
山口製作所、川崎重工が提供する「外観検査ロボットシステム」を導入
1950年に創業した山口製作所は、2025年で75周年を迎える精密部品メーカーである。祖父の代に軍需工場での勤務経験を活かし、戦後に独立して設立された。研究開発に注力し、日本初となるマイクロフォーマーの導入などを行い、戦後の技術革新とともに成長を遂げてきた。1989年には中国・大連に進出し、日系企業として4番目の進出企業となった。現在は主に樹脂事業に注力しており、自動車業界を中心に需要が広がっている。品質方針としては「後工程に流さない」を掲げており、製造現場での品質作り込みを徹底している。
こうした取り組みの中で、2024年に川崎重工の「外観検査ロボットシステム」を導入。初めてアーム型ロボットの採用となった本システム導入の背景や経緯、効果について伺った。
新製品立ち上げで求められた検査の高度化と人材の確保
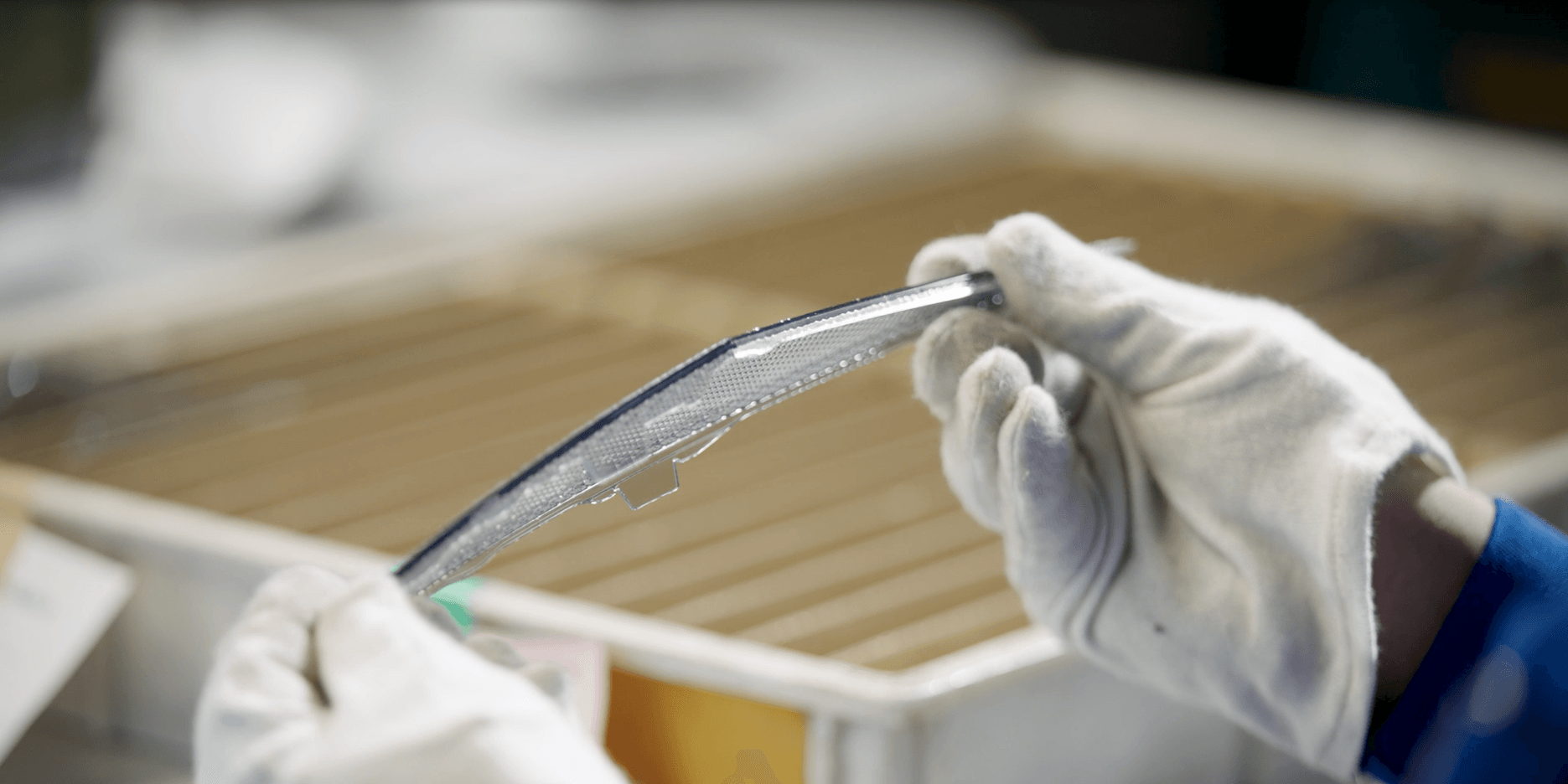
