3/3 Pages
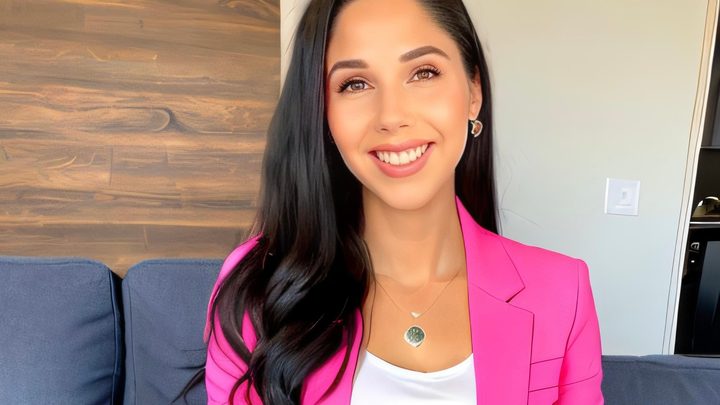
For many people who now have engineering careers, it was obvious from a young age what they would become. Brooke Mewton, Project Engineer, took a different route.
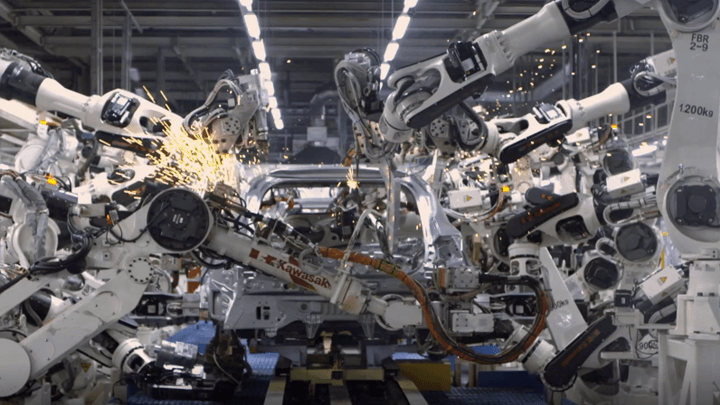
Learn how technology and robotic automation has affected the automotive industry over the last 30 years – from someone who’s experienced it all firsthand…
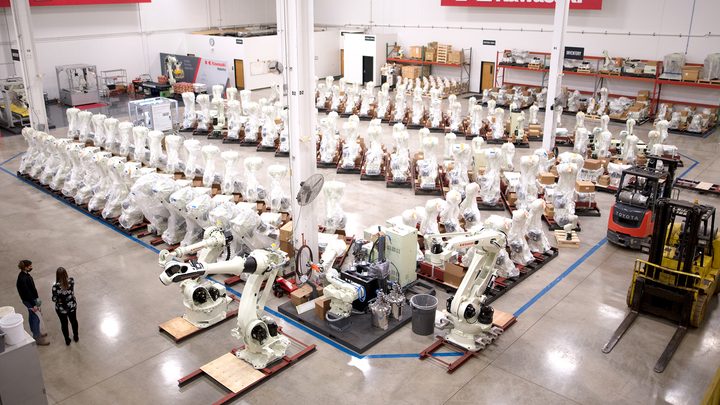
Should you spec on a single robot for your facility automation? Do the benefits of a single-source strategy outweigh the risks? While I am all for streamlining and simplifying, in this case I think companies can “standardize” themselves right into obsolescence.
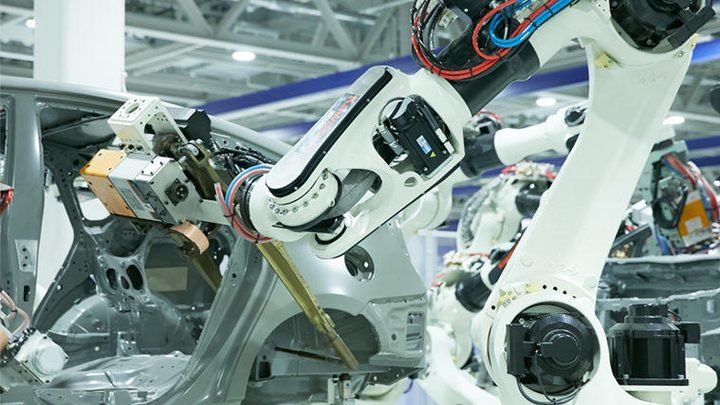
Ever wonder how a robot arm actually works?
