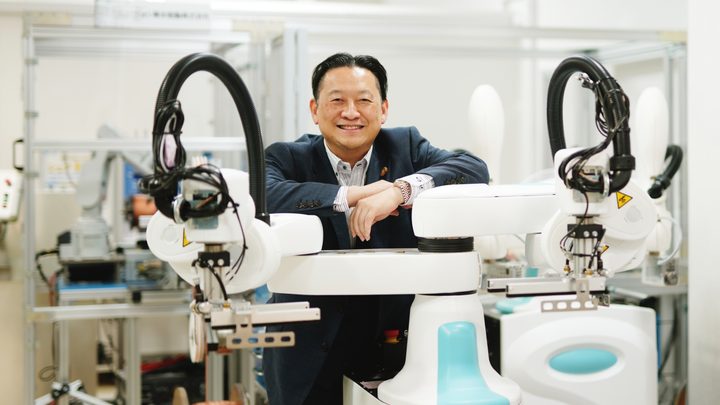
- IndustriesFood & Beverage
- ApplicationsAssembly, Material Handling
- Robot SeriesRS series, duAro series
System integrator: HCI Co., Ltd.
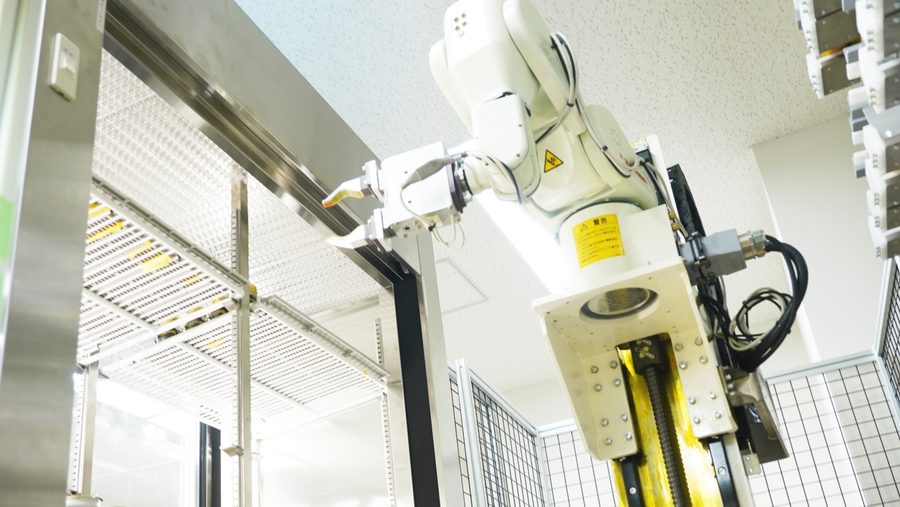
HCI Co., Ltd. was established in 2002 as a manufacturer of machinery such as twisting machinery for the processing, assembly and inspection of flexible materials including cables, wires and tubes. The company utilized the know-how it had developed in the world of machinery to start up a robot system integration business 12 years ago. That business has been highly rated for its flexible ideas and technological strength and is growing rapidly. The company is actively promoting the advancement of robots into society and has grown to become one of the leading robot system integrators in Osaka, with a large-scale R&D facility with a total of 41 robots, and an AI system development department.
