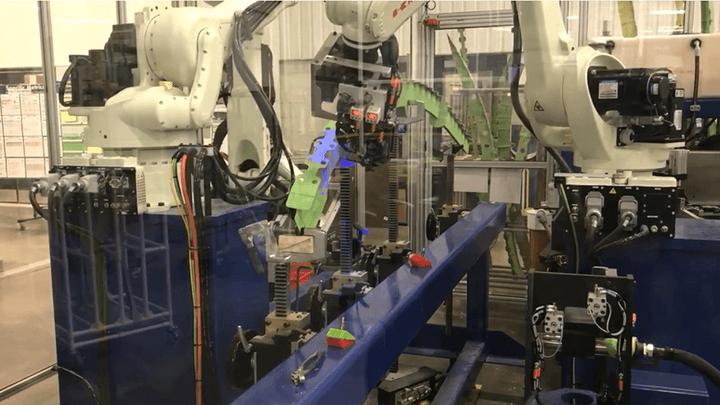
- IndustriesAerospace
- ApplicationsSealing / Dispensing
- Robot SeriesR series
System designed by:
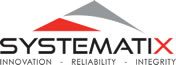
OVERVIEW
Unlike many of today’s manufacturing sectors, aerospace tends to stay away from automation. Robotic arms are a rare sight in this industry due to low production volumes and highly specialized parts. Despite this, aerospace part supplier teamed up with Ontario-based integrator SYSTEMATIX to design a complex robotic vision-guided assembly cell for nutplate installation.
Nutplates are an irregular part with over 200 variations used to hold the external skin of the aircraft to the frame. Although this complex application doesn’t necessarily sound like an ideal candidate for automation, SYSTEMATIX thought differently. Repeatable Kawasaki robots and 3D vision-guided assembly products cut down cycle times, increased product consistency, and decreased manpower.
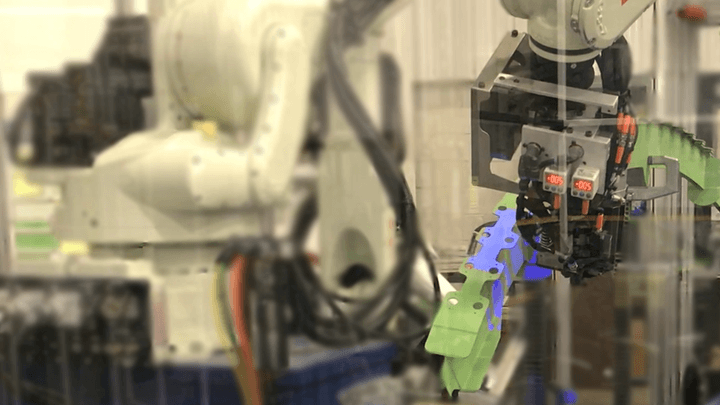
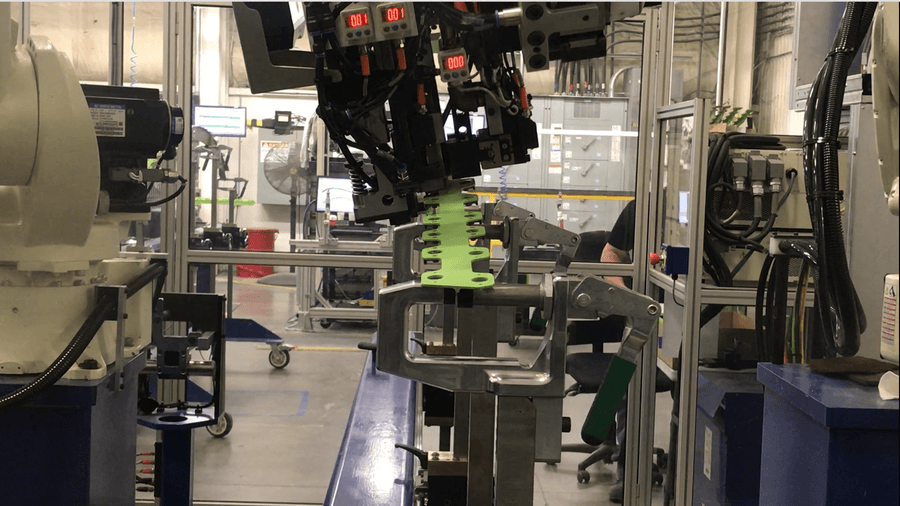
CHALLENGES
Tough and tedious application
There were multiple reasons why the customer chose the nutplate installation process for automation. In order to meet strict quality requirements, all employees had to undergo intensive training and certification for each part. They also had to document their work in real time. This combined with the monotonous nature of the nutplate installation process created retention issues for the manufacturer.
Quality control
Because of the integral role the nutplate plays in aircraft construction, nutplate rivet heights need to be exact. Prior to automation, human operators had to shave the rivets to the exact height needed – a tedious and time-sensitive process.
