System designed by:

OVERVIEW
Since the 1880s, German dental company ERNST HINRICHS Dental developed and manufactured dental impression and model plasters worldwide. The company only uses high-quality natural and synthetic raw materials without the addition of allergenic substances for their products.
As ERNST HINRICHS began to experience high demand for their products, they implemented a Kawasaki ZX130S robot to palletize bags of dental plaster in an automated end-of-line system. Despite the dusty environment, the system has been extremely successful. With the help of automation, their product portfolio, sales and the company grew steadily. Today, ERNST HINRICHS Dental is the international market leader, supplying dental wholesalers and private labels worldwide.
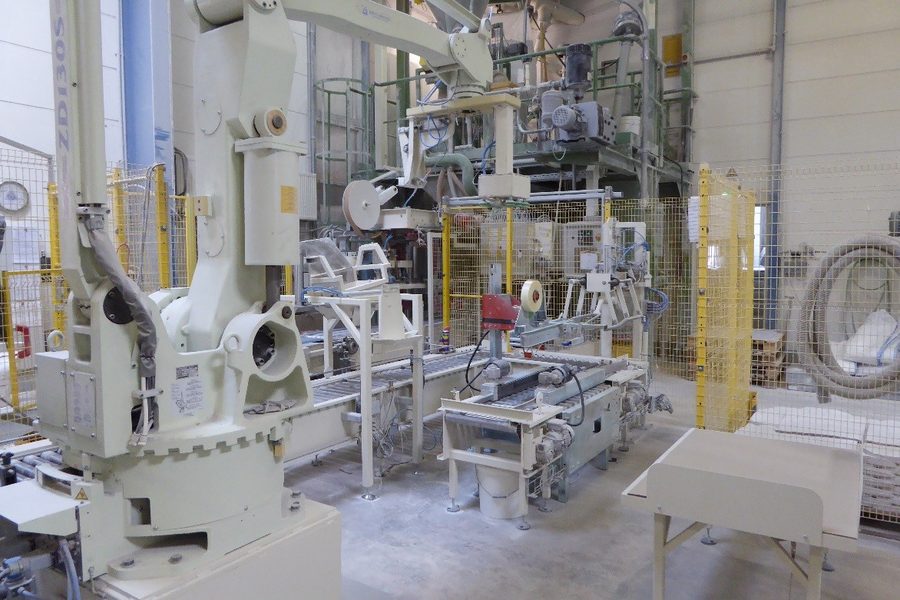
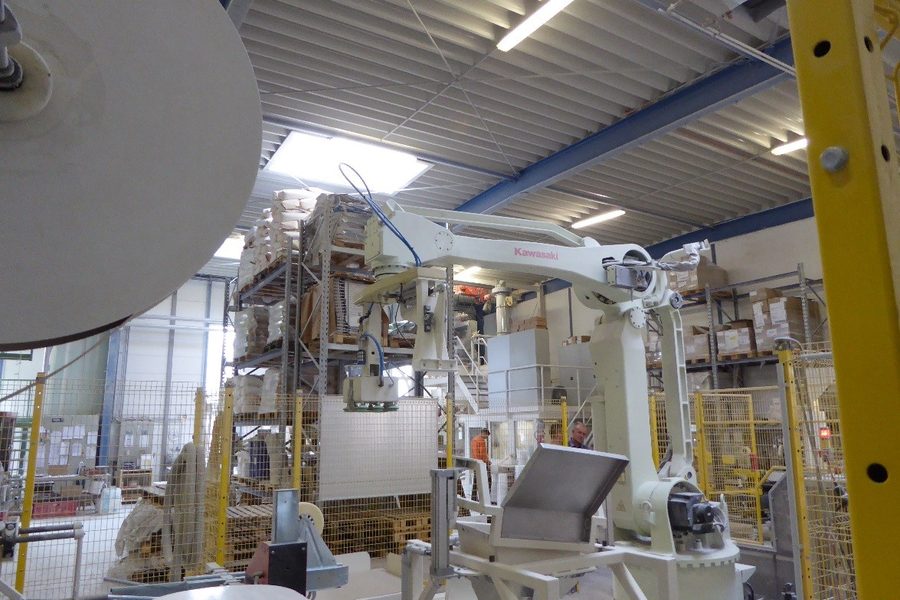
CHALLENGES
Dusty Environment
Historically, dusty industrial environments have not been ideal for automation. However, ERNST HINRICHS Dental has successfully used their Kawasaki Z series palletizing robots for the packaging of dental plaster for years. The Z series’ wrist motors are located on the shoulder, making them able to operate in dusty environments.
Custom Gripper
To avoid a time-consuming tool switch, this application required a gripper capable of accomplishing three tasks simultaneously. ERNST HINRICHS’ system integrator Wehling Anlagen-und Maschinenbau developed and constructed a multi-function gripping tool to grip bags of varying sizes, orient them properly, and compress them in the finished boxes.
SOLUTION
- Dental plaster is processed, packaged and sealed
- Kawasaki ZX130S robot picks bags from conveyor and places into boxes
- Case erector is used to construct boxes
The entire filling and packaging facility consists of a carton erector, sagging plant, case sealer, Kawasaki ZX130S robot and multiple conveyor systems. It processes several products at the same time, with minor variations depending on the product category.
To begin the process, the sagging plant finishes, packages and seals the dental plaster product in 20 kg bags. From there, a Kawasaki ZX130S robot picks the bags off a conveyor using a multi-functional gripper and loads them in a box produced by a carton erector.
If not properly positioned, the bags may swing in a pendulum movement inside the box when shipped. To counteract this movement, the robot places the bags into the boxes along a sliding plate and compresses the bags. Next, the boxes are properly sealed for distribution.
Reliable, High Performance Robots
Kawasaki robots are known in the industry for their reliability and 10,000 hour maintenance intervals, which translates to automation users can rely on day in and day out. From a technical standpoint, the general-purpose Z series combines a large payload capacity with a long reach for a minimal amount of dead space, wide work envelope and greater flexibility. These robots use high-output, high-revolution motors and advanced motion control technology to reduce cycle time and maximize production.
RESULTS
- System packs 120 boxes per hour and 2,000 boxes per day
- ERNST HINRICHS Dental increased production and improved flexibility
- Employees relieved of ergonomically challenging tasks
By automating their packaging process, ERNST HINRICH Dental increased production and flexibility, allowing them to put product into their customers’ hands quicker than ever before. Automation also relieves employees of physically taxing end-of-line tasks, creating a safer and more pleasant workplace.
ERNST HINRICHS Dental transitioned from a three-shift to a two-shift operation because of this system. They are currently producing roughly 120 boxes per hour and 2,000 boxes (40,000 kg) of dental plaster per day.
Since implementation, ERNST HINRICHS Dental’s system has proven to run smoothly and be user-friendly. Stefan Schuetze, Head of Procurement, explained that automation has had a positive impact on their company: “The robot allowed us to increase production significantly and relieve our employees from exhausting physical labor.”