Introduction background/issues:Realizing robot business in one year by utilizing knowledge in mechanical design and manufacturing
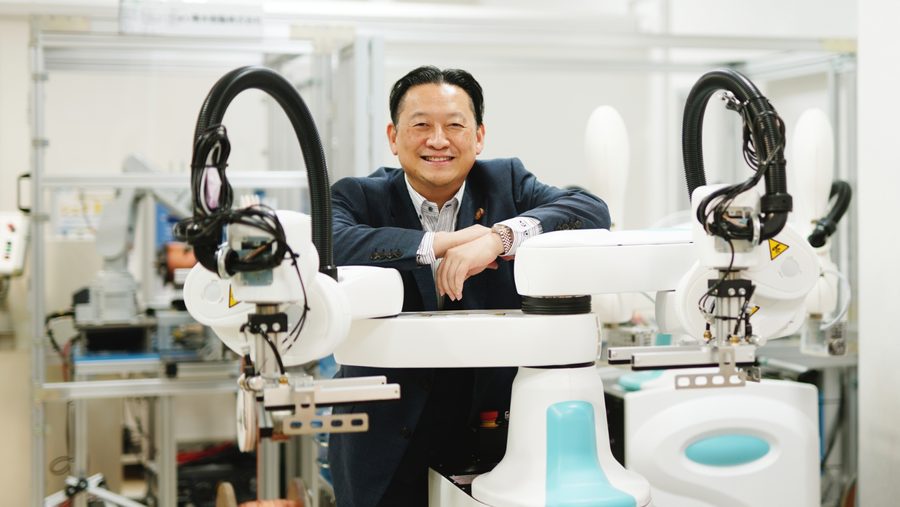
While conducting AI development in-house, the company is also catching up on the latest technologies from various directions, such as with the operation of the “Izumiotsu AI Research Group” to search for business applications for AI technology.
“Automated machinery is surely going to become increasingly necessary in the era of declining population from now on.”
After working at another machinery manufacturer, President Okuyama anticipated the wave of automation that will surely come. In 2002, he started up a company to make manufacturing equipment for cables.
With his background of being able to design and produce original machinery that is not possible elsewhere, he developed machinery for high-speed twisting of ultra-fine cables with a diameter of 25 microns.
The cables thinner than a human hair were essential for the folding type mobile phones that were spreading at a rapid speed at that time, so there was great demand for their manufacturing equipment.
The sales of the original twisting machine developed increased rapidly and this quickly formed solid foundations for the business.
However, in November 2008, there was the shock of the Lehman Brothers’ bankruptcy.
President Okuyama thought that it would be necessary to have a new pillar for the business in addition to the existing manufacturing business, so he began the development of robot systems, which he had wanted to do since the establishment of the company.
President Okuyama says, “There are a great variety of factories in the world, and also, with robots, it is possible to get into various areas such as medical care and services.
Fortunately, as a machinery manufacturer, we had the knowledge to be able to do everything from design to component production, assembly, panel production, wiring and electrical control.” Let’s do robots!
In 2009, just one year after making that decision, HCI managed to deliver its first machine as a robot system integrator.
Although the sales at that time were almost entirely for the manufacturing equipment for wires and cables, the strong demand for the robot business continued to grow each year.
It has now grown to be more than 60% of the business overall.
Furthermore, in addition to striving to acquire and nurture young engineers from overseas, such as from India, Indonesia, Vietnam and Myanmar. In 2017, the company also started the in-house development of artificial intelligence (AI).
It opened a R&D lab which has 41 robots and develops unique robot systems that can support workplaces in any industry, from component transfer, assembling, packaging, picking and inspections.
Introduction effects/solutions:Automated box packing system using a dual-arm robot, the duAro
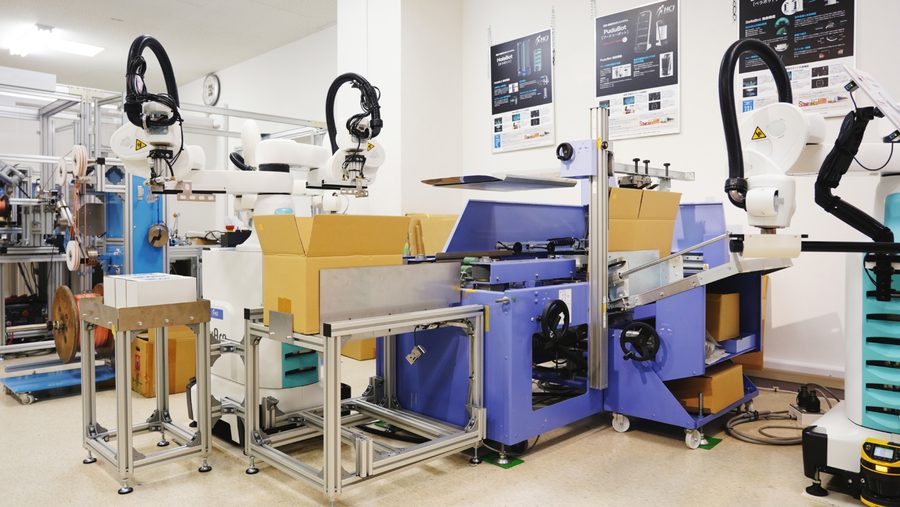
The box packing work itself could be performed by applying a six-axis articulated robot, but with duAro, the work area is kept compact and also work in collaboration with humans is possible without the need for a safety fence.
