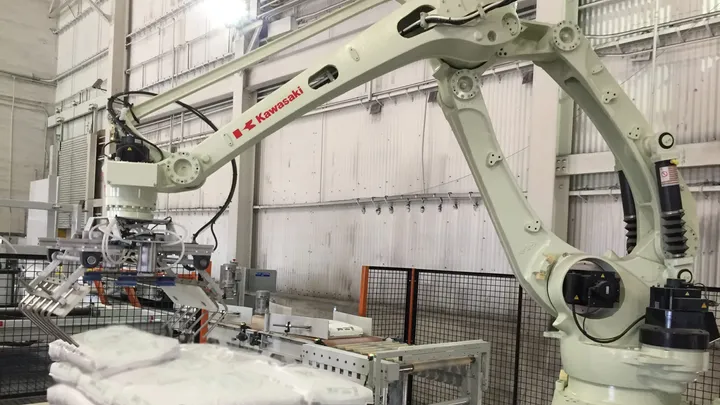
- IndustriesFood & Beverage
- ApplicationsPalletizing
- Robot SeriesCP series
System designed by:
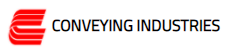
OVERVIEW
In this example, the end user faced a dilemma that many manufacturers experience. As machinery ages, should they put money toward fixing or replacing their line? Downtime caused by frequent breakdowns made the decision easy for the end user. They worked with Denver-based Kawasaki robot integrator Conveying Industries to revamp their entire line with a new palletizing robot and equipment.
Their solution includes upgraded valve baggers, robot and stretch wrapper, which had a tremendous impact. A Kawasaki CP180L palletizing robot was one of the customer’s biggest upgrades. It