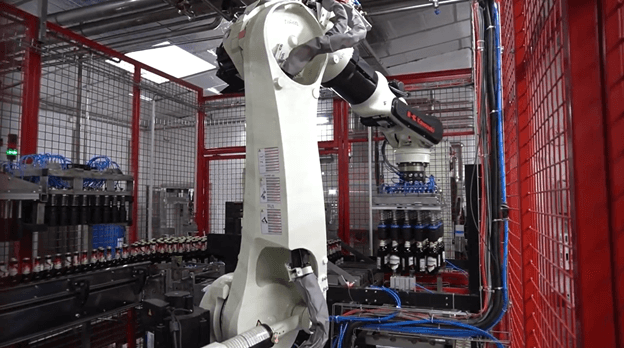
- IndustriesFood & Beverage
- ApplicationsMaterial Handling, Palletizing
- Robot SeriesBX/BT series, CP series
OVERVIEW
Westheimer Brewery has been brewing regional beer specialties for the German and international markets for more than 150 years. In order to assert themselves in a competitive market and stay productive despite labor shortages, the brewery decided to automate its entire bottle production line step by step. In 2017, Westheimer Brewery took the first step toward automation by installing a Kawasaki palletizer to replace outdated machinery. After seeing success with their first robot, they decided to add two additional Kawasaki robots, this time BX200L models. Now, they have automated their entire bottle production line – from managing empty bottles and filling them, to palletizing for distribution.
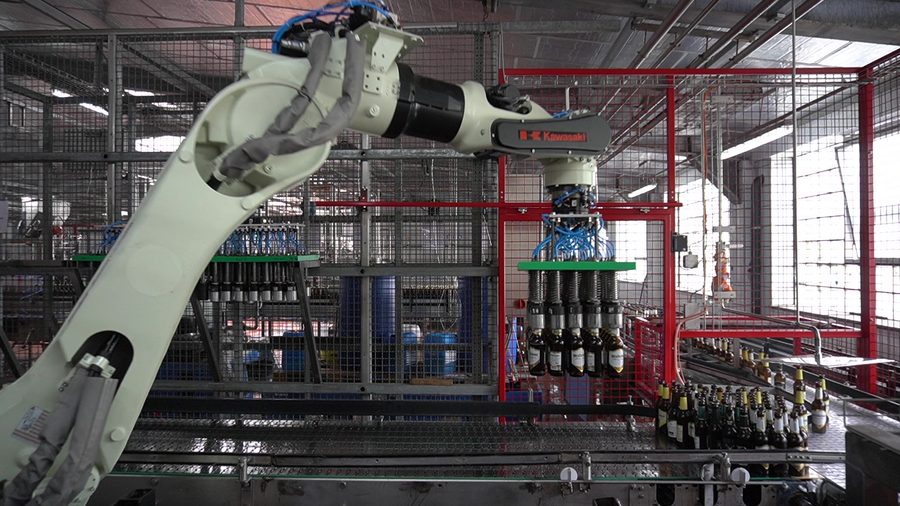
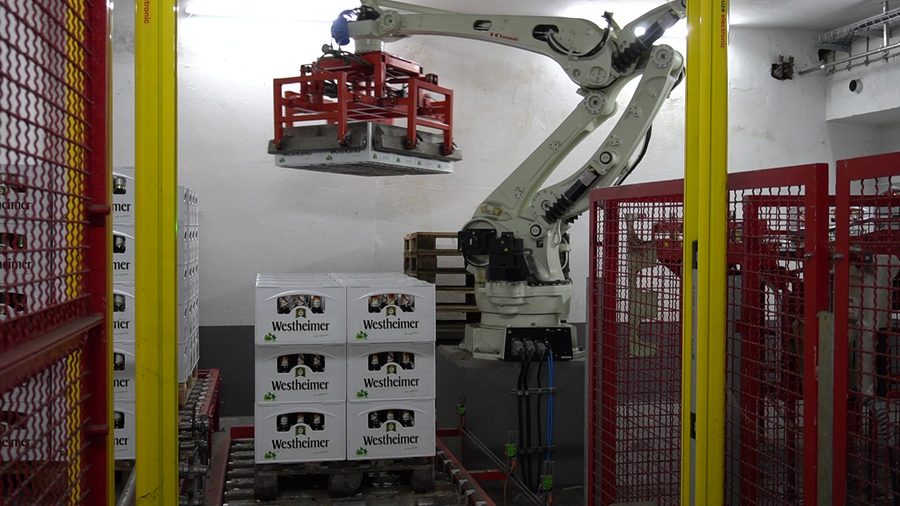
CHALLENGES
Retaining skilled workers
In-house training and retaining skilled workers has played a large role in Westheimer Brewery’s continued success, explains master brewer Jörg Tolzmann: “Long-term retention of good skilled workers is crucial, because the shortage is clearly noticeable in the brewery and the craft sector, especially in rural regions like the Sauerland (where the brewery is located).” As in almost all industries there is fluctuation, and retaining experienced employees is particularly important as new employees are increasingly difficult to recruit. The new system makes their employees’ daily tasks easier, thus making it easier to retain their workforce.