In addition, the cost for the system is reasonable.
HCI developed the automated box packing robot system in collaboration with a manufacturer of case formers for corrugated cardboard.
The case former is combined with Kawasaki’s duAro collaborative dual-arm SCARA robot to automate the processes of forming a box from folded corrugated cardboard to product picking and to box packing.
The greatest reason for selecting duAro for this system was its dual-arm construction. Its feature is utilized to the full. For example, they are used to fold the flaps that will form the cardboard box lid to the outside to create a shape that will make the insertion of products easier, or to clamp with two arms the products placed randomly and align them before packing.
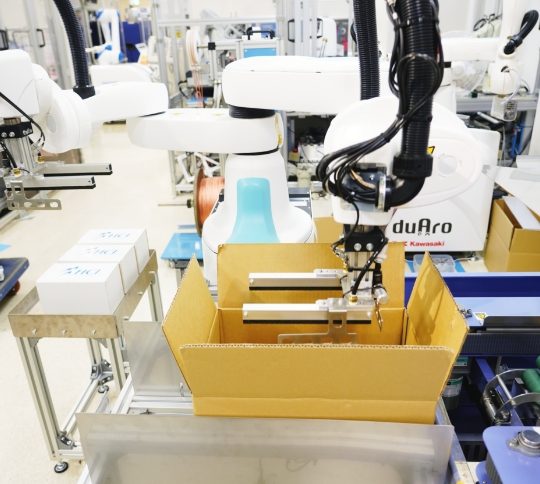
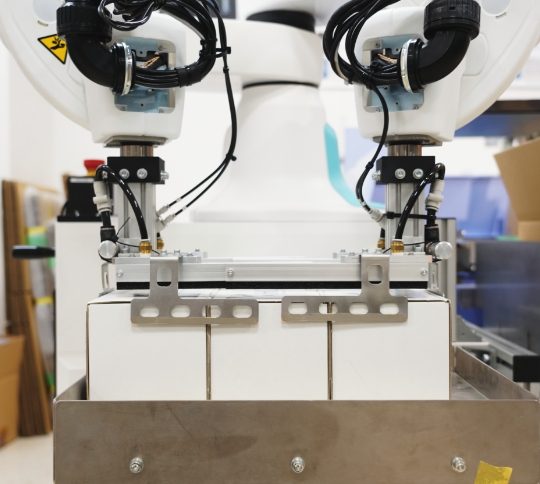
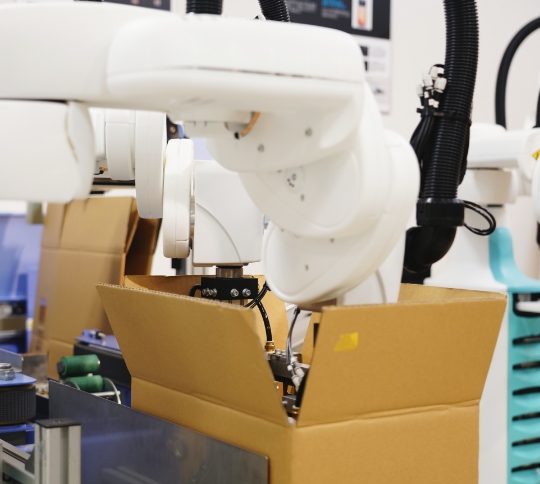
▲Box packing work processes using duAro.
First, hands with brackets attached are used to widen the flaps of the cardboard box outward to make packing of the products easier.
(Left photograph) Next, the products are held by clamping them with the two arms.
(Center photograph) Finally, duAro packs the products in the cardboard box.
A duAro demonstration robot assumes the packing of small, lightweight boxes into a box and is equipped with hands that have brackets and vacuum grippers.
