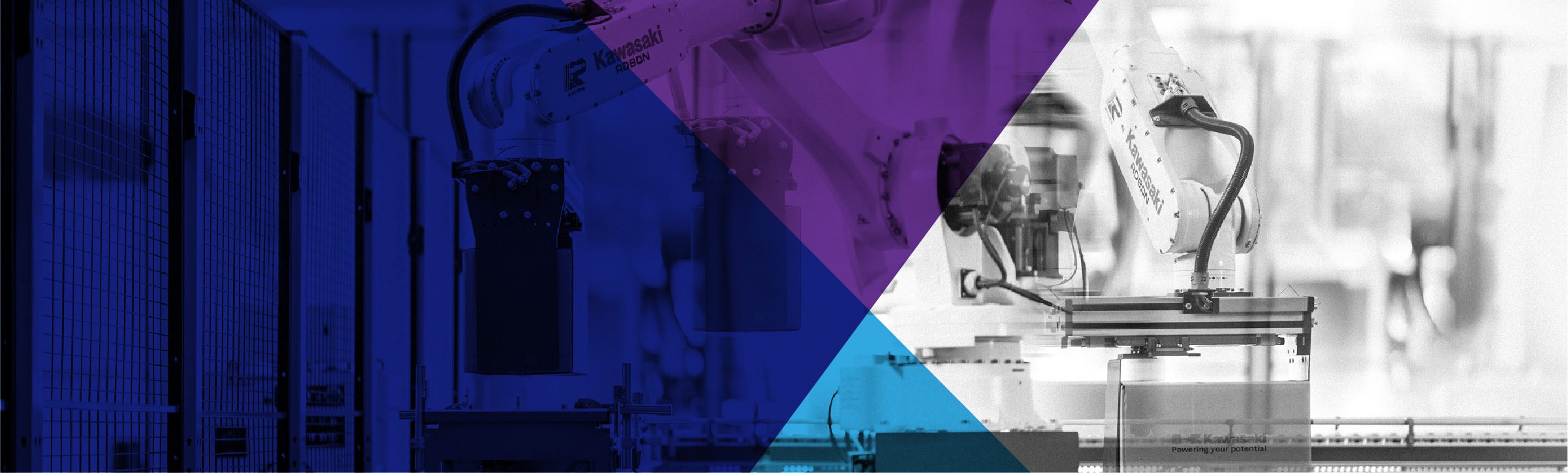
PALLETIZING
Robots
WHAT ARE PALLETIZING ROBOTS?
Chances are you know this answer already, so we’ll keep it short and sweet: palletizing robots use a strong and accurate arm to grab, position and place products into a tidy stack on top of a pallet. Often palletizing robots are deployed for end-of-line applications in industries such as food and beverage, retail, chemical, plastics, and pharmaceuticals.
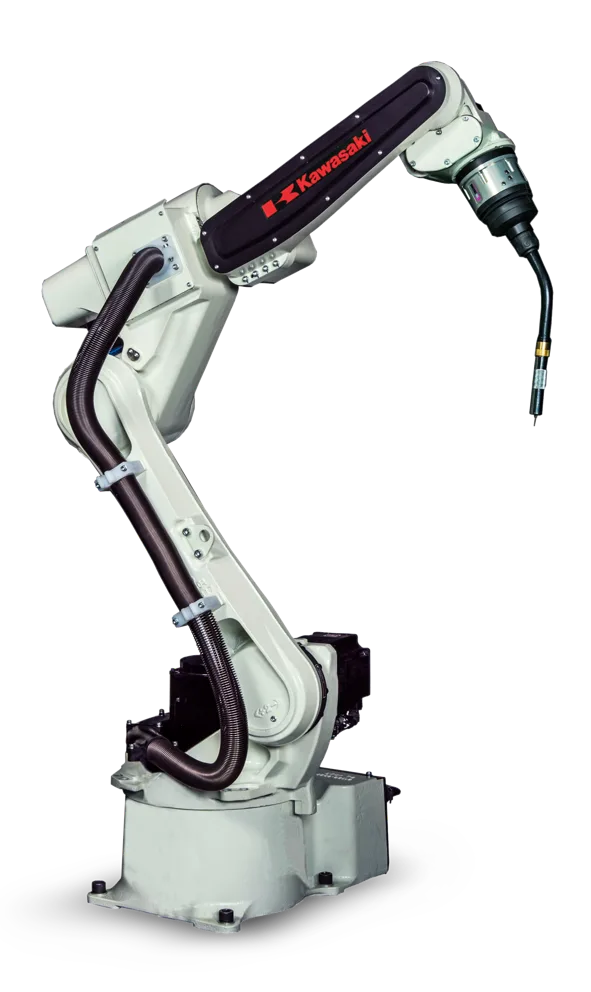
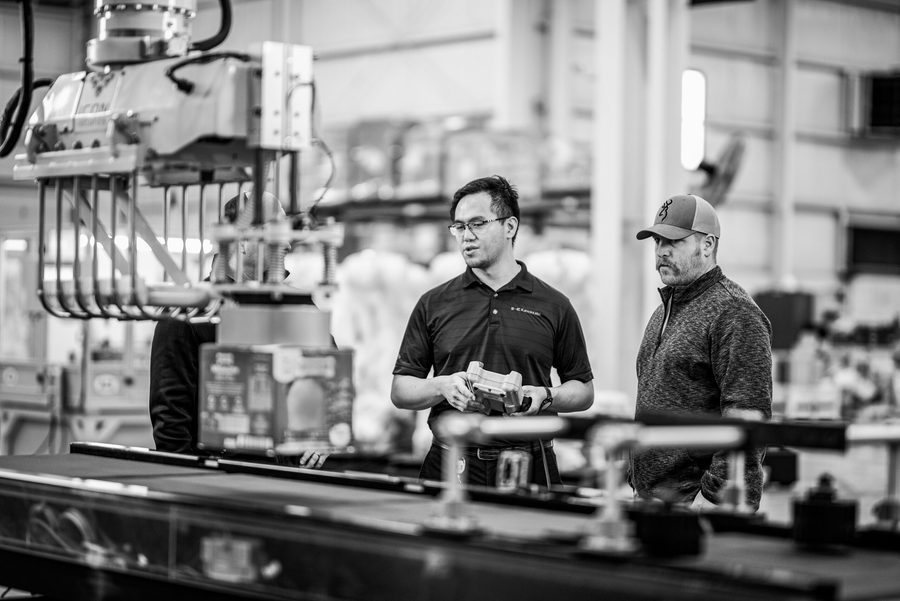
YOU CAN USE ROBOTS TO CONQUER PALLETIZING CHALLENGES
The first challenge you’re likely facing is not unique to palletizing: finding reliable skilled labor is difficult across just about every industry. Thankfully, palletizing robots fill in the gaps nicely. Their wide-ranging and hefty payload capacities free up existing staff to focus on other tasks, while taking on heavy lifting that humans aren’t equipped to do long-term.
However, the next big challenge is unique to palletizing: properly handling a wide range of SKUs, sizes and weights so cycle time can remain healthy. This requires pallet pattern and tooling flexibility, imperative qualities for a successful project.
