ロボットユーザー:KHファシリテック株式会社様
システムインテグレーター:川重ファシリテック株式会社様 溶接と切削工程の自動化
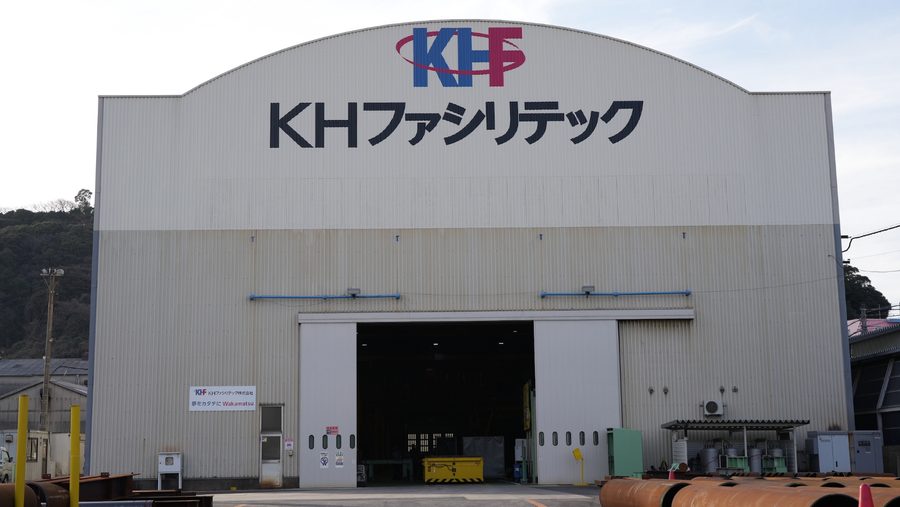
KHファシリテック株式会社は、3次元造形の鉄骨を中心に製作している“特殊鉄骨造り”のプロフェッショナルです。新国立競技場のスタンドを円形に覆う鉄骨トラスの大屋根、鋼管が絡み合いながら天空を目指す東京スカイツリーの塔体、折り紙のように幾何学的なシルエットでターミナルを包むJR高輪ゲートウェイ駅の屋根、恐竜の骨を思わせる東京・渋谷区ミヤシタパークのアーチ型天蓋など、同社が手掛ける意匠性の高い構造部材は、造形にこだわる最新の建造物を数多く支えています。そんな大型ワークを主に扱うKHファシリテックが自動化に成功した背景には、ティーチレスで効率的にロボット動作データの生成が可能となる「KCONG」ソフトウェアの存在がありました。
導入背景/課題:
加工対象物は地下トンネルに使用する大型鋼製構造部材
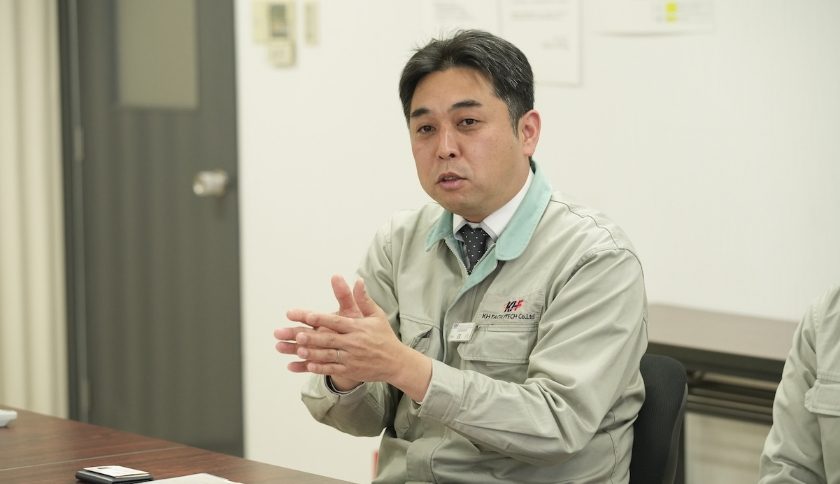
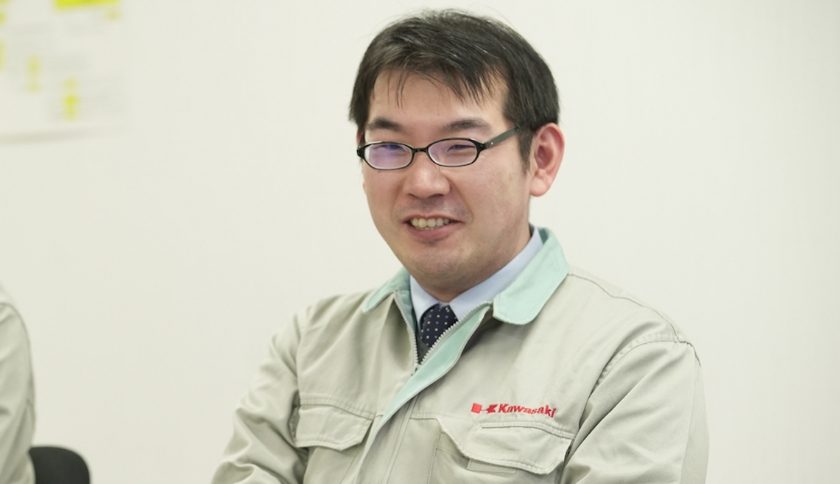
KHファシリテックは、3次元構造の特殊鉄鋼や鋼管を扱うプロフェッショナル。「我々はあまり同じものは作らないので、基本的に自動化は困難でした。しかし、“鋼製セグメント”の大量製造を行うにあたりロボット導入を決断しました。」とKHファシリテックの森川 淳一 部長(生産総括部)はロボット導入のきっかけをそう説明します。一方、お客様のニーズに応じたオリジナル仕様のロボットシステム作りを得意とする川重ファシリテックの寺岡 直哉 リーダー(設備技術本部 ロボット設備グループ)は、「近年は省力化・自動化が困難な領域への参入を積極的に図っています。」と多様な活用分野への取組みを話します。
