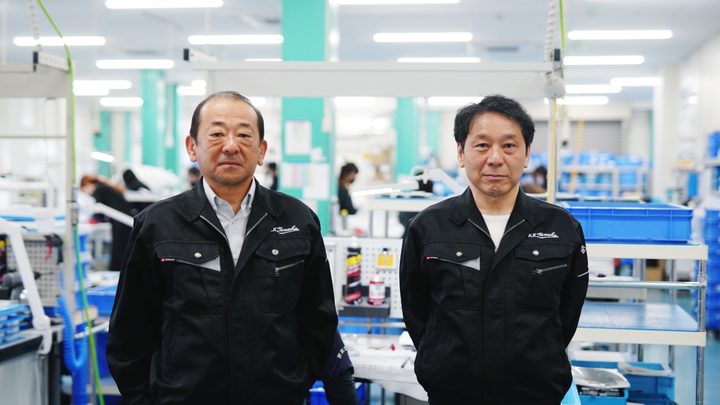
- IndustriesMachinery & Metal Manufacturing
- ApplicationsAssembly
- Robot SeriesduAro series
Robot user: Tanaka Iron Works Co., Ltd.
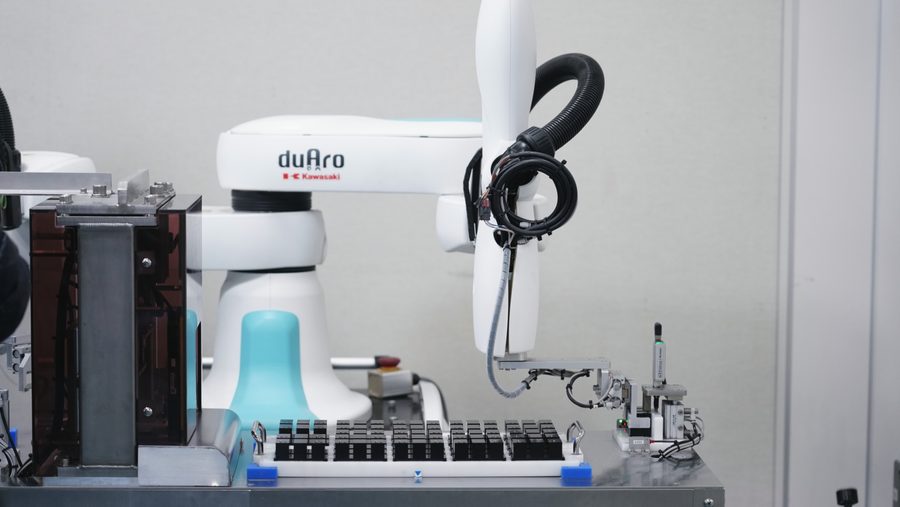
Tanaka Iron Works Co., Ltd. (Headquarters: Kobe City, Hyogo Prefecture, President: Yoshinobu Tanaka) manufactures precision machined parts for industrial robots, medical devices, aircrafts and nuclear power plants. The company had already constructed a production system that operates unmanned 24 hours a day in its plant for cutting processes using dedicated machine tools.
However, the company had not been able to realize automation for the finishing process, where the main work is performed manually.
What should be done to introduce industrial robots into a space where people are performing the main part of the work? The answer to that was the “duAro” collaborative type dual-arm SCARA robot from Kawasaki.
