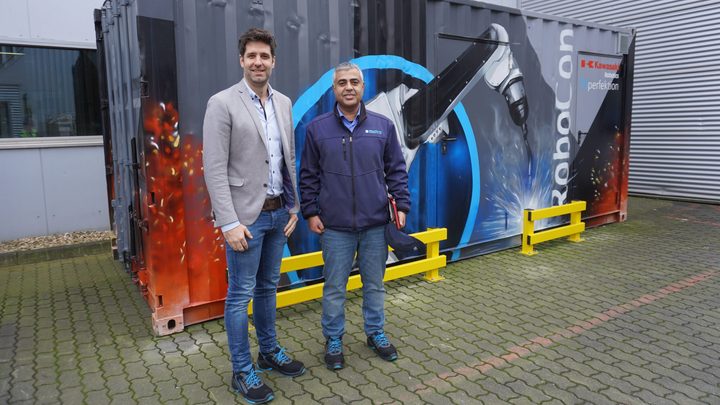
- IndustriesMachinery & Metal Manufacturing
- ApplicationsMaterial Handling, Machine Tending, Arc Welding
- Robot SeriesRS series, BA series, M series
From a compact welding system inside of a shipping container to 1.5-ton heavy-duty robots: The world market leader for filter systems relies on Kawasaki Robotics for its automation strategy
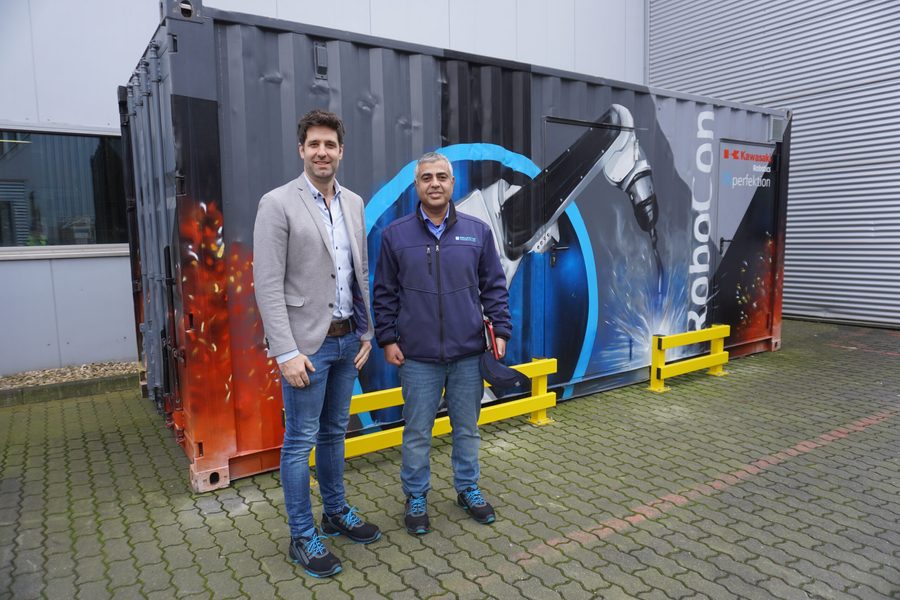
Overview
Since the company was founded in 1950, BOLL & KIRCH has developed into the global market leader for filtration technologies. Today, more than 900 employees work on modern, sustainable and customized filter solutions for international customers from a variety of industries. In addition to technology and network, their employees are the key to success, says Jan Willkomm, Technology Manager at BOLL & KIRCH: “From our engineering teams for development and testing to our welding experts in production: The many years of experience, close cooperation and individual commitment of our employees enable us to meet complex and new customer requirements time and time again.”
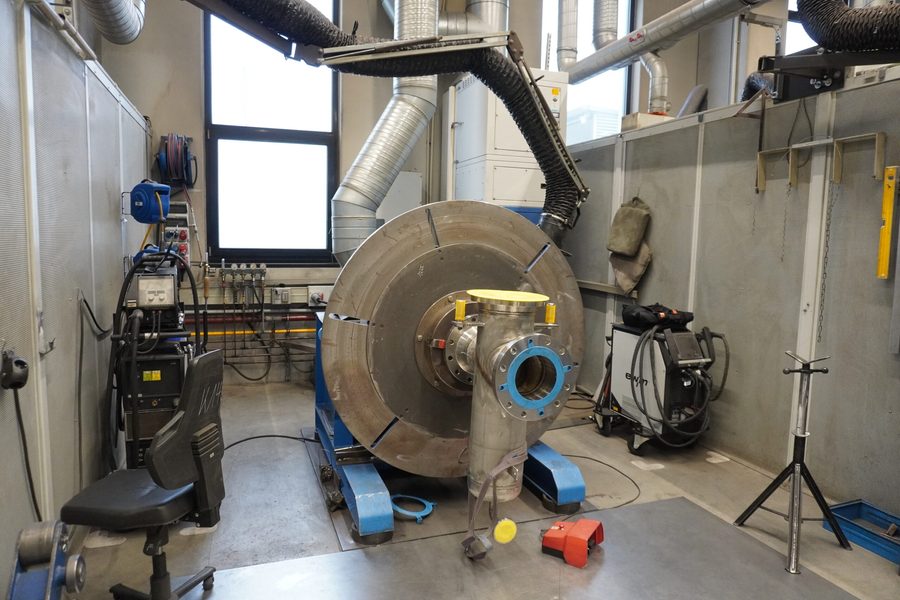
In order to not only support the company’s continued growth, but also to contribute to clean water, optimized air quality and conservation of resources with sustainable solutions, the focus is on