現代に生きる私たちの身の回りには電子機器が溢れています。その心臓部ともいえるのが、プリント基板。スマートフォンやタブレットはもちろん、エアコンや冷蔵庫といった家電、コピー機やパソコンといったOA機器、街を行き交う自動車だっていつの間にか電子部品の塊になりました。いまやプリント基板無しには、物流も、製造も、日々の暮らしも成り立たないのです。
我々の生活に欠かすことのできないプリント基板の設計・製造において、国内外で屈指のシェアを有するリーディングカンパニーが株式会社メイコーです。今、川崎重工の自走式ロボット「TRanbo-7(トランボ セブン)」が、その製造現場で活躍しています。
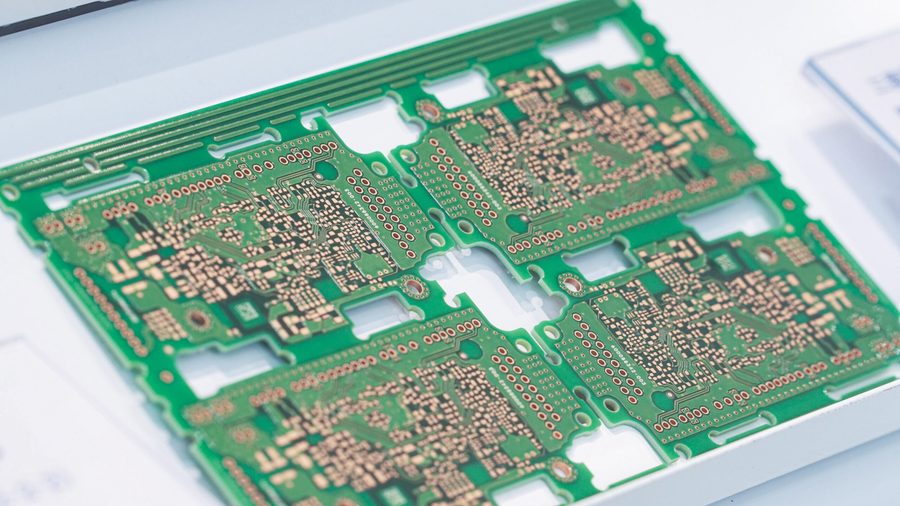
山形・天童に誕生した最新鋭の「エコスマートファクトリー」
株式会社メイコーの歴史は、十坪の小屋から始まりました。1974年、現社長・名屋祐一郎氏が自宅の庭にあった建屋を整備してパターンの設計とスルーホール基板(基板の穴に銅めっきを施し電気伝導性をもたせたもの)の製造をスタート。当初は基板穴明け加工のための工作機械もなく、穴あけはすべて手作業、めっきも外注先に出していたということです。
メイコー躍進のきっかけとなったのが、「スペースインベーダー」の大ブーム。株式会社タイトーが1978年に発売し、世界的な人気を獲得したシューティングゲームです。その後も、急速に需要が高まっていく車載基板の開発・製造へ迅速に着手。高度なデジタルデバイスに不可欠な高多層プリント基板など、時代のニーズに柔軟に合わせ、幅広い製品を展開してきました。
現在は、国内のみならず中国やベトナムにも生産拠点を置き、グループ全体で1万人超の従業員を擁するスケールの企業へ成長。彼らが完全自動化を見据えた最新鋭の拠点として2023年10月に竣工したのが、山形県の天童工場です。
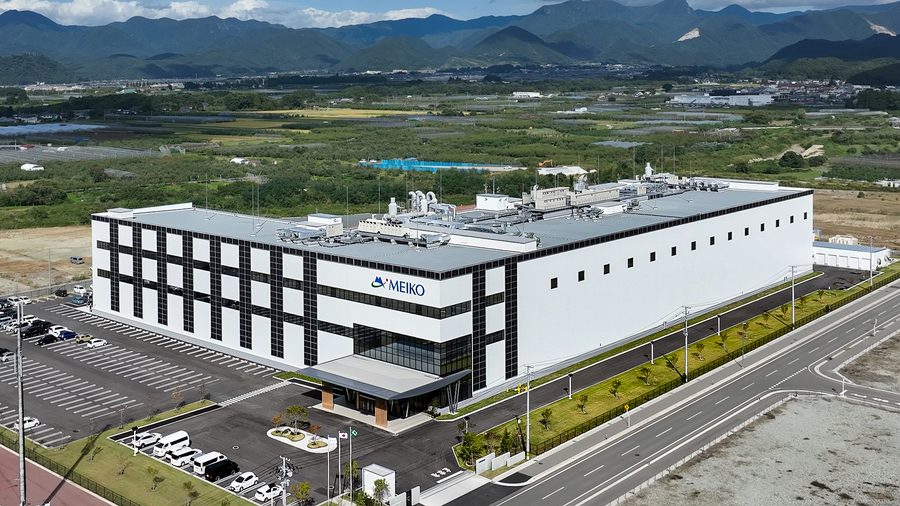
