By Zachary Thoma, Regional Sales Manager at Kawasaki Robotics
The robotic process automation (RPA) audit is not just a formality, but a crucial step in your automation journey. It helps you identify and mitigate potential risks, ensuring a smooth transition to automated processes. If you’ve considered automation in your facility and thought, “Where do we start?” You’re not alone. Automation is more than a trend in the manufacturing
industry: it’s inevitable as it brings a host of benefits that you’ve probably already heard about.
The problem is, when you look around your floor, it’s hard to know where to automate next. I’ve been on multiple sides of the robotics industry for many years. Generally, I advise first-time automation users to address minor pain points first, gain confidence in the automation process and tackle more significant challenges.
What is the quickest way to automate?
That’s the question you should ask yourself before that first automation project.
When your company starts its automation journey, you don’t need to spend big up front. It’s risky, and you still don’t know what you don’t know. So go for a project that will bring rapid ROI and get a win under your belt. This proves to you and your stakeholders that automation is a viable business practice that should be expanded upon.
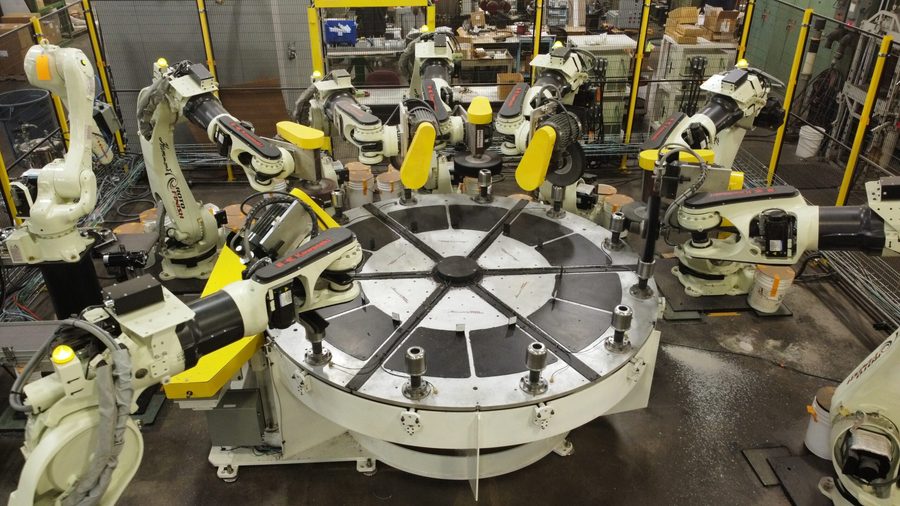
This brings us to the concept of a robotic process automation (RPA) audit.
That previous paragraph is the kind of thing that Kawasaki Robotics does during its RPA audits. Someone (it might be me if you’re in my territory) shows up to your place and, free of charge with no strings attached, walks through your facility with you to evaluate potential projects—for now and in the future.
A key benefit: the end-user gets a bespoke experience. It’s important to remember that every manufacturing process varies widely—even if those processes result in the same product in the end. Space considerations, workforce factors and even the simple preference of “how things are done” all come into play.
Imagine a world where A and Z have to be at the start and finish, but all other letters can be moved anywhere. That’s what it’s like walking into a new manufacturing environment. This means that our job is to ensure that the arrangement results in something we can accomplish in an efficient way. If the way you accomplish tasks is unique, our solutions have to be too. That’s what we set out to do with our robotic process automation audits.
So, you might be interested in an RPA audit. What can you expect?
In terms of preparation before the actual audit, there are some things you can do to facilitate the process:
- List of production bottlenecks, potential automation projects and goals: what are the key issues that need to be solved? Is there a required ROI?
- The ability to show us all the entire facility and visit the various departments.
- Permission for us to take some pictures and videos
- Identify and poll internal stakeholders and production employees, to provide a rundown of what we should be prepared for (skeptical operators, tight budget, difficult to implement change, etc.)