スタジアム・空港などの屋根鉄骨や、アーチ構造の橋りょう、箱桁などに使われる3次元構造を描く特殊鋼構造物を得意とするKHファシリテック。立体的で複雑な形状の鋼構造物を形成するには職人による手作業が不可欠で、製造工程の自動化はこれまで困難とされてきました。そんなKHファシリテックがロボットの本格導入を決断したのは約5年前。地下トンネルに使われる「鋼製セグメント」の受注がきっかけでした。一般的な都市トンネルの工法は、円筒状の掘削機で前面の土を掘り進めていくシールド工法が主流となっています。その際、掘った部分が崩れてこないように壁面へ組み付けるのが「セグメント」と呼ばれる構造材です。近年は施工性や経済性の観点からコンクリート製セグメントが使われることが多いものの、引っ張り強度、曲げ靱性、耐衝撃性、および施工性の観点で、より大開口で複雑な構造部(Uターン路やインターチェンジをはじめとした箇所)には鋼製セグメント*1が必要とされています。
KHファシリテックが自動化したのは、この鋼製セグメントの製造工程です。「量産品を扱わない我々にとって、ロボット導入はなかなか難しい課題でした。かつて鋼管の切断に一度採用したことはあったのですが、継続して使うことはありませんでした」(森川部長)ところで、直径10mを優に超える円状のセグメントは、数分割したピースによって構成されます。数人分に切り分けたバウムクーヘンの一片を想像すると分かりやすいかもしれません。そのピースを、重量に換算すると数千トンにも及ぶ単位で納品するとなれば、大量生産は必至です。「実は16年前にも一度鋼製セグメントの製造を受注したことがあるのですが、そのときは何しろ手探りで、全て人手で行ったんです」(森川部長) 今回改めてKHファシリテックが鋼製セグメントの大量生産をスタートするにあたり、過去の経験を活かして自動化を決断。効率化、品質安定化、そして従業員の負担軽減を図るべくロボットを導入することとなったのです。
