正確で器用なアームを駆使して、与えられた仕事を着実かつ確実にこなす産業用ロボットは、社会を支える縁の下の力持ちだ。最近では医療や食品、農業など幅広い現場で活躍しているロボットも少なくないが、やはりメインはモノづくりの現場。主要な用途といえば、何はさておき「組立」、「マテリアル ハンドリング(搬送、移送)」、そして「溶接」である。産業用ロボットが普及するきっかけを作ったのは、溶接作業だと言われている。高熱や有害な紫外線、金属の粉塵といったリスクが常に付きまとう過酷な環境に加え、熟練を要する作業であることから人材も不足する。厳しい労働環境下であっても、常に同じ動作を精密な軌跡で繰り返すことが得意なロボットにとって、なるほど溶接作業はもってこいの仕事だった。今や製造業の現場の大ベテランとなった溶接ロボットだが、とあるアメリカ・ネブラスカ州最大規模の製造所では今から30年前にまだ“新人”だった溶接ロボットの導入に思い切って踏み切ったという。「彼ら」の導入には、ロボット伝道師との異名を持つ謎の男“Agent K”の影響があったと聞く。その事実を探るべく、今回XYZ取材班は“時空ジャーナリスト”として、タイムマシーンでネブラスカの州都を目指すこととなった。
人手不足に悩む溶接業界
アメリカ合衆国のほぼ真ん中、ネブラスカ州リンカーン。今から47年前、川崎重工は我が国の二輪車・自動車メーカーとしてこの地に最初の現地工場を開設した。メイド・イン・アメリカのモビリティを作るパイオニアとして、いち早くモーターサイクルの生産をスタートしたのである。1981年にはKawasaki Motors Manufacturing Corporation(KMM)として独立し、四輪バギーや水上バイク、スノーモービル、多用途四輪車、鉄道車両などの生産も担っている。
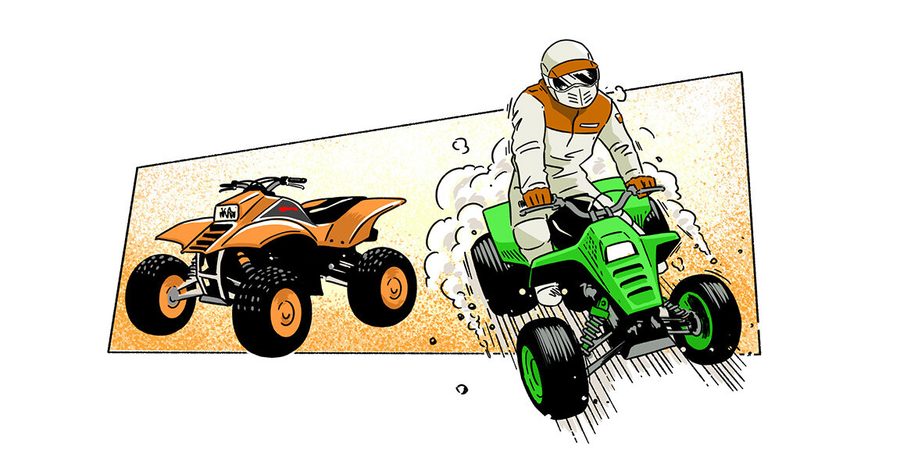
とりわけKMMリンカーン工場が大量に生産する四輪車は、悪路をものともせずに走行するタフなモデルばかり。堅牢で高品質、かつ多彩なモデルを滞りなく製造するためには、様々な部品を溶接出来る柔軟性に富んだ確かな“腕”が必要だった。
