ロボットユーザー:株式会社田中鉄工所 精密部品ハンドリング自動化
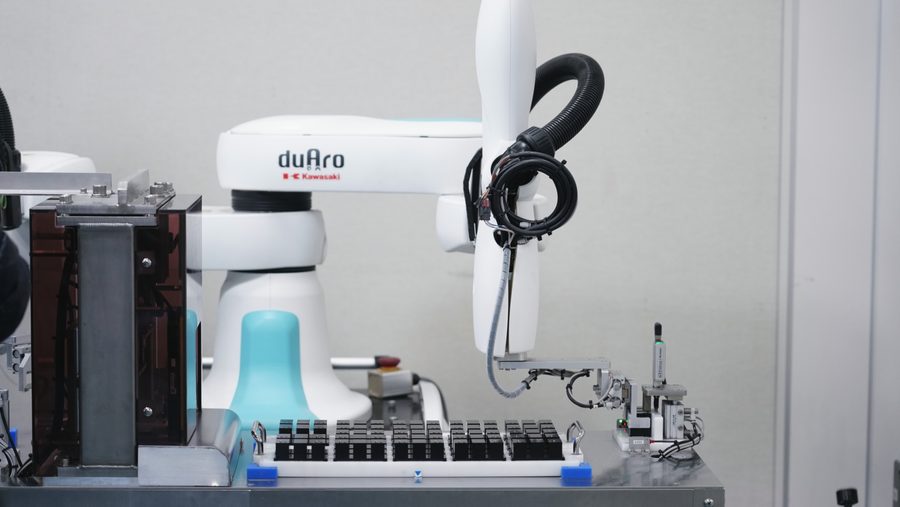
産業用ロボットや医療機器、航空機、原子力プラント向けの精密加工部品を製造する株式会社田中鉄工所(本社・兵庫県神戸市、田中祥靖社長)は、専用の工作機械を使用する切削加工の現場で24時間無人運転の生産システムを構築しています。一方で、人の手による作業が主体となる仕上げ工程ではなかなか自動化が実現できずにいました。作業者がメインとなって働く空間に産業用ロボットを導入するにはどうすれば良いのか−−その答えとなったのが川崎重工の人共存型双腕スカラロボット「duAro(デュアロ)」でした。
導入背景/課題:
安全策なしで人と共存できる 協働ロボットが拓いた自動化の扉
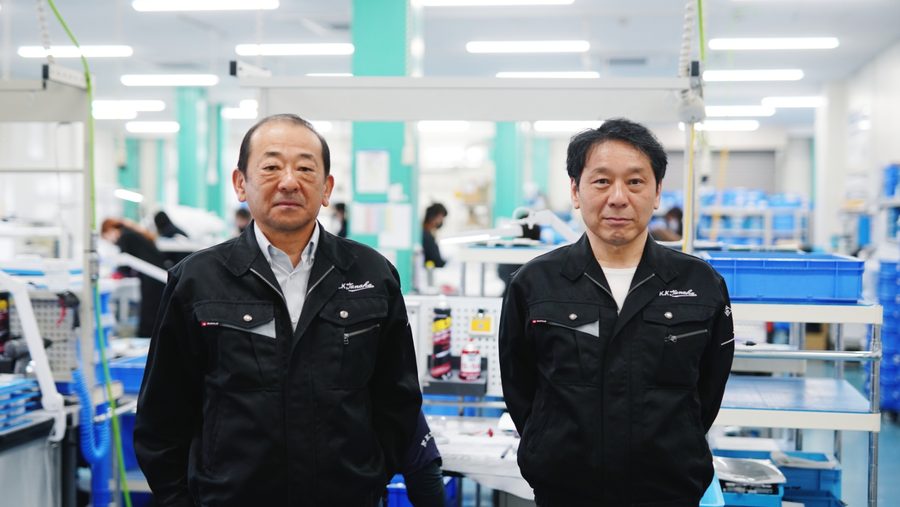
株式会社田中鉄工所は、精密金属加工のプロフェッショナル。1938年に戦闘機「紫電改」の主脚づくりから事業をスタートして以来、航空機や医療機器、原子力機器などに使われる精密加工部品の製作を80年以上にわたり行ってきました。国内初の自動血球計数装置を実用化した東亞医用電子株式会社(現シスメックス株式会社)とも黎明期から関係を構築。今では世界No.1シェアを誇るまでになったシスメックスの血球計数検査機器にも田中鉄工所製の部品が使われています。また、1977年以降はカワサキロボットのサプライヤーとして、産業用ロボットの心臓部といえるアームなどの機械部品を納めてきました。
