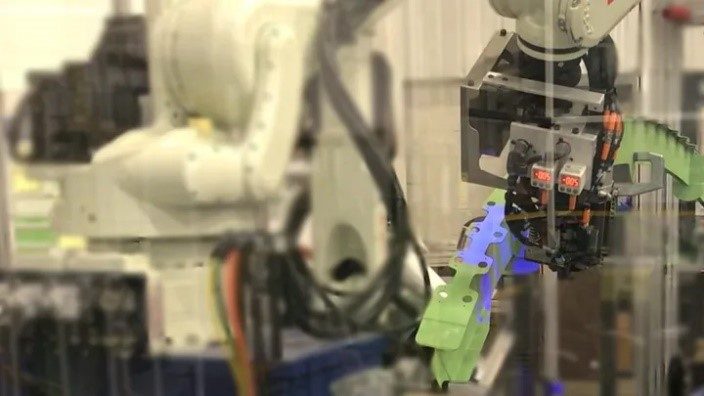
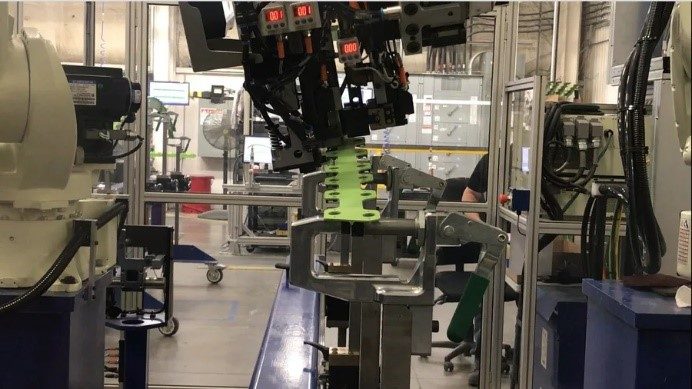
導入課題
過酷な単純作業からの回避
この航空機部品メーカーがナットプレート取付けを自動化した理由は多くありました。厳しい品質要件を満たすため、全従業員は各部品製造に関する教育を受講し、認定を受けなければなりません。また、作業内容をリアルタイムで記録する必要もありました。その上、長時間の単純作業であるため作業員の定着率が低いなど、多くの問題を抱えていました。
品質管理
重要部品であるナットプレート取付けでは正確なリベットの位置(高さ)が求められます。以前は作業員がリベットを研削し、規定の高さにする必要がありました。時間を要する単純作業です。
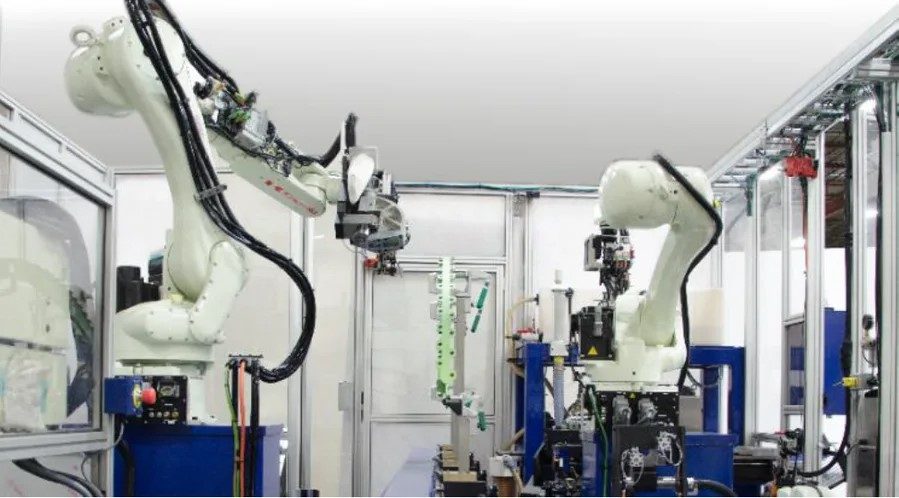
ソリューション(組立て作業自動化の解決策)
- 川崎重工のRシリーズロボット3台と3Dビジョンシステムによる全自動組立
- Matrox画像認識ソフトとLMIロケータが225種類の部品を正確に認識
工程の概要
まず、カワサキロボットRS080Nが3Dビジョンでワークの特定箇所3ヵ所をスキャンし、位置決めをします。そして、ロボットの先端に取付けたグリッパーでワークを把持し、ナットプレート取付け用リベットの皿穴を2個あけます。
次に、ロボットがアームを回転させ、形状や寸法が異なるリベットのうち適したリベットをリベットスライド装置から取り出します。その間、別のロボットRS010Lがナットプレートを把持し、ビジョンカメラを使って28種類のナットプレートを認識します。そして、ロボットがナットプレートの位置確認ツールの上にリベットを置き、正しい部品であることをビジョンで再チェックします。
その後、ロボットはナットプレートをターンテーブルに置き、もう一台のロボットRS005Nがシーラント (耐食性を確保するための塗布剤)を塗布します。また、シーラント塗布前後には2回の検査を行い、塗布が適切に行われていることを確認します。
さらに、ターンテーブルを回転させ、RS010Lがナットプレートと位置決めツールなど部品全体の搬送の準備をします。部品3箇所をスキャンして正確に面合わせをしながら所定の位置で部品を把持すると、RS010Lが部品を固定しつつRS080Nのヘッドと合体します。RS080Nのリベット吸着ヘッドがRS010Lのヘッド内にリベットを置き、ワークをリベット接合します。
