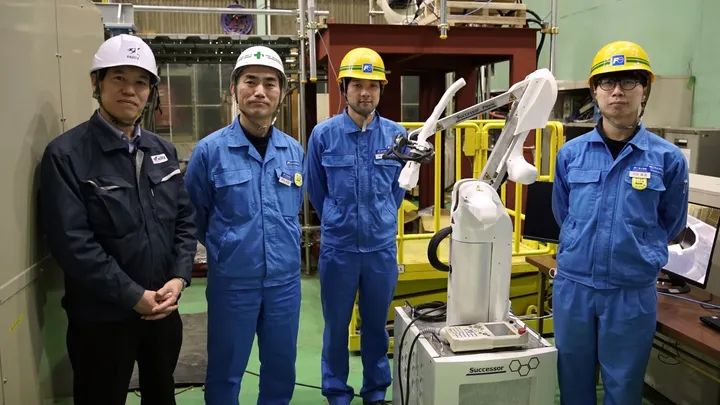
- IndustriesFoundry
- ApplicationsMaterial Handling
- Robot SeriesBX/BT series
Fuji Electric Co., Ltd.
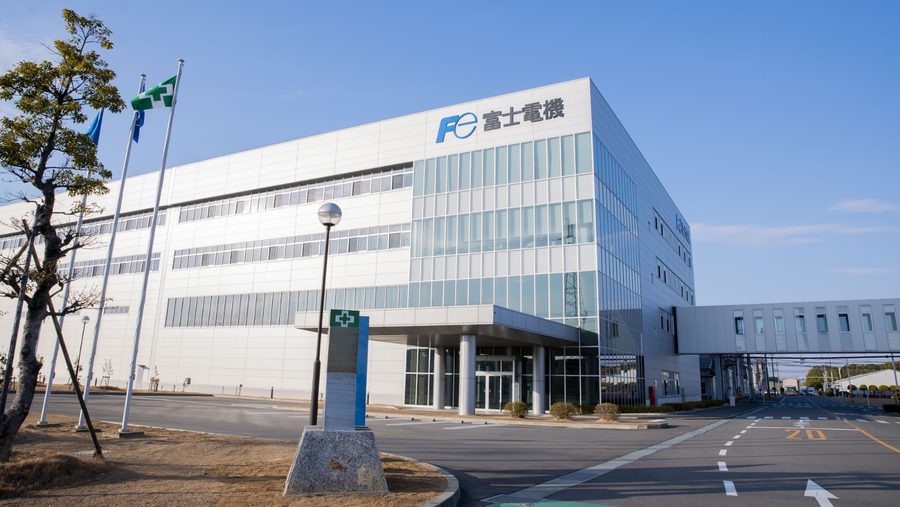
Fuji Electric Co., Ltd. is Japan’s heavy electric equipment manufacturer that produces a wide range of products and supports society, from power electronics products and semiconductors to renewable energy facilities, automatic vending machines and showcases for foods. The induction furnace, one of essential items for casting manufacturing industry is also a product of the company, for which it takes the top share in Japan. The temperature of the cast iron melting inside the induction furnace is 1,500℃. It would be good if the people working in this severe workplace could work in greater safety and security. This wish led Fuji Electric to start efforts for the practical application of remote work utilizing the remote collaboration system, the Successor for slag scraping around an induction furnace.