「エコスマートファクトリー」をコンセプトに掲げる天童工場は、現時点で90%以上の自動化を達成しています。6万5000平方メートルの敷地内に、延べ床約2.5万平方メートルの生産エリアを整備。ADAS(先進安全運転支援システム)向けなどに対応する最新のビルドアップ基板や貫通多層板などの量産を行なう、車載基盤のマザー工場として稼働しています。
川崎重工とメイコーの知見を融合して次世代型の自走式ロボットを開発
多数の部品を実装できる多層板には、スルーホールと呼ばれる貫通穴が必要です。この穴あけ加工は基板製造の初めの工程にあたるため、ここでの品質が後工程に大きな影響を及ぼします。つまり、非常に繊細な精度が求められるのです。
基板づくりの最初の最重要関門ともいえる基板穴明けドリルマシンを使った穴あけ工程ラインで、いま活躍しているのが川崎重工とメイコーで共同開発した「Drinbo」です。
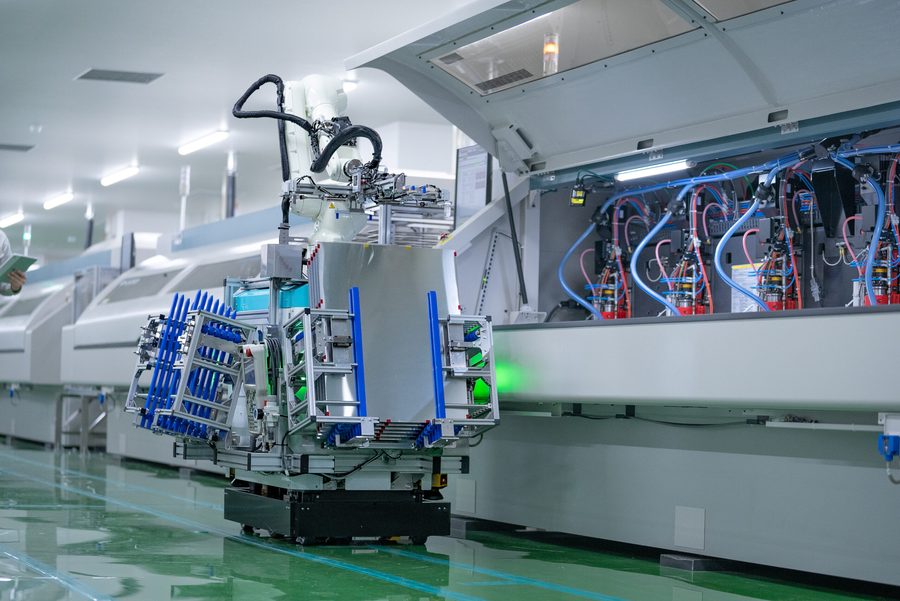
「当社は業界のリーディングカンパニーとして色々な取り組みをして参りました。今回Drinboを導入したのは『基板穴明け工程』と呼ばれるところで、プリント配線板に穴を空ける工程になっています。この作業に関しては、世の中に自動化の設備はあったのですが、非常に高価で業界内でもあまり広がっていないような状況でした」
そう語った天童工場の豊島 智仁工場長は、最新鋭のエコスマートファクトリーとして誕生した天童工場で、基板穴明け工程をいかに自動化するかということは大きなミッションだった、と振り返ります。穴あけ加工自体は基板穴明けドリルマシンが自動で行なうのですが、そこまでワークを運び、加工後にワークを取り出す作業は、自動化を積極的に進める彼らでも、前述の理由により人手に頼ってきました。
90%の自動化を、100%にするための一歩として、メイコーが選んだのが川崎重工の「TRanbo-7(トランボ セブン)」でした。小型の垂直多関節ロボットとスリムな筐体、そして自走式システムを組み合わせた「TRanbo-7」は、装置への加工品や部品のセット作業(ロード/アンロード)、保管棚からの部品のピッキングなどに適用できる次世代産業ロボットとして開発されたもの。