外観検査の自動化を検討したのは、新たに量産開始したインナーレンズ製品がきっかけだった。この製品は車両外観のデザイン部に使用される部品であり、従来のような車内に隠れる部品とは異なり、微細な異物やキズ、変形なども許されない高い外観品質が求められた。
山口製作所では、従来は目視による検査を行っていたが、新製品の複雑な湾曲形状に加え、必要な検出能力を持つ検査員を安定して確保することが困難であると判断。「検査員は手作業で部品を取り、表面・裏面・側面・文字などの確認を行っていたが、検査内容が複雑で、1個あたり15秒以上を要する工程でした。熟練者の確保と教育にも多くの時間が必要であり、慢性的な人材不足の中で安定した検査体制を構築するのが難しかった」と技術2部の渡辺氏は話す。
従来の体制と課題

導入前は、製造部門と技術部門が製造責任を持ち、品証部門が外観検査を担っていた。しかし、不具合情報のフィードバックが翌日以降になるなど、即時対応ができない体制だった。人の目に頼る検査では、判断のばらつきやサイクルタイムの限界も課題となっていた。
特に今回の新製品は、サイクルタイム内に1回で4個を検査する必要があり、全ての検査項目を人手で実施すると時間内に収まらない状況だった。「どこまでを自動検査でカバーし、どこを製造技術で抑えるか、その線引きと検査基準の調整が課題でした」と渡辺氏は当時を振り返る。
「外観検査ロボットシステム」導入の決め手
まず、ロボットシステムを導入した大きな理由の一つは、「ハンドリングによる高い汎用性」でした。今後、製品の品種が変更になった場合でも、設定の変更だけで外観検査を継続できるため、多品種への対応が可能である点に期待し、「ロボットを使う」ことを決断しました。
外観検査ロボットシステムについては、Webでの情報収集をきっかけに商社へ相談したところ、川崎重工のシステムを紹介された。検査カメラについては複数社の比較検討を行ったが、ロボットについては、ラインスキャンカメラとの相性を考慮し、「高速パルス出力機能」を備えた川崎重工製のロボットのみが要件を満たすと判断し、比較は行わなかった。