【参考文献】*1:日本シールドセグメント技術協会 http://jssa3.org/index.html
導入効果/ソリューション:
オリジナルトーチの採用で自由度の高い溶接を実現
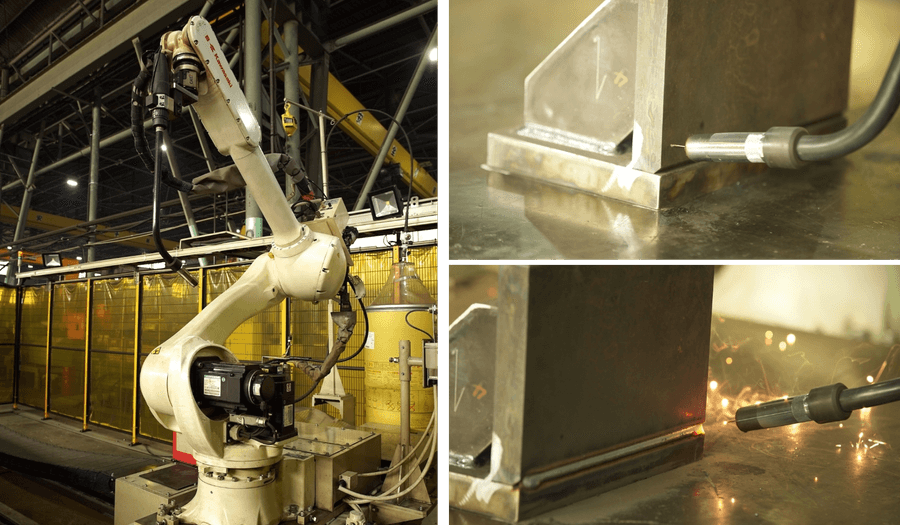
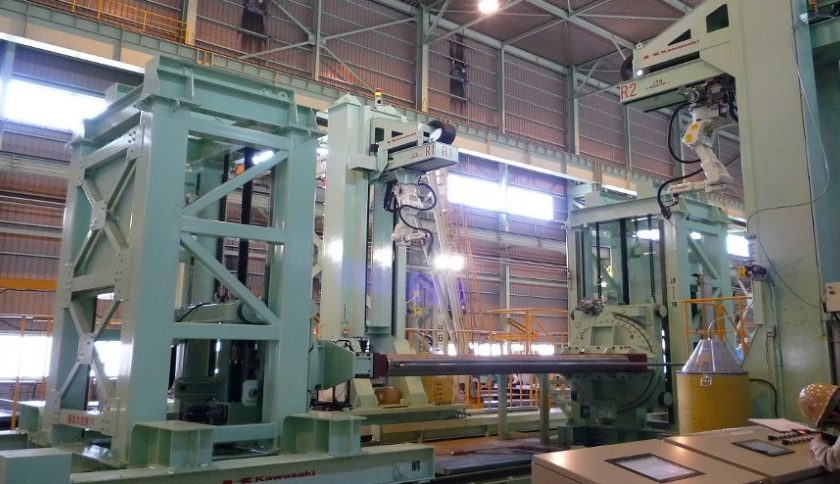
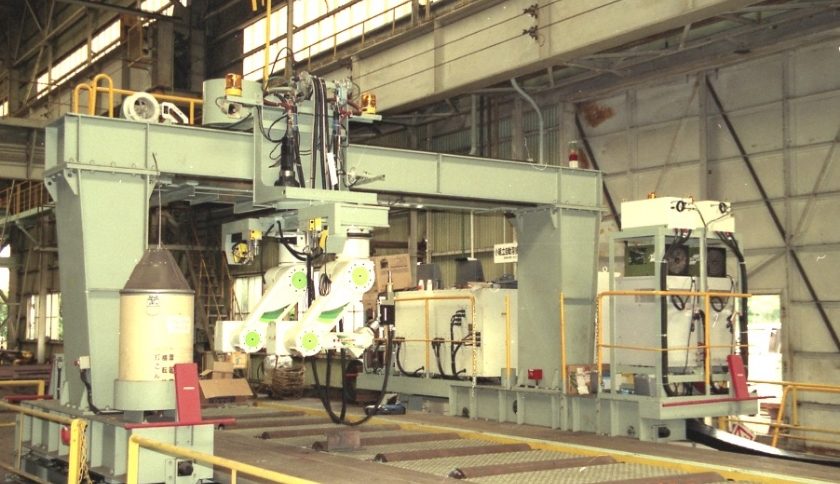
システムアップを担当した川重ファシリテックは、複数台のロボットを組み合わせた溶接自動化システムや可搬型ロボットといったユニークなソリューションを種々開発し、船舶や航空機など特殊な大型構造物を効率的に製造するために走行装置や可動治具、可搬装置といった周辺機器を組み合わせた独創的な設備をインテグレートする専門家集団です。大型ワークの生産効率向上を図るロボットシステムを作るという性質上、ロボットの最適な動作データを生成する為には、オフラインでのティーチレスシステムが必要となります。 「そこで、川崎重工で開発された3D CADデータからロボットの動作データをPC上で生成し、シミュレーションを可能とするロボット自動教示ソフトウェア「KCONG」を適用したシステムを数多く構築しています。」(寺岡リーダー)
今回の対象となるワークも、長さ約5m、高さ1m以上に及ぶ大きさで、重量も重たいもので4〜5t、軽くても2tという大型鋼製構造材です。システムの自動化にあたっては、やはり「KCONG」が有効活用されました。「まず最初に溶接工程へ、続いて溶接のビードを切削するロボットシステムを導入しました。ロボットであれば条件を一定(同じスピード、角度、順序)にして溶接を行うことができるため品質が安定し、かつ休まず連続的に作業させることが可能です。元々2人がかりで行っていた溶接工程を1人のオペレーターが担当できるので省人化にも繋がりました」(森川部長)