この「TRanbo-7」をベースに、FA機器開発も行なうメイコーの知見を組み合わせることで、天童工場の基板穴明け工程自動化を推進する新たなオートメーションシステムが完成しました。それが「Drinbo(ドリンボ)」です。システム開発の責任者である天童工場 工場管理室の新澤 要室長は説明します。
「今回Drinboを導入したラインで扱う基板は多層板と呼ばれていて、中に何枚かの基板をサンドイッチする構造になっています。めっきで銅を析出させて導通を図るため、数枚の基板を重ねた上で穴を空ける必要があるのですが、空ける穴の位置に求められる精度は髪の毛一本分くらい。マシンに基板をセットするときにも、細かなガイドにピンをセットして、きっちりと固定してから操作を開始しなければいけません。従来も自動機は存在したのですが、加工機と同じくらいの値段がするためあまり普及していませんでした」
その繊細な作業を担うことになったのがDrinbo。そのベースとなったTRanbo-7を最初に見たときの印象を、新澤氏が振り返ります。
「まずは、スリムな形をしていて非常に使いやすそうだと思いました。工場内というのはスペースが限られておりますので、通路も狭い。そこを動き回ることができて、かつマテハンが上についている設備ということで、非常に使い勝手が良さそうだという印象を受けました」
1台の基板穴明けマシンにセットできるワークの数は6個。穴あけ加工時間は平均1時間半〜2時間ですが、完了時間は各マシンで異なるため、これまでは人が終わったマシンの元へそれぞれ足を運び、加工後のワークを回収して次のロットをセットしていました。
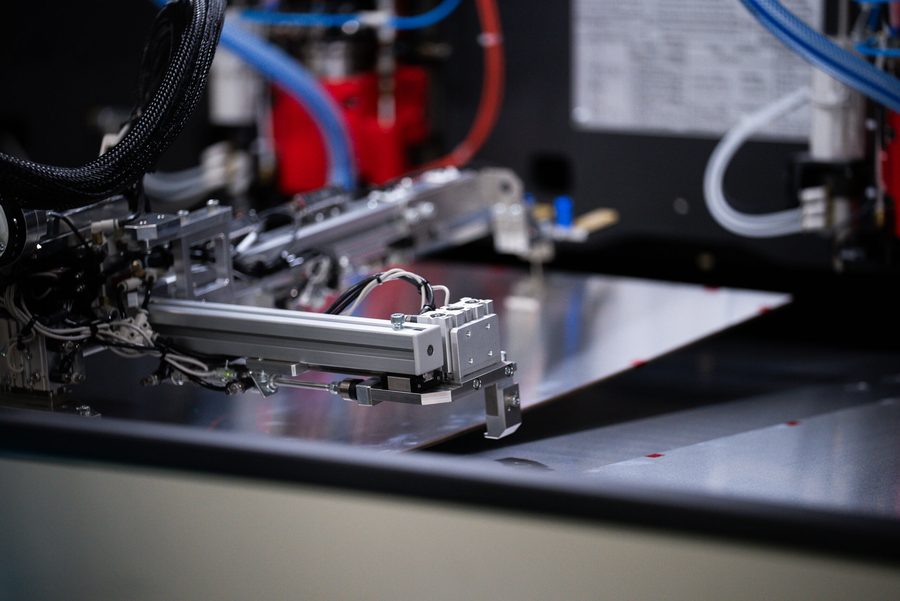
「穴あけ加工がいつ始まっていつ終わるのかは、それぞれのマシンで異なるため、どのマシンにワークを投入しにいけばいいのか、どのマシンからワークを取り出せばいいのかを探しにいくのは大変な作業です。それをデジタル化してDrinboに任せられれば、人は別の作業に当たることができます。ここ天童の工場に設置している基板穴明けマシンは9台ですが、海外だとその数が100台、200台超にのぼります。将来的には、そういった大規模工場での稼働も見据えています」(新澤氏)