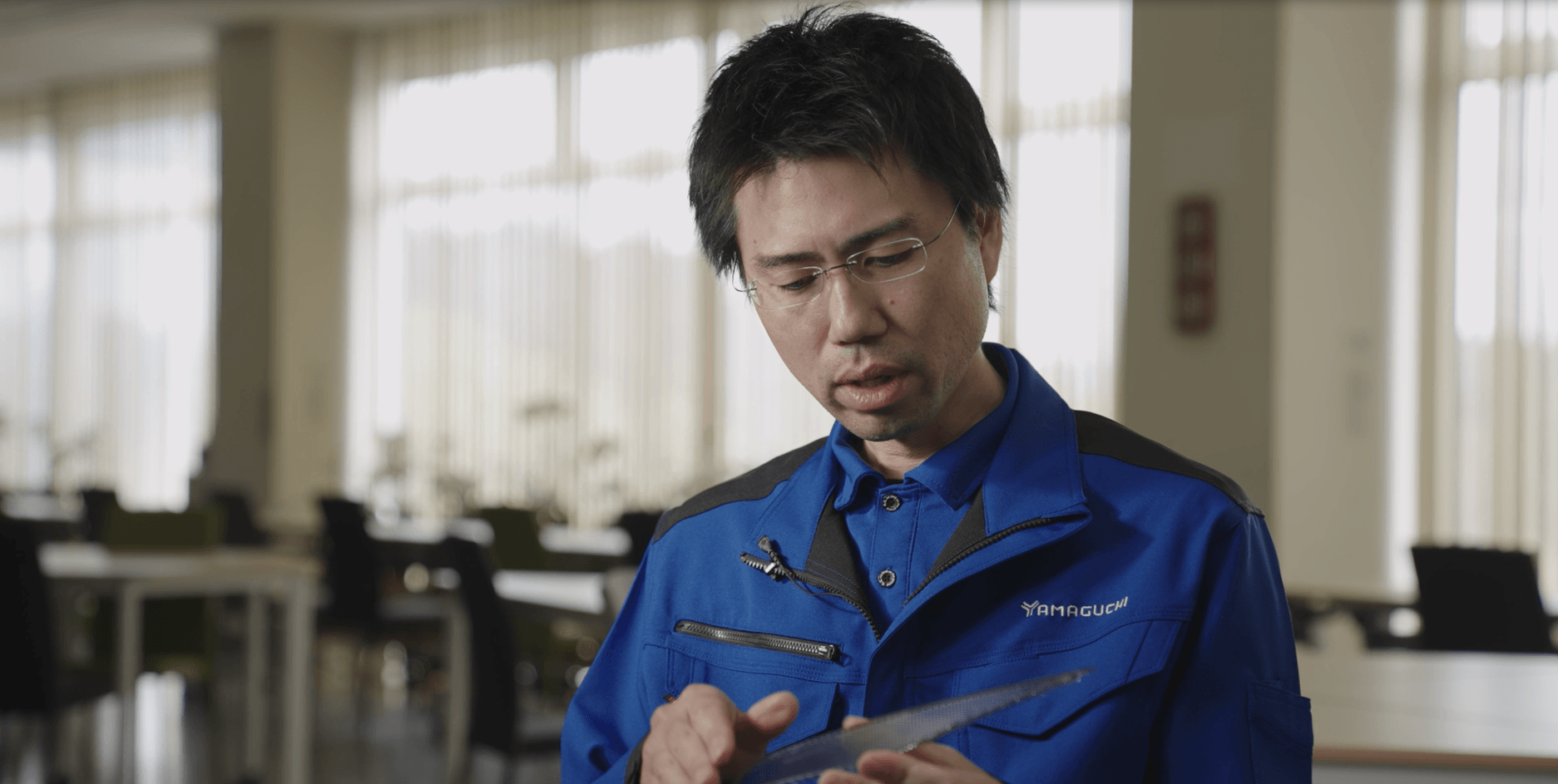
「製品選定にあたっては、客先図面に基づく検査基準を満たしながら、成形サイクル内で検査を完了できることを重視しました。高速で複雑な動作を可能にする同機能が評価され、導入の決め手となりました」とロボットシステム導入に携わった品質保証2係の野中氏は話す。
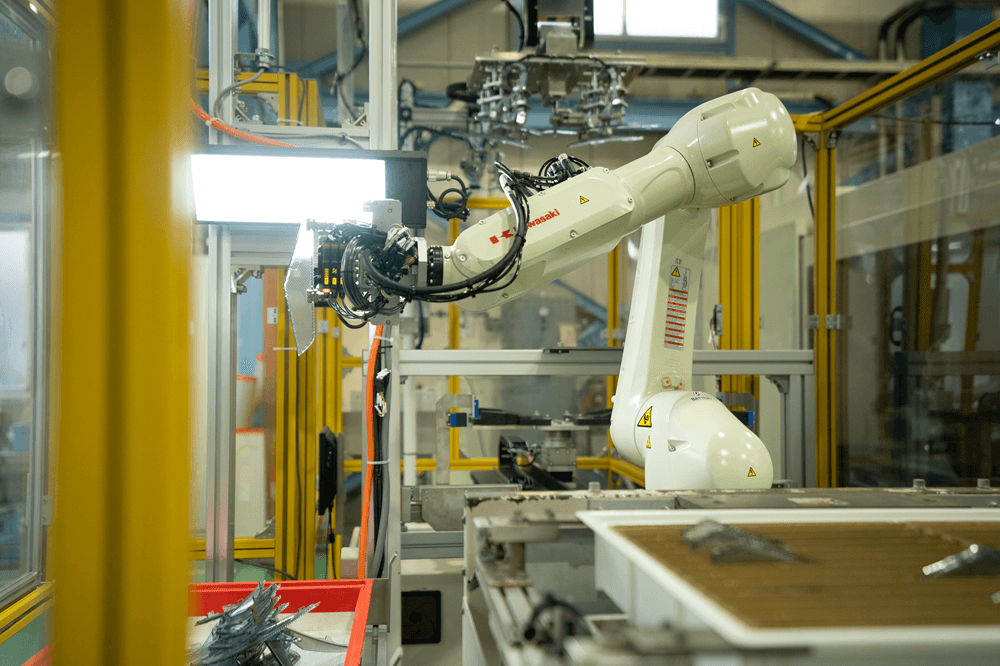
導入時の対応と体制
導入にあたって、山口製作所内にロボットの専門家はいなかったが、※FA担当者が中心となり、SIerとの連携を取りながら対応。まだ扱いに慣れていないこともあり、現在も現場ではむやみに触らず、問題があればFA担当が対応する体制を取っている。
検査基準の設定においては、川崎重工のラボや現場で調整を行い、サイクルタイム内に処理するために、全項目を網羅するのではなく、重要項目に絞った設定を行った。
※FA:ファクトリーオートメーション
実際の効果と手ごたえ