provided the reliability and consistency they needed to meet their production goals, avoid costly downtime, and streamline overall efficiency.
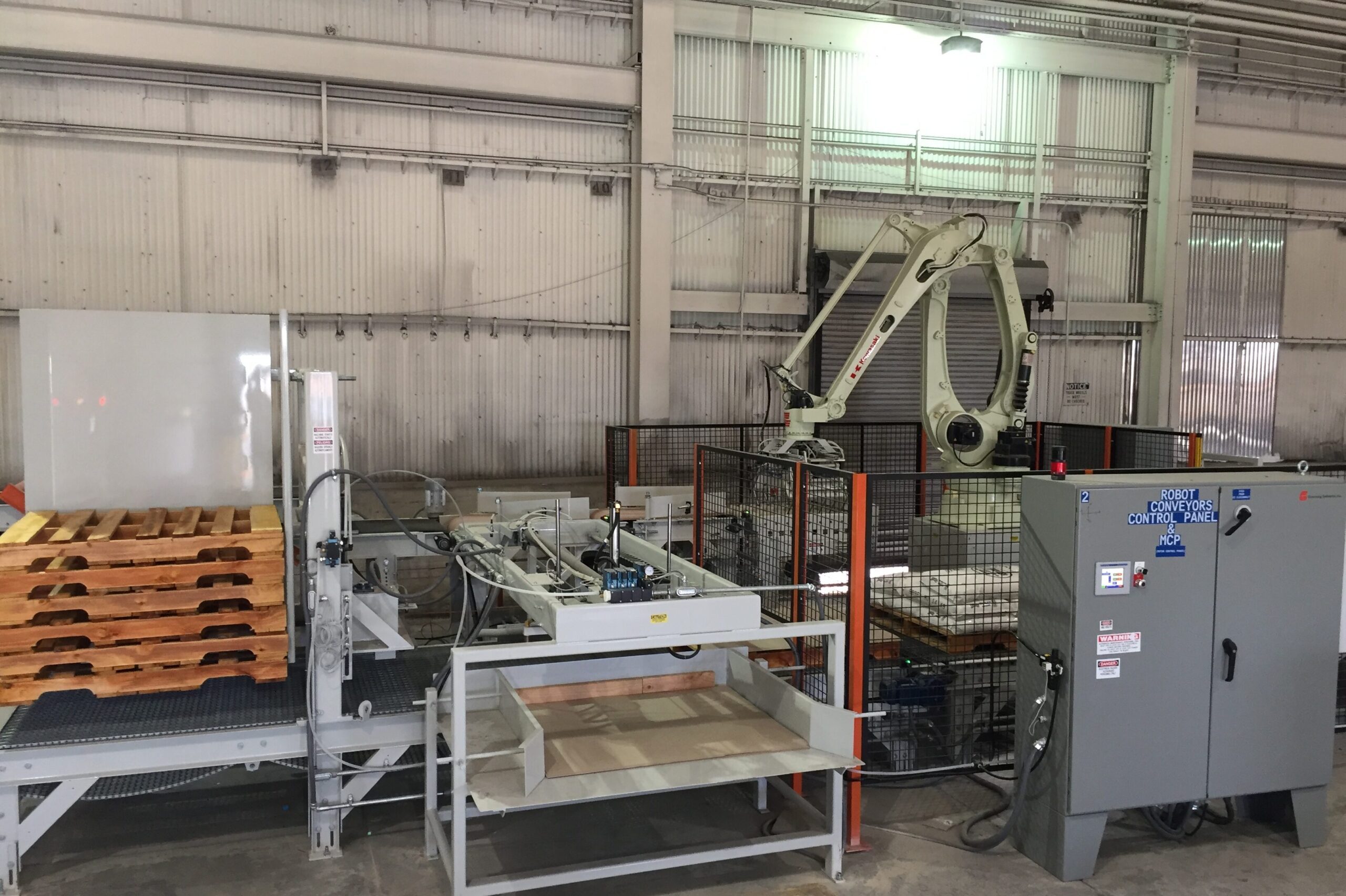
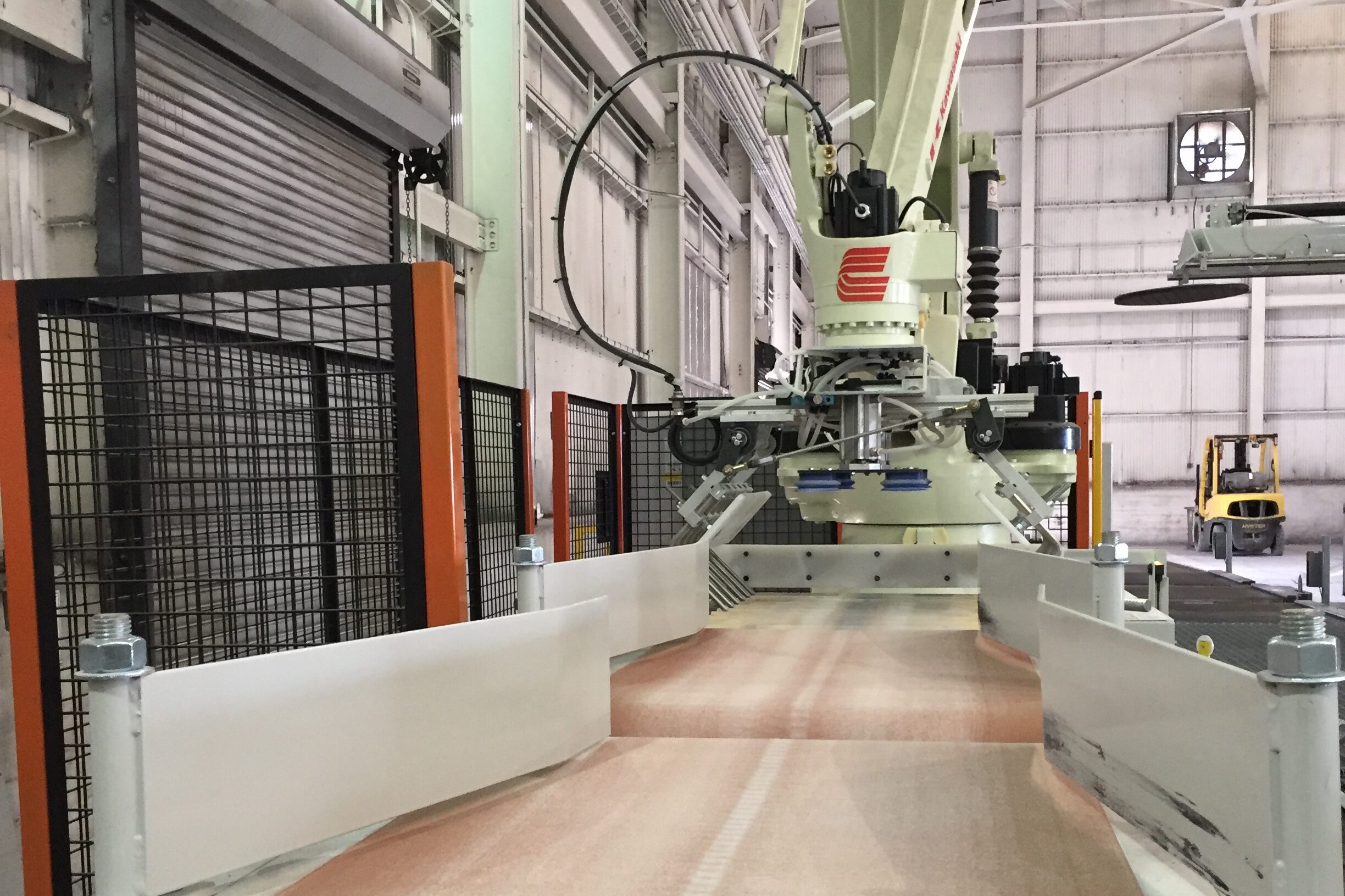
CHALLENGES
To achieve their goals, the customer needed a custom, high performance robotic solution. They produce a temperature-sensitive food product, which melts easily. The system needed to be able to operate 24 hours a day, seven days a week, and in extreme temperatures – oftentimes over 100°F. The new robot needed to be able to palletize a minimum of 20 bags per minute in order to match their current rate of production.
Time sensitivity
The highly time sensitive nature of the food product in this process caused concern as well. Once the product is made, the manufacturer has limited time to bag the product and start distribution before becoming unusable. Any downtime would result in immediate, critical delays in production and bagging, which resulted in loss of sales. “Once you start processing (this product), you can’t afford downtime,” said Bill Priday, Sales Director at Conveying Industries. “It was critical that [the solution] was reliable, running and with no downtime.”
Feeling the heat
The customer’s facility is located in southern California’s desert climate, where temperatures can reach up to 120° in the summer months. The region’s extreme conditions presented challenges for the integrator, who needed to ensure all equipment would be able to operate at such high temperatures.
