By Zachary Thoma, Regional Sales Manager – Kawasaki Robotics (USA), Inc.
The automation industry is filled with myths. In all fairness, this isn’t so different than any other industry. Anyone who has ever been married can likely attest to the pressures they may have felt to spend a ton of money on their wedding. Ironically, at least in my experience, the things that people spend money on at their weddings seem to be the things that they remember the least. Yet, the wedding industry keeps buzzing along to the tune of $57.9 billion in the U.S. alone.
Unknowingly, we all absorb things that influence what we think we want. For better or for worse, our own industry has its own fairytales where robots are running in perfect unison with multiple high-tech end-effectors, no collisions, and elegant AI guiding the way in real-time – nary a wire to be seen.
As a former robotics integrator, I can tell you that people often had this image twinkling in their eyes when they came into my office. After learning more about their application – and their budget – I started asking tough questions. I would explain what that type of system would likely cost, as well as the intensive development and labor hours that goes into them.
That’s when the questions started rolling in:
- “Why does it cost so much?”
- “Doesn’t the vision system just tell the robot where to go?”
- “Why does it take so long?”
- “Don’t you have someone who knows how to do that?”
- “I thought collaborative robots didn’t need a fence?”
These are all valid questions, and it makes sense why someone new to robotic automation would ask them. While I assured them these things certainly can be done, I would also explain that these systems are all very customized, very involved, and usually very labor-intensive.
Now this can all sound pretty dismal. It’s really quite the opposite, though. These exercises are a means of peeling back the onion to not only understand the customer and their needs, but to arm them with the correct information and knowledge needed to take their project into the market. It sets the stage for a real partnership, one where we are fully aware of each other’s expectations, needs, and capabilities.
It is on that footing that I’d like to share with you the top five myths I have encountered so far in my 20-year career in automation:
MYTH NO. 5: The Robot Does Everything On its Own
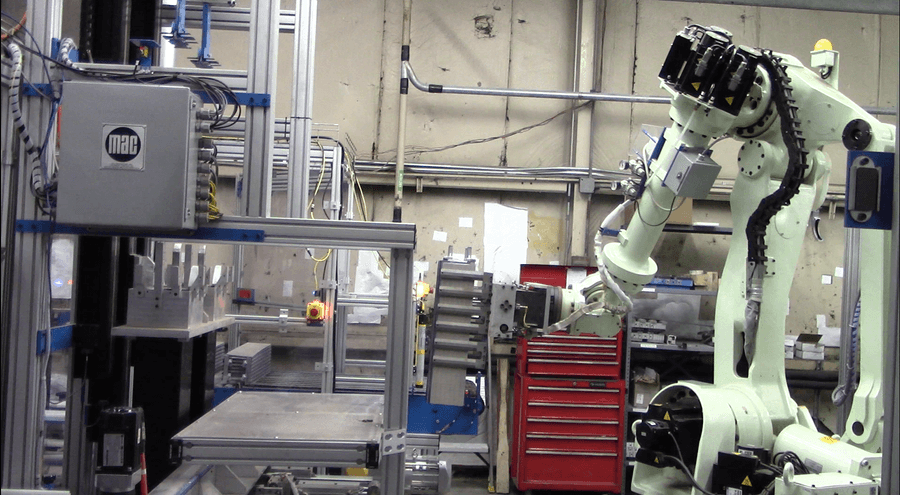
Certainly, the robot is often the centerpiece of the system. It’s probably doing more visible, actionable work than any other component. That being said, PLCs actually drive most complex robotic cells interconnected with a myriad of hardware and equipment. Things like sensors, scales, fixtures, actuators, light curtains, and on and on… These things are all communicating and orchestrating the actual functionality of the cell. The robot path programming itself is usually pretty straightforward. The I/O communication and interconnection of all these devices into a fluid and (mostly) error-proof system is where the rubber meets the road, and it’s where the integrators tend to spend most of their time.
