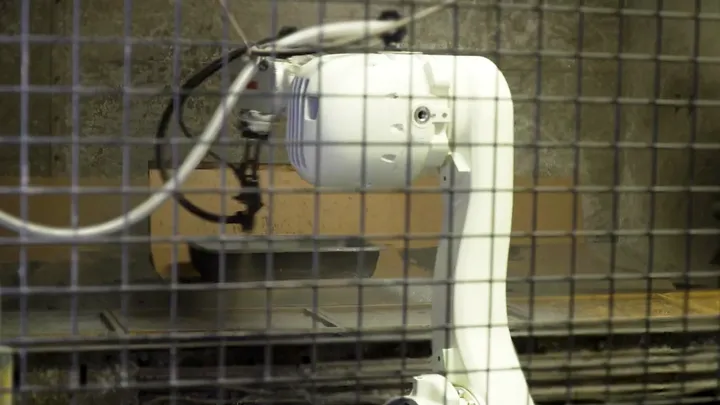
- ApplicationsPainting
- Robot SeriesRS series
System designed by:
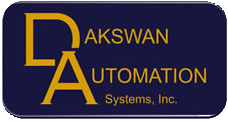
OVERVIEW
In the eyes of some manufacturers, installing an industrial robot can seem intimidating. Misconceptions of having to rebuild everything from the ground up and having to adopt a completely new process can make automation seem like a bigger endeavor than it truly is. In reality, there are many ways to embrace automation without starting from scratch. The available resources make programming and maintaining a robot possible for all knowledge levels, including first-timers.
Baton, LLC, a Louisville-based manufacturer of AirStone faux stone veneers and siding, learned this firsthand when they installed their first robot with the help of Dakswan Automation. Once installed, the Kawasaki RS080N robotic spraying application helped Baton cut down production time and significantly reduce waste, with minimal changes made to their existing production line and tooling.
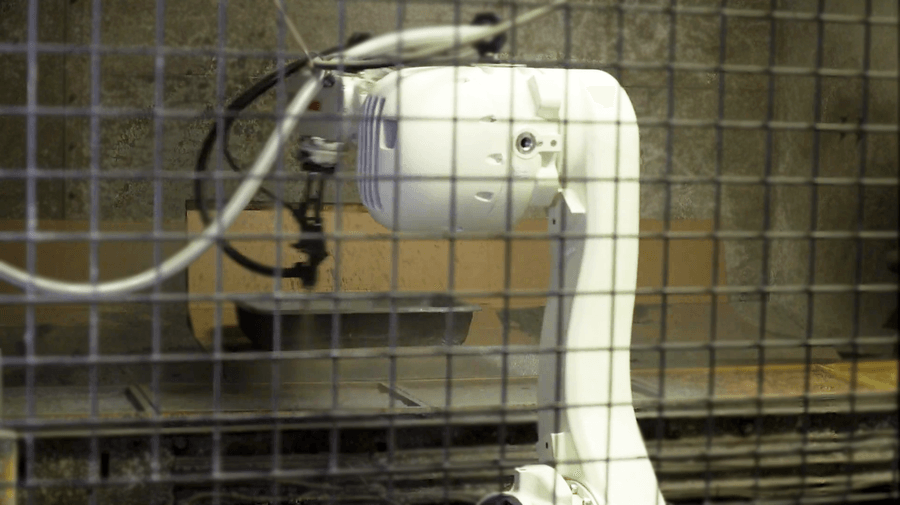
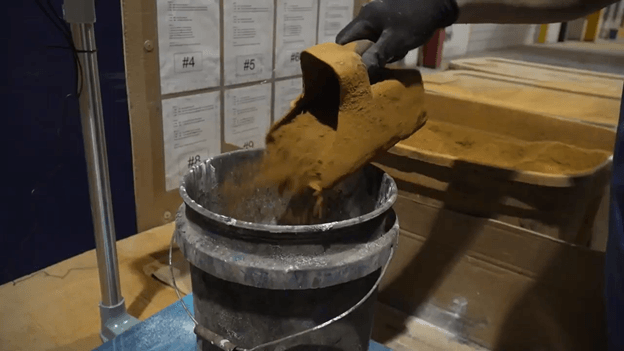
CHALLENGES
- Inconsistent manual process yields large amounts of waste
- Unfriendly work environment for employees
- Must automate production line using existing equipment
Product inconsistencies
In order to produce AirStone prior to automation, four painters sprayed liquid cement onto molds as they approached on a conveyor. Each painter used a different amount of material, resulting in inconsistent products and over use of materials. Robotic spraying allowed Baton to improve product quality.