開先(溶接を行う母材間に設ける溝)に合わせて、繰り返し溶接を自動で行うラインには、走行装置と組み合わせた垂直多関節ロボット「RA010L」2台をワーク台の左右に設置。ロングリーチタイプのロボットにオリジナルのロングトーチを取り付けることで、奥行きのある箇所まで溶接出来る設計となっています。2台のロボットはワイヤの先端部カット→ノズルクリーナー→スパッタ付着防止液塗布→ワイヤを母材に接触させて溶接位置をセンシング→ワーク両側から同時に多層盛溶接、という一連の工程をすべて自動で行います。
「ロボット化によりビード厚が一定となったため、そのビードを削る切削工程も自動化できる。川重ファシリテックからそう提案をいただいたんです」(森川部長) 切削は溶接よりも人の手がかかる作業であり、切削工程の自動化は長年の課題でした。開発を担当した川重ファシリテックの服部 孝司 主査(設備技術本部 技術グループ)は、「前工程の溶接の自動化でワークの状態(=ビードの盛り)が一定となったおかげで、後工程となる切削にもロボットを適用できる可能性が生まれました」と説明します。
タクトタイムを最大25%短縮した切削加工ロボット
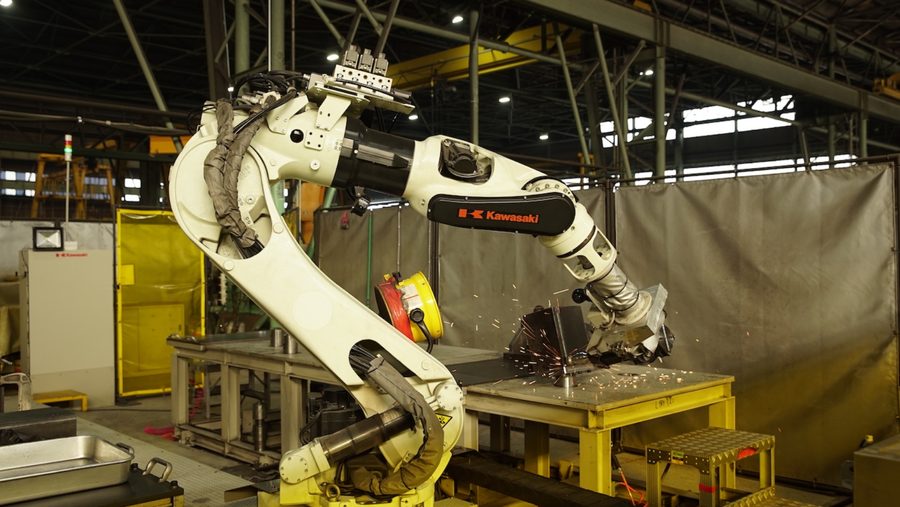
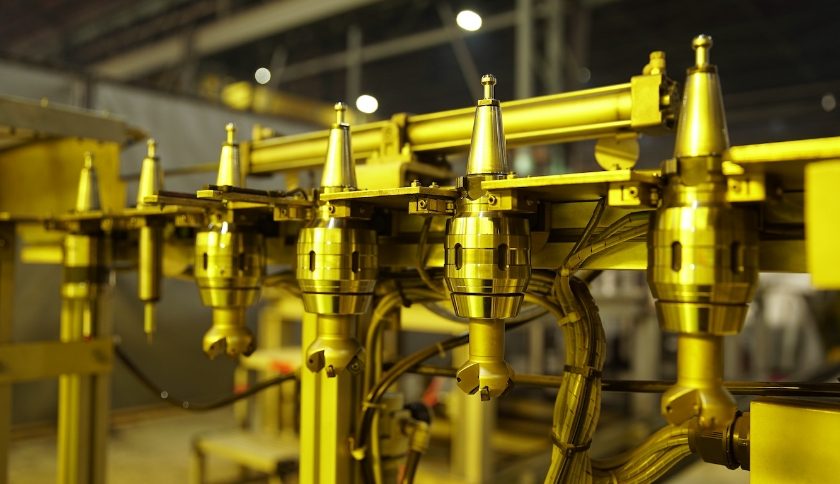
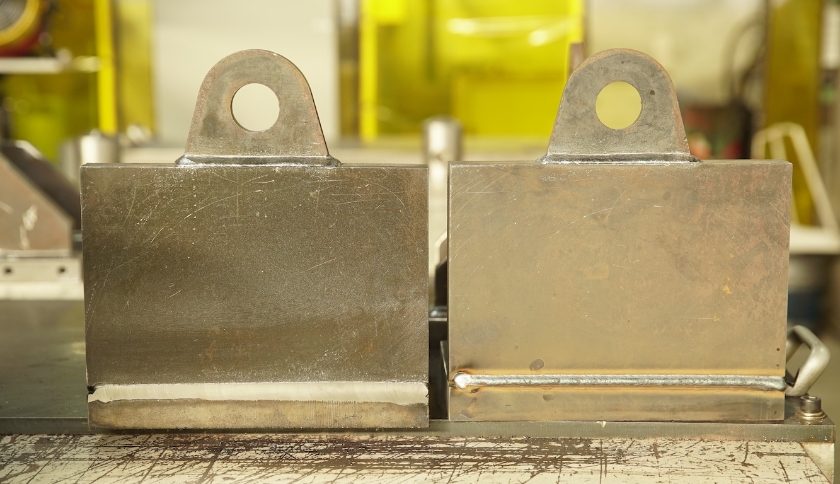
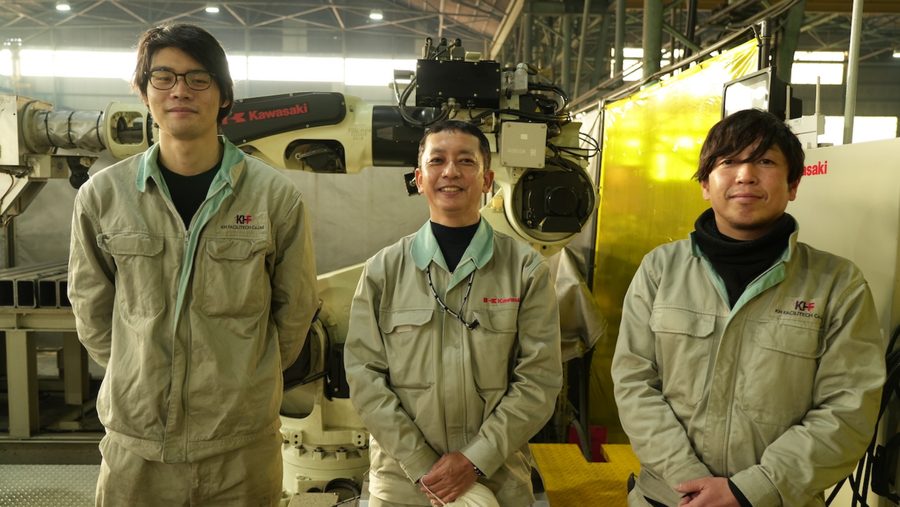
鋼製セグメントの1ピースを仕上げるのに、これまでは1人で1日半かかった切削加工。自動化により作業時間は最大25%短縮できました。ツールチェンジャーを適用し、様々なエンドミルを使い分けることも可能としています。