同社の強みは、17台のマシニングセンタと熟練の職人技を融合したフレキシブルな「変種変量生産」。増産が相次ぐ半導体や自動車製造向けの産業用ロボット、医療機器向けの部品づくりを事業の中心とするため、「近年は120%の稼働状況で回している感覚で、とにかく人手不足で困っています。だからロボットが人の代わりにできる作業をずっと探していました」(田中祥靖社長)。2階建ての工場1階には専用機械がフロア全体にずらりと並び、精密加工部品の切削加工が24時間無人運転で行われています。その一方で、仕上げ工程を行う2階は人がメイン。何人もの技術者が作業台を前に黙々と最終加工を行う現場を見るにつけ、田中社長は「ここには自動化できる要素が何かある」と考えていました。
しかし、人が中心の作業場へ産業用ロボットを導入するには、安全柵の設置など、大規模な改修が必要になります。「町工場にとって何が一番問題になるかというと、やはりスペースなんです。だから産業用ロボットを使えるのはほとんどが自動車や半導体業界のような大規模な製造ラインだけで、まさか我々の工場に導入できるとは思っていませんでした」(田中社長)。そう語る田中社長が出会ったのが、2015年に川崎重工が発表した人共存型双腕スカラロボット「duAro」。「柵から出して人と共存できるロボットと聞いて、これならうちでも使えるのではないかと思いました。duAroだったから入れられたんです」
導入効果/ソリューション:
単純な連続作業だからこそ起こりうるヒューマンエラーを防ぐ
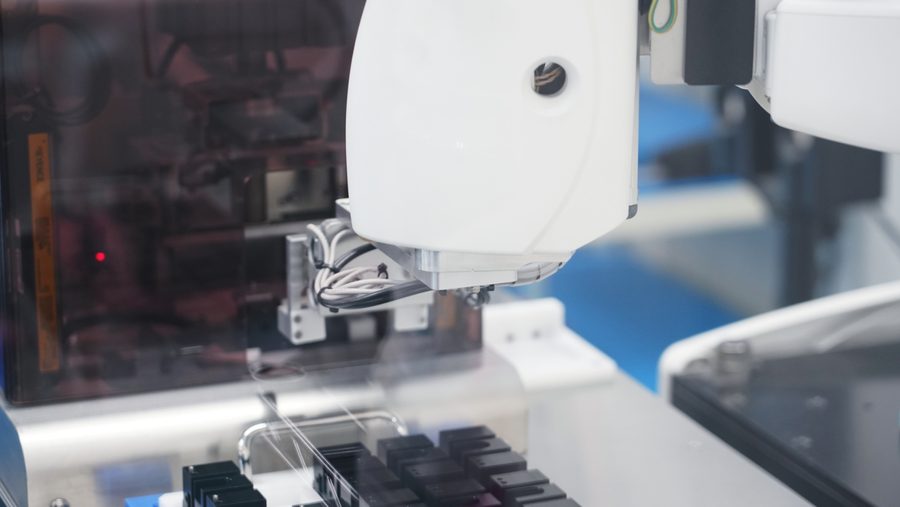
田中鉄工所でduAroが担当しているのは、シスメックスの製品に使用する重要部品の組立作業。具体的には、人間の手の甲ほどの長さのアルミブロックに、ステンレス製の平行ピンを2本圧入するのが仕事です。