チーフエンジニア:溶接業界の労働力不足は今に始まったことじゃないが、それにしても状況は深刻だね。
エンジニア:いつも人材が足りないから生産目標にもなかなか追いつきません。結局溶接士一人一人の残業がかさんでなおさら費用がかかる、っていう悪循環ですよ。
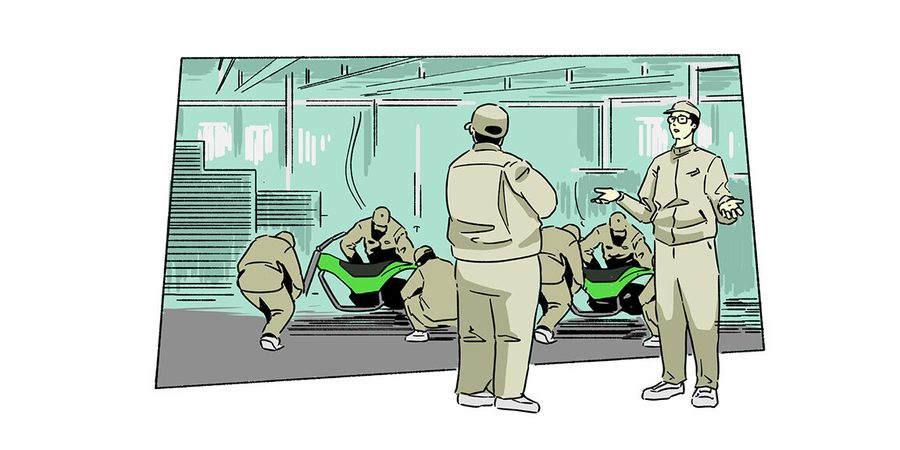
チーフエンジニア:それに、マーケットの「目」だって昔とは違う。彼らはより良い物を求めている。「ある程度」の品質であれば、ちょっと前までなら許されていたかもしれないけど、今じゃあ受け入れられないからね。
エンジニア:一定の技術を持つ溶接士を育成するために、我々独自のトレーニングコースを設けてきましたが、これにも時間とコストが膨大にかかります。とはいえ、当然クオリティに妥協は出来ないし。だからといって、腕利きの溶接士を今すぐ大量に雇用するなんてこと、ほとんど不可能ですからねえ……。
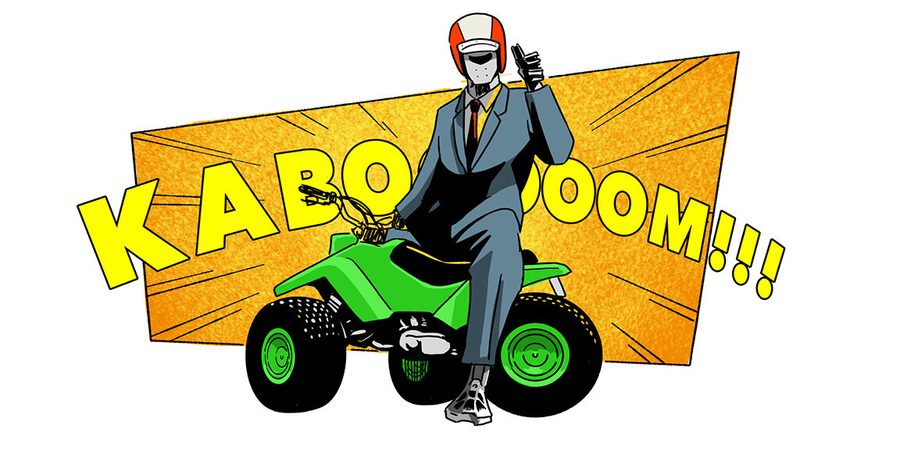
Agent K:そんなときこそ、ロボットにお任せを!
チーフエンジニア:ロ、ロボットだって? そりゃあもちろん一つの手かもしれないが……いやしかしだね、我々の仕事は複雑なんだ。異なるサイズや重量、形状のパイプ同士を溶接しなくちゃいかん。やっぱり人間の手が必要なんじゃないか?
Agent K:ふむふむ。なるほど、ここはこうこうして、あそこはこうすれば、っと(KKMが生産している様々なサイズと形状のATV[※ All Terrain Vehicle 全地形対応車]と多用途四輪車をチェックしながら、手元に書き付けていたメモを2人に差し出す)。うん、これなら8割の作業をロボットに委ねることが出来るでしょう!
チーフエンジニア:なんだって? 手作業がたったの2割で済むっていうのかい。そ、そりゃ願ってもないことだが、一体どうやったらいいんだ?
部品のサイズや形状ごとにワークセルを設置
Agent K:まずは扱う部品の種類に合わせて、4種類のセルを準備します。そこで組み立てたそれぞれのモジュールを、最終的に車体全体のフレームを溶接する大型セルに送り込む。こうした5セル構造のシステムを構築してはいかがですか?