MYTH NO. 4: The Robot Knows What to Do On its Own
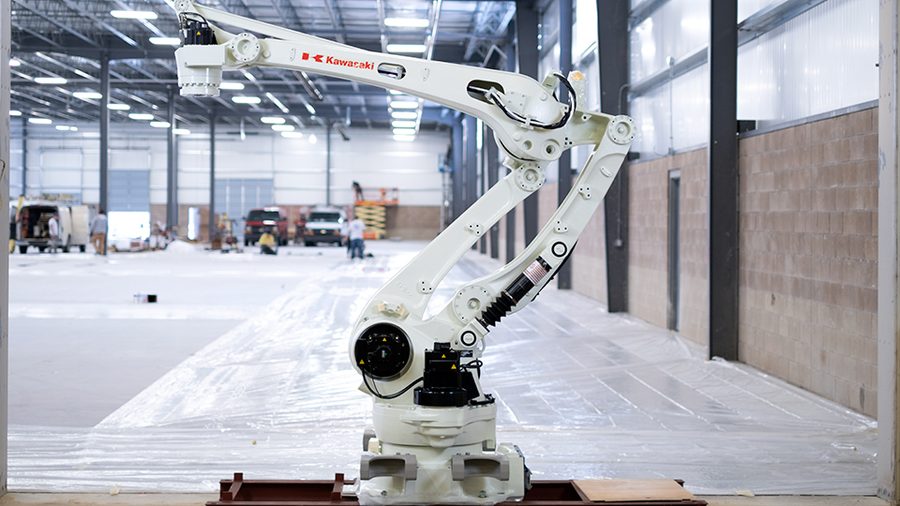
This is a dangerous one. I can’t say it any more plainly than this: robots are machines. They know absolutely nothing that you don’t tell them. Without sufficient input, guidance, path programming, I/O interfacing, error checks, etc. the robot is essentially a floating-vessel immobilization device, aka, boat anchor.
Think of the robot as a six-axis arm used for any application or task it fits for. The reason for the six axes is it seems to be the magic number for what it takes to get in and out of spaces and complete movements in a way that is most useful for, well, just about everything. The robot OEM basically wants to provide a blank-slate machine that…
- … is practically adaptable
- … receives data from other pieces of technology
- … accomplishes programmed tasks
- … works within the laws of physics without hurting itself or anyone else
This alone is no small task.
MYTH NO. 3: Robots Take Jobs
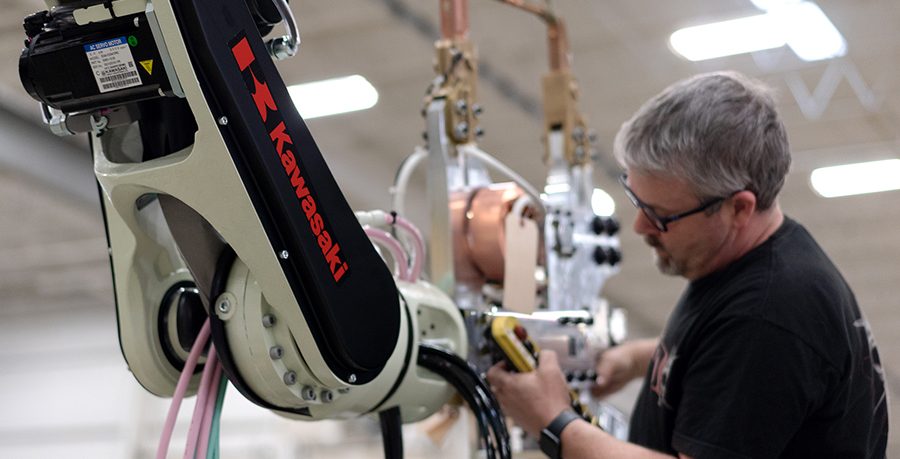
This one is a bit controversial. To be fair, there are scenarios where putting robots into service caused layoffs. However, this is far more the exception than the rule. Particularly in today’s labor market, manufacturers put robots into place to execute unsafe, physically taxing, or monotonous jobs they have trouble finding anyone that can – or will – do. In most cases, robot deployment spares workers and operators from these types of jobs, moving them to more human-friendly jobs. The new equipment can even advance their skillset to operate the robotic cell. (A task far more lucrative, marketable, and enjoyable than, say, stacking 50 lb. boxes onto pallets all day.) In many cases, the increased production actually results in hiring more people.
MYTH NO. 2: Vision Systems Solve Everything
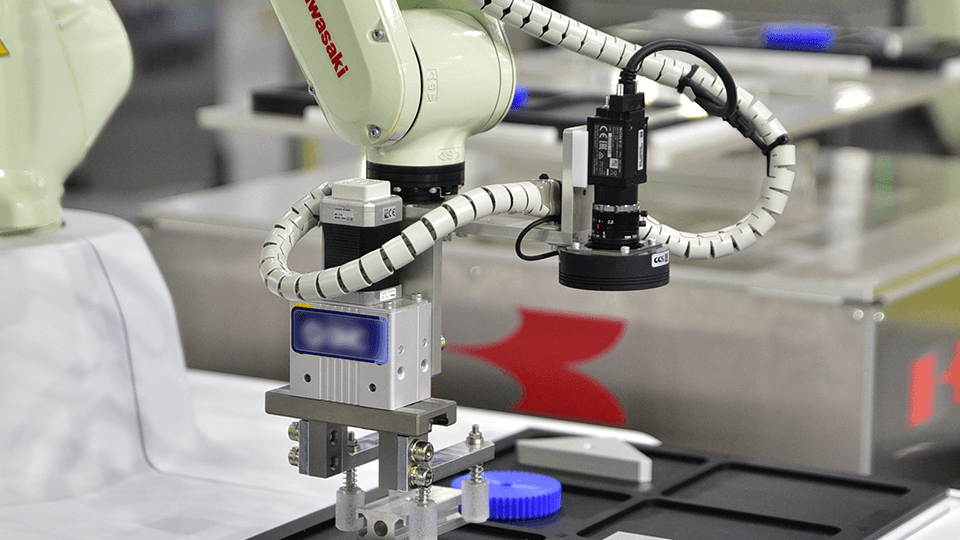
There was a time when only to the most advanced and elite manufacturing entities out there used machine vision, due to cost and complexity of programming. Those days have passed. Vision systems are now cost effective, easier to program, and abundantly used in facilities from large auto manufacturers to mom-and-pop machine shops.