Introduction background/issues:
Slag scraping that was a bottleneck for the automation of casting workplaces
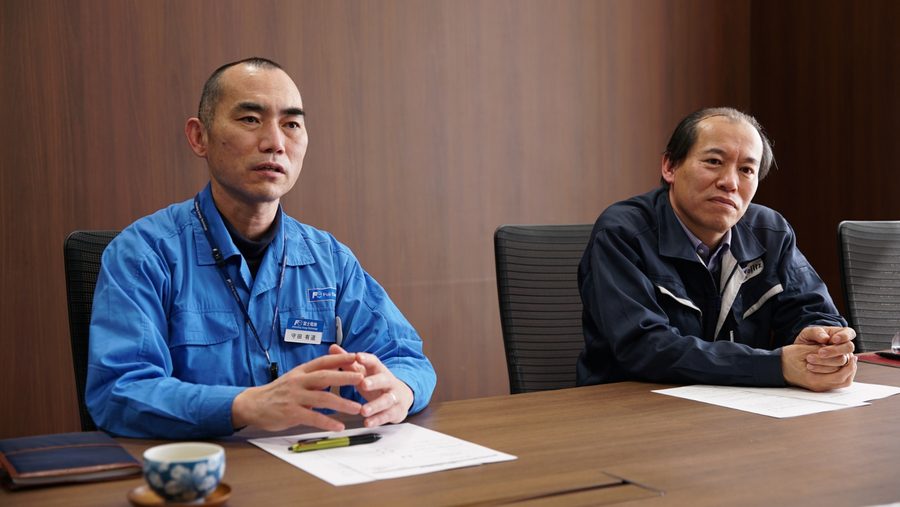
It is said that cast production began in around 4,000 B.C. Today, it is an industry inseparably linked with a wide range of sectors such as automobiles, aircraft and construction. In the casting process, melted metal material is poured into a mold and solidified in that state. The equipment used in the first stage of that process, to melt the metal materials, is an induction furnace. The mechanism is that electromagnetic induction is used to convert electrical energy into thermal energy, so that the metal materials inside the furnace heat up and melt. The structure is that an alternating current is made to flow in a coil wound from copper wire to generate magnetic flux lines, which is a familiar process also found in the induction hobs for household use. Using this physical phenomenon, induction furnaces have become the mainstay in casting workplaces today, as they offer a clean melting method that can be used instead of a cupola furnace or equipment using fossil fuel directly. After making their first model in 1964, Fuji Electric has since delivered around 2,600 induction furnaces in Japan and overseas.
When the cast iron is melted inside the induction furnace, iron impurities generate within the molten metal (melted iron), which can reach the high temperature of 1,500℃. These impurities are called slag. If they are not removed, then it is not possible to produce highly accurate cast parts. The slag generated in the molten metal is solidified using a coagulant and then a steel, rod-shaped tool is used to capture and scoop out the slag. This work is called the slag scraping and it is one of the processes that always occur in a casting workplace. The factory is hot in the first place. The work to remove slag which can weigh several tens of kg from the molten metal at 1,500℃ is a heat, heavy and dangerous work. As Assistant Section Chief Arimichi Morita, of the Fuji Electric, Power Electronics Industry Business Group, Process Automation Division, Industrial Electric Heating Technology Department explains, “The state of the molten metal, which is a liquid, and the shape of the slag are constantly changing, so it is not possible to deal with this using dedicated machinery or a robot, which are good at the repetition of fixed operations. The labor-saving in slag scraping has long been an issue for the casting industry.” Furthermore, aiming for and catching the slag with the tip of a long and thin piece of metal about two meters long is like using the tip of a fencing sword to aim for a small target. Know-how and skill are also required in order to scrape the slag out efficiently. It is truly heavy labor that requires human hands. There are expectations that the Successor remote collaboration system proposed by Kawasaki may be a solution that can release the employees from this severe labor environment of slag scraping.