On top of that, there are often a lot of different products that robots have to palletize. Boxes, bags, cases, bottles, cartons, pails, kegs and more. These objects might be varying sizes and weights, in poly bags, thin cardboard boxes or shrink wrapping. Kawasaki palletizing robots set themselves apart with speed and integration of any advanced peripheral equipment such as end-of-arm tooling, sensors, vision and more. More on that in a bit.
And finally, there’s still a perception that palletizing robots are difficult to learn and use. Many facilities feel they need an engineer or a high-level programmer to handle things.
But there’s good news: each one of these challenges is easily overcome with Kawasaki Robotics.
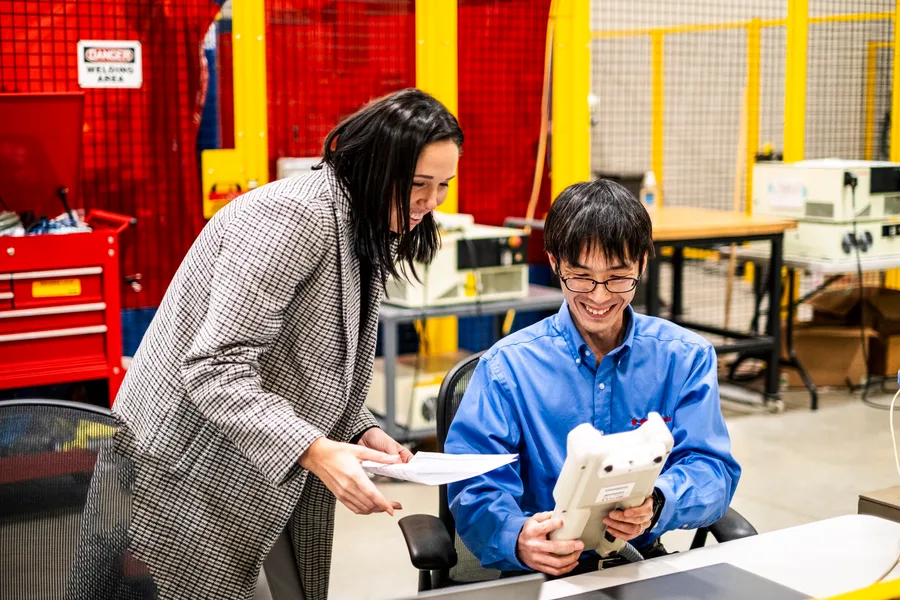
The Kawasaki Robotics Difference
Our industrial palletizing robots help to solve the skilled labor and seasonality issues, and they’re smart enough to make sorting decisions in milliseconds. What’s more, our open software architecture allows users to easily build interfaces without limitations. And most of our robot options are yours from the jump, we don’t charge you for add-ons.