繊細かつ複雑、かつ高い正確性が求められる作業を人に代わって行なうロボット、Drinboはよりシビアな生産効率が求められる海外のメガファクトリーでの活用も想定したうえで開発されました。また、生産性の向上に加えて、Drinboの適用は品質安定にも繋がると豊島工場長は付け加えます。
「ものづくりにおいて、品質を上げるためは『いかにばらつきを小さくするか』というのが一番の命題だと考えています。Drinboの導入は、人の作業を除くということ。人作業を除くということは、標準を守るということに繋がります。これによって、なるべくばらつきの小さい安定したものづくりが可能となり、品質の向上にも役立っていくのではないかと思っております」
ロボットに作業させるために「あいまい」を取り除く
Drinboの完成までには、紆余曲折のプロセスがありました。本稼働に至るまでに要した期間は1年半〜2年。果たしてどんな苦労があったのでしょうか。
「人がやっていた作業をロボットに任せるにあたって、一番苦労するのが『あいまい』を取り除く作業です。人の場合、あいまいな領域があっても何気なくカバーすることができます。しかし、ロボットだとそうはいきません。例えばそれぞれの工作機械やラック類などの配置も、機械で出し入れすることを考えると、ミリ単位でレイアウトしなければならないという事実に気がつきました」(新澤氏)
また、いままで人がなんとなくやっていた作業をひとつひとつ洗い出して、それをシステムに落とし込む際、やはり条件があいまいだった部分がかなり散見されたといいます。そういった設備や作業の「あいまい」を改めて認識できたのも、今回のDrinbo導入が生んだ副産物。新澤氏はそう語ります。
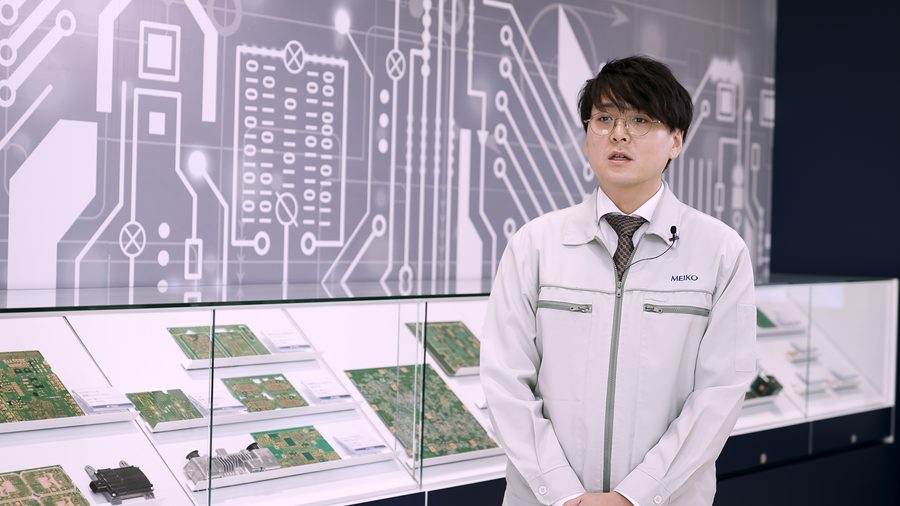
開発当初のコンセプトからプロトタイプ、そして最終完成形にいたるまで、ロボットの造形にも大きな変化がありました。
「最初はちょっとしたラックを積んで、それを牽引するようなタイプのものを検討していました。でも、そうすると現在の倍くらいのサイズになってしまい、工場内の狭い通路では回転できない、曲がれないという問題が生じました」(新澤氏)