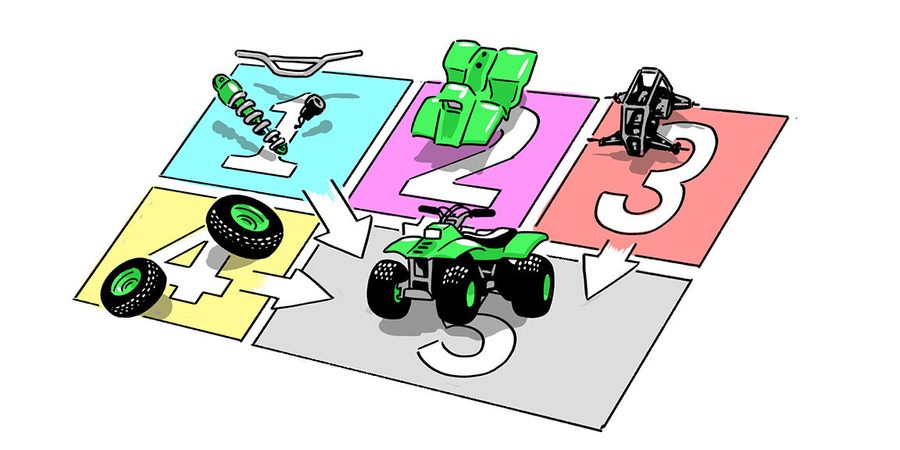
チーフエンジニア:そうか、例えばサスペンションアームのような小さな部品。シートやフロントグリルガードといった中型部品。それとサブフレームなどの長尺部品。3つのセルでそれぞれの作業を完結すればいいわけだ。でも、キャビンそのものをすっぽり囲うロールケージみたいな大きくて複雑な形状の部品はどうする?
Agent K:複雑な絵画をしっかり描き込むためには、しっかりとした画架が必要です。複雑な溶接部品にも、最適なイーゼルを用意してあげましょう!
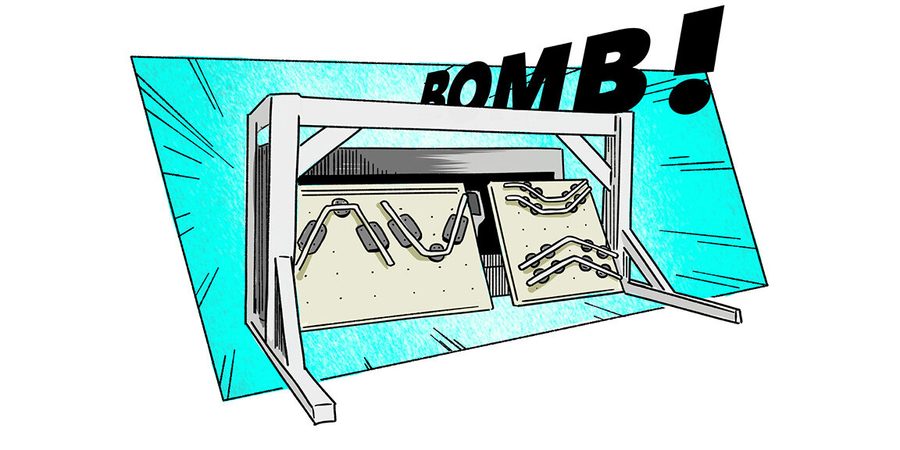
Agent K:こちらは名付けて「ニーリング イーゼル」。6フィート(約1.82m)の大型パイプのロボット溶接を可能にする特製の治具です。
チーフエンジニア:大型フレームの溶接には、かなり無理な姿勢での作業を強いられてきたからなあ。ロボットに任せられるならありがたいよ。それに、複雑な形状だから溶接トーチが届きづらい部分もあったりして、溶接ビード[*アーク溶接時に生まれる波状の塊。部材同士を溶接で繋いだ部分に見られる]に一貫性が保ちづらいのも難点だった。ロールケージはお客様の目に直接触れる部分だから、見栄え品質にも妥協したくないし……。
Agent K:もちろん研磨工程も自動化OKです!
エンジニア:それぞれの部品を繋ぎ合わせる最後のセルは、クリーンルームになっているようですね。
Agent K:ここでは、しっかりとした強度と美しい見た目をキープするために、パルスMIG溶接法を使って車両の一体化を行います。最小限のスパッタ[*溶接時に金属粒やかすが飛び散り周辺部材に付着するもの。こびりついたスパッタは工具で取り除かなくてはいけない]で一定品質の製品を完成させることが出来ますよ。
チーフエンジニア:(ロボットの溶接作業を眺めながら)ううむ……私も長く溶接の現場に携わってきたが、アンタの言うとおり「彼ら」の腕は確かだな。ほら、見てみろよ、あの綺麗なビードを。
エンジニア:我々の扱っている製品のほとんどは、パイプ同士を溶接して組み合わせる複雑な形をしていて、手溶接では完全な一貫性をキープすることが難しかったですからね。これならシャーシ自体の歪みも大幅に減って、製品の品質が全体的にアップすること間違いなし!いや、これはありがたい。貴方のおかげですよ……ってあれ?居ない?
