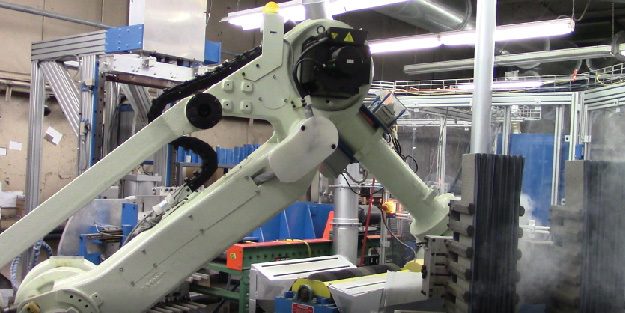
- IndustriesElectronics
- ApplicationsMachine Tending
- Robot SeriesZX series
OVERVIEW
Manufacturers use automation to take their operations to the next level. Whether it is increasing throughput or decreasing labor costs, robotic automation gives enterprises of all sizes the opportunity to expand their business. They can also eliminate pain points in their processes, which oftentimes has a ripple effect of unforeseen benefits throughout the organization.
Battery Builders, LLC. (BBI), is a Naperville, IL based industrial lead-acid battery manufacturer. When they decided to upgrade their facility, it seemed obvious to include their six-station COS (Cast-On-Strap) machine in the update. They worked with robotic integrator MAC Engineering from Benton Harbor, MI to install a large payload Kawasaki robot within a 6-station robotic cell. Almost immediately after installation, Battery Builders saw a more consistent product – an unforeseen benefit that had a huge impact on their business.
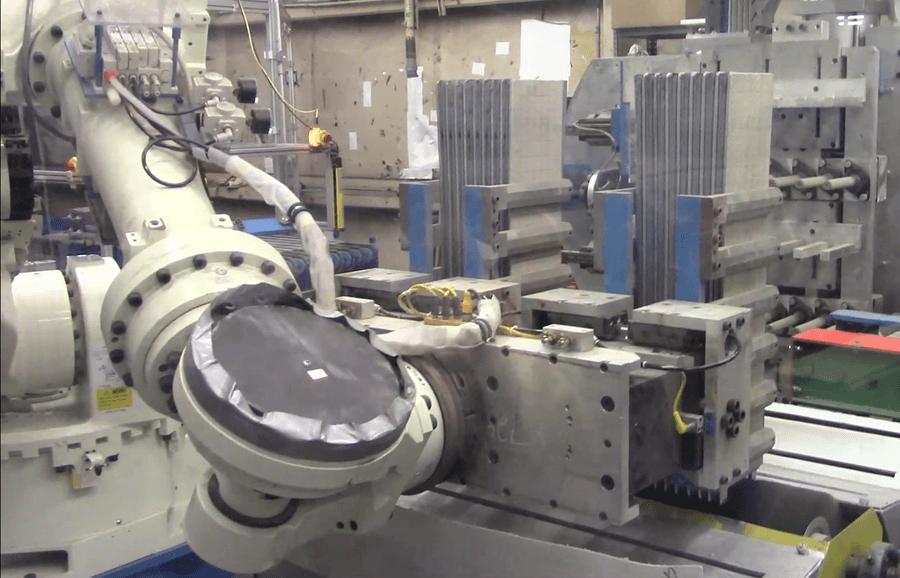
CHALLENGES
- Precise, versatile robot needed to tend multiple machine types
- Must decrease number of operators needed
- Need to increase throughput and product quality
The robot needed to have a high payload and high repeatability in order to lift and align the battery plates accurately. BBI also needed to be able to rely on their robot and peripheral equipment to meet steep production goals. The company set out to process 1,000 battery cells per day – more than double their daily production – using less manpower.
Top of Mind: Reliability
BBI was plagued by frequent machine breakdowns from their manually run COS machine, which they had for over 25 years. The antiquated machine was causing costly delays in production – BBI experienced four to five hours of downtime a week.
Health & Safety Risks
Manually handling battery plates generates more airborne lead dust than an automated process, posing a greater risk for exposure. The older machine also required employees to lift heavier loads, resulting in a greater risk of injury. For BBI, it was important to see the positive impact of automation reflected in their work environment – not just on their bottom line.