The specific processes
The duAro performs the series of the following tasks: (1) move the cardboard box transferred from the case former to the preset position,
(2) fold the four flaps on the cardboard box outward so that they will not close the box,
(3) use the brackets to gather together the workpieces placed randomly, and then vacuum-grip them, and
(4) pack them in the cardboard box.
Robot systems can be used to pack a number of small boxes into a cardboard box in various industries, including stationery and cosmetics makers.
“The system can be used widely wherever a workplace has a process to pack in boxes for shipment” (President Okuyama).
Since it is possible to work together with humans, the overall dimensions of the system can be kept compact. It can be installed anywhere, regardless of the scale of the site. This is another merit of the system.
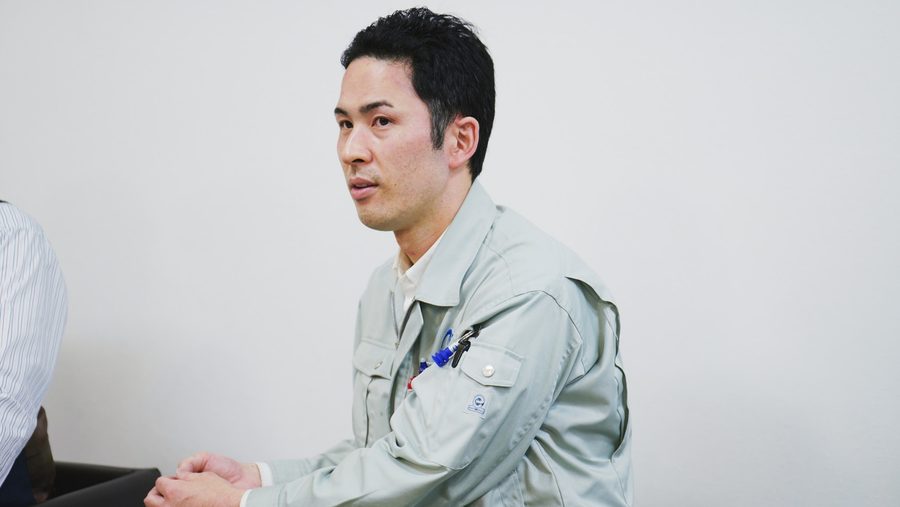
Every day, the company is developing a great variety of robot systems that can be applied to various work tasks, such as the press forming process for resin, and the fitting (fitting together to assemble) of components.
Robot system to automatically display drinks facing its front
The “automated drink displaying robot system” is expected to be used in supermarkets and convenience stores.
Shelf stocking or shelf filling is a backyard work to fill the shelf and display a sufficient quantity of bottles and cans in a store. It is performed in interval times and therefore often the case that it cannot be managed during busy time.
A robot system enables the products to be filled and displayed automatically around the clock.
In addition to reducing the workload for employees, it is also possible to prevent cases of products running out during the busy periods.
The automated drink displaying robot system is composed of an RS003N six-axis articulated robot from Kawasaki, an originally developed transfer unit, storage shelves and display shelves.
The RS003N robot has a gripper that can grasp various products such as 350 ml cans and plastic bottles, and also a distance sensor.
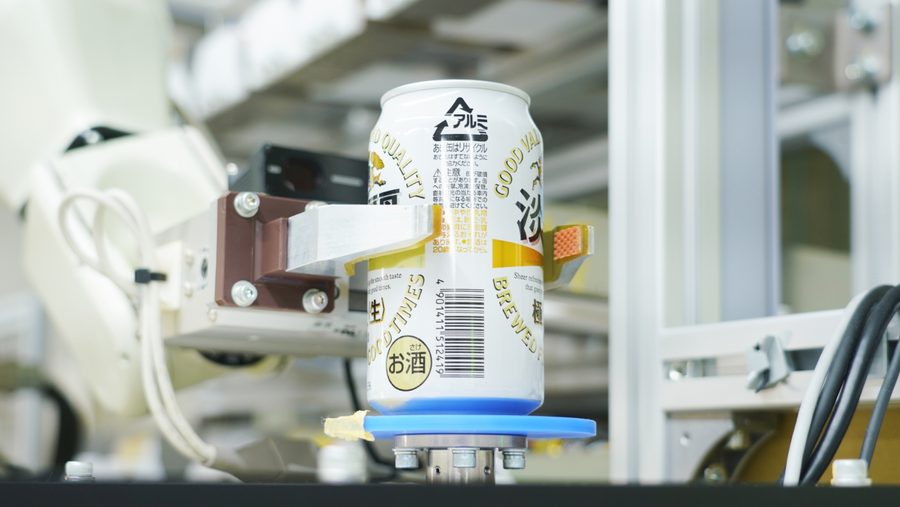
The blue part on the bottom is a turntable and the position of the barcode is used to check and adjust the angle of the product so that the label is always facing the front of the display shelf.
