By Mike Dawson, Service and Operations Manager
When it’s time to perform scheduled robotic maintenance, partnering with your robot provider can offer a smooth path to a successful and efficient process. With expert guidance, a company will learn how to plan for the downtime, recognize equipment problems on robots prior to shutdown and become familiar with robot preventive maintenance (PM).
During the shutdown process, maintenance on the robots as well as PM are commonly done. For inexperienced companies (those that have integrated their first robots over the past two to three years), Kawasaki Robotics recommends the initial upfront investment for on-site PM training from an experienced maintenance team member.
Consider the price of PM gone wrong by an inexperienced technician. For example, if pressure sensors aren’t cared for during maintenance, seals can be blown out, which on average cost $3,000 to $4,000 to replace. Paying the upfront $1,500 fee to hire a professional technician would have saved a lot of money in this case.
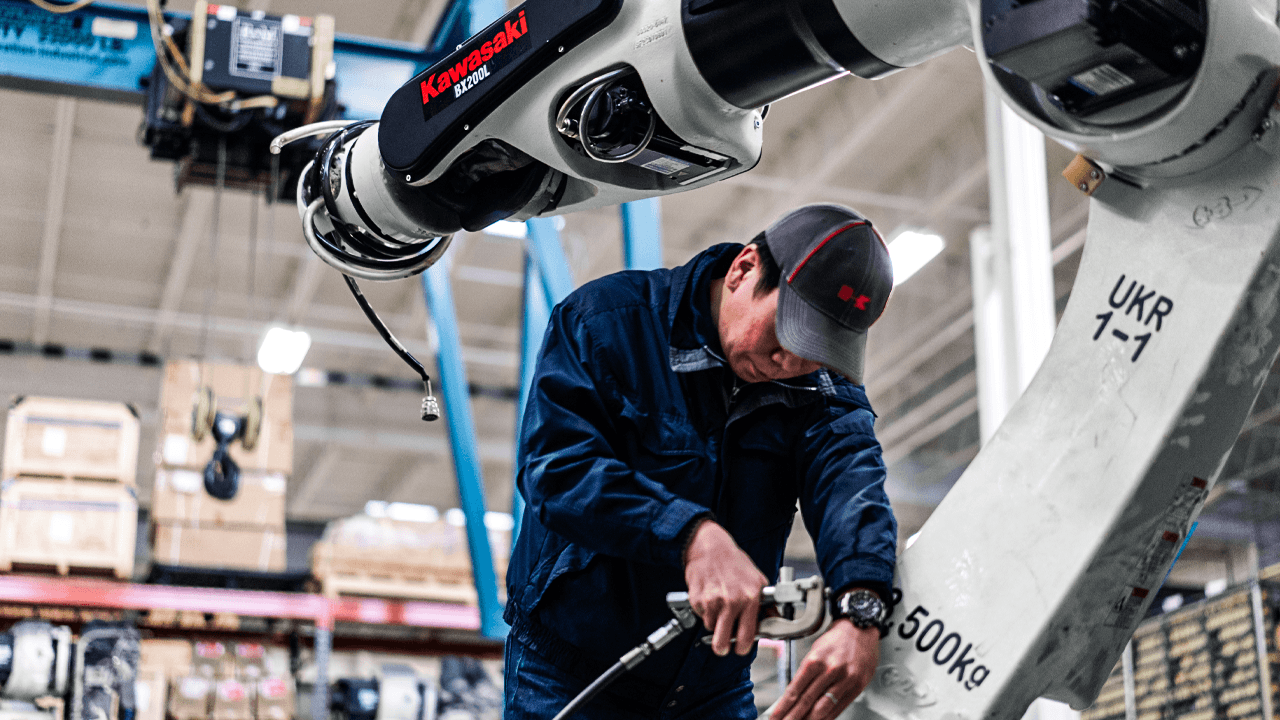
Kawasaki Robotics, which assists between 3,000 and 5,000 shutdowns per year in the United States and Canada alone, offers hands-on training sessions to help maintenance teams around the world to simplify the concept of the whole robot. Training empowers maintenance teams to know when it’s time to troubleshoot, or replace a part themselves or at least to know the right
questions to ask over a phone call to support. With valuable and engaging training under their belts, these maintenance teams can report high-quality data, which enables not only a faster response time from support but a more accurate answer to the problem at hand.
By the time a company has been maintaining its robots with the assistance of the manufacturer for two and a half to three years or so, the facility will become independent and confident enough to do its own robotic maintenance. At that point, the robot manufacturer is still available for support and to answer questions that might arise.
Planning for Robotic Maintenance
Prior to shutdown day, it is crucial for the parties involved to plan and schedule the maintenance. For instance, a first visit by the robot support team might entail gathering data for predictive maintenance such as the robot count and models, the processes performed and the amount of time the robots are running. Knowing this information enables the maintenance team to return with the proper parts and components on shutdown day. When teardown begins, it is quite possible that problems on the robots, such as broken components, will be discovered that might necessitate these spare parts.
For robotic maintenance, it is critical to start with a new encoder battery or the current encoder battery should be in spec for the expiration date. The encoder battery saves the fingerprint data that commands its existence. If the battery is dead when the equipment is shut down, recovery and startup problems might follow that can necessitate robot reprogramming.
Common Issues
At shutdown, Kawasaki Robotics suggests inspecting for specific robot issues that often inconveniently rear their ugly heads during this time. When all equipment is shut down, it is a good opportunity to inspect robots with a fine-tooth comb—a task not easily done when the robots are running. Robot backlash and damage to the harnesses are two main problems that are often discovered.
To inspect for backlash, a gentle wiggle of the powered-down robot arm can reveal slop in the wrist area. This indicates the need for repair, which can be completed either at that time or can be scheduled for maintenance later for a more in-depth fix.
For the robot harnesses, technicians should do a thorough inspection to ensure no rub marks, tears or scratches on the wire components are present.
Maintenance Intervals
Upon completion of a shutdown, a robot provider can create a predictive maintenance schedule around a company’s maintenance needs. This can include a year’s worth of maintenance intervals for changing the grease and changing the belts on the robots, among other maintenance items. Creating a schedule also helps determine the robots’ needs at the next PM cycle.
Ready for a Successful Shutdown? Talk to Kawasaki Robotics.
If you’re due for robotic maintenance, bring in the professionals who know how to get you back up and running quickly. Contact Kawasaki Robotics to put your shutdown date on the calendar.