That all said, the primary takeaway from myth no. 4 still applies. The camera is just another tool that knows absolutely nothing that you don’t tell it. A smart camera at its most basic is just a lens and a processor. Manufacturers design cameras to perceive certain characteristics and details while sending and receiving signals, but someone has to tell the camera everything it needs to do.
The people who make circular saws and hammers don’t intend for those tools to build houses by themselves. It takes a skilled user to make those tools work in their favor to accomplish a specific task. Vision systems are no different.
MYTH NO. 1: Collaborative Robots Don’t Need a Fence
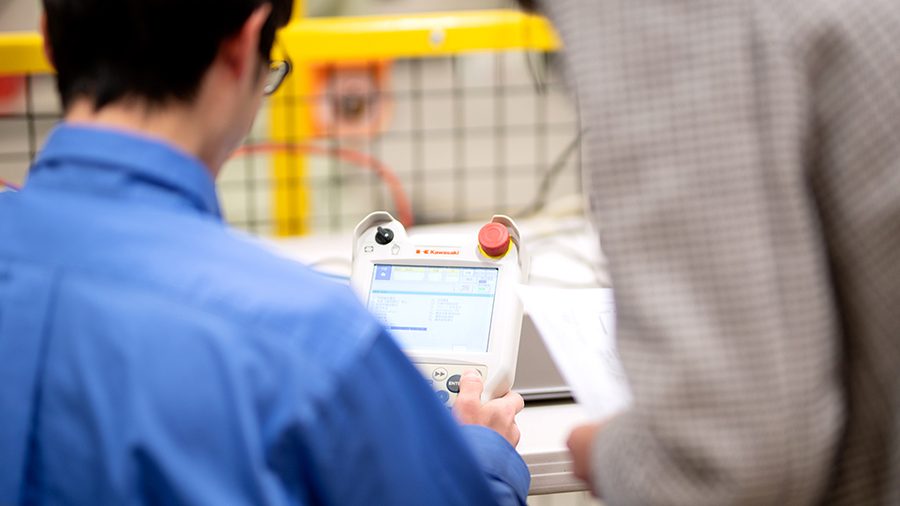
Collaborative robots have hit the market with the force of NASA’s Saturn rocket. While they are still a very small segment of the overall robotics market, they have set a new narrative about who robotic automation is for, how easy it is to execute, and how affordable it is. As such, more people have started approaching robotics in a way they never have before. Where people often see this value is in not needing a fence around the robot. But… (as I tap my pipe on my chin). Is. That. Really. True?
The simple answer is no, it’s not true.
Here’s why: there are no collaborative robots, only collaborative applications. What makes an application collaborative is not whether the robot can detect your presence, stop on a dime, or keep from getting your fingers pinched. What makes an application collaborative is if it can safely be executed with the appropriate equipment in the presence of humans and without guarding. If you speed a collaborative robot up beyond the current ceiling for collaborative operations, you no longer have a safe application.
Also, one might not think that they will care if the robot runs a little slower. Or, that their application is an exception and won’t need guarding. I can’t tell you the number of people I’ve seen purchase a collaborative robot with dreams of one day having a fence-less facility. Then, they deploy the robot and find out from their safety manager that they do, in fact, need a fence.
Also, I’ve seen this scenario play out: Collaborative robots are purchased and deployed. Next, an engineering manager comes out to the floor and sees it running at a snail’s pace. They are immediately frustrated by the capacity they’re missing out on all for want of not having a fence.
Want to know more?
Well, there you have it: my top five robotic automation myths. If you have any questions or would like to continue this conversation, feel free to shoot me an email.
Please note the views and opinions expressed in this blog belong exclusively to the content creator, not to Kawasaki Robotics as an organization. The content of this blog post or any user content it generates in no way convey the thoughts, sentiments or intents of the organization.