After the audit, you’ll get a quick report of everything we discussed, which you can share with whoever needs to see it. When you’re ready for a deeper dive, we pair you with one of our integrator partners who has proven success with your chosen automation system. We can meet again to discuss the recommendations we covered in the audit, and you’ll get a formal quote
from your integrator.
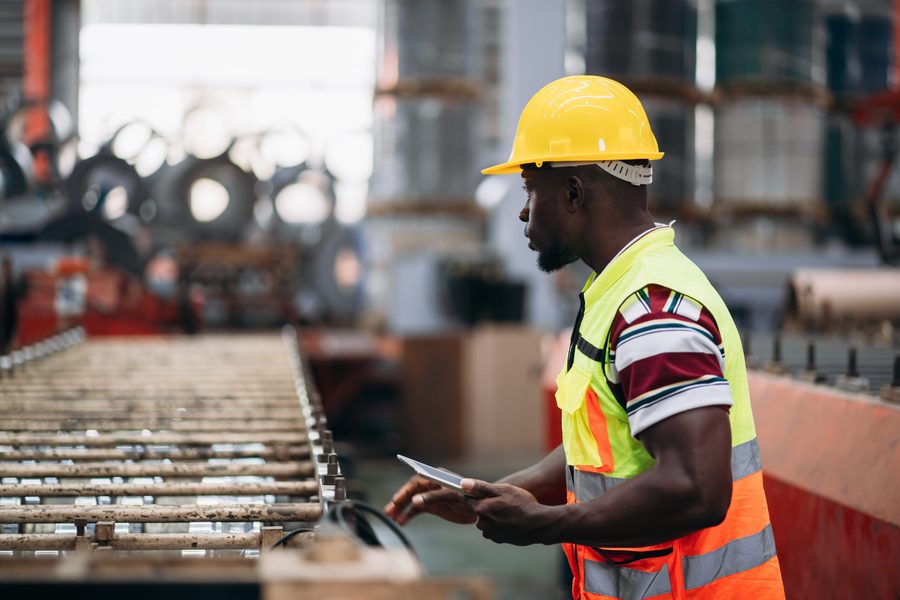
All of this—from asking us for an RPA audit to getting a quote from the integrator—can happen in as little as four weeks.
Let the RPA audit be your catalyst for change
It happens to all of us. You get comfortable with your processes and routines, and it’s daunting to change them up. For your inaugural automation system, we want you to build confidence and comfort. That’s easiest to do with the easiest projects.
Even the most cost-effective automation systems can be a significant expense. Some of the people on your floor might have some objections, too. These are real hurdles, and we’re happy to help you have those conversations while we’re there for the RPA audit.
When you should skip an RPA audit
If you’re well-versed in automation already and have multiple systems installed, you probably don’t need this first step.
But honestly, if you’re starting out, I can’t think of a good reason not to take advantage of it. Personally, I used to be an automation systems integrator before I came over to Kawasaki Robotics. I can take a quick look at your floor and feel good about recommending your first project. In all likelihood, your ideal system will be something you haven’t identified yet.
And beyond simply identifying the project, your robotic process automation audit will tell you why it was chosen. Explained in-person and on your terms and getting that all-important buy-in from everyone at the company.
The RPA audit, like a lot of other things, is done a bit differently here.
Our RPA audits were created to be a no-cost value add. It helps you learn the questions to ask, the decisions to make and the conversations to have with the people around you to ensure your next automation system is a massive W. Our goal is to set our customers up for success as much as we can, and on-the-house audits are a great way to begin that journey.
If you’ve scrolled this far, first of all, thank you and congratulations. Truly impressive attention span. Hopefully you’ve come to the conclusion that at Kawasaki Robotics, we’re never about the hard sell. The people who work here are always collaborative, friendly, and easy to work with.
If you have some questions or want to book your RPA audit, contact us any time. You’ll have your local rep taking a tour in no time.