Introduction effects/solutions:
Working “as usual” while viewing a monitor
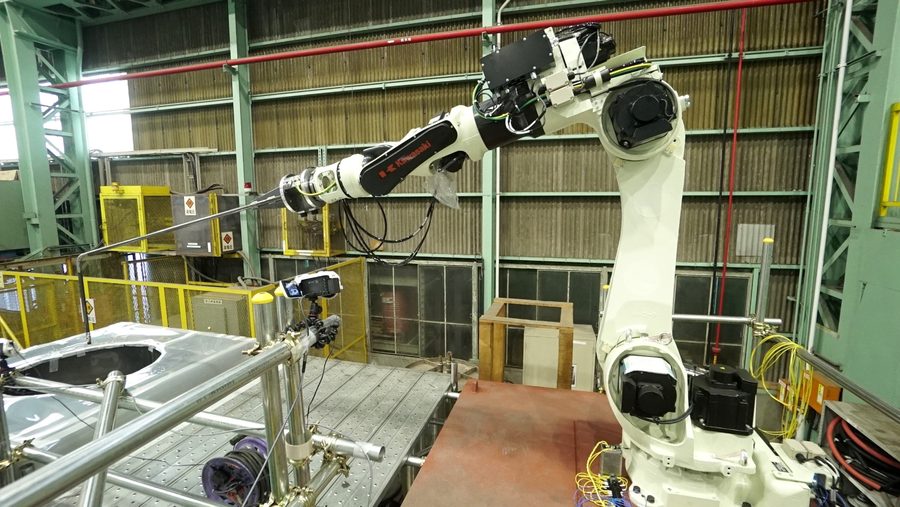
Sojitz Machinery Corporation is a general machinery trading company that distributes a wide range of manufacturing equipment, including the induction furnaces from Fuji Electric. The Mobility Division of Sojitz Machinery has proven results in the handling of a large number of the industrial robots that are essential for automobile production lines. As Yukio Kakuta, Specialist Department Manager of the Sojitz Machinery Mobility Division, Mobility Department 1, Section 2 says, “With the Successor, in addition to the operation originally intended with robots, operations that were impossible with just the robot alone can be complemented with the person performing remote operation instead. We thought that we would be able to create products with merits for the customers if we used that feature to create robot systems for sectors that have problems because automation has not been achieved.” In October 2020, Fuji Electric and Sojitz Machinery started to consider the use of the Successor in the slag scraping work for the induction furnace. In order to verify the movements of the robot, remote experiment equipment was set up in one corner of the Fuji Electric Suzuka Factory, with the combination of a real 5-ton induction furnace and the Kawasaki BX200L vertical articulated robot and the Successor.
A communicator called Plesio was selected for the operation of the Successor. A camera is installed in a position where it can look inside the furnace, and the operator checks the monitor from a location away from the red-hot molten metal. The design is such that it is possible to hold the rod-shaped communicator with both hands and operate it to remove the slag from the molten metal. The feature of this system is that the “usual” movement, which is like stirring the contents of a massive cooking pot with a big spatula, can be performed via the robot system. Mr. Morita says that the positioning of the melting furnace and the robot, and the length of the slag scraping tool on the end of the arm were, “determined after considering the ideal distance so that the robot would avoid the effects of the heat as much as possible.” The unique profile of the slag scraping tool, which is bent towards the furnace at the end, was also a result of ideas to ensure that the robot did not get too close to the furnace, and also so that the action to stir inside the bath could be reproduced with the movement of a six-axis robot.
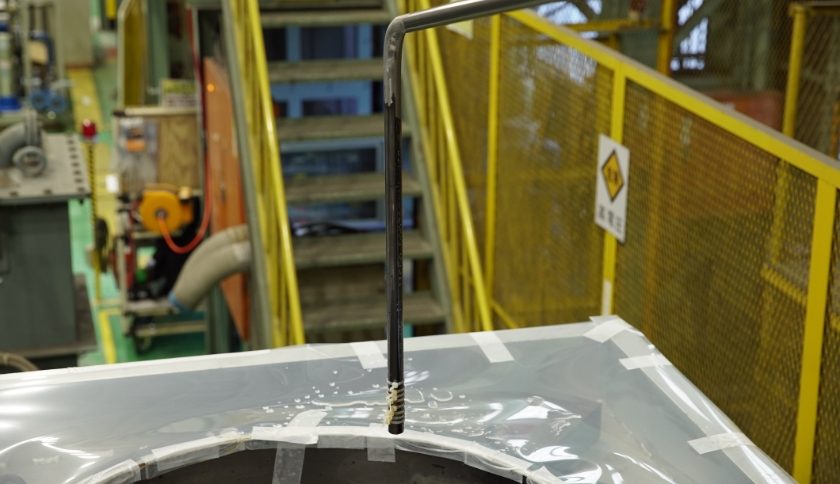
A force sensor has been installed on the end of the arm and the mechanism is that the reaction force is transmitted to the communicator. As Mr. Morita says, “How much feedback would make the work easier to perform? What is the optimal position for the camera? Should we install a heat-resistant camera close to the furnace, or place it away from the furnace and use a telephoto lens? We are currently in the process of considering the actual usability while repeating detailed testing.” The end of the scraping tool slowly melts due to the high temperature, so tool changer using a chucking tool is used. In addition, four ribs were attached at the base of the tool to secure strength and accuracy. Mr. Kakuta explains, “In the current state, the design provides quite large margins for the robot payload and the tool strength. In actual applications, it will probably be the case that customized systems are created, such as with a compact type robot to suit the environment in the customer’s workplace, or the application of a mechanism for simple tool changes.”
