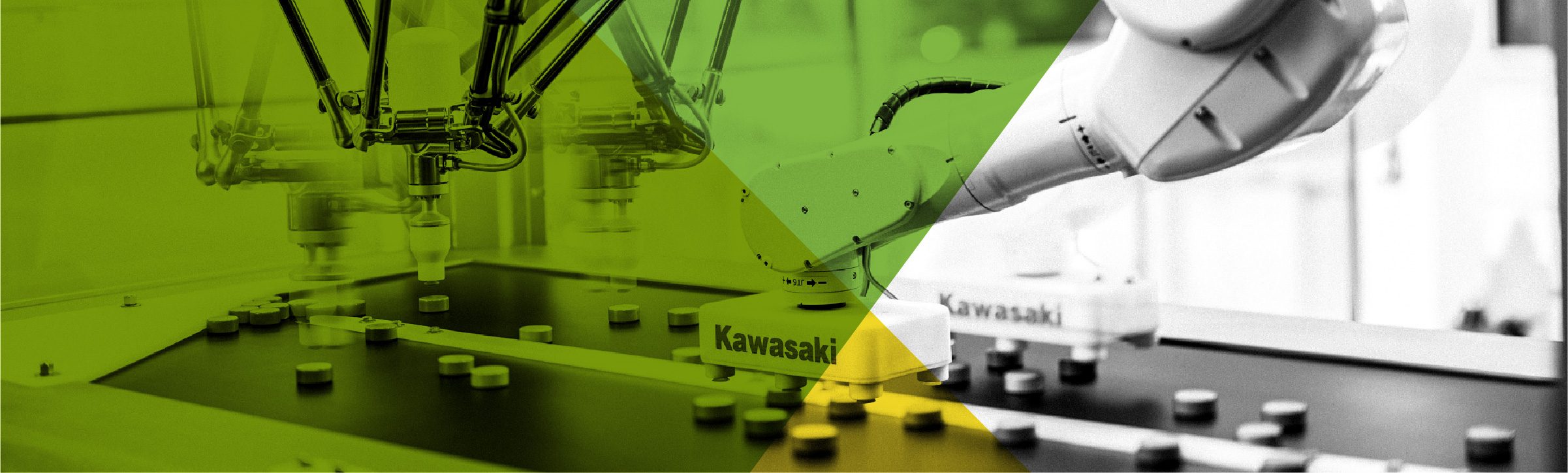
PICK & PLACE ROBOTS
Robots
WHAT ARE PICK & PLACE ROBOTS?
Widely used across industries such as food, pharmaceutical, cosmetics, electrical, electronics and machine parts, pick & place robots are known for their ability to pick and sort small objects that are moving quickly on a conveyor.
“Picking” is the process of grabbing and sorting small parts and food products floating on a conveyor belt at high speed. Doing it properly requires high-speed operations. The right pick & place robots can be used for diverse applications, including systems using multiple picking robots.
As customer and consumer demands for on-time delivery and fully-stocked shelves increases, the need for intelligent, reliable and long-lasting pick & place robots is going up in factories and warehouses all over the globe. Automating these long-manual jobs helps to increase the rates of production in an accelerated world.