「近年、(当該部品の)生産数がどんどん増えてきたんです。月2000個だった生産数は、3年後には5000個という増産ペースへ。5000個となると、ピンの圧入する箇所は1万か所にも上るわけです」(田中社長) 上下の向きがあるピンを正しい方向、正しい圧、正しい深さで挿入するのは単純なようでいて熟練の技術が必要であり、かつ単調な連続作業であることからヒューマンエラーが起こりやすい工程でもありました。「スピードを重視するなら人が入れるほうが速いんです。でも今回我々が求めたのは、速さではなく、正確で確実な作業でした」
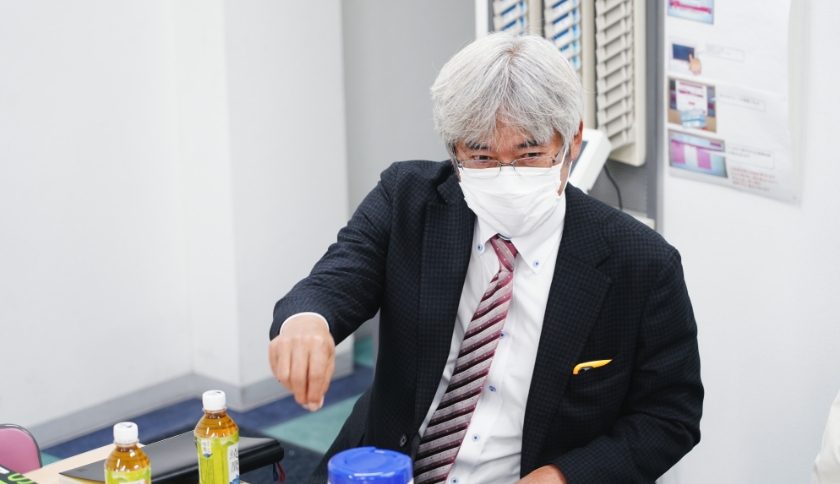
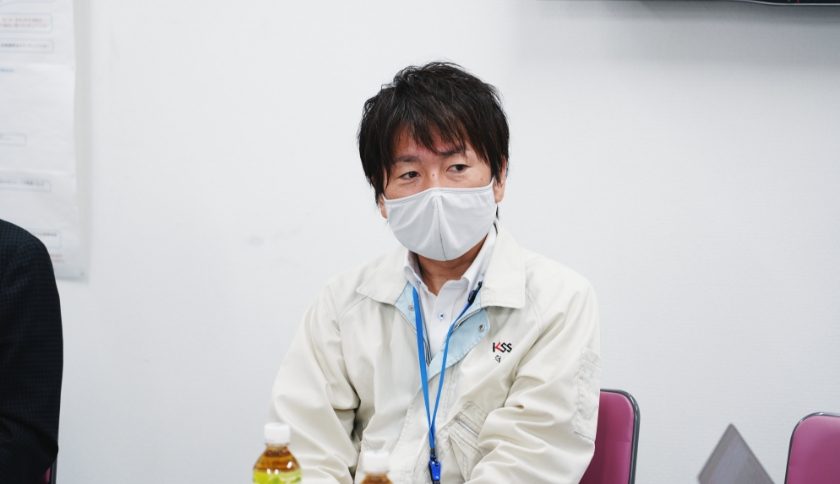
田中鉄工所初の産業用ロボット導入は、SIerである南北産業およびケイエスエスとの三人四脚で進みました。初めに考えたのは、人が並べたピンをduAroがピックアップし、ブロックへ挿入するというシンプルなシステム。田中社長はそのアイデアを見て、「思ったより人がする準備が多いな」という疑問を抱きました。そこで川崎重工 精密機械カンパニー ロボットビジネスセンター長 橋本康彦氏(当時。現:川崎重工 代表取締役社長)に相談すると、明快な答えが返ってきました。「もっとロボットをこき使ってください」
試行錯誤の結果、平行ピンのセットから圧入後の検査まで、圧入作業工程の一連を自動化することに成功。①ピンを正しい方向でセットする供給ユニット、②ピンの向きが正しいかダブルチェックするための面積センサー、③ブロックとピンを治具にセットするduAro、④圧入ユニット、⑤プレス力測定のロードセル、⑥正しい奥行きまで挿入できているかを検査する高さ測定の接触式センサー、⑥全製品の検査記録保管システム、という6つの要素を組み合わせた「ピン圧入ロボットシステム」が完成しました。
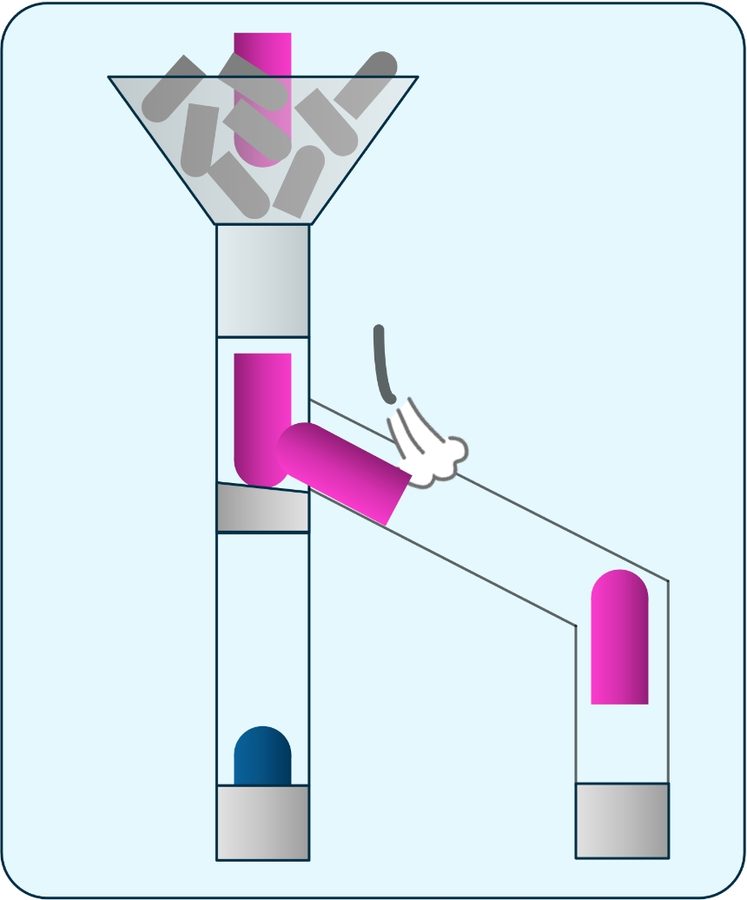
