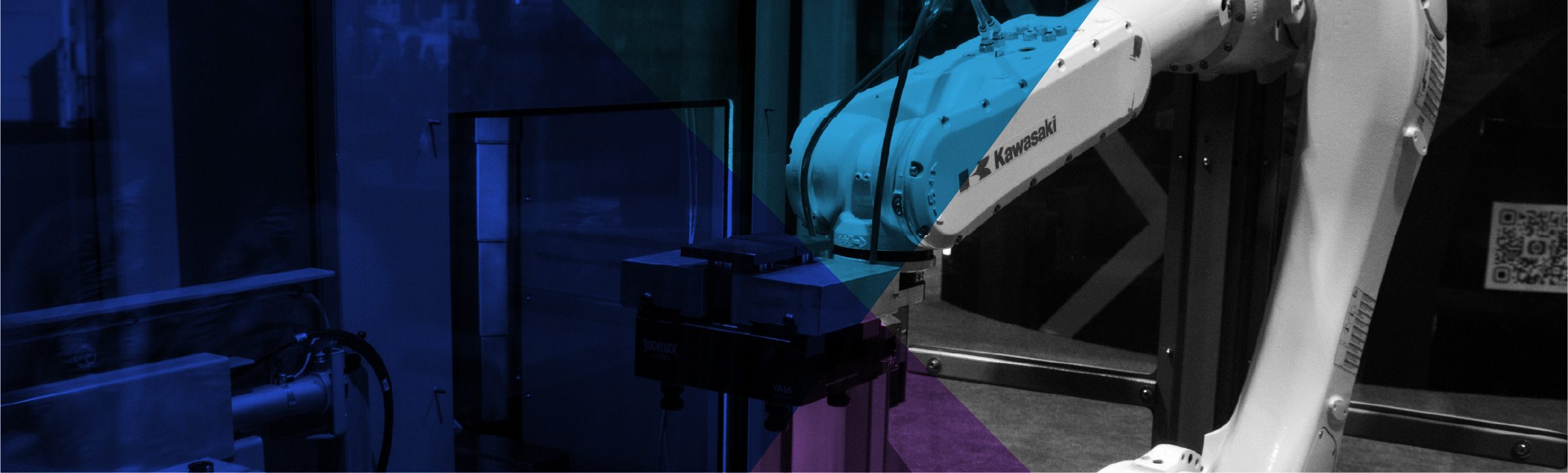
MACHINE TENDING
Robots
WHAT ARE MACHINE TENDING ROBOTS?
If you are constantly loading and unloading parts—and struggling If you have CNC machines on your shop floor and you’re struggling to find operators to work with them, chances are you’re already familiar with machine tending robots. But in case you’re not, these robots were built to do plenty of jobs that human operators do: part loading, part unloading, transferring finished parts to post-processing, material handling and more.
Robotic machine tending offers consistent benefits: increased productivity and reliability, cost savings over time, worker safety and worker comfort are some of the key benefits that can be expected with the right solution. On top of that, you get safer, more consistent machine operation, less idle time and the opportunity to put workers on higher value tasks.
If you have CNC machines, injection molding machines, press brakes, washers or any other type of machinery that can be automated, machine tending robots might be a perfect fit. We have a full range available to suit your needs, from lightweight collaborative robots to strong and capable industrial robots.
