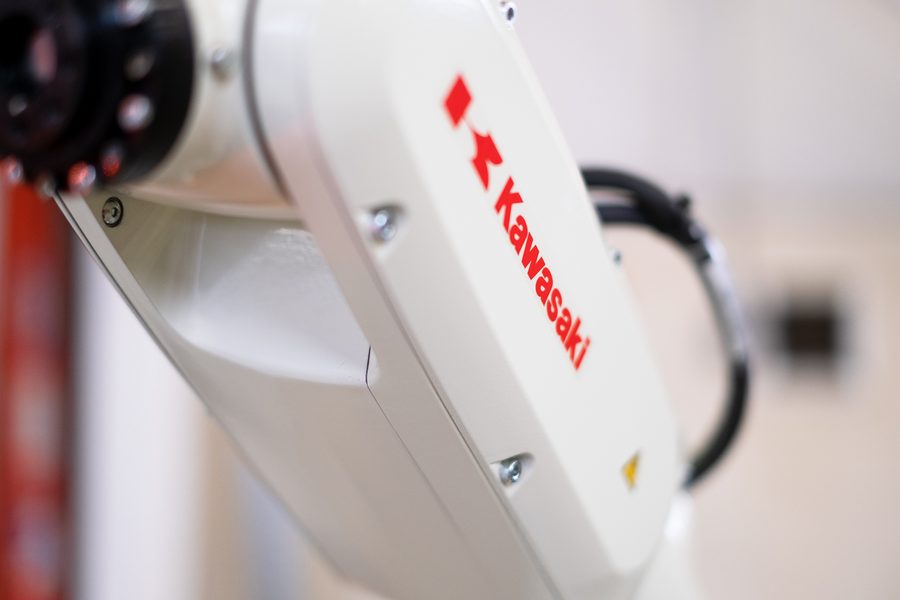
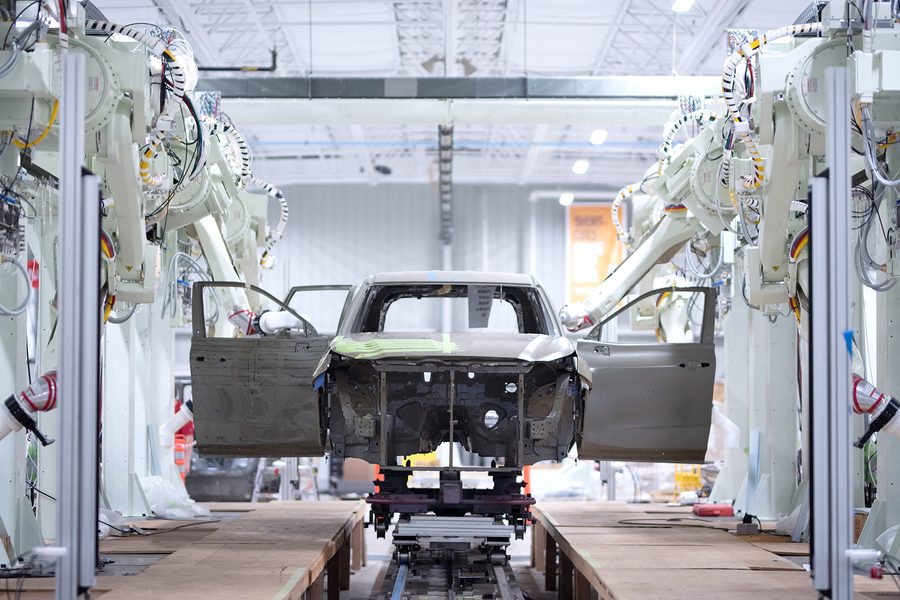
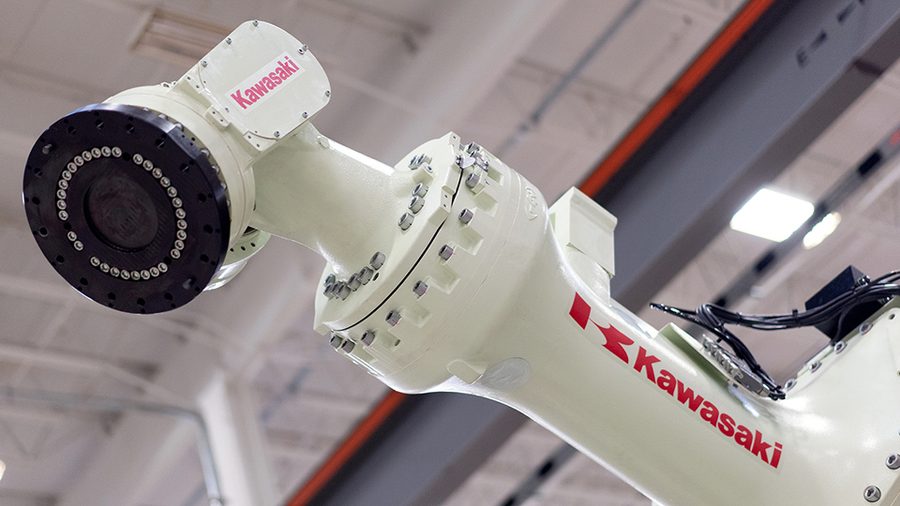
Robots, robotics and automation – what’s the difference?