Introduction background/issues:
The door to automation was opened by a collaborative robot that can coexist with humans without safety fences
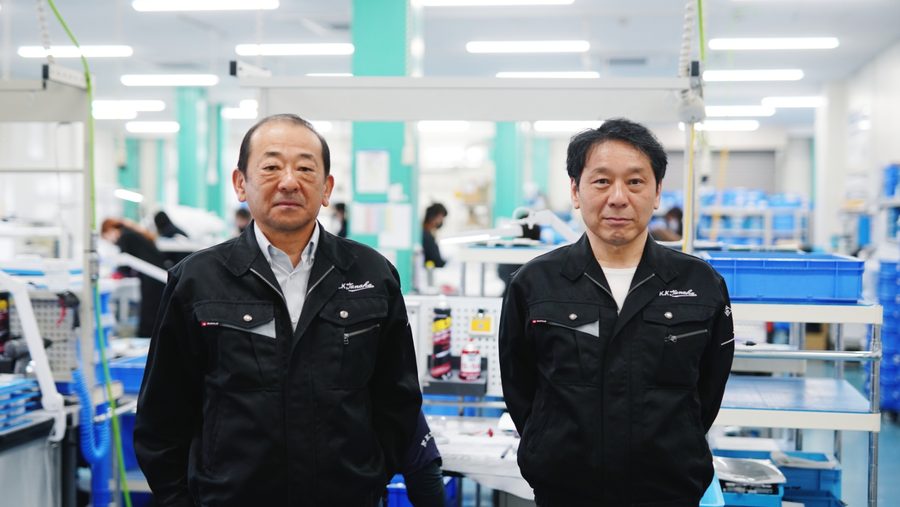
Tanaka Iron Works is a professional in the field of precision metal processing.
The company started business in 1938, with the production of the main landing gear for the Kawanishi N1K fighter plane. For the more than 80 years since, it has continued to produce precision processed components that are used in aircrafts, medical devices, nuclear power plant components and the like.
It also built up a relationship early on with Toa Medical Electronics Co., Ltd. (currently Sysmex), which achieved the practical application of the first automatic blood cell counter in Japan.
Components from Tanaka Iron Works are used in the current blood cell counting inspection equipment from Sysmex, which boasts the top share globally.
The company has also been a supplier to Kawasaki Robotics since 1977 and has delivered the mechanical components for the arms, etc., which can be described as the heart of industrial robots.
The strength of the company is its flexible multi-product variable quantity production, which merges 17 machining centers with skilled craftsmanship.
The company is engaged in ever expanding businesses of industrial robots for manufacturing automobiles, semiconductors, and medical device components. President Yoshinobu Tanaka explains that, “In recent years, we seem to be operating in a 120% utilization situation and we have really struggled with a shortage of labor.
For this reason, we have always been searching for work that robots can perform instead of people.”
The first floor of the two-story plant is filled with dedicated machinery where the cutting processing for precision processed components is performed unmanned 24 hours a day.
On the other hand, people are mainly performing the work on the second floor, where finishing processes are performed.
When President Tanaka looked at that workplace, where there are multiple technicians in front of work benches silently performing the final processing work, he thought, “There must be some elements here that can be automated.”
However, introducing an industrial robot to a workplace where human workers are the main element requires large-scale improvements, such as the installation of safety fences.
President Tanaka says that, “If you ask what the biggest issue is for a small factory, it is of course space.
This is why the majority of locations where industrial robot use is possible are large-scale manufacturing lines such as in the automobile and semiconductor industries. I had never considered that we would be able to introduce one to our factory.”
What President Tanaka found was the duAro collaborative type dual-arm SCARA robot launched by Kawasaki in 2015.
“I heard that it is a robot that can be outside of a fence and coexist with humans, so I thought that it might be something that we could use.
The installation was only possible because of duAro.”
Introduction effects/solutions:
Preventing human errors that occur because work is simple and repetitive
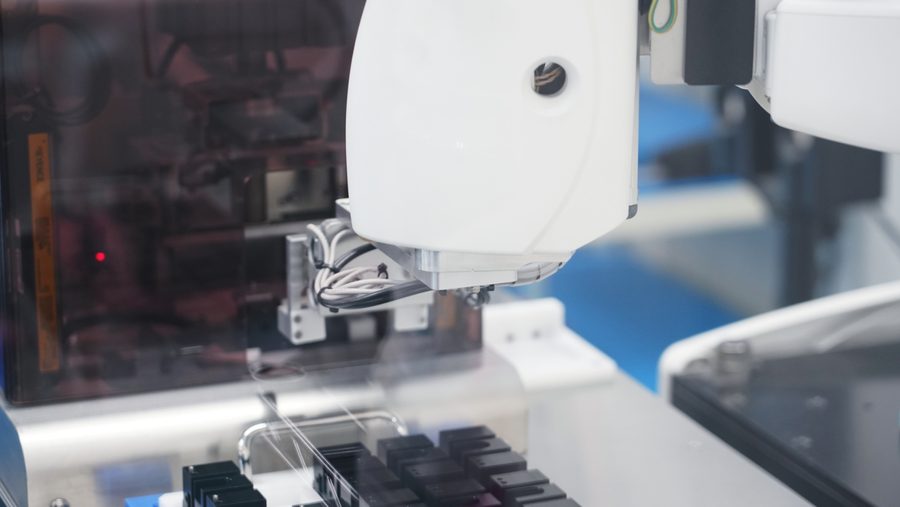
Tanaka Iron Works collaborated with the system integrators (SIers) Nanbokusangyou Co., Ltd. and KSS Co., Ltd. and constructed a system that fully automates the process that press-fits two parallel pins into the blocks.