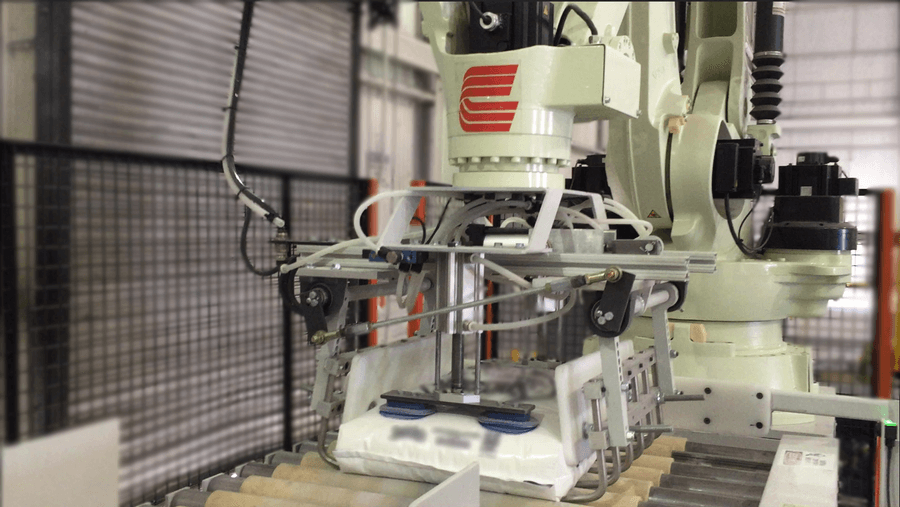
SOLUTION
- Older robot replaced with new, high-speed Kawasaki CP180L palletizing robot
- Manual bagging system replaced with form-fill-seal bagging system
- Air conditioners mounted to robot controllers to control temperature
- Custom HMI allows for simple operation and troubleshooting
Conveying Industries updated the customer’s line with new machinery, including a Kawasaki CP180L palletizing robot and a new form-fill-seal bagging system. It uses durable polyester bags, as opposed to the kraft paper bags they were using.
Once a bag of is filled in the vertical form-fill-seal bagger, the sealed bag goes through a bag flattener conveyor to redistribute the product. Next, it goes through a square roller conveyor to ensure the bag is level. From here, the product travels through a metal detector and a laser jet printer adds tracking codes.
Palletizing begins once the conditioning process is complete. An empty pallet is dispensed from the pallet magazine and delivered to the palletizing station via conveyor. The robot picks bags individually and places them on the pallets in a pre-configured pattern at a rate of 18-20 bags per minute.
Conveying Industries designed a custom end-of-arm tool for the customer, which uses an air-operated clamshell design with fingers that fit between the rolls of the pickup conveyor. Plats on the top of the gripper hold the bag in place as the fingers glide underneath the bag, ensuring the product stays put for reliable and consistent placement.
Once a pallet is completed, a conveyor transports it to a top slip sheet dispenser and an automatic stretch wrapper. The last step is the gravity accumulation conveyor. Then, forklift drivers pick the finished pallets, and take to the warehouse for distribution.
To avoid equipment malfunctions due to the extreme desert heat, Conveying Industries installed air conditioning units on top of the Kawasaki E controller units to prevent overheating.
Smooth Operation
To help the customer with day-to-day operations, Conveying Industries developed a custom touch screen HMI that communicates directly with the robot. The interface provides a bag and layer count to ensure goals are being met, and allows the operator to adjust the number of layers or placing positions per pallet. If any issues arise, the system provides troubleshooting suggestions. It also tracks the alarm history so operators can better understand the robot.
The (Kawasaki) CP180L is a dedicated palletizing robot — reliable, simple to operate and maintain, and downtime is virtually zero. It’s a robot that will run and run and run… and not present problems for the customer.
Bill Priday, Sales Director at Conveying Industries
RESULTS
- Robot palletizes up to 22 bags per minute, 18-20 bags per minute on average
- Number of operators needed for this process decreased by more than 50%
The customer experienced numerous benefits after implementing the new equipment. “The CP180L is a dedicated palletizing robot – reliable, simple to operate and maintain, and downtime is virtually zero.” Priday said. “It’s a robot that will run and run and run… and not present any problems for the customer.”
With their previous robot, the end user could not achieve their production goals due to breakdowns. Now, the Kawasaki CP180L is able to consistently palletize 20 bags per minute for hours a day with fewer operators. At full speed, the rate increases by 4 bags per minute from the previous robot’s capabilities. In addition, the new system only requires two operators as opposed to five – a benefit reflected in the customer’s bottom line.
The Kawasaki CP180L robots offered a simple design with high reliability, ruggedness and speed. When combined with Conveying Industries’ custom HMI interface and tooling, the customer saw a positive impact on their efficiency and bottom line.