Robots, robotics and automation are used almost interchangeably but have different meanings. Robots are the actual robot arms you see in a factory setting, and robotics is the technology that involves conception, design, construction, and operation of robots in manufacturing. Automation is defined as a technology that uses mechanical, electronic, and computer-based systems in operation and control of production. An automated robot system uses many components to autonomously complete a task.
What are the major types of robot applications?
- Material handling processes involve moving an item from one place to another, just as the name suggests.
- Assembly tasks require a robot to put something together. That could mean assembling multiple parts, like a gear box or a printed circuit board.
- Processing applications include tasks like painting, arc welding, spot welding, polishing, and grinding.
How do I choose the right robot arm for my application?
Take the following items into account:
- Payload is the amount of weight a robot arm can lift. Don’t forget to include the weight of the end effector and bracketing, if needed, into the payload calculation.
- Reach is how far your robot arm can reach vertically and horizontally, which helps define the robot workspace and the application design.
- Type is defined by the mechanical joints, rotary and/or linear, that impart movement to the robot arm. Robots come with one to seven axes: Cartesian, SCARA, Delta, Collaborative and Articulated robots.
What components go into an automated robotic cell?
A robot needs additional equipment to be operational and to carry out tasks. Here are a few examples:
- End effectors are also known as a gripper or end-of-arm tool. It’s mounted to the end of the robot arm and is central to the application.
- Cell controls include a controller that runs all operations of the cell. A teach pendant allows the user to program and operate the robot.
- Peripheral equipment encompasses a wide range of items, such as infeed/outfeed conveyors, part positioners, fixtures, vision systems and more.
- Sensors relay presence/absence information of parts to the robot. For example: When a part has reached a certain position on a conveyor, the sensor detects the part so the robot can execute a pick-up motion.
- Safety is the most important part of any automated robotic cell. Safety methods protect personnel from hazards associated with the robot cell in operation. There are a wide range of options for safety equipment, from full safety fencing to sensors that require no actual hardware.
How are robots programmed?
Every robot manufacturer uses its own programming language, however ours is an engineer’s best friend. Kawasaki Robotics’ programming platform is comprised of three powerful, intuitive, and flexible programming languages for the most basic to complex applications – we don’t limit your potential.
- Kawasaki Block-Step Language is our simplest programming language and can be used for most applications. It’s for the everyday operator and can be used to touch up points if necessary.
- Kawasaki AS Language is our more complex programming language, which allows users to write simple or complex motion paths and control logic. The open structure of AS Language allows users to program even the most advanced applications.
- KRNX is for our more advanced programmers. It uses an API that lets externally generated motion programs control the robot.
What types of applications are ideal for automation?
Industrial robot arms are ideal for tasks that aren’t ideal for humans. Here’s a list of criteria:
- Dull: Tedious and repetitive tasks
- Dirty: Applications in environments with lots of dust, paint or excessive debris
- Dangerous: Hazardous processes that put employees at risk of injury
- High precision: For products that require a flawless finish or highly accurate measurements
What are the advantages of robotic automation?
For the right application, robotic systems provide a wealth of benefits for the end user. A robot can run non-stop at a defined speed without supervision, which provides you the opportunity to increase production volumes.
Another benefit of robotic automation is consistency. Robots run with high repeatability and accuracy, and that is reflected in improved part quality. And by allowing robots to handle non-human-friendly tasks, employers can re-skill their workforce to more fulfilling work in a safer environment.
What measures can I take to make sure my automated robot system is successful?