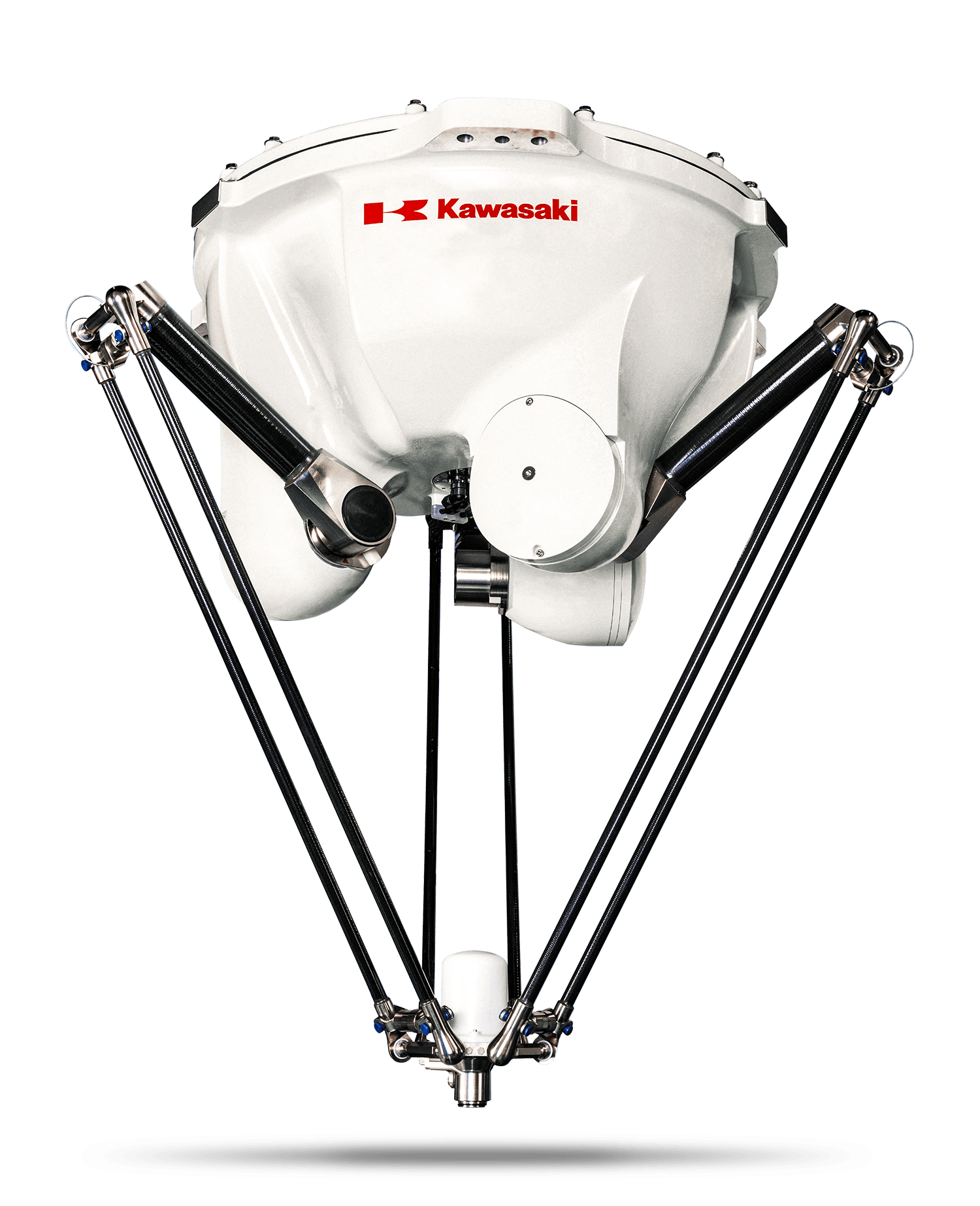
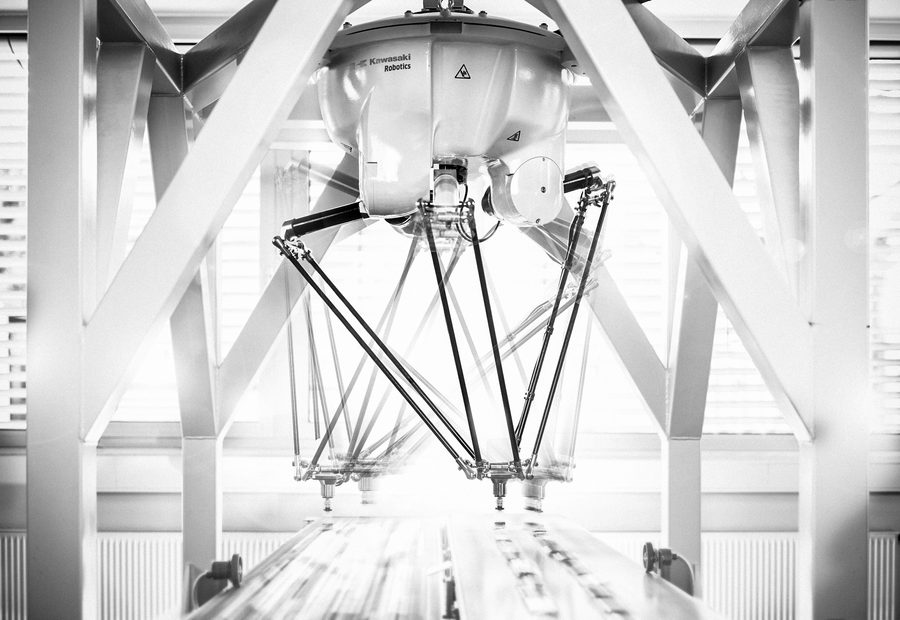
THE CHALLENGES OF PICK & PLACE APPLICATIONS
Conveyors filled with small parts or food products move quickly, and it can be difficult for some pick & place robots to keep up. If the objects are randomly arranged, shiny or reflective, that can make a robot’s job tricky as well.