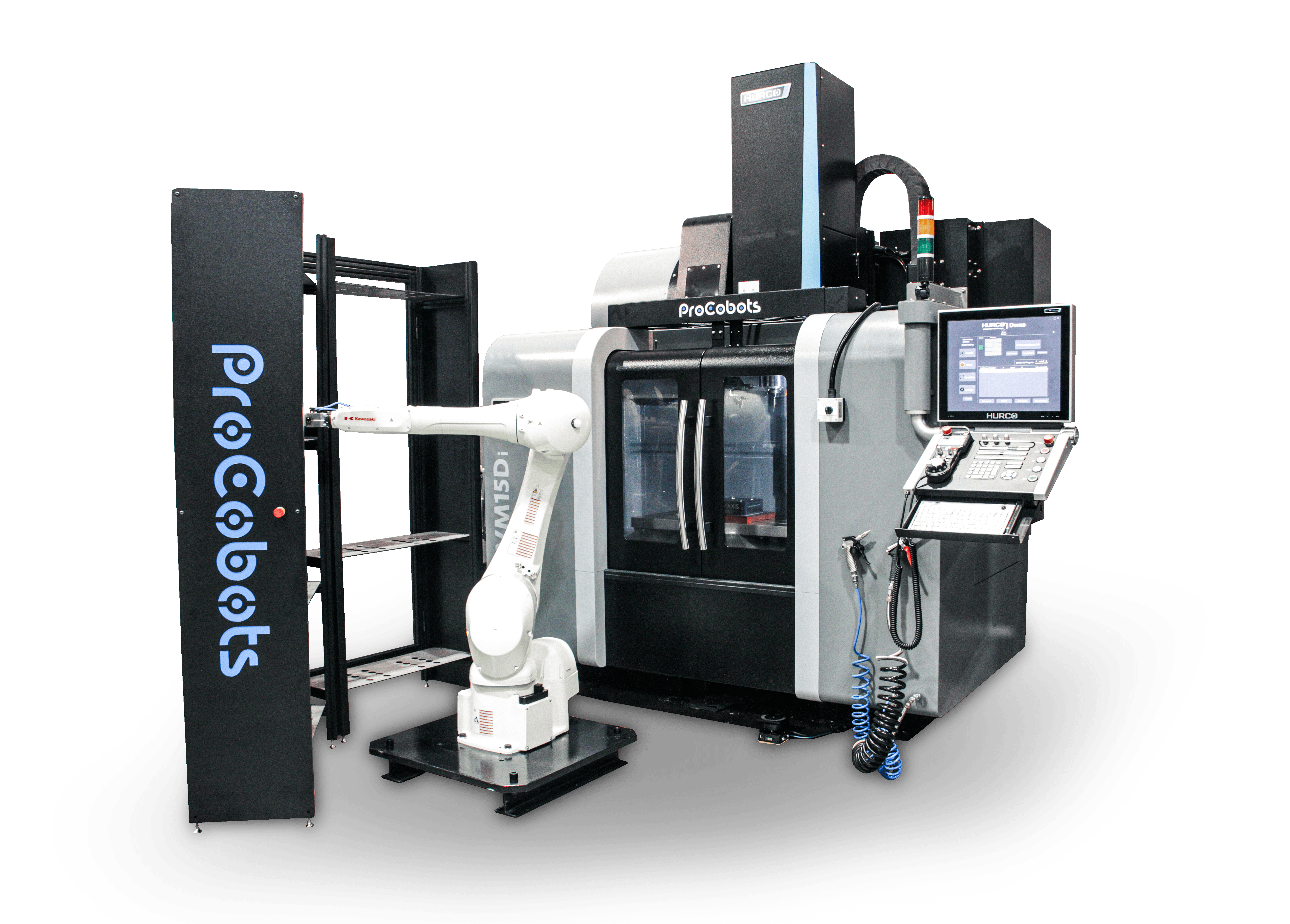
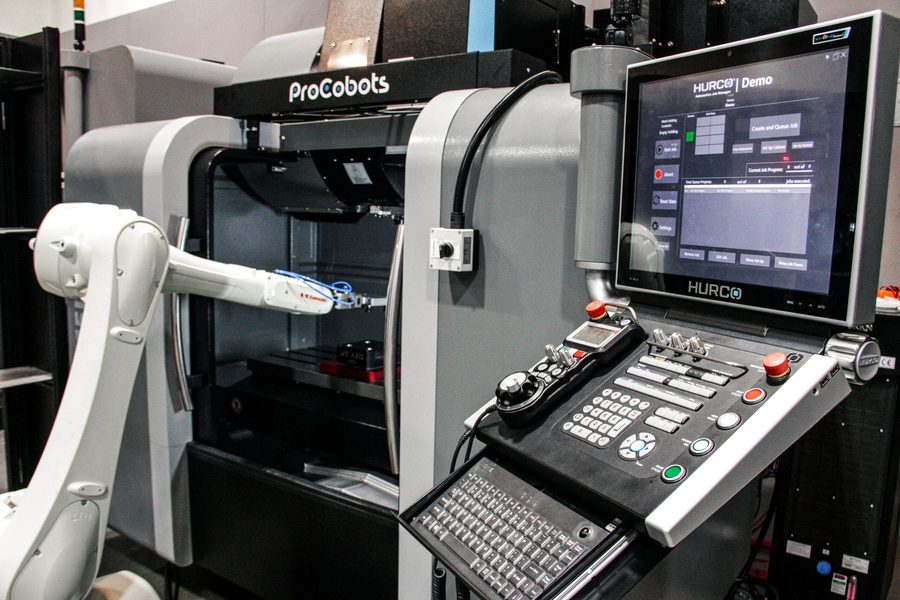
THE CHALLENGES OF MACHINE TENDING APPLICATIONS
CNC machine shops, sometimes known as job shops, often don’t know exactly what they’ll be working on a week or a month from now. They might be low mix, high volume., They might be high-mix, low-volume. Whatever the case, machine tending robots on machining centers, turning centers, multi-tasking machines or other machining and fabrication equipment need to make it easy to add a new application whenever a new job comes in.