When it comes to actually installing robots, even a slight knowledge of the structure and movement of industrial robot arms can go a long way toward a successful implementation. By knowing what’s going on inside the robot, you can better understand what the robot is capable of…
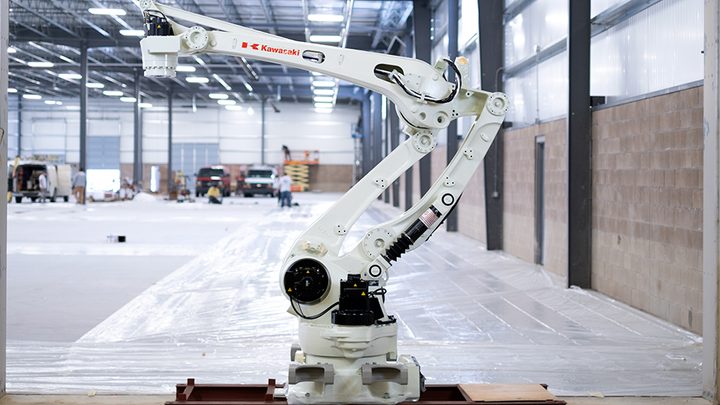
The automation industry is filled with myths. In all fairness, this isn’t so different than any other industry…
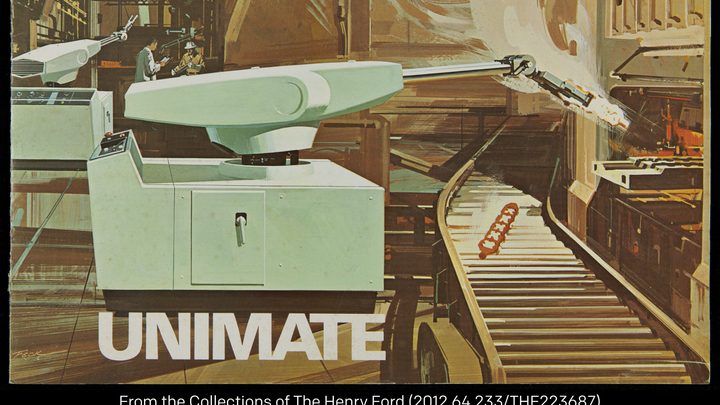
When Kawasaki manufactured the first domestic industrial robot in Japan in 1969, the automotive industry was the only field utilizing robotic automation. Now, you see vastly different types of industrial robotic arms used by companies from all industries, performing both complex and simple tasks. Let’s explore how the adoption of the Kawasaki-Unimate robot paved the way for the robots we see today.
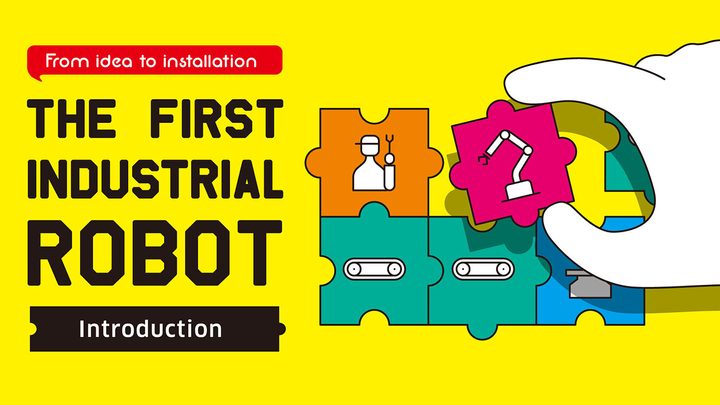
Industrial robots were born to perform laborious tasks for humans, including repetitive, dangerous processes and handling heavy objects, among others. Initially, robots were implemented for the automotive industry, but they have since expanded to others, including machinery and appliance manufacturing, agriculture, forestry, civil engineering, medical/pharmaceutical, food, and cosmetics industries — and more. Robots have proven to be particularly useful for lines with short product cycles, small-lot production of goods, and mixed-quantity production. As these needs are increasing, robots’ abilities are expanding. But when it comes to actually implementing a robot, a lot of questions arise. “What tasks can you leave to the robot?” “What steps do I need to take?” […]