最後に、リベット接合後ロボットヘッドが分離してRS010Lが部品を外し、RS080Nはリベット接合位置までドリル先端工具を回転させて作業が完了します。
以上の全工程は39秒間で終了します。
ビジョン、精度、スピード
このような複雑な工程では3Dビジョンは重要です。Matroxイメージング・ソフトウェアとLMIロケータは、225種類の部品と28種類のナットプレートの識別に重要な役割を果たします。
SIerのSYSTEMATIX社が川崎重工を選んだのは、オープンアーキテクチャ(仕様が公開された)のプログラミング言語と、高度なプロセス処理能力があったからです。「今まで当社は多くのロボットメーカーのロボットを取り扱ってきました。カワサキロボットの良いところはプログラミング、特にAS言語での作業のしやすさであり、それがカワサキロボットを使う理由の一つとなっています。」とプロジェクトリーダーのP.J.氏は語っています。
この適用で重要なところは、「複数のロボットがいかに緊密に連携するか」ということです。RS080NとRS010Lの先端部分は衝突せずに動作しなければならず、これには高い再現性が必要です。川崎重工の汎用ロボットRシリーズの位置繰返し精度は、可搬質量 (3 kgから80 kg) に応じて±0.02 mmから±0.06 mmです。P.J.氏によれば、「アームはとても堅牢でフラつきません。非常に正確な位置に移動する必要がありますが、カワサキロボットは何ら問題がありません。」
結果
- サイクルタイムが26秒短縮
- 作業品質の均一化97%を達成
- 作業員3人から1人に削減
- セルで全工程が完了するため、中間製品置き場が不要
ロボットによる自動化は大きな成果をもたらしました。サイクルタイムの大幅短縮・作業品質の向上・省人化などが挙げられ、当初設定したコスト削減と生産目標の達成に成功しました。
自動化の最大の改善点について、P.J.氏は迷わず「作業品質の均一化」を挙げています。製造開始から1年余りで、この自動化セルにより作業品質のムラを解消できました。97%の均一化を達成しただけでなく、コストと人員削減の両面で収益に大きく貢献しています。
-導入ロボット
モデル名:
RS010L/RS080N
特長
広い動作範囲と余裕の可搬能力を持ち、スポットからハンドリングまで様々な用途に対応できる大型汎用ロボット。
可搬重量:
RS010L:10kg/RS080N:80㎏
軸数:
6軸
繰り返し精度:
RS010L:±0.05㎜/RS080N:±0.06㎜