Additional benefits of Kawasaki Palletizing robots:
- Our CP Series has a consistent form factor regardless of payload. No need to find additional floor space!
- Every time the CP Series decelerates, it generates energy. This energy is converted back to consumable power for the robot. This decreases power needed and reduces CO2 emissions.
So if you’re looking to solve your current palletizing problems, our advice is simple: find a partner you can trust who’s easy to work with and who won’t nickel and dime you. You might choose us, and you might go with someone else. But no matter your choice, don’t compromise or settle.
OUR PALLETIZING ROBOTS
and What Makes Them Special)
Using open architecture and state-of-the-art technology, our line of palletizing robots are perfectly suited for end-of-line tasks. They bring high speeds and payload capacities that range from 80 kg to 700 kg, boosting efficiency and throughput.
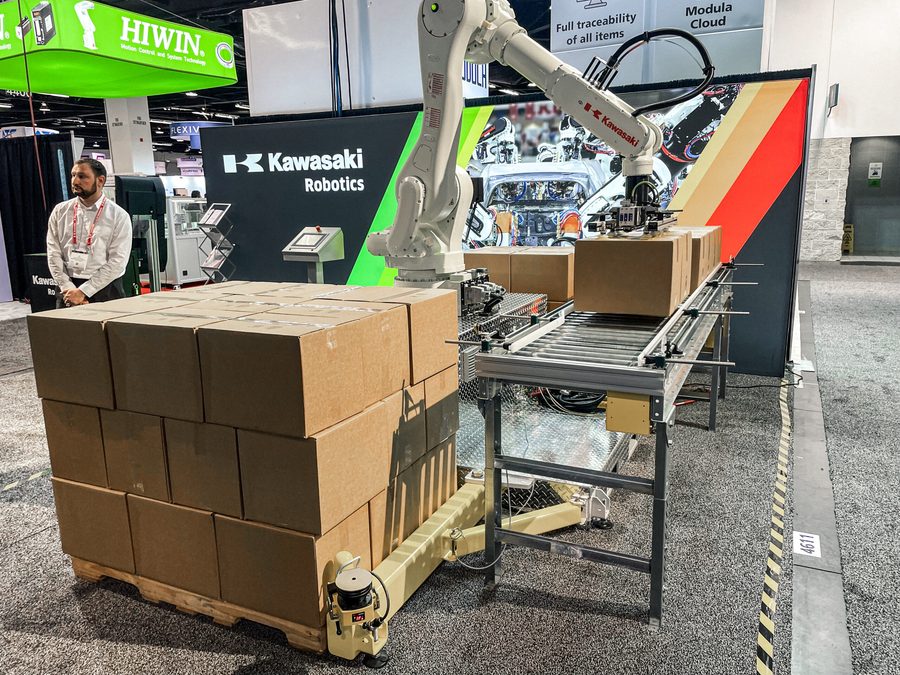
SOFTWARE & SERVICE SUPERLATIVES
Kawasaki Robotics hardware is proven and productive, and the open architecture of our software is not often seen elsewhere in the industry. We have the software suite and partners to handle various palletizing needs, customizing pallet recipes and patterns for a single product or multiple SKUs. We can create everything from interlocked to column patterns to mixed-SKU rainbow pallets and random SKU mixed pallets.
Our full stack of integration and technology partners let you leverage our software suite to provide everything you need—from simplistic to complex palletizing solutions that use AI.
And the icing on the cake: Kawasaki has inventory available. All in all, you get industry-best lead times on delivery, followed by complete freedom to develop exactly as you want to.