An evolving brewery market
The brewery market has changed massively in recent years, and being able to provide one product type is not enough to meet market demand. The new robot-assisted production provides the flexibility Westheimer needed to meet customer requests. “It used to be one type of beer in small and large bottles. Today, we have several private labels, lemonade and other beverages, and produce for other companies. In short, there is an incredible variety. Our team and production facilities are being challenged much more than before,” says Tolzmann.
Pandemic pivot
By automating their line, Westheimer met the high demand for more bottled beer and greater product variety – including non-alcoholic beverages – that arose during the COVID-19 pandemic. Now that bottle production has been fully and successfully automated, the brewery can shift their focus to expanding their keg and cask production line.
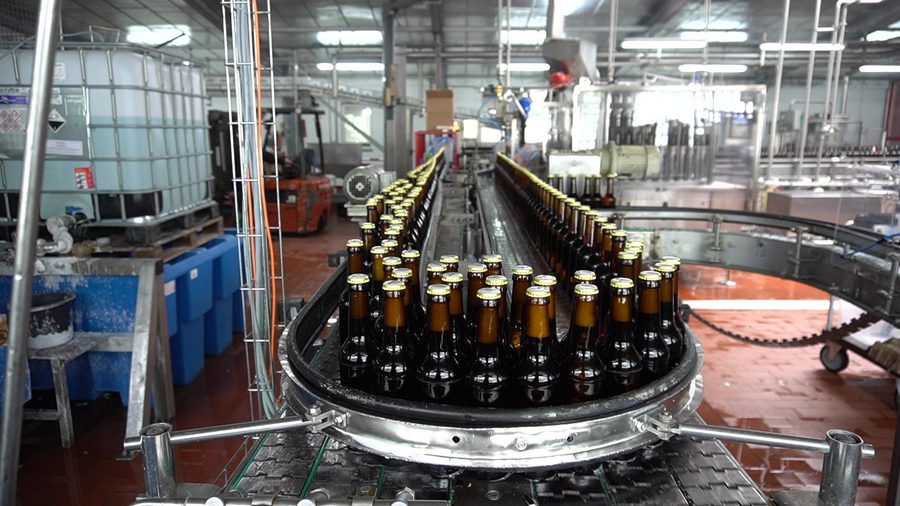
SOLUTION
- Kawasaki CP500L first installed to replace outdated palletizing machinery
- Two BX200L robots added in second phase of automation to load an unload bottles into crates
Westheimer’s production takes place on two linked levels – handling empty bottles and end products below and filling above. The crates with empty bottles are fed from the first floor to the bottle line via a conveyor system. There, a BX200L robot removes the bottles from the crates with a gripper and places them on a conveyor. A waiting crate washer cleans the crates and feeds them to the packer. The empty bottles are transferred to the bottle washer via a feeder. There, the bottles are first checked for damage, incorrect shapes, and similar factors, and then intensively cleaned. After cleaning, the bottles are additionally checked by an inspector. Only the bottles in perfect condition move on. They are then filled, checked again, labeled, and packed into the crates provided by the packer – another BX200L. By switching to double crates, the speed of the packer has increased.
The filled and ready-to-sell crates are then fed via the conveyor system to the palletizer to process for distribution. Integrating the new robots was a straightforward task. Because all relevant machines basically remained in the same place and the new robots have such a small footprint, only safety fences and new belt settings were necessary.
RESULTS
Above all, the significantly reduced running costs – especially compared to older machines – have provided a tangible advantage for the Westheimer brewery after only a short time. Now that they complete automated their bottle production line, they’re looking to further automate their keg and cask production line in the future. Westheimer employees approved of the new robots, seeing them as a great relief, according to Tolzmann. “In the past, you had to get bottles out manually, check them, move pallets here, etc. The robots are a tremendous relief… physically above all.”