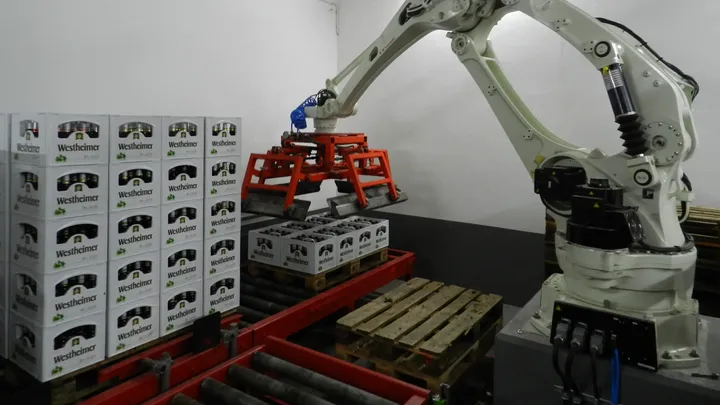
- IndustriesFood & Beverage
- ApplicationsPalletizing
- Robot SeriesCP series
OVERVIEW
Westheimer Brewery, founded in 1862, is a private brewery rooted in more than 150 years of tradition. From their factory in the Sauerland region of Germany, they produce regional beer specialties and prepare them for distribution both regionally and internationally. In order to remain competitive in an increasingly diversified market, Westheimer installed a Kawasaki robot in August 2017, one of the first to do so among their competitors. The ease, flexibility and efficiency of their automated system has inspired them to automate additional processes in the future.
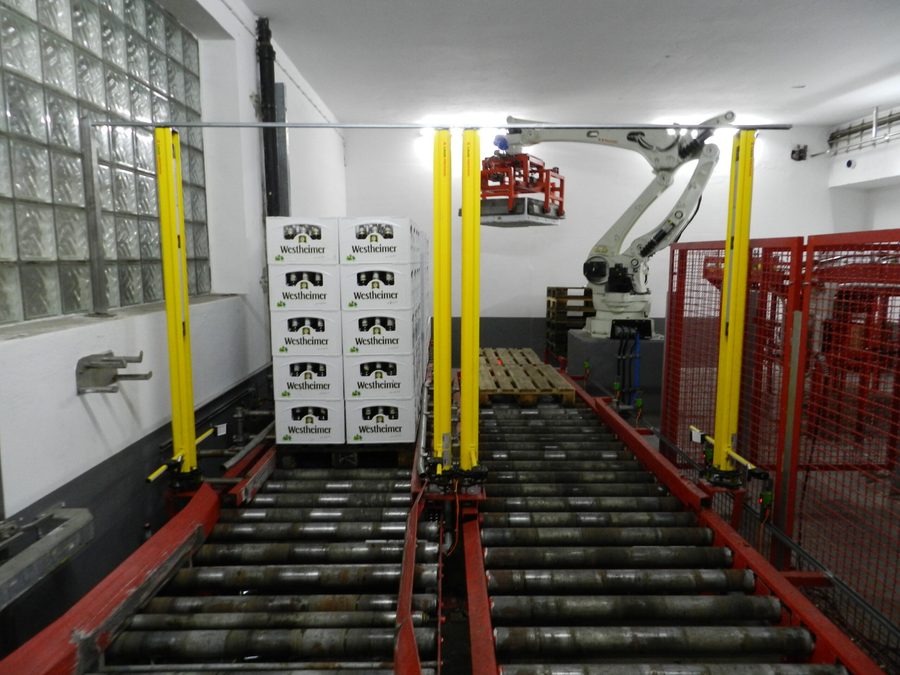
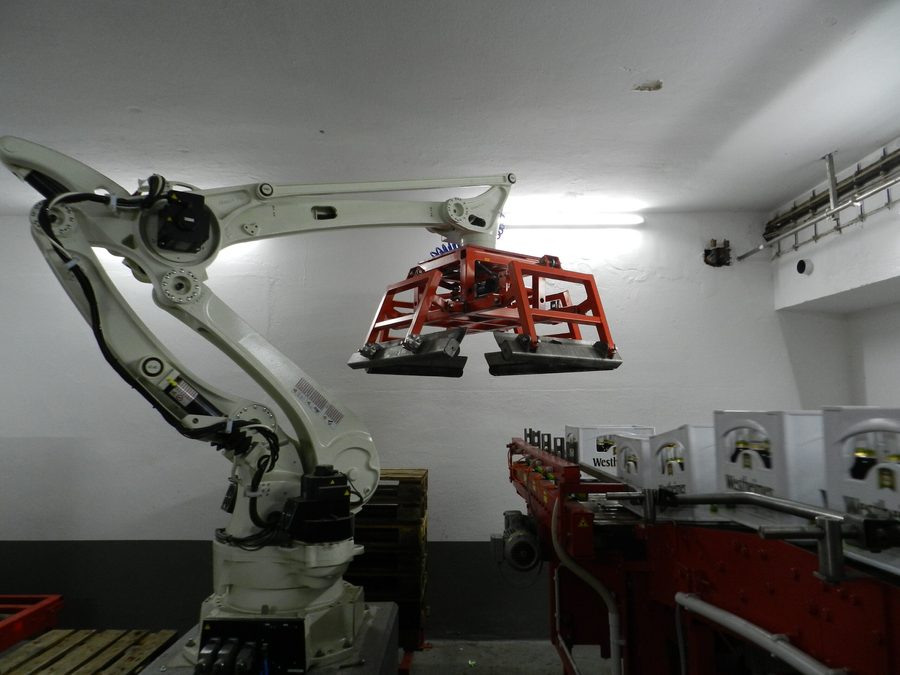
CHALLENGES
- Qualified workers increasingly difficult to find
- Current tasks ergonomically challenging for employees
- Antiquated existing machinery prone to breakdowns
- Flexibility a must for evolving product line
Finding qualified workers is a growing challenge for Westheimer Brewery and the greater manufacturing industry. The number of applicants in the region is continuously declining, which can cause lapses in production. In addition, Westheimer wanted to reduce the physical strain on employees that can be caused by end-of-line work.