平行ピンを正しい向きでセットするために考案した供給ユニット。受け皿から降下したピンが正しい向きならメインルートへ、上下逆ならサブルートへ逸れて方向転換する仕組みをからくりのような仕掛けで実現した。
とりわけユニークなのが①の機構。シンプルなからくり機構でピンの向きを選別するというユニークなアイデアを採用しています。「費用対効果を考え、一番シンプルなカタチにしました」 そう語るのはケイエスエスの守田 大氏。ピンの向きや穴の位置を認識するビジョンセンサーを設置するには、遮光設備などの周辺環境やAI機能といった大がかりな仕組みが必要になります。「そうすると値段も大きく跳ね上がります。ですから、できるだけビジョンを使わずに、物理的にピンの選別を行うメカ主体の供給ユニットを考案したんです」
供給ユニットは、一端が丸く、一端が平坦というピンの形状を活かした仕組みになっています。まず、じょうごの様な形状の受け皿に投入したピンが、一本ずつ管の中へ降下。管の途中には傾斜のついた仕切り板があり、降下したピンの下面が平らであれば仕切りにあたっても倒れず、仕切り板が開いてそのまま直下の排出口へストレートに向かいセットされます。一方、上下逆で降下した場合はピンの丸面が仕切り板にあたってパタンと倒れ、正しい向きに方向転換しながら側道へ分岐、それをエアーで送り出して排出するという仕掛け。万が一このユニットを通過してもなお上下逆方向になっていた場合に備え、面積チェッカーでピン端の形状を読み取り、あいまいな場合は排除するというダブルチェック機構も用意しました。
人が作業していたときに0.05%あった不良率は「自動化により、ピンの向き間違いから圧力不足、挿入不良を100%無くすことができました」(田中社長)。2016年から5年間、およそ10万個の製造過程で生じた不良はゼロ。何よりも、単純作業をduAroが担うことで、社員がより高度で専門的な作業に従事できるようになったことが大きい、と田中社長は語ります。田中鉄工所の社是は“企業は人なり”。duAroはその理念を実践する一助となっているのです。