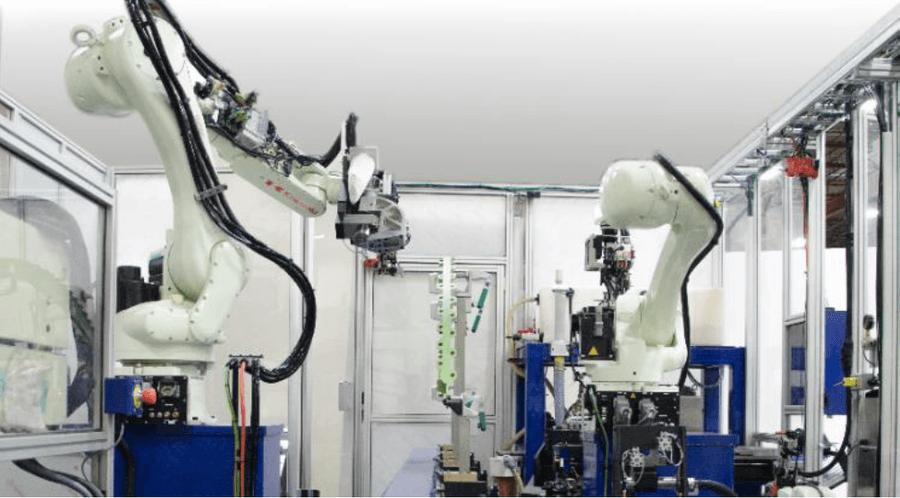
SOLUTIONS
- Three different Kawasaki R series robot models installed for vision-guided assembly cell
- Matrox imaging software and LMI locators correctly identify 225 part types
The process
First, a Kawasaki RS080N determines part position by scanning three distinctive part features using 3D vision and adjusting accordingly. After alignment, the robot’s drill head end-of-arm tool (EOAT) grips the part, drills, and countersinks two rivet holes for nutplate installation.
Next, the RS080N rotates the arm to retrieve the correct rivets out of four possible lengths, and at one of two specific pitches, from the rivet slide tooling. While the RS080N is retrieving the rivets, the RS010L robot picks up a nutplate and uses vision cameras to verify that it is correct out of 28 possible types. From here, the robot places the rivet on the nutplate locating tool. Cameras perform a vision check before placing the nutplate on the tooling to ensure it is clear to receive a new nutplate.
The robot then places the nutplate on a turntable so the RS005N robot can apply sealant – a customer requirement to ensure corrosion resistance. The RS005N robot conducts two vision checks at this point in the process: one before sealant application and another afterward to ensure proper application.
From here, the turntable rotates so the RS010L can pick up the complete tooling package, which includes the nutplate and nutplate-locating tool. The RS010L robot scans three part features to ensure proper plane alignment for installation. Next, it grips the part at the defined feature. While the RS010L robot holds the part in place, the RS080N robot enters the area and the two heads marry. Next, the RS080N robot’s rivet vacuum head places rivets inside the head of the RS010L robot, which installs the rivets into the part.
After rivet installation the robot heads separate. The RS010L safely releases the part and rotates to drop off the dirty tooling, and the RS080N rotates the EOAT to the correct position for rivet crimping, which completes the 39-second process.
Vision, Precision & Speed
Throughout this complex process, you likely noticed a common theme: the importance of 3D vision. Matrox imaging software and LMI locators play a vital role in identifying 225 part styles and 28 different possible nutplate configurations – all of which can be installed at two different pitches.
The supplier chose Kawasaki robots because of the open architecture programming language and ability to handle more advanced processes. “I’ve touched almost every robotic arm out there… One reason I like Kawasaki is the ease of working with the programs, especially the AS Language,” project leader P.J. said. “It’s one of the driving forces why we use Kawasaki.”
One of unique aspects of this application is how closely the robots work together. The heads of the RS080N and the RS010L have to connect without colliding – an action that’s impossible without highly repeatable robots. Kawasaki’s R series of general purpose robots fit this criteria, with repeatability ranging from ±0.02 mm to ±0.06 mm as payload increases (3 kg to 80 kg). “The arms are very robust; they don’t wander,” P.J. said. “The arms have to go to some very exact positioning, and we’ve not had a single issue with that. They’re very precise.”
RESULTS
- Cycle time reduced by 26 seconds
- 97% consistency achieved
- Number of operators reduced from three to one
- Cell creates fully completed part – no work-in-progress stations needed
Since installation, the supplier has experienced the benefits of automation firsthand. Some of the benefits include drastically shortened cycle times, increased product consistency, and reduced manpower helped them reach the cost reduction and increased production goals they set from the beginning.
But when asked where they’ve seen the biggest improvement, P.J. cited consistency without hesitation. After being in production for just over one year, the cell has virtually eliminated part inconsistencies. They have achieved 97% consistency – a statistic that greatly affects their bottom line through both cost and time savings.