When transitioning from a manual to automated process, you may have to make some changes to your part design, tooling, and fixtures to make sure it’s suited for automation. This investment will be justified in the cost savings you see once your cell is up and running.
It’s important to select a system integrator that will supply the robot system from the get-go. You want to partner with tenured experts that have expertise in concepting, designing, constructing, and commissioning the robot system. But don’t forget you’re the expert in manufacturing your product – it’s the combination of your expertise and their experience that results in successful applications.
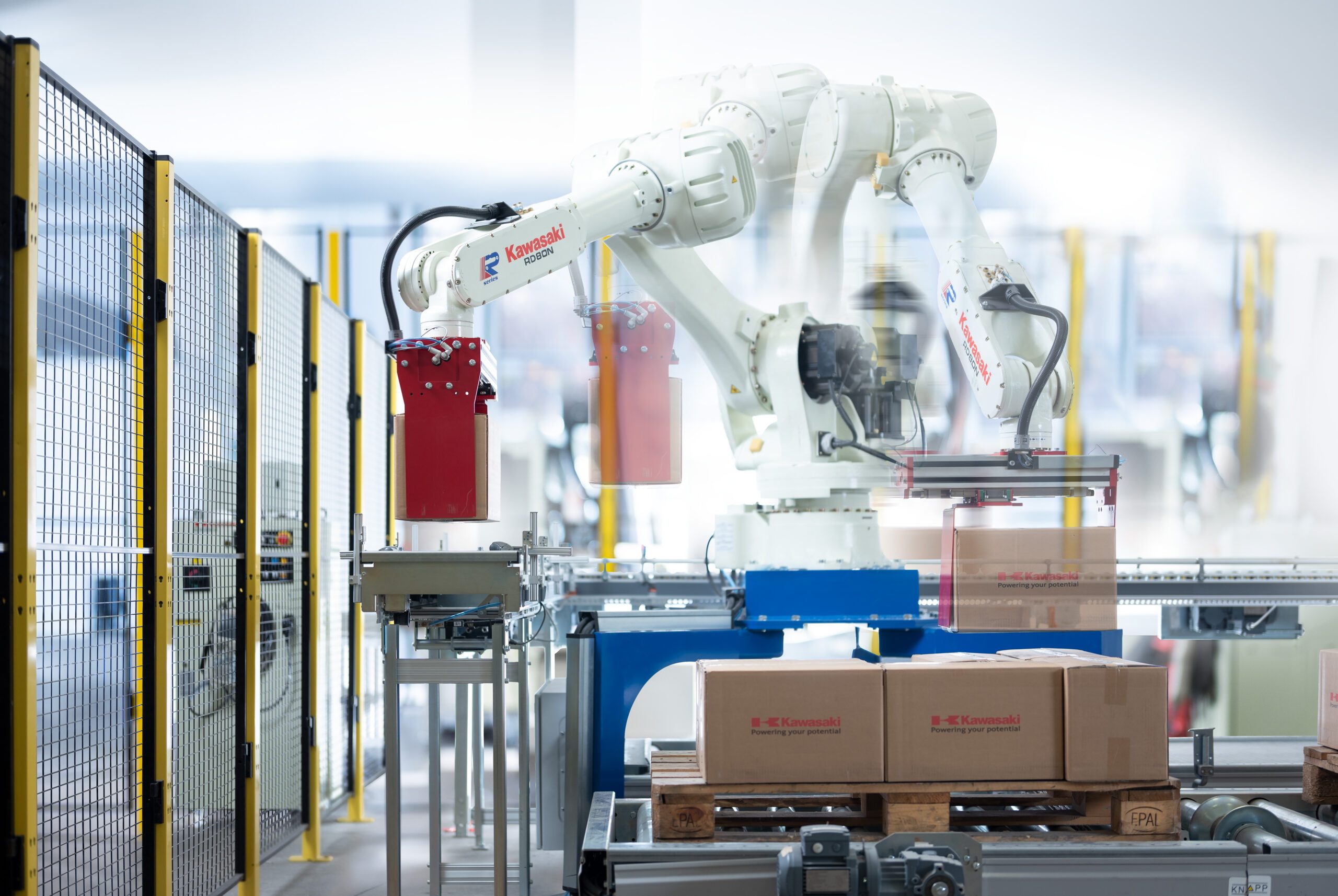
Still have questions?
We’re happy to chat.