概要
1997年3月、カワサキモータースマニュファクチュアリング株式会社(KMM)は、カワサキバルカン800モーターサイクルの
フレームサイドの溶接にカワサキJシリーズロボットを導入しました。22年後、この信頼性の高いロボットはKMMの施設で稼働し続け、より需要の高い製品のために、さまざまな部品を溶接しています。
このロボットの稼働時間は38,390時間で、20年分の8時間シフトに相当する。メンテナンスの記録は57回のみで、2つの異なる溶接ラインで働くことで柔軟性を示しました。
ROI
資本設備は大きな買い物であるため、当然ながら投資収益率(ROI)は最重要事項です。ロボット・アプリケーションのコストと要件はそれぞれ異なるが、この例ではKMM社の投資はすぐに回収され、将来にわたって大きな節約につながりました。
「KMMのチーフ・エンジニア、スコット・ゴードン氏は言う。「ロボットは90年代、2年足らずで元が取れたので、この22年間は基本的にタダで使っています。頻繁に買い換える必要がないのは、資本的支出予算にとって本当に助かります。」と。
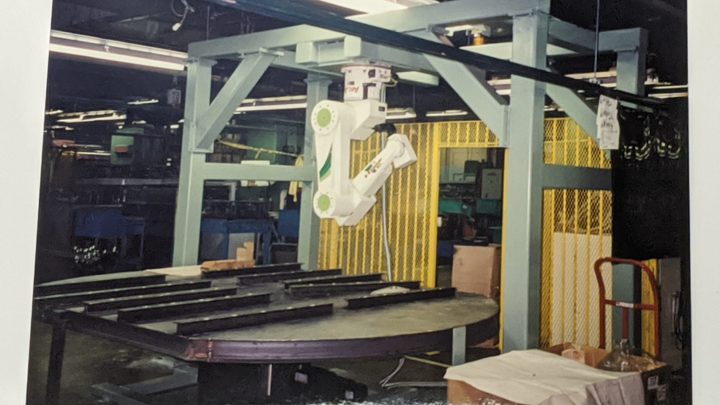
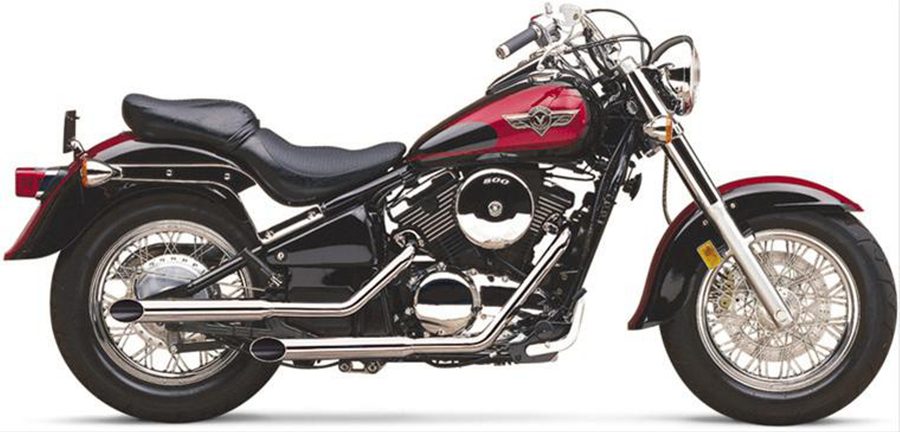
1997年、KMMはカワサキ・バルカン800オートバイのフレーム側面の溶接にJシリーズロボットを導入しました。
柔軟性
2004年に、KMMがバルカン800モーターサイクルの製造を中止したとき、ロボットを再プログラムして、人気が急上昇していた製品のステアリングシャフトを溶接することができました。ATVです。年間6万台ものATVを生産していましたが、そのすべてにステアリングシャフトが付いていました。導入当初は非常に忙しいロボットでした。
メーカーは、刻々と変化する市場のニーズに俊敏に対応する必要があります。カワサキの信頼性の高いロボットは、AS言語を使って再プログラムすることができ、さまざまなアプリケーションに対応することができます。
安全第一
自動車を特別に生産する場合、溶接部に不整合やエラーがあると、安全でない製品になる可能性があります。このため、同社の工場ではロボット溶接が必須となっています。「新製品を開発する際には、品質の観点から、溶接をできる限り自動化するようにしています。」とゴードン氏。毎日、毎日、朝から夕方まで一貫して手溶接に頼ることはできません。
カワサキの最新鋭のBAシリーズとRシリーズの溶接ロボットは、熟練した溶接工が毎日最高の状態で行う溶接に匹敵する品質を備えています。各ロボットには溶接専用のソフトウェアが標準装備されており、プロセス経路を素早く簡単にプログラミングすることができます。アダプティブ溶接機能により、溶接中のロボットの位置、ウィーブパターン、速度を変更することができ、可変なハンドを埋めこむことができるため、どのサイクルでも高品質の溶接が可能です。
信頼性
労働力不足は、特に金属加工分野では、多くのメーカーにとって継続的な問題です。トレードメン・インターナショナル社によると、米国人溶接工の平均年齢は55歳で、これは米国人労働者の平均年齢より13歳高い。この職業に興味を持つ若年労働者はますます少なくなっており、この分野の労働力確保が困難になっています。
オートメーション化により、製造業者は人件費を削減し、労働力不足によるダウンタイムを最小限に抑えることができるため、需要に対応し、高品質の製品を提供することに集中することができます。
ロボットはひたすら走り、走り、走る。軋む車輪にはグリースが塗られるが、決して軋むことはなかった。
スコット・ゴードン、KMMチーフエンジニア
カワサキは、よくできた信頼性の高いロボットを製造することに誇りを持っています。しかし、その主張を耳にすることと、
それを直接目にすることは別のことです。カワサキのJシリーズロボットを24年間使い続けてきたKMMは、カワサキのロボットの品質を目の当たりにしてきました。Jシリーズロボットを活用することで、コスト削減、製品の品質向上、効率化、市場のニーズへの対応が可能になりました。ゴードン氏は、「ロボットは、ただひたすら走り続けました。」と言います。