ワークを運ぶためのラックを取り付けると、TRanbo-7のもつ美点であるスリムさが失われてしまう。その課題を解決するべく、メイコーと川崎重工の技術陣は試行錯誤を重ねました。新澤氏は説明します。
「これまでは品質上製品を縦に置く、ということをしてこなかったのですが、Drinboの形状をもっとスリムにしないと工場内を自由に動かすことができない。そこで、ボディのサイドに薄型のラックを装備して、そこに基板を縦に収納するという新しいやり方を検証して、それで量産を実現することができました」
Drinboのボディ側面に装備しているのは、加工前のワーク6枚、加工後のワーク6枚を格納できるラック。薄いスリットに、ワークを縦に1枚1枚しまい込める仕組みになっています。ホテルのロビーや銀行などで見かける新聞架をイメージしていただくとわかりやすいかもしれません。ワークの品質を保持するため、ロボットアームによるアンロード時に衝撃が加わらないよう、ハンドはもちろん、受け入れ側のラックの角度や構造も苦労して設計されました。
単なる生産工場ではなく「自動化のショールーム」へ
Drinboが現在行なっている作業の流れは次の通りです。
1.加工機ごとの作業情報が、メイコーが独自に開発した基幹システムからDrinboに送信される
2.司令塔からの指令を受けたTRnbo-7αが次ロットの仕掛品置き場へ移動
3.取り出す対象が適正なワークかどうかQRコードでチェック
4.ボディサイドのラックへワークを積載
5.指定された基板穴明けマシン前へ移動
6.該当マシンで加工完了した前ロットのワークを回収→次に加工するワークのセットを繰り返す
7.回収したワークを後工程へ搬送するためのラックへ格納
なお、Drinboは、レーザースキャナーにより人の接近を監視する安全機能を搭載。もちろん、多層基板の穴あけには非常に高い穴位置精度が求められるため、ワークのセットにはビジョンセンサや距離センサも活用しています。
