3/19 Pages
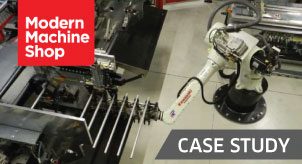
Kawasaki robots cut Ossenberg’s pipe processing times by over four minutes and boosted production volume to over 10,000 parts per day. Learn more about the cell in the latest edition of Modern Machine Shop…
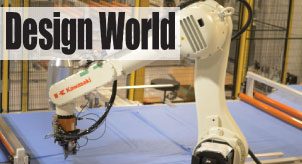
Learn how Harbour Technologies’ Kawasaki robotic PPE cell helped frontline workers during the COVID-19 pandemic in this feature from Design World magazine.
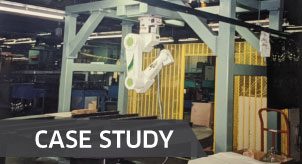
For more than two decades, Kawasaki Motors used their flexible Kawasaki robot to weld different motorcycles as their product line evolved.
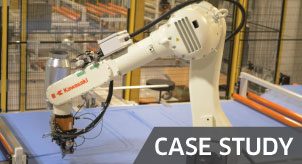
Mid-pandemic, Harbour Technologies pivoted their business model to manufacture PPE using a Kawasaki robot cell. Learn how this helped frontline workers, and allowed Harbour Technologies to expand their business.
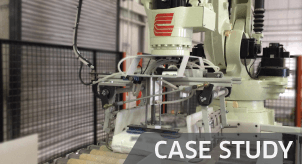
“This end-of-line solution that can palletize at least 20 bags per minute in factory temperatures of more than 100°F. The end user’s outdated machinery was causing frequent downtime, so Conveying Industries updated their line with a brand new Kawasaki CP180L robot…
(PDF:204.7K
)”
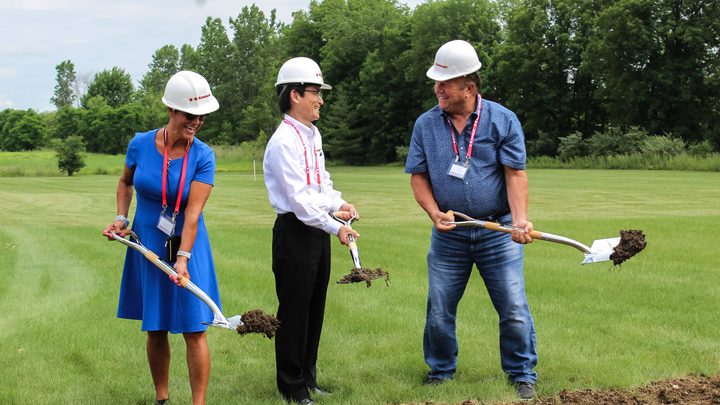
On June 28, 2021, Kawasaki Robotics (USA), Inc. broke ground on the new addition to their Wixom, MI facility, which serves as the company’s North American headquarters and Training Center. ..
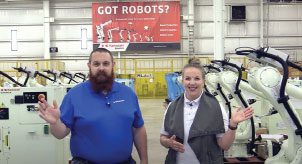
In this episode, you’ll learn how Kawasaki has optimized their general purpose robots since they first hit the market in the mid 1980s, and an overview of the newest addition to the lineup: the RS013N…
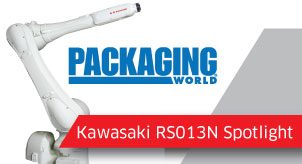
Check out the RS013N spotlight in Packaging World to learn what makes our newest robot an industry leader for small-to-medium payload robots…
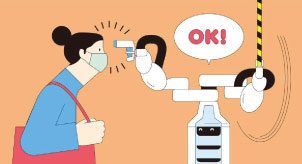
In the “new normal,” where virtual contact and social distancing are required, the number of workplaces where robots could play an active role is increasing…

Make no mistake about it. Kawasaki is robotics. But at the same time, we are not robots. Learn more…