今後の展望や計画:
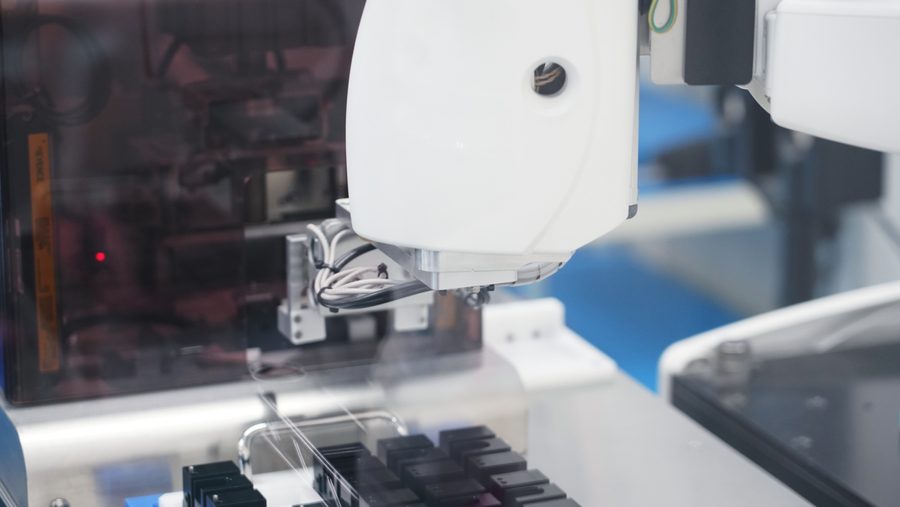
ピン圧入作業の自動化を実現するには、SIerの存在が欠かせなかったと田中社長は振り返ります。「ロボット関連の専門用語などは、我々でも分かるように説明してもらわなければ理解できないものが多い。SIerは、ロボット導入業者とロボットメーカーを繋ぐ通訳のような存在といえるのではないでしょうか。彼らのような架け橋がいてくれれば、まだまだ小さな工場にもロボットが広がっていく可能性があると思います」
手元の細やかな作業に一心集中する技術者のすぐ傍らで、今日も静かにピンの圧入作業を淡々と行うduAro。田中社長は、その活躍の場をさらに広げようと考えています。「例えばブロックのマスキング処理や部品の出荷前検査といった、ピン圧入作業の前後工程もduAroで自動化できるはずです」 さらに、現在はレンズの組み込み作業にもduAroが導入できるのではないか。そんな検討も始まっているそうです。
ー 導入企業情報
会社名
株式会社田中鉄工所
代表者
代表取締役社長 田中祥靖
設立
1938年6月
資本金
1200万円
事業内容
産業用ロボット部品及び医療機器関連部品などの精密機械加工
社員数
40人
事業所
本社=兵庫県神戸市兵庫区駅前通2-2-3
ウェブサイト
http://www.tanaka-iron.com/index.html
ー 導入ロボット
モデル名
duAro1=「人共存型」をコンセプトにした双腕スカラロボットの第1号
特長
省スペース、簡単教示、簡単設置、高い安全性
可搬重量
各アーム2kg(両アームで4kg)
軸数
各アーム4軸
繰り返し精度
±0.05mm