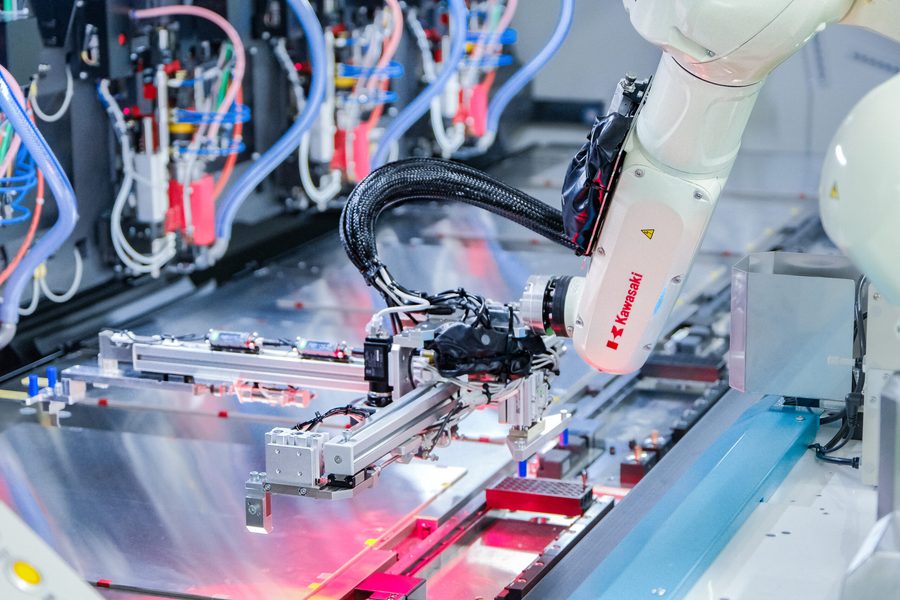
メイコーがもつFAのノウハウと、カワサキロボットのテクノロジーを融合することで、基板穴明け工程のワークのロード/アンロードを担っているDrinboですが、今後はさらなる“業務拡大”が期待されているようです。
「基板穴明けの工程にもまだ自動化できていないところがあります。例えば基板に穴をあけるためのドリルの出し入れです。今後は、各ドリルを収めたマガジンの交換も、是非自動化していきたいと考えています。また、特殊な製品が流れる際に、ラインの途中からワークを投入し、途中で取り出すということがあるのですが、そういう場合にもフレキシブルにDrinboで対応できていければと思っています」(新澤氏)
完全自動化を視野に、最新鋭の設備を積極的に適用するメイコー・天童工場。Drinboが活躍する同工場には、いち生産拠点としてだけでなく、もうひとつの重要な役割が与えられていると豊島工場長は言います。
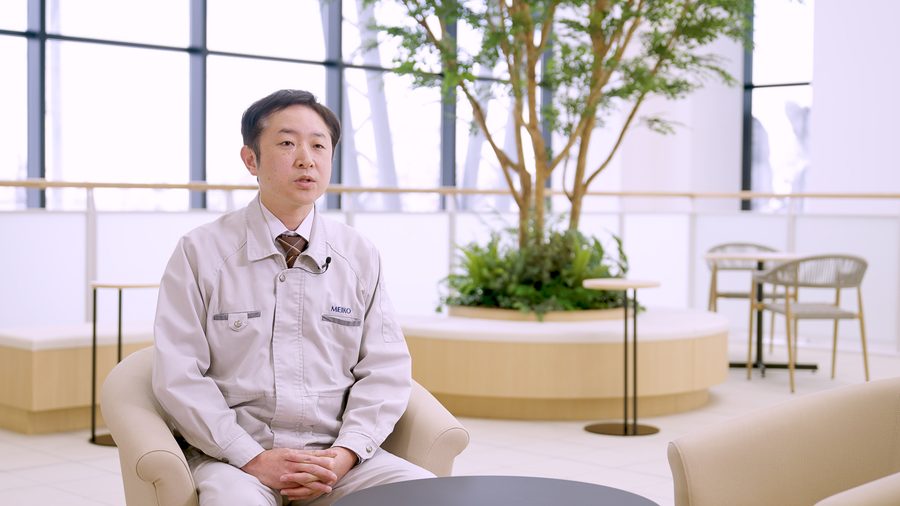
「Drinboを使用した自動化もそうなのですが、それ以外の工程についても、弊社独自のFA機器も活用しながら工場の自動化を進めていきたいと考えています。天童工場は、グループ内で先駆けて自動化を進めている工場ですので、同業者の方々を含めた色々な企業の皆様に見ていただきながら、新たな自動化の提案をする拠点となって欲しいですね。自動化のショールームのような工場、そんな存在にできたら嬉しいです」
(会社概要)
株式会社メイコー
事業内容:プリント基板等の設計、製造販売およびこれらの付随業務の電子関連事業
主要製品:両面・多層スルーホール基板、ビルドアップ基板、フレキシブル基板、フレックス・リジッド基板、大電流基板、放熱基板、部品内蔵基板、EMS、メタルマスク、メカトロ機器、映像機器、映像システム
本社:神奈川県綾瀬市大上5-14-15
設立:1975年11月25日
代表:代表取締役社長 名屋 佑一郎
売上高(連結):1,672億76百万円(2023年3月期)
従業員数(連結):12,337名(2023年3月末)