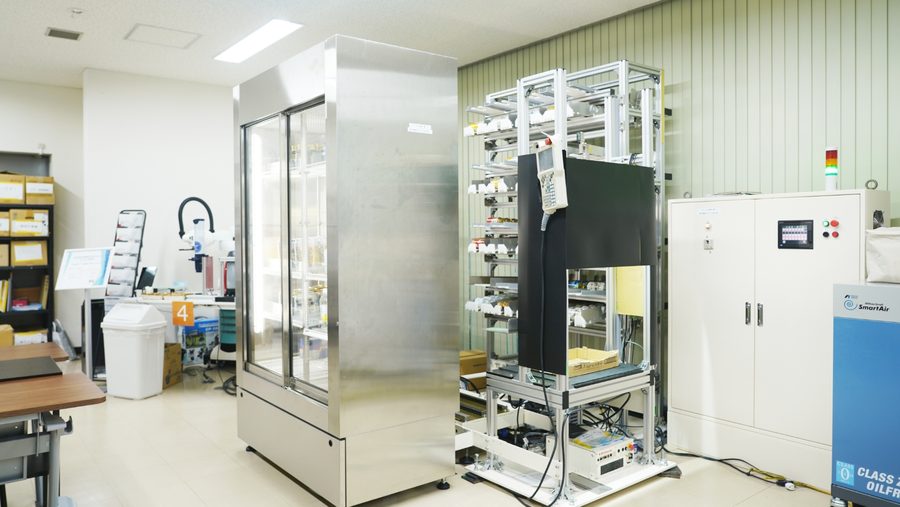
The robot moves between those two and constantly uses a sensor to search for the display slots that require refilling.
The RS003N moves in the horizontal and vertical directions on a travelling device and constantly monitors the product quantities with sensors.
When refill is necessary, the robot picks up a product from the storage shelf and places it on the turntable. The camera in the equipment then reads the barcode and the angle is adjusted (face-up) so that the product is displayed facing forward. The hand then grasps the product and refills it on the display shelf. This series of tasks is implemented seamlessly with centralized control using a PLC.
The time required from the pick-up, face-up and refill is about 20 seconds.
“We investigated how many degrees the product must be turned from the barcode position so that it would face forward to make this face-up displaying possible.
It is also possible to change the rotation angle for each different product.” (Akihiko Hamamoto, Acting Manager of the Design and Development Department and Group Leader of the Machinery Design Group)
The information for each product is linked to the locations on both the display shelf and the storage shelf.
When the inventory on the storage shelf runs out, the products for stock are placed on a reading area that is equipped with a camera. Then, the robot places the items in the designated location for each product.
Furthermore, it is possible to use a tablet device to check the status of the display and storage shelves from a remote location, and it is possible to receive notifications when inventory runs out.
The interface for the tablet device and controller unit was also developed in-house at HCI.
It has a user-friendly configuration and design for easy operations.
“In addition to the backyard work, we also have the idea of using a layout that actually shows the display work by the robot to the customers.