At Tanaka Iron Works, duAro performs the assembly work for critical components used in Sysmex products.
Specifically, the work is to press fit two parallel pins made of stainless steel into aluminum blocks about the length of the back of a human hand.
President Tanaka explains that, “In recent years, the production (for this components) has been increasing more and more.
The production used to be 2,000 per month, but it increased to 5,000 per month three years later.
When making 5,000, the pin press-fitting requires 10,000 points.” The pins have a correct up/down orientation and must be inserted in the correct direction, at the correct pressure, and to the correct depth. It seems to be simple, but requires skilled techniques. In addition, it is monotonous, repetitive work, so it is also a process where human errors can easily occur.
“If we prioritize speed, then people are faster at inserting them.
However, it was not speed we required, it was precise and reliable work,”
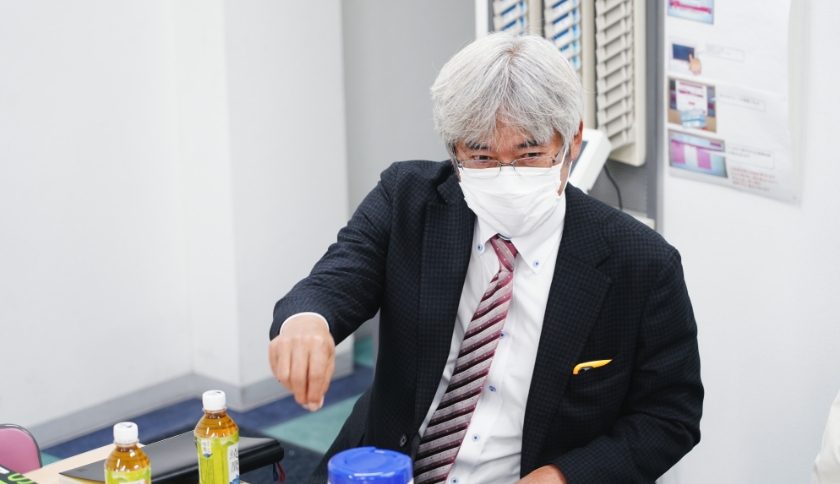
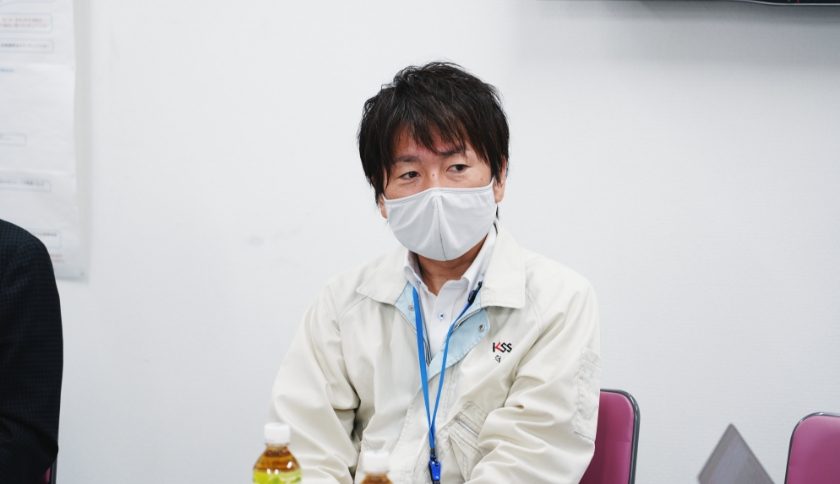
The first idea was for a simple system where a human worker places the pins in a line and the duAro picks them up and inserts them into the blocks.