溶接部のビード切削工程に採用したのは可搬重量200kgの垂直多関節ロボット「BX200L」。ハンド部にエンドミル(切削工具)とスピンドルモータ(回転駆動装置)を装着しており、「切削時の振動、そして反力を吸収するために力のあるロボットを使用しています。さらに、振動を低減する機能も盛り込みました。」(服部主査)走行装置に据え付けられたロボットはツールチェンジャー機構により位置センシング用のタッチプローブ、複数のエンドミルを自動的に交換できる設計となっています。これにより、切削前のセンシングから加工終了まで、人の手を介することなく全自動で切削を行うことが可能になりました。「一回の切削量とパス回数、エンドミルの回転数、電流値、移動速度など、すべての条件の最適解を見つけ出すのが最も苦労した点です。実際のワークを使い、さじ加減を調整していきました」(服部主査)
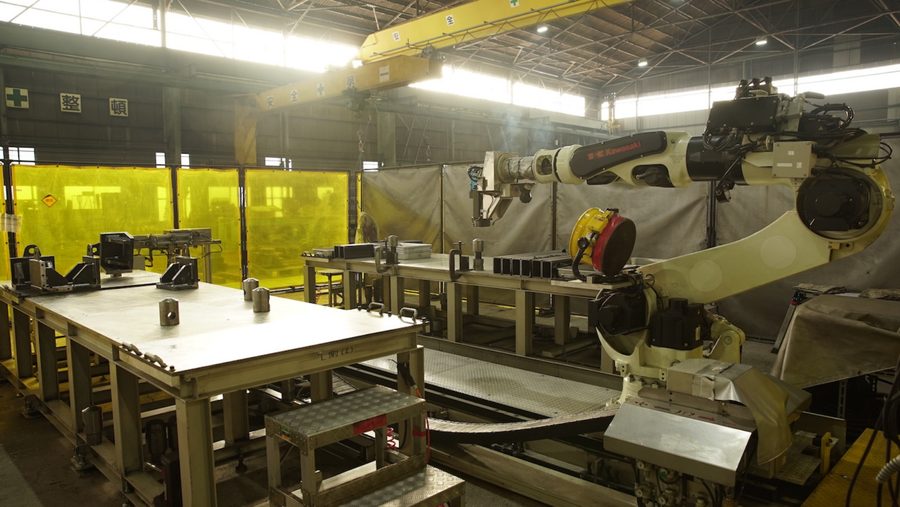
ロボットの両脇にワーク台を設置した自動切削加工ライン。自動切削は次のような順序で行われます。まず①ロボットが走行装置上をツールチェンジャー位置まで移動、②ツール保管庫の防じんカバーが自動オープン、③センシング用のタッチプローブをアーム先端に装着、④タッチプローブをワークに接触させて適正な位置をセンシング、⑤ロボットがツールチェンジャー位置に戻り先端をエンドミルに交換、⑥ワークの切削加工を実施する、というのが一連の流れです。ロボットの両脇に一つずつワーク台を設置することで、二つのワークを一度にセットできるのも特徴です。天井クレーンを使う大型ワークの移動には時間がかかるため、ワーク台が一つだと切削完了からワーク排出までの間、ロボットは次の切削作業に入ることができません。両脇にワークを設置しておけば、切削が完了した一方のワークを動かさずとも、ロボットは二つ目のワークの切削作業に取り掛かることが出来るのです。また、二つのワークを連続で自動切削加工することが出来るため、オペレーターの対応時間も最小限に抑えることが可能です。切削工程を自動化したことで、タクトタイムは従来比で最大25%短縮。人の居ない夜間にも自動で作業することが可能なので、製造効率は格段に向上しました。「無人で作業が出来るので、従業員の負荷の軽減、および安全性の向上にも寄与しています」(森川部長)