導入後6ヶ月が経過し、現在は2名体制で運用。他部署での展開は未実施だが、NC加工やブランクの自動供給などでの展開も検討中。KPIとしては検出精度や不具合数の記録を行っている。
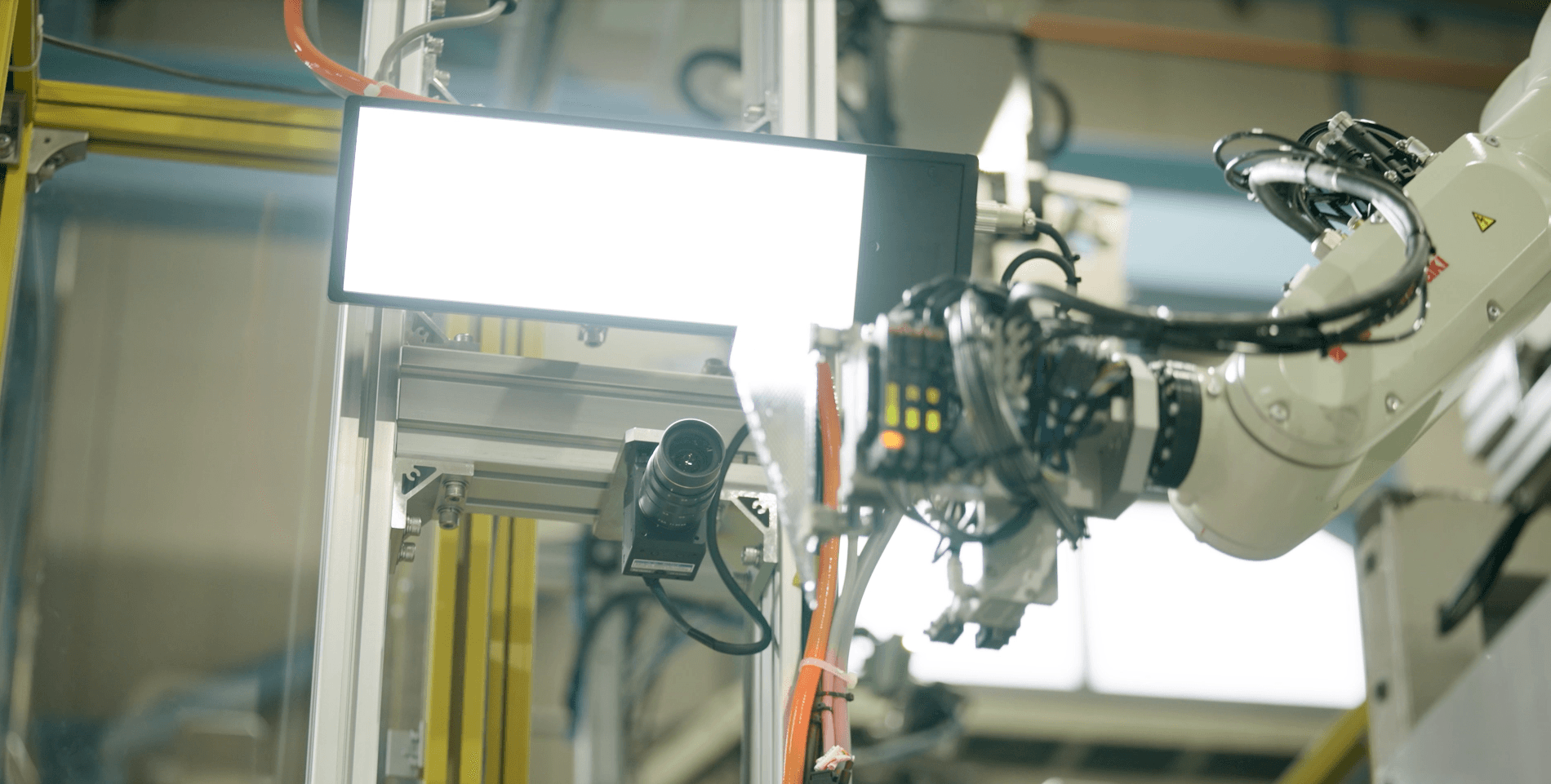
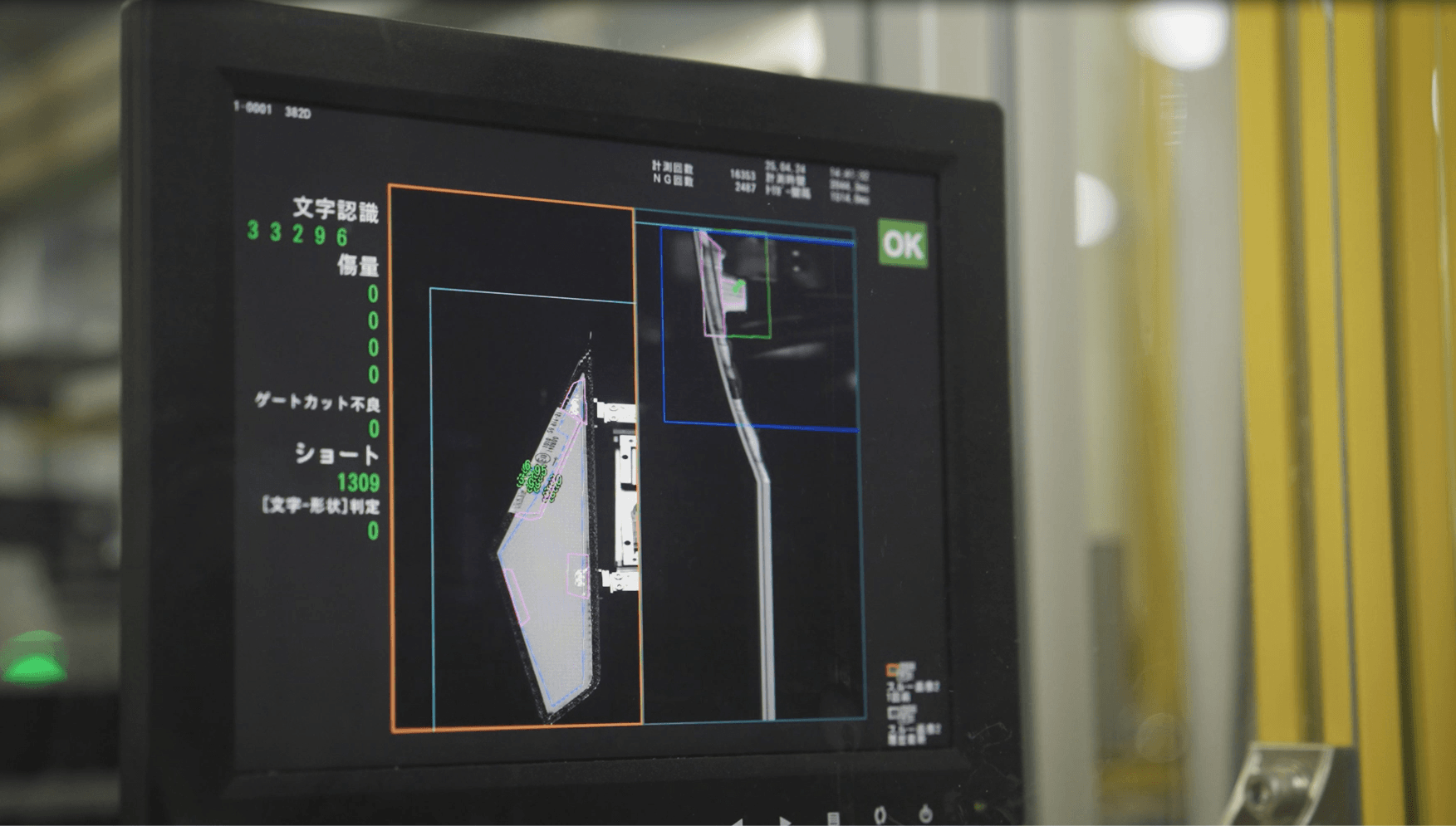
導入によって、検査員3名分の人件費(年間約1300万円)を削減。従来1日~2日後だった不具合のフィードバックが即時対応可能となり、成形直後の不良検出でライン停止・改善が可能になったことで、生産ロスの低減にもつながった。検査工数としては、月間297時間の削減効果があったという。
「高速パルス出力機能」により、湾曲した製品の外観検査を高速で行える点は、導入後もっとも評価している機能である。また、静電気で付着したチリや微小なごみも検出できる精度があり、予想外の成果だった。
今後の展望と要望
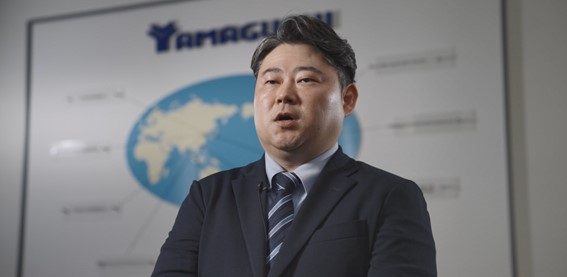
「今後は、海外拠点も含めて自動検査の導入を推進していきたい」と取締役副社長の山口氏は話す。特に、多品種小ロットの製品にも1台で対応できるシステムを構築し、最終的には多品種対応の交互検査が可能な構成にしたいと考えている。
川崎重工への要望としては、今後さらに部品の形状が複雑になる中で、より柔軟な動きが可能なロボットや、簡易設置が可能な汎用システムの開発を期待している。また、現場の作業者が川崎重工のロボットスクールに参加できるよう、教育体制も整備していく方針だという。
ロボットが担う「不具合検出」という重要な役割
山口製作所では、本システムを「検査工程における不具合検出」という重要な役割を担う存在と位置づけている。もし他社に紹介するなら、「川崎重工製ロボットのスペック、信頼性、サービスの質の高さ」が推奨ポイントになるという。
今後も、品質要求の厳しい製品への対応や、安定した人材確保が難しい中で、同社にとってロボットの外観検査は重要な選択肢となるだろう。