President Tanaka examined that idea and had doubts because, there was “more preparation work by people than originally thought.”
In response to this, he consulted Yasuhiko Hashimoto, then General Manager of the Robot Division, PrecisionMachiner and Robot Company
(currently President of Kawasaki Heavy Industries, Ltd.). The response was quite clear.
“Please make the robot work harder.”
They completed a pin press-fitting robot system that combined the seven elements of (1) a supply unit to set the pins in the correct orientation, (2) a surface area sensor to double check that the orientation of the pins is correct, (3) duAro to set the blocks and pins on jigs, (4) a press-fitting unit, (5) a load cell to measure the press force, (6) a contact type sensor to measure the height to check that the pin has been inserted to the correct depth, and (7) a system to store the inspection records for all products.
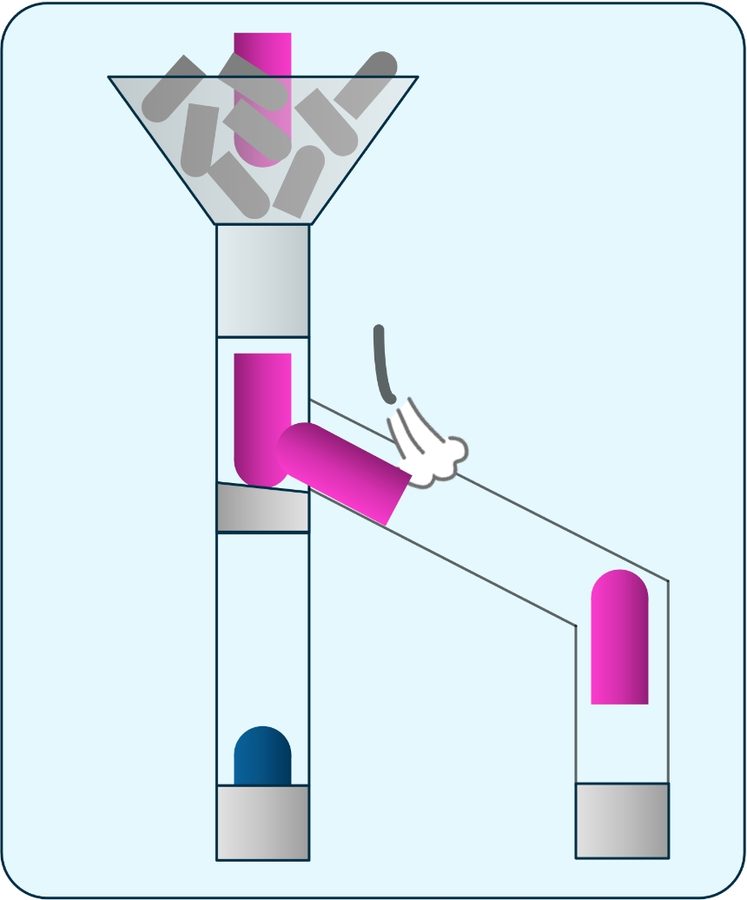
Supply unit devised to set the parallel pins in the correct orientation.
This was realized with a trick: When a pin comes down from the receptacle in the correct orientation, then it goes along the main route. If it comes upside down, it is directed to a sub-route where there is a mechanism to change its orientation.
This mechanism for (1) is particularly unique.
It uses a unique idea to sort the pin orientations with a simple mechanism.
Dai Morita from KSS explains that, “When we thought about the cost effectiveness, we chose the simplest format.”
The installation of vision sensors to recognize the pin orientation and the hole position would have required large-scale systems for the peripheral environment, such as shading equipment, and AI functions.
“This would have greatly increased the cost.
We therefore devised a mechanical supply unit to sort the pins without using vision sensors wherever possible.”
The supply unit has a mechanism that exploits the profile of the pins, where one end is rounded and the other end is flat.
First, pins that have been placed in a receptacle shaped like a funnel go down into the tube one at a time.
There is a dividing plate placed at an angle part-way along the tube. If the lower end of the pin that comes down is flat, then it will not tip over when it hits the dividing plate. The dividing plate opens and the pin goes straight down as it is to the discharge port and is set.