今後の展望や計画:
専用機にはないロボットならではの“将来性”
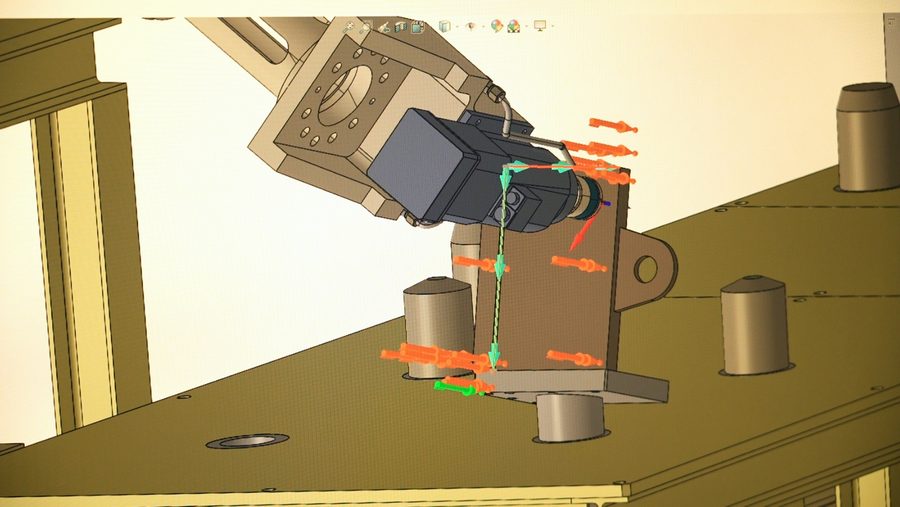
川重ファシリテックは、各種走行装置や昇降/旋回装置をロボットに付加し、更にポジショナー(ワークを最適な角度に位置決めできる可動式治具)まで組み合わせた非常に高度なシステムも数多く手掛けています。それらの走行装置やポジショナーの駆動モータをロボットの外部軸として、「ロボットの能力」を最大限活かすシステム作りを得意としています。大型部材の切削加工には、門型マシニングセンタのような専用機を入れる方法もありますが、設置にあたっては多大な設備投資および広大な設置スペースが必要となります。ロボットによる自動化システムであれば比較的コンパクトなスペースに設置が可能で、プログラムや周辺機器を変更すれば別のワークにも適用できる“汎用性”もロボットの強みです。川重ファシリテックでは、その強みを利用し、これまでに無い独創的な切削自動化システムを開発しました。「弊社へ見学にいらっしゃるお客様の多くは、切削ロボットシステムに一番興味を持たれますね。切削や研削・研磨といった工程は、様々な業種、業態で自動化に悩んでいる部分なんだと思います」(森川部長)
また、「今回は溶接、切削の両工程ともにロボット自動教示ソフトウェアの『KCONG』を活用して、設備の設計から教示までを行っています。第一段階の溶接自動化の際には、苦労してこのソフトウェアをカスタマイズしました。そこでノウハウを蓄積出来たおかげで、切削ロボットは設計から本稼働までスムーズに進めることができました」(服部主査) また、「KCONG」のカスタマイズはソフトウェア開発の技術者集団、川重テクノロジー(現ベニックソリューション)が参画しています。