Wouldn’t children be happy if they could watch the robot perform its work behind glass?” (President Okuyama)
Future prospects and plans:The belief that “Robots will save people”
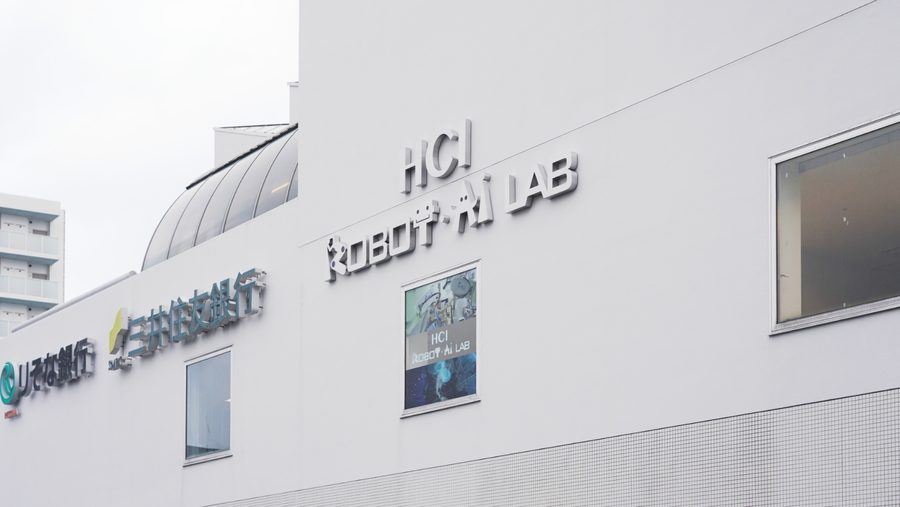
HCI has installed a wide variety of robots at the ROBOT AI LAB, ROBOT CENTER, test centers and elsewhere.
Verification of the work and takt time, etc. is performed using various sensors and hands in which system creation is performed for unique products.
The average age of the employees is 29.
HCI gathers young professionals in areas from AI and other software to hardware of machinery design, and is pushing forward to spread robots more widely into society.
The new headquarters relocated to in January 2021 has a company canteen, the HCI ROBO HOUSE, where robots conduct simple cooking and serve on a tray.
It is also opened to general customers as part of the company’s active efforts to increase the venues for robot use.
Our world is changing significantly after the coronavirus pandemic and the demand for robots will surely increase further — This is the assertion of President Okuyama.
“I believe that ‘Robots will save people’.
Up until now, robots have been something that goes in a factory, as is represented by the phrase of factory automation.
However, robots have the potential to go beyond this category and enter all industries, such as with smart factories, smart medical care, smart services and others.
I want us to continue to rapidly develop new robot systems in preparation for the cyber-physical society that is expected to arrive.” (President Okuyama)
― Company information Company name: HCI Co., Ltd. Representative: President and Representative Director Takateru Okuyama Established: June 2002 Capital: 20 million yen Core business: Production of manufacturing and testing equipment for cables, wires, tubes and sheets, system integration for robot and AI systems using industrial robots, service robots and custom order-made robots Employees: 50 Offices: Headquarters: 3-14-10 Higashitoyonaka-cho, Izumiotsu-shi, Osaka HCI ROBOT and AI LAB: Alzar Izumiotsu Building 2, 20-1 Asahi-cho, Izumiotsu-shi, Osaka HCI ROBOT CENTER: 10-7 Tanaka-cho, Izumiotsu-shi, Osaka Izumiotsu Shikinai Factory: 6-30 Shikinai-cho, Izumiotsu-shi, Osaka Kishiwada Shimoikeda Factory: 1-6-16 Shimoikeda-cho, Kishiwada-shi, Osaka HCI TEST FACTORY: 2-8-11 Itahara-cho, Izumiotsu-shi, Osaka Izumiotsu Itahara Factory: 4-17-38 Itahara-cho, Izumiotsu-shi, Osaka Website: https://www.hci-ltd.co.jp/ ― Robots installed Model: duAro2, a dual-arm SCARA robot with a collaborative concept Features: Compact space, simple teaching, simple installation and high level of safety Max. payload: 3 kg on each arm (6 kg with two arms) Axes: 4 axes on each arm Positional repeatability: ±0.05 mm Vertical stroke: 550 mm Model: RS003N, a compact vertical articulated robot with “a faster, wider, accurate and compact arm” Features: Compact design, lightweight, wide motion range Payload: 3 kg Axes: 6 Positional repeatability: ±0.02 mm