The right robots need to pick precisely, place quickly and do the job again with remarkable repeatability. If they can’t keep up, time is lost, and lost revenue and customer frustration become real possibilities.
On the robot user side of things, there is still a perception that pick & place robots are difficult to learn and to use. The good news: these challenges are smoothly picked and placed with Kawasaki Robotics.
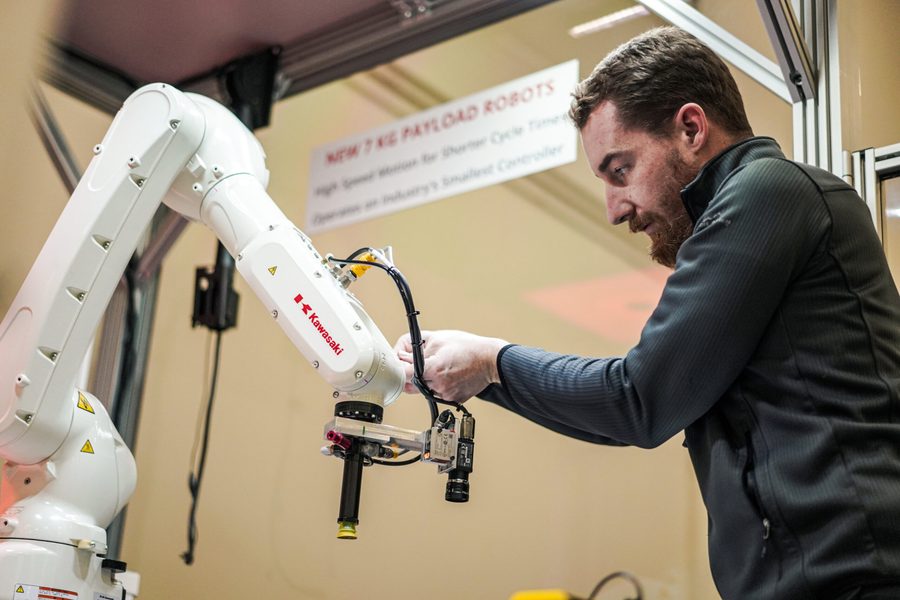
The Kawasaki Robotics Difference
If you’re wondering how Kawasaki pick & place robots stand out, it comes down to two things: speed and vision. In 0.2 seconds, our robots process an image and pick up the correct object.
The industrial pick & place robots at Kawasaki are high-speed, precise and reliable. They’re well-suited for a range of pick & place applications, including systems that use multiple picking robots.
On top of that, Kawasaki is famously technology-agnostic. Whether your solution needs a simple 2D camera or it needs to be a high-powered vision system, our robots work with your preferred vision partner. Our technology integrates with the latest and greatest vision solutions—many of which are powered by AI.
OUR PICK & PLACE ROBOTS
(AND WHAT MAKES THEM SPECIAL)
With an always-open architecture and high-end technology, Kawasaki pick & place robots were made to bring order to fast-moving product conveyance. Their high speeds, relentless work ethic and state-of-the-art vision make them an ideal fit for any pick & place application.