これだけ大きなワークの切削工程をロボットで自動化できたのは、川崎重工のロボット開発技術、川重テクノロジーのソフトウェア技術、川重ファシリテックのエンジニアリング力という三者のテクノロジーが結びついたからこそだったのです。
ー 導入企業情報
会社名
KHファシリテック株式会社
代表者
取締役社長 橋岡康浩
操業開始
2020年4月
事業内容
建築鉄骨、橋りょうなどの鋼構造物の製作、据付
事業所
本社=福岡県北九州市若松区北湊町9-27
ウェブサイト
https://www.khf.co.jp
ー システムインテグレーター企業情報
会社名
川重ファシリテック株式会社
代表者
取締役社長 土田義夫
設立
1977年1月
事業内容
各種生産設備、生産ラインの設計・製作、大型可動構造物、貯槽・配管設備のメンテナンス、プラント設備の各種検査業務
事業所
本社=兵庫県加古郡播磨町新8番 川崎重工業株式会社 播磨工場内
ウェブサイト
https://www.khi.co.jp/corp/kis/
ー 導入ロボット
【溶 接】
モデル名 RA010L=1925mmのロングリーチで大きなワークにも対応しやすい6軸垂直多関節ロボット
特長 コンパクト&スリムながら高剛性なアーム、クラストップレベルの動作範囲、高い防塵・防水性能
可搬重量 10kg
軸数 6軸
繰り返し精度 ±0.05mm
最大リーチ 1925mm
【切 削】
モデル名 BX200L=高速の動作スピードと高密度配置を実現した6軸垂直多関節ロボット
特長 コンパクト&軽量アームや高出力/高回転モータの採用、最新の防振制御による速やかな動作スピード。配線・配管類を内蔵する構造により設置面積もコンパクトに。
可搬重量 200kg
軸数 6軸
繰り返し精度 ±0.06mm
最大リーチ 2597mm