The brewery’s previous, older palletizing machinery would frequently break down, making it clear that it was time for modernization. “The modernization and automation of the plant must begin here. In the long term, the entire infrastructure of the bottling plant will be renewed and optimized.”
The production volume of the Westheimer Brewery has remained at a constant level for years, but the increasing product diversification was another factor the company had to consider when building their new system. It had to be flexible and adaptable to new products.
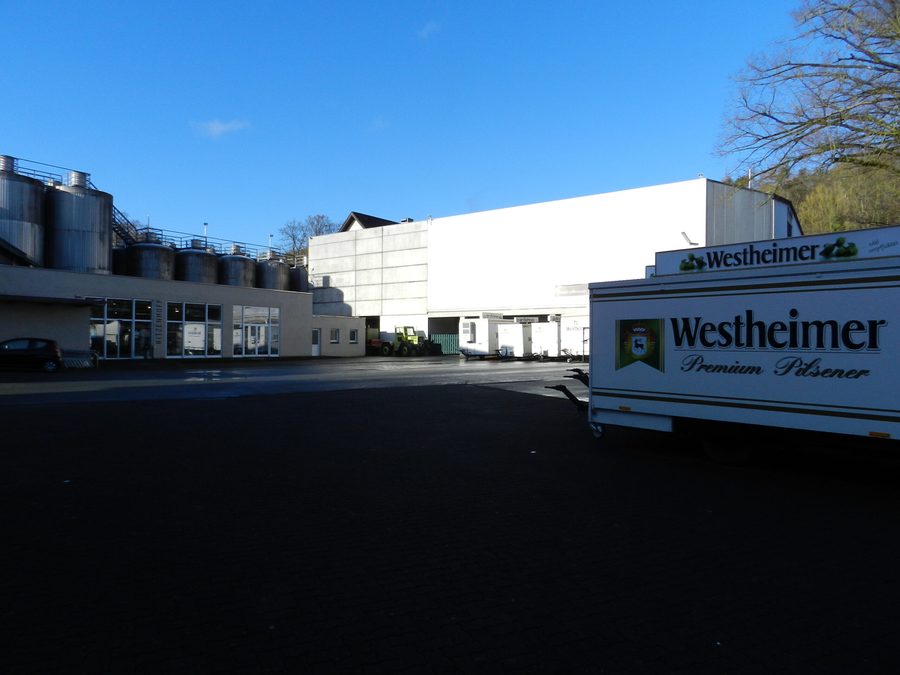
SOLUTION
- Kawasaki CP500L robot and Cubic-S safety hardware/software installed
- Robot loads empty bottles onto pallet en route to filling station, and filled bottles onto a pallet for distribution
- Tool changing station allows system to adapt to product changes
Empty bottles are manually fed into an automatic sorting machine at the entrance of the plant, where they are cleaned and rinsed. After filling, the bottles are inspected and placed in crates. These steps are still manual, but Westheimer plans to install a pick and place robot in the future to handle these tasks.
