By Mike Dawson, Service and Operations Manager
When working with automated equipment, users often assume it will run reliably “forever.” After all, it was implemented on the plant floor to work harder, longer, faster and more dependably than humans, right? Yes. However, over time, even robots wear down or become damaged, which decreases their accuracy and repeatability. When operators notice a decline in robot performance, it is worth making a call to their provider to inquire about opportunities for improvement.
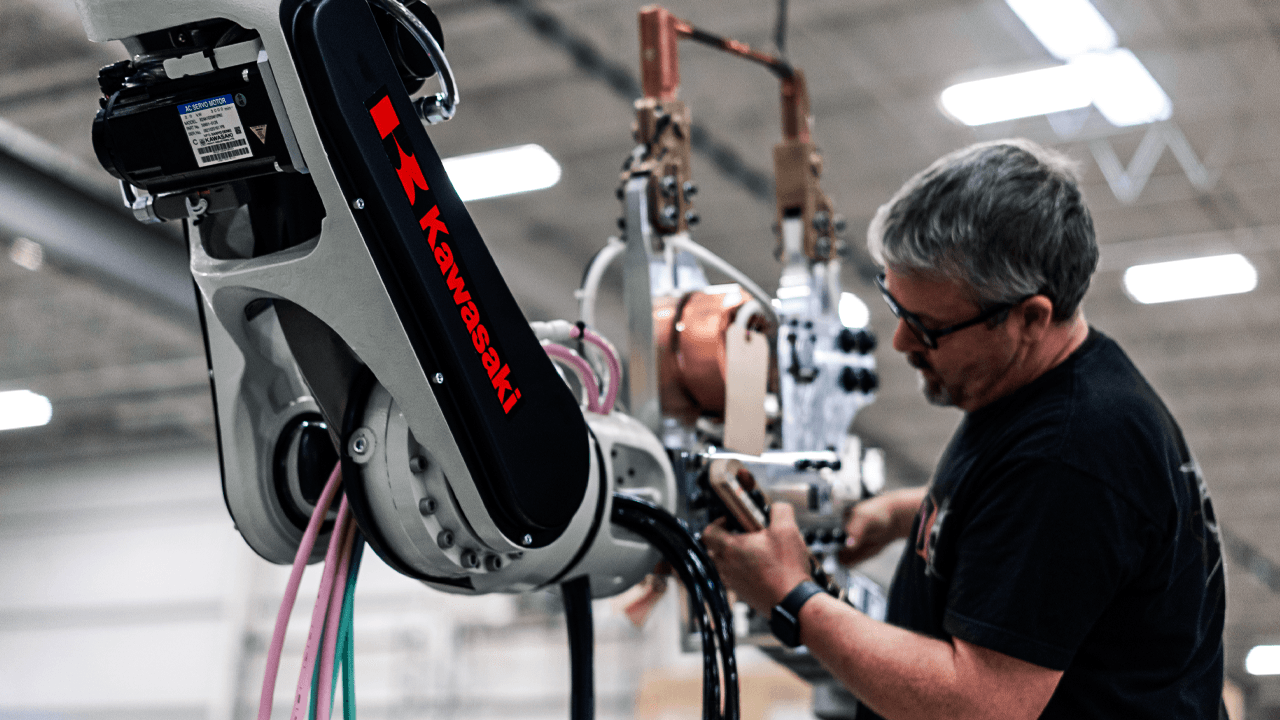
What is a robotics retrofit?
Kawasaki Robotics North America presents two options to solve this automation efficiency problem: a robot upgrade or retrofit. A retrofit is building a new robot from the ground up, which will ultimately replace your existing system. Using specifications required by the customer, a retrofit replaces equipment with faster or stronger (or whatever the need might be) robot options. A retrofit can also consist of adding new robots to a cell to increase throughput.
What is a robotics upgrade?
An upgrade, on the other hand, takes existing robotic equipment and improves upon it. This includes upgrading to new controls and components to the current standard to provide compatibility throughout the cell. For instance, if a customer has a robot with A, B, C or D series controllers from Kawasaki Robotics, while the current controllers are E and F series, the older controller parts are no longer supplied by the company. Therefore, it would benefit the customer to perform a retrofit to have access to those replacement parts. In a nutshell, an upgrade makes your automation systems faster, stronger and better.
What to expect from your robotics retrofit or upgrade
Whether an upgrade or retrofit is chosen, Kawasaki Robotics can either visit a company at its facility or help with the project remotely. The service technician’s first duty is to gather the diagnostic data from the robot just as they do for a regular service call. With information from the error log as well as operation data stored inside the backup, the technician can discover the pain points within the system. Then, those issues can be addressed at the start of the project. For a fee, the tech will also run full simulations with different robot models to ensure the best fit for an application. Kawasaki Robotics suggests a few tips for users during the initial meeting with the robot
technician and before making a purchasing decision:
- Be forthcoming with an extensive wish list. Users are often surprised by how much the service provider can check off a list such as this.
- Ask lots of questions. The technician might overlook a point if the user doesn’t mention it.
- Use Kawasaki Robot Solutions’ offline programming software tool to play with available options. The software creates 3D models of the user’s robot cell and workpieces. It will program the robot and design simulations on the PC prior to installation.
Ready for an upgrade or retrofit? Talk to Kawasaki Robotics.
Does your robot cell feel a bit sluggish lately or not as accurate as it once was? Bring in the professionals who know how to set up your cell for the highest efficiency and throughput. Contact Kawasaki Robotics to put your service date on the calendar.