By Bon Carter, Regional Sales Manager at Kawasaki Robotics
“How much does it cost?” is a question everyone asks before making a purchase, no matter how small. For manufacturing companies looking to spend on new capital equipment, that question is given so much attention it overpowers all other factors.
But beyond that initial question is an opposing one that forward-thinking companies consider as well: “How much will it cost us if we don’t make this purchase?”
Industrial automation systems come with a price, just like all other capital equipment. But the effects of choosing not to automate can be just as impactful as the effects of an upfront purchase price.
1st Cost of Not Automating: Cycle Times, Product Quality, Wasted Materials

Humans are often faster at performing a task than cobots and industrial robots, but they also get tired, distracted, or even injured on the job. Industrial automation systems are a real-life version of The Tortoise and the Hare. All it wants to do is its job. No food, rest or breaks of any kind are necessary.
That consistency pays big dividends over time, leading to improved cycle times, stronger product quality and fewer wasted materials. Those who decide not to automate are missing out on these attractive benefits.
2nd Cost of Not Automating: Labor (or the Lack Thereof)
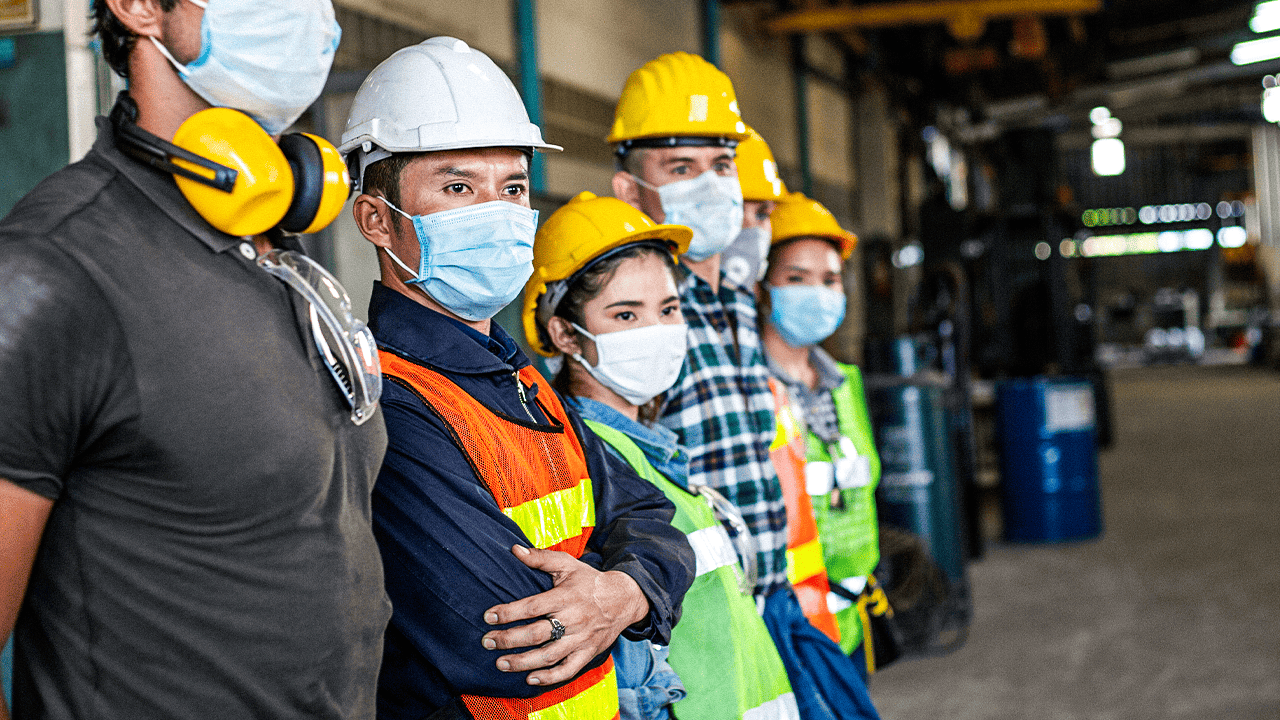
It’s no secret at this point: it’s hard for pretty much every sector to find skilled workers to fill open positions, and it’s certainly true in manufacturing. Many facilities have plenty of work to be done, but the workers they need are either inexperienced or not there in the first place. What’s more, the tasks might be dull, dirty, or even dangerous—three traits that are not suitable for humans.
Industrial automation is one of the best solutions we have for this labor problem. Existing staff is empowered to perform higher-value tasks, which are (ideally) safer, more ergonomic, and much more satisfying. And on that note:
3rd Cost of Not Automating: Workplace Injuries and Workers’ Compensation