From there, production takes place on two interconnected levels – empty bottles and the final product are processed on the lower level, and bottles are filled on the upper level. In the new system, a conveyor belt transports the bottles between the two levels, which allows crates to be loaded and unloaded by the Kawasaki CP500L palletizing robot.
The robot sits on a concrete base with cabling laid through its interior. The brewery worked with German Kawasaki integrator Schröder Engineering Team to design the ideal system for their process. Together with Kawasaki Robotics GmbH, the integrator was involved in every step of the installation.
Flexibility achieved
The new palletizing system is flexible and adaptable to new or different products. A tool changing station is connected to the magazine, where the right gripping tools are readily available for the robot to change based on product type. This flexibility not only saves time, but also enables significantly higher and consistent product quality.
The high degree of flexibility is also a great advantage when it comes to external orders. Westheimer Brewery works in a one-shift operation, and special orders – such as organic beer – are added at regular intervals. They also support other breweries from their large network and numerous craft beer labels and start-ups that have shaped the beer market in recent years. Having a flexible automated system allows Westheimer to more easily keep up with beer industry trends.
“In the 1970s, 1980s and 1990s the question in breweries was simple: barrel or bottle?” Tolzmann said. “Today, we change production four times a day on average – precise planning and flexibility are essential.”
High performance robot & safety software
To meet their goals, the brewery needed a workhorse with a high payload that could fit in their space. The Kawasaki CP500L robot checked all of the boxes: the compact palletizing robot has a payload of 500 kg and a maximum speed of 900 cycles per hour. With a reach of 3,255 mm, a palletizing height of 2,200 mm and a net weight of only 1,650 kg, it is the most powerful robot in its class.
In addition to the speed, precision and compact design of the robot, the independent loading of the machine and Kawasaki’s Cubic-S safety system were also key selling points. A new chain gripper for the same purpose would have been required more programming, and been more susceptible to faults.
After a few weeks of fine-tuning and a comprehensive safety check, the plant went into operation in August 2017. When the installation was completed, Tolzmann was pleasantly surprised with the seamless transition. “I know from other companies that comparable plants were not ready to start even after eight months,” Tolzmann said. “Here, everything was ready in less than two months. We were also able to remain within our budget without any problems.”
RESULTS
- Robot palletizes at a rate of 1,200 crates per hour, with potential to go 25% faster
- Employees redeployed to more suitable roles
- Brewery plans to introduce more robots for other processes
Currently, the Kawasaki robot CP500L processes more than 1,200 crates per hour – and there is even more potential, says Tolzmann. “For optimum coordination with our older machines, we are not yet able to cope with the speed of the robot. After the modernization of our conveyor system, the robot will be up to 25% faster.”
Thanks to its integrated control system, the robot enables effective crate handling utilizing a single machine in a small space. The Cubic-S-based safety system also functions reliably and easily: As soon as the door to the robotic cell is opened, the power is switched off and employees can enter the system without hesitation. A one-week training course at Kawasaki Robotics taught Jörg Tolzmann and integrator Thomas Juckenath everything they needed to know to operate the robot.
The brewery’s robotic palletizing system simultaneously helps them combat an industry-wide labor shortage while allowing them to redeploy their existing employees to more human-friendly roles better suited for their skills.
Blazing a trail
From Jörg Tolzmann’s experience, the automation of the brewery market is still at an early stage – despite some pioneers. Although trade fairs show a clear trend towards robots, equipment such as light barriers, pneumatic motors and mechanical solutions are really the closest most breweries get to automation. In addition, many of Westheimer Brewery’s suppliers do not yet rely on robot-based automation. “The companies know their old machines and the necessary maintenance,” Tolzmann said. “But we know from our own experience that thinking outside the box quickly pays off.”
The new CP500L robot is just the beginning in the Westheim Brewery. In the long term, the company plans to replace more machines robots and automate numerous steps in their process. Jörg Tolzmann and his team plan to continue combining traditional brewing art with modern bottling and production processes.