One Robot, Six Stations
BBI had to install a robot precise enough to consistently align 300 lbs. of battery plates up to 500 times per day. The robot also needed to be able to brush off the end connectors on the batteries, dip them into molten lead, and package them in a plastic jar, among other tasks. In order to accomplish this diverse list of detailed tasks, they needed a versatile robot.
Streamline Operations & Redeploy Employees
One of the manufacturer’s primary goals was to increase their overall plant efficiency and increase their battery cell production numbers. The old COS process they targeted for automation required nine or 10 employees to operate, and they were looking to decrease that number. BBI also recognized that their employees could be more useful in other areas of the manufacturing plant.
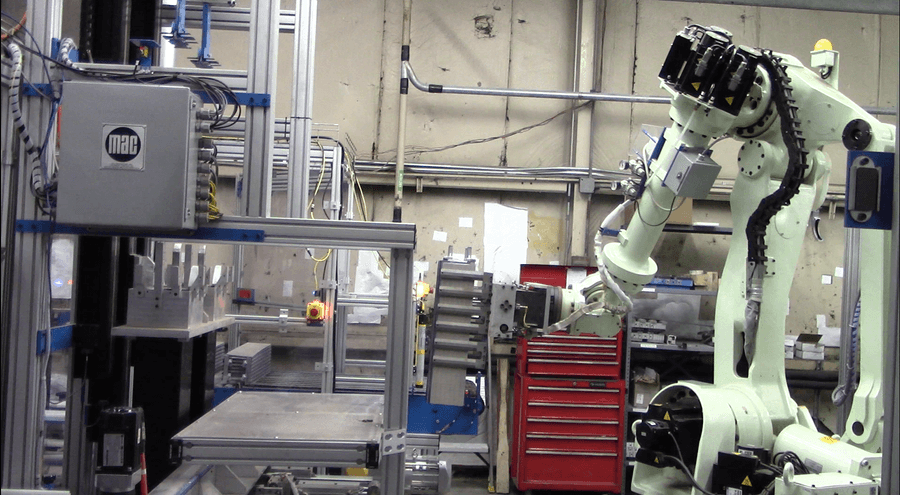
SOLUTION
- One robot moves product through entire six-station COS process
- Number of operators needed to man this process decreased from seven to five
Almost immediately, Battery Builders saw the advantages of their newly installed Kawasaki robot reflected in the quality of their end product.
The number of laborers needed to man this process has gone down from seven to five. The robot steps in after the battery plates have been manually slid onto the conveyor to align the plates and ensure they are even and flush. During this new process, operators no longer have to lift the plates from the ground. They move of the plates laterally onto a conveyor which is a more ergonomically friendly move.
The robot picks up the plates and runs them over a bristle brush to remove any debris from end connectors. Next, the robot runs the product through a flux process. The end connectors are dipped into tin and again into molten lead. Last comes the case out process, where the robot places the battery plates into their plastic casing.
Kawasaki’s ZX300S robots can carry payloads of up to 300 kg. They combine a long reach arm with a minimal amount of dead space for a wide work envelope. They also have a high repeatability of ±0.3 mm, making them ideal for applications that require precision and heavy lifting. When combined, these features created the perfect solution for BBI, which required a robot to reach machines at varying heights.
Kawasaki’s newer large payload robots, the BX series, have even higher repeatability, ranging from ±0.06 to ±0.08 mm. They have a hollow arm structure, which allows for internal dressing of the robot. This feature allows for easy installation, maintenance, and minimized wear.
RESULTS
- One large payload robot covers enter six-station COS process
- Risk of employee exposure to airborne lead dust decreased
- Product quality and consisted increased significantly
- Throughput will increase by 150%
For BBI, working with their new robot has been smooth sailing. “The robotics part of this process was very easy. Installing the robot was no problem at all, it was very simple, and learning to work with it wasn’t too complex,” BBI Assistant Manager said.
Since replacing the COS machine, BBI experienced better product quality using fewer man hours, while creating a safer work environment. Employees who operated the old machine are now working in the battery assembly department, which allows BBI to put more man hours toward the final stages of battery assembly. These changes ultimately improve the quality of their batteries. Once all of the integration is complete, they will be able to increase production from 400 to 1,000 battery cells per day – more than double the output they saw prior to automation.