“Human un-friendly” environment
While spraying, employees had to wear uncomfortable respirator masks to remain safe and minimize exposure to liquid cement particles while on the job. For manufacturers whose products are constructed in harsh environments, it can be difficult to retain employees, and that task is even more challenging during an industry-wide labor shortage. This lack of consistency can lead to low production, and is a primary reason why Baton decided to implement a robotic spraying process.
Minimal process changes only
This was Baton’s first robot, so the manufacturer was hesitant. They didn’t want this new equipment to disrupt a process they’d developed over the past five years. Dakswan needed to design a customized robotic spraying solution that aligned with their customer’s manual process.
“It took years to develop our spray system that applies color into our product, and the manual gun we use works well for a number of reasons. It would have been hard to replace”, Tom Scanlan, Owner and President of Baton, LLC said.
SOLUTION
- One Kawasaki large payload, general purpose RS080N robot installed
- Built-in PLC option, K-Logic, used to cut costs and streamline operations
- Minimal changes made to customer’s existing production line, tooling and processes
The robot is positioned in the same place as the workers were previously. When the parts arrive in front of the robot on a conveyor, the robot is programmed to paint at the same speed as the human workers before it. The robot’s ability to work all day without breaks saves Baton an average of 2.5 hours of downtime each week.
“Being able to work continuously by eliminating the attendance issues, as well the consistency of the painting, has been great,” Scanlan said. “That station is no longer an area that creates downtime.”
Choosing a robot from Kawasaki’s line of high performance general purpose robots, as opposed to paint robots, was a purposeful choice by the integrator, who picked this specific model due to its long reach capabilities. The RS080N robot’s extended reach (2,100 mm) made it perfect for Baton’s application, which required the robot to spray a large area from one fixed location.
Kawasaki’s R series robots are effective in workspaces of any size. In addition to their extended reach, the large rotation range of the R series’ axes translates to a larger usable work area with minimal dead space. The slim arm design of the R series makes them a great option for tight spaces like Baton’s paint booth.
User-Friendly PLC
Kawasaki’s option for a built-in PLC, called K-Logic, was another major selling point for Dakswan Automation. The integrator wanted a cost-effective and user-friendly solution, easy for a first-time robot user to navigate. A built-in PLC checked both boxes. K-Logic internalizes all communication between the production line and the robot, making it easy for the end user to operate. K-Logic also kept costs down by eliminating the need for an external PLC, which minimizes the amount of external cabling needed.
Same Process, Modernized
Because the RS080N robot isn’t designed for performing paint/spray applications, Dakswan designed a custom end-of-arm tool to hold the exact same paint system Baton was using. This allowed them to retrofit their current paint gun, utilize spare parts they had acquired for years, and keep their end product consistent.
Since we hadn’t had any experience with robots, there was apprehension (around) the robot going down, how often that could happen… or if (the robot) was going to cause headaches with our manufacturing process, but it’s been the opposite. It works every day – we don’t really have to do anything.
Tom Scanlan, Owner & President, Baton, LLC
RESULTS
- Downtime reduced by 2.5 hours / week
- Workers removed from harsh environment & redeployed to safer roles
- Product consistency & quality increased significantly
- Amount of over-spray reduced
- Customer programs and maintains robot using knowledge from Kawasaki training course
Although Baton is technically a first-time robot user, the knowledge their maintenance staff acquired from the Operations & Programming training course they took at Kawasaki’s training center has enabled them to keep their robot up and running smoothly entirely on their own. Additionally, they are able to reprogram the robot to test out different spraying patterns for new products.
“Robots are not as difficult to program or maintain as they seem,” Vyas said. “I see a lot of people afraid of robots… People who are nervous to touch or maintain them… But it’s not that difficult.”
After installing their RS080N robot to perform a “human un-friendly” task, the benefits of automation showed themselves in multiple ways. Baton saw a boost in production, so they redeployed employees who formerly sprayed the AirStone molds to different areas of the company without exposure to harsh chemicals.
From an operational standpoint, Scanlan uses the words “worry-free” to describe using the new Kawasaki robot – despite his initial concerns as a first-time robot user.
A Worthy Investment
For Baton, automation didn’t mean overhauling a proven process or experiencing stress from complex programming or unexpected shutdowns. The robot has improved their manufacturing process while creating a safer work environment for their employees. Dakswan Automation designed a cost-effective solution that utilized the machinery and tooling Baton had spent years adopting. This paved the way for a seamless transition and a robotic spraying solution they can maintain entirely on their own.
“It was a very easy process to convert from manual to robotic. Without a doubt, it was worth the investment,” Scanlan said. “It’s been such an absolute positive to our plant… the reduction of material costs, the reduction of downtime — all of it. Using the robot is just kind of worry-free.”