Studies have shown the significant costs involved with workplace injuries and fatalities, and the verdict is official: on-the-job injuries place a massive toll on organizations—not just financially, but operationally as well. The average workers’ compensation claim is a little over $40,000 per incident, and that number does not consider factors like increased premiums and lost time.
Facilities all over the globe are filled with human workers who perform tasks that pose an injury risk. But with industrial automation, robots can take on riskier tasks with ease, making workers safer—and saving manufacturing companies significant money and time.
ID Logistics, an international contract logistics company, has a goal to reduce the frequency and severity of workplace accidents by 40% before 2027. To help make this happen, the company deployed almost 500 robots in 2023 across nine countries. Alongside the ergonomic and job satisfaction benefits, ID Logistics has become even more attractive to the best talent in the industry.
4th Cost of Not Automating: Lack of ROI Realization
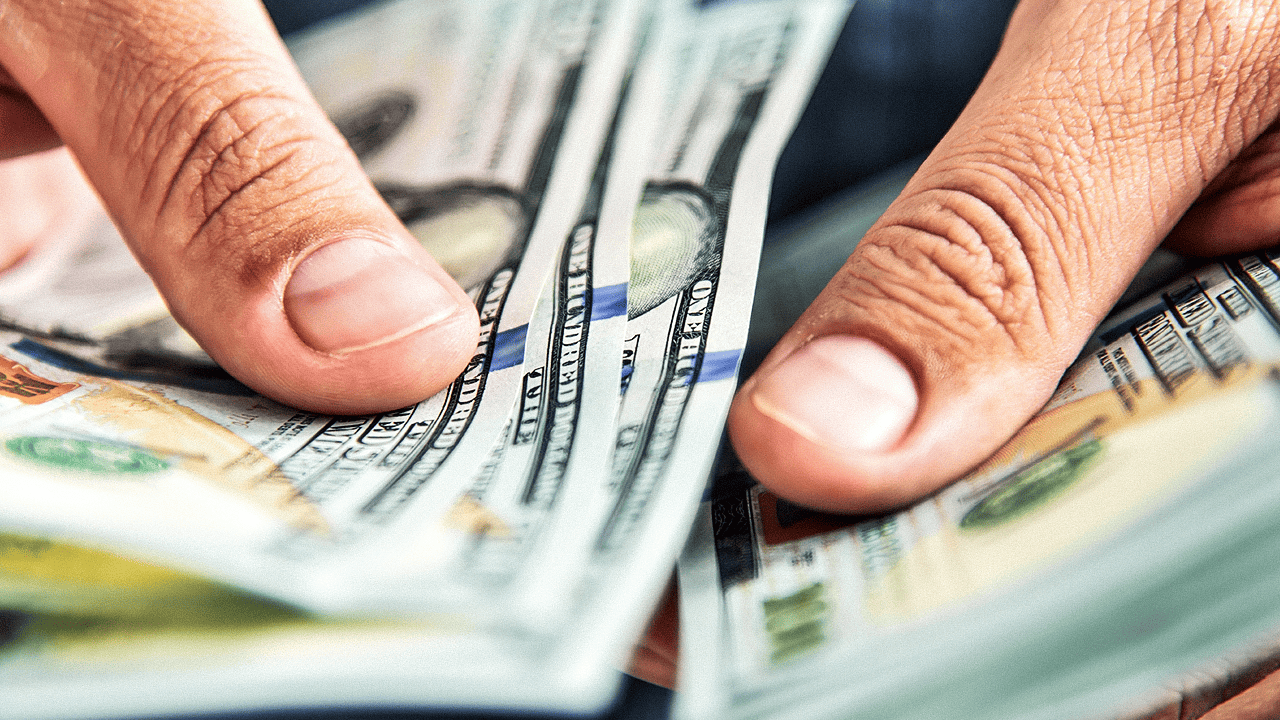
Take a look at this ROI calculator from automate.org. It has variable fields you can adjust to see what you can expect to gain by automating, but it also has default values in place.
In their example, two robots were installed to operate two shifts per day, five days a week. They estimate that the cost of this two-robot system would be $250,000 total. This new system would save $45,000 in annual labor costs per operator, bringing a 27% productivity gain.
Using these numbers, it would take just 16 months to fully recoup the purchase price. If you choose not to automate, over a 15-year period, you would miss the labor savings of $2.8 million and productivity savings of $750,000. Those savings are even higher when you factor wasted materials, improved product quality, happier and more productive staff.
5th Cost of Not Automating: Missed Opportunities for State & Federal Funds

Many states reward automation-minded companies with cash reimbursements for equipment and training. A couple of examples:
- In Kentucky, Grant-in-Aid (GIA) gives cash back for occupational and skills upgrade training at businesses in the state. The Skills Training Investment Credit (STIC) offers state income tax credits for Kentucky companies to offset the costs for approved training programs.
- The Bureau of Workers’ Compensation (BWC) in Ohio recently awarded a $40,000 Safety Intervention Grant for the purchase of one custom-designed mechanized assembly line integrated with robotic welding arms to reduce the risk of injury to fingers, hands, wrist, arms, shoulders, neck, back and legs.
Check with your state to find out if any breaks, credits, or grants are given to companies who automate processes!
What Is Your Cost of Not Automating?
If you need a partner to help you crunch the numbers, talk to Kawasaki Robotics. Our people are known for being as flexible and supportive as our robots are. Reach out anytime to get the conversation started.