チーフエンジニア:もうどこかへ行っちゃったのか。ずいぶんせわしない人だねえ。
ネブラスカ州最大の製造所へ
それから30年。ときは現代へ。相変わらず忙しそうに工場内を歩き回っているチーフエンジニアの目の前へ、謎の男、Agent Kが姿を見せる。
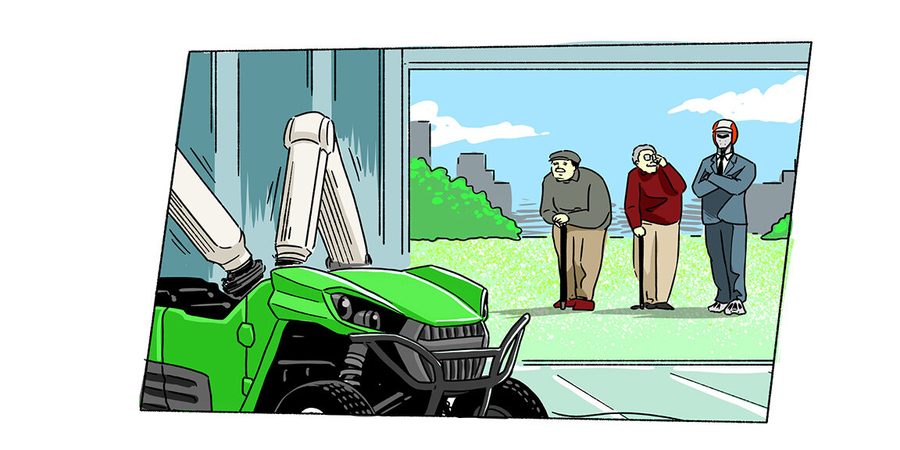
チーフエンジニア:あれ?(メガネをかけてまじまじ眺めながら)……アンタか! 驚かさないでくれよ、随分久しぶりじゃないか。それにしても、いつも突然現れるんだなあ。いやしかし、何十年経ってもちっとも老け込まんね、私と違って。
Agent K:自動化した現場のその後が気になりまして。生産はスムーズに進んでいますか?
チーフエンジニア:ああ、今やアーク溶接作業のあるすべての現場のうち、80%はロボットに任せているよ!
エンジニア:これはこれは! どうもご無沙汰しておりました。おかげさまでね、手作業が必要な工程は貴方の言うとおり僅か2割で済んでいます。ロボットの作業をダブルチェックしたり、ロボットにはどうしても細かすぎる部分なんかは人間が行っていますが。
チーフエンジニア:今は71台のロボットを使っているがね、来年には84台まで増やす計画なんだ。カワサキ製のロボットは信頼性も高いから、現場からももっと増やしてくれって声が続々届いているよ。
エンジニア:30年以上にわたる使用実績がありますから。信用度も抜群ですよ。
Agent K:それは何より!それじゃあまた、いつか!
チーフエンジニア:おっと、もう居なくなっちゃったよ。やっぱり相変わらずせわしない人、だな。
操業開始からおよそ50年、KMMのリンカーン工場がネブラスカ州最大規模の製造所と言われるまでになった影には、カワサキ製ロボットの存在があった。ATVの「KFX」「BRUTE FORCE」、多用途四輪車の「MULE」に「Teryx」。2021年の今、KMMの工場では年間数千台もの四輪車フレームを送り出している。
[付記]
このストーリーは、川崎重工における事例に基づいたフィクションです。舞台となった実際の現場は、1980年代のKawasaki Motors Manufacturing Corporation(KMM)のアメリカ・ネブラスカ州リンカーン工場。当時のKMMリンカーン工場では、四輪車製造にあたり「パーツの品質に一貫性を持たせ、シャーシの歪みを解消」すること、「多種多様な部品を効率よく溶接」すること、そして「手動溶接への依存を最小限に抑える」ことが課題となっていました。それらを解決するために、川崎重工製の小型・中型汎用ロボット「Fシリーズ(現在は生産終了)」、「Rシリーズ」を導入。部品の形状・サイズ別にモジュールを組み立てる4つのセル、そこから供給される部品を最終的に一体化する1つのセルを設置しました。その後、手動溶接が必要なプロセスは全体の20%のみに縮小。KMMのチーフエンジニア、スコット・ゴードン氏は「川崎重工のロボットは、市場に出回っているものの中では群を抜いて信頼性が高い」と語っています。
今回のケースで登場した川崎重工製品については、以下をご参照ください。
小・中型汎用ロボット「Rシリーズ」
可搬重量3〜80kgに対応する13種類のバリエーションをラインナップした垂直多関節ロボット。組立・ハンドリング・シーリングなど、幅広い用途に適応可能。高速、大トルク、広範な動作領域を誇り、ハーネスの内蔵化やスリムなアーム形状などにより、コンパクトに設置出来るのも特徴。