However, if the pin comes down upside down, the rounded end of the pin hits the dividing plate and the pin falls over. It then branches off to the side route as it is changing direction to the correct orientation. Air is used to send it off from there and then it is discharged.
In preparation for the small possibility where a pin with the wrong orientation may pass through, a double check mechanism is installed. A surface area checker reads the profile of the pin end and removes it if there is a doubt.
The failure rate by manual work was 0.05%. “However, through automation, we have been able to eliminate 100% of errors in pin orientation, pressure failures and insertion failures,” says President Tanaka.
In the five years since 2016, around 100,000 pieces have gone through the manufacturing process, but there have been zero defects.
President Tanaka says that more than anything else, it is significant that having duAro take on the simple work tasks makes is possible for the employees to engage in the more sophisticated and skillful work.
The business creed of Tanaka Iron Works is “A company is its people.”
duAro helps the company put that principle into practice.
Future prospects and plans:
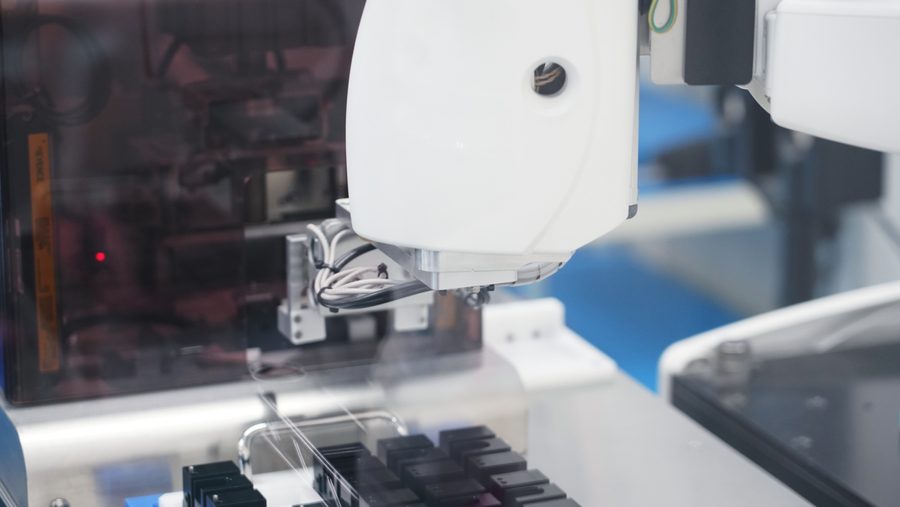
Incidentally, some of the components used in duAro are from Tanaka Iron Works.
President Tanaka looks back and says that the existence of the SIers was essential for the realization of the automation of the pin press-fitting work.
“A lot of the specialist terminology related to robotics is impossible to understand unless it is explained in a way that even we can understand.
The SIers are something like an interpretor, connecting the company installing the robots and the robot manufacturer.
If you have somebody to be a bridge like that, then I think that there are still a lot of opportunities for robots to spread in small factories.”
Right next to a technician who is concentrating on the delicate work at hand, the duAro is today again quietly working monotonously on the pin press-fitting work.
President Tanaka wants to expand the sites of utilization even further, and says,
“We ought to be able to use duAro to automate the processes before and after the pin press-fitting work too. For example, the block masking processing and the inspections of components before shipping.” Furthermore, there is also now a possibility of introducing duAro for lens assembly work.
Such planning has already begun.
― Company information Company name: Tanaka Iron Works Co., Ltd. Representative: President and Representative Director Yoshinobu Tanaka Established: June 1938 Capital: 12 million yen Core business: Precision machining of items such as industrial robot components and medical device related components Employees: 40 Place of business: Headquarters: 2-2-3 Ekimaedori, Hyogo-ku, Kobe-City, Hyogo Website: http://www.tanaka-iron.com/index.html ― Robots installed Model duAro1: the first dual-arm SCARA robot with a collaborative concept Features: Compact space, simple teaching, easy installation, high level safety Max. payload: 2 kg on each arm (4 kg with two arms) Axes: 4 axes on each arm Positional repeatability: ±0.05mm