To make it as easy as possible for operators—who might be new to automation or new to the industry—machine tending robots need to have a strong and easy to use interface.
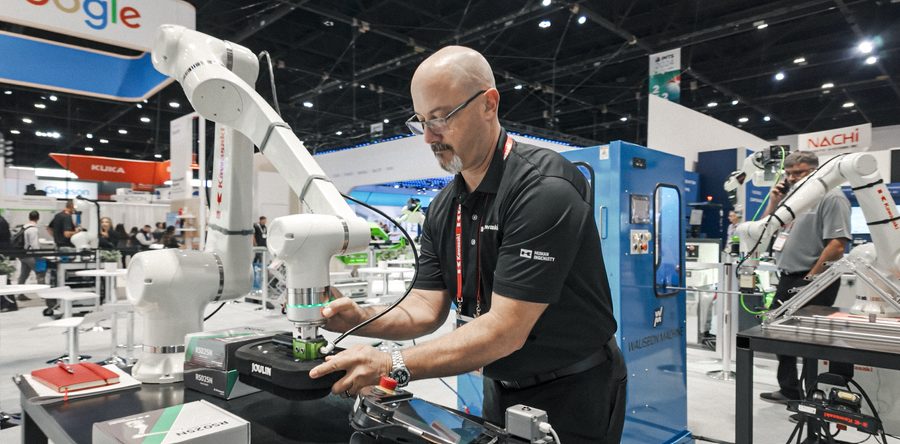
The Kawasaki Robotics Difference
Kawasaki Robotics makes world-class automated machine tending robots that you and your shop can count on for years. That said, if you’re evaluating strictly what the robots are capable of, it probably looks fairly similar to other options out there.
The major differences arrive when you factor in our open source programming and surprisingly human support.
We’ve always had a manufacturer-first mindset, because we’re a manufacturer ourselves. Our open source programming platform offers several types of programming languages for all skill levels, letting users easily scale from basic operations to AI integrations. This, combined with our exclusive online resources and tools, puts our customers and partners comfortably in the driver’s seat at all times.
And when you work with us, you won’t find hidden and costly surprises for added software capability, product manuals, training, remote service calls and more. We pick up the phone when you call, and we treat you the same whether you’re a large-scale enterprise or a small business. We speak plainly and we never mislead, always treating our customers and partners the way we would hope to be treated.
