By Brandon Day, Senior Engineer Robotic Metal Fabrication
Robot integration in many welding applications makes sense, given that welding is not conducive to pleasant working conditions for humans. Not only is it a hot and dirty process, but it also emits unhealthy chemicals such as hexavalent chromium when welding stainless steels and other chromium-containing material. Although these health concerns might seem like enough reason to implement a robot, there are other considerations.
To ensure that robot automation is beneficial for an application, Kawasaki Robotics North America recommends evaluating these four questions for the best return on investment:
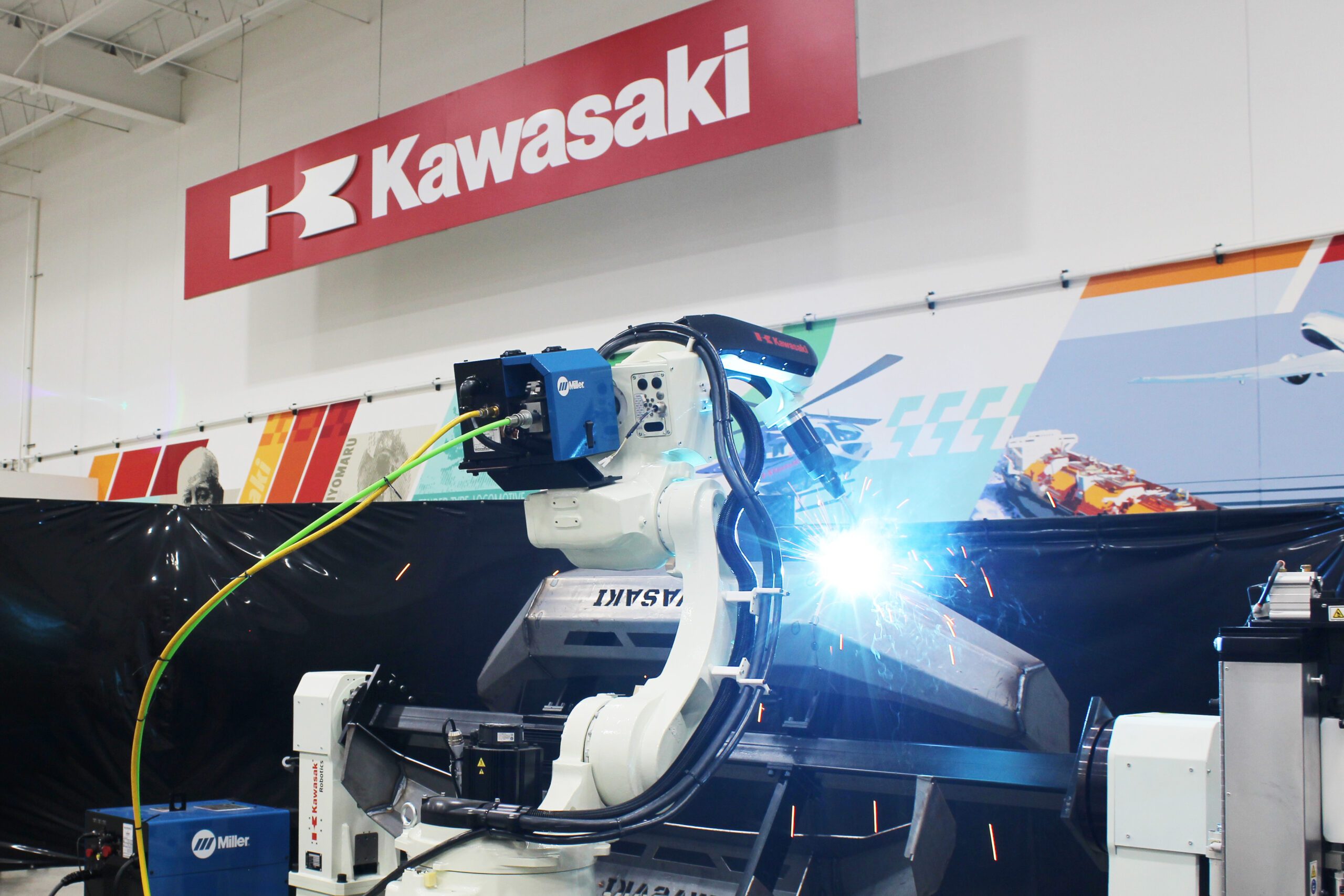
1. What is the part size?
Small parts that fit inside the welding cell are ideal for robot welding, but larger sized parts are possible.
2. How large is the volume size?
Best case scenario for robot welding is high volume (thousands of parts per day, hundreds of thousands per year). Also, consider whether the application includes volumes high enough to create the return that is necessary to pay off the machine in a respectable amount of time.
3. Are tolerances tight enough?
Tight tolerances on parts are necessary to provide accurate repeatability. The robot welds on the exact same spot every time; therefore, too much tolerance will cause the weld to miss often.
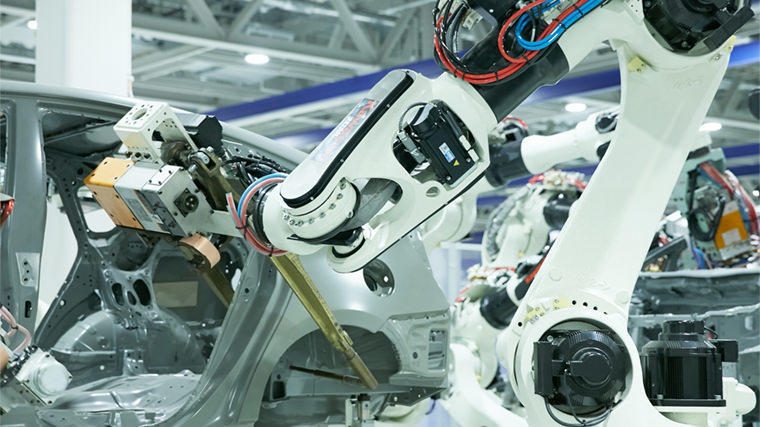
4. Is manpower an issue?
A worker shortage might demand robot integration in a welding application.
Although robots offer accuracy, repeatability and labor and cost savings, human welders are still a necessity. Their knowledge of the art – including the ins and outs such as torch angles, gasses, metrology, metallurgy – is required to properly program robots for these applications. Because every major manufacturer has its own welding specifications, it is key for every facility
that performs welding to have a specialist on staff who can interpret these different specs.
Robot Programming Made Easy
When robots are added to an application, instead of doing the welding themselves, welders can learn the job of programming the robots. Progressing into this higher skillset leads to not only a higher paying position where a welder is running multiple robot cells, but also a healthier work environment.
Kawasaki Robotics North America makes it easy for anyone with basic welding knowledge, including engineers, technicians and programmers, to learn robot welding programming quickly and thoroughly. The robot provider offers a three-and-a-half-day training course, “Arc Operations and Programming,” at its training center in Wixom, Michigan.
The class is designed for basic robot and arc welding operations, programming and safety training. It includes topics such as operating controls, selecting proper menus for programming, positioning the robot by use of pendant control, and program creation procedures and modification techniques. Upon course completion, students will know how to run the robot system in both manual and automatic modes, create a block step program using weld conditions, teach a path using weld and non-weld steps, and modify programs.