Future prospects and plans
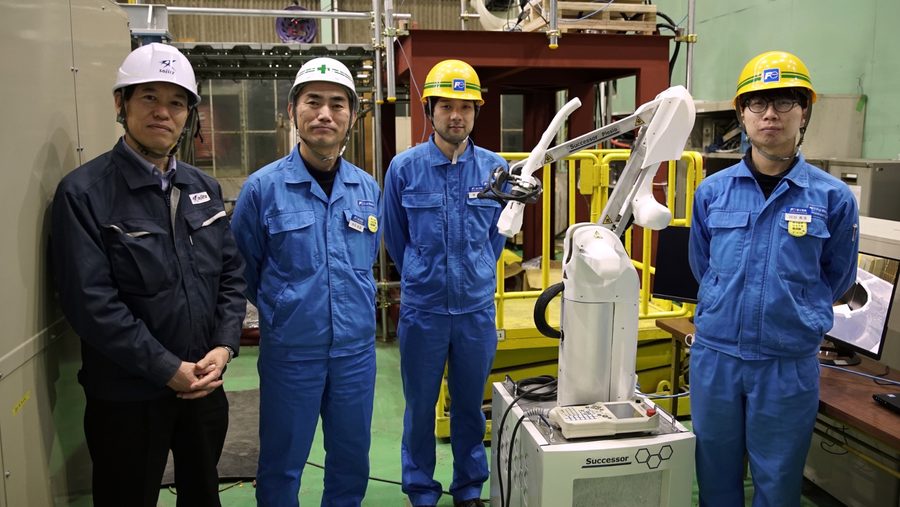
The robot system is currently being tested with water and dummy slag. However, Mr. Morita says that, “During fiscal 2022, we want to proceed up to the stage of actually installing the system in the workplace of a cooperating customer and performing actual slag scraping work.” In addition to the slag scraping, researches have also begun on substituting work to utilize the feature of the Successor by connecting the robot and human workers in remote collaboration. Mr. Kakuta says, “The workers around the furnace could be further reduced if the robot could also perform work such as measuring the temperature of the molten metal, and scooping up some of the molten metal, analyzing it and adding any components that are insufficient.” If the robot changes the tool automatically and it becomes possible to substitute it in for all of the temperature measurement, composition analysis and adjustment, and slag scraping, then the bottleneck of the casting process will be dramatically resolved.
The application of remote operation using the Successor will lead to the use of IoT in the entire casting factory — This is what Mr. Morita explains. “Installing a robot makes it possible to keep a record of the product quality. If it is possible to know what kind of melting it was, and what kind of materials the iron was made from, then this should also help improve quality.” This is a breakthrough remote collaboration system that reduces the personnel required around an induction furnace and creates a safe and secure environment for workers. It offers new possibilities for areas where labor-saving is difficult, both in Japan and overseas. Mr. Morita says, “When we have created the induction furnace system using a robot, we definitely want to spread it both in Japan, and also overseas.” The development of a future robot system that will bring safety and security to casting around the world is being advanced again today in one corner of a factory in Suzuka City, Mie Prefecture.
― Company information Company name Fuji Electric Co., Ltd. Representative President and COO Shiro Kondo Established August 1923 Capital 47.6 billion yen Core business Design and manufacture of social infrastructure, industrial infrastructure, power electronics equipment, electronic devices, and food distribution systems Employees 27,593 (as of March 31, 2021) Offices Head Office: 1-11-2 Osaki, Shinagawa-ku, Tokyo Suzuka Factory: 5520 Minami-tamagaki-cho, Suzuka-City, Mie Prefecture Website https://www.fujielectric.co.jp/ ― Robots installed Model BX200L, A six-axis vertical articulated robot that realizes fast operation speeds and high density layout. Features Lightweight arm, high output/high speed motor, fast operation speed thanks to the latest vibration control. A hollow structure wrist that accommodates wires and tubes inside the arm for a compact installation area. Max. payload 200 kg Axes 6 Positional repeatability ±0.06 mm Maximum reach 2,597 mm