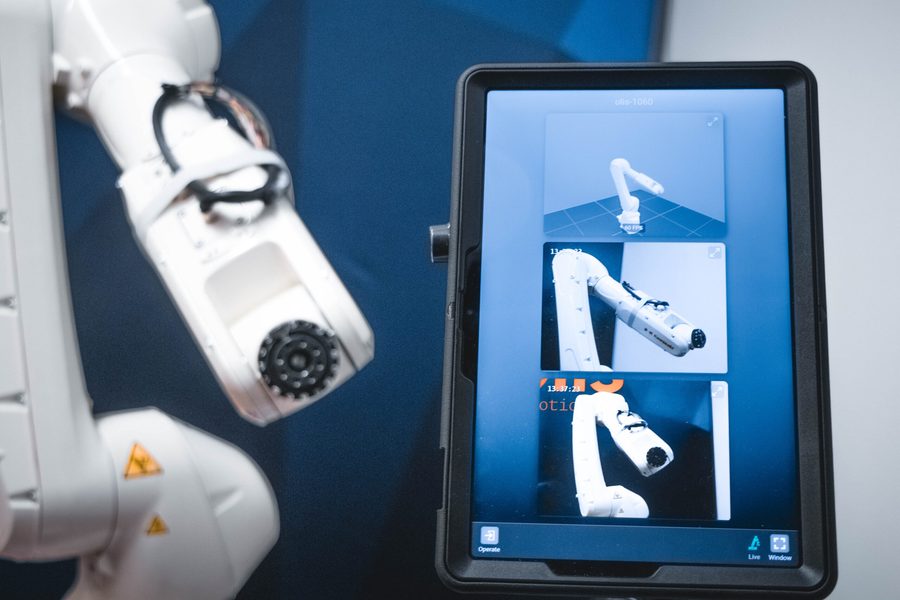
HOW WE DO ROBOTIC MACHINE TENDING DIFFERENTLY
Cycle time reduction is so critical in robotic machine tending because no value is being added to the product when tending a machine. This is why Kawasaki Robotics continually develops product to bring cycle time benefits.
- Our robot software allows for both automatic quick-change tooling and servo-controlled end-of-arm tooling
- Custom HMIs and custom operator safety solutions allow for operator interaction with the machine tending process
- Our robots can be programmed using simple Block Step style programming
- Or, for more logic-intensive work, the full Kawasaki AS programming language is yours
- We offer standard and custom machine tool automation interfaces—plus complete machine control and operator safety solutions
OUR MACHINE TENDING ROBOTS
(AND WHAT MAKES THEM SPECIAL)
Using open architecture and state-of-the-art technology, our line of palletizing robots are perfectly suited for end-of-line tasks. They bring high speeds and payload capacities that range from 80 kg to 700 kg, boosting efficiency and throughput.
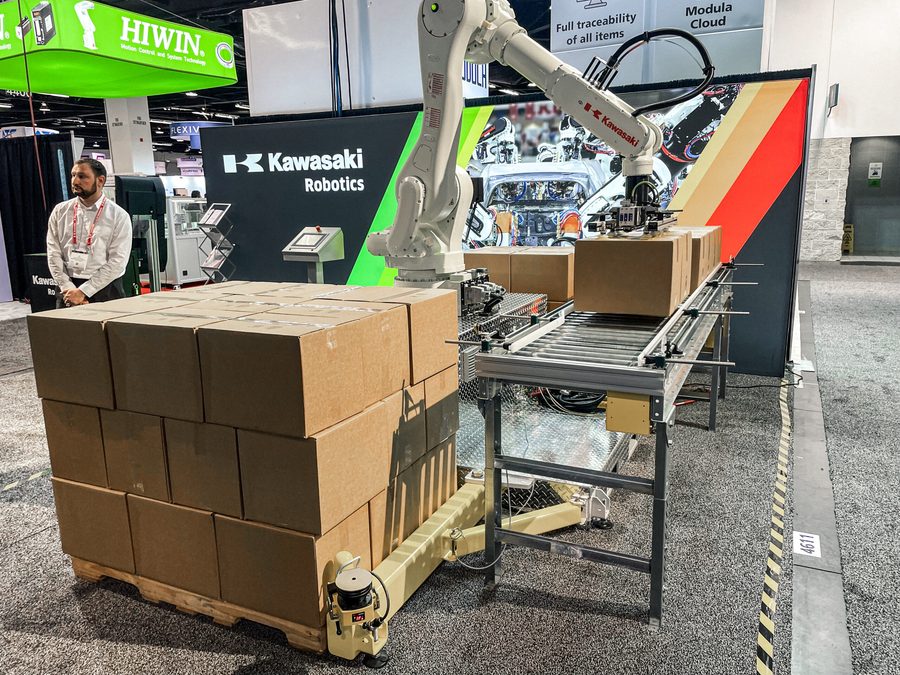
MACHINE TENDING AUTOMATION IS BETTER WITH KAWASAKI
Kawasaki Robotics hardware is proven and productive, and the open architecture of our software is not often seen elsewhere in the industry.
And on that note, we come to the icing on the cake: the people at Kawasaki. We try hard to be as flexible, open and easy to work with as our robots are. It’s simply the right way to do business.