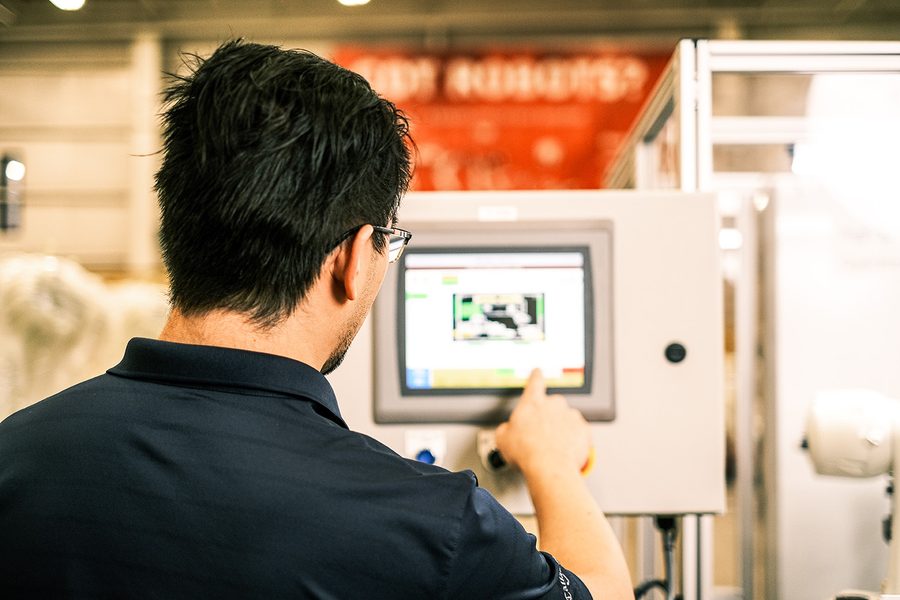
IT’S BETTER TO PARTNER WITH KAWASAKI
Kawasaki Robotics hardware is proven and productive, and the open architecture of our software is not often seen elsewhere in the industry. We have the software suite and partners to handle your specific robotics needs, with real-time control ability and a tech-agnostic stance that ensures you get the best possible solution.
Our full stack of integration and technology partners let you leverage our software suite to provide everything you need—from simplistic to complex solutions that use AI.
And on that note, we come to the icing on the cake: the people at Kawasaki. We try hard to be as flexible, open and easy to work with as our robots are. It’s better for all parties involved.
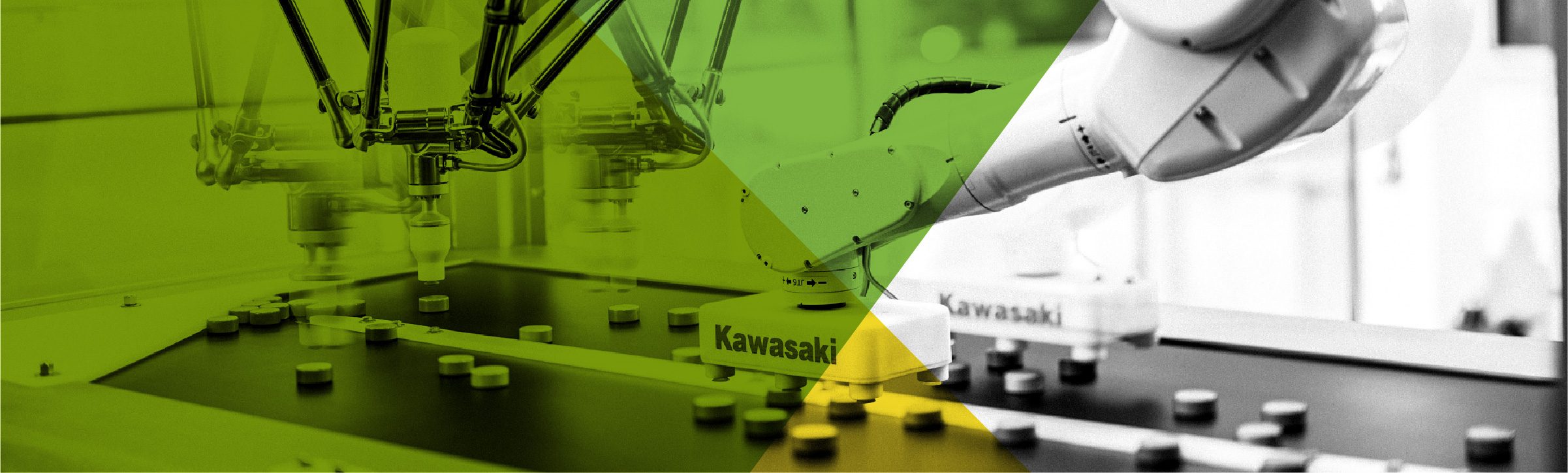
SUCCESS STORIES
Mask Manufacturing with Delta Robots
- Kawasaki Y series pick and place robots run 24 hours a day
- Production increased from 1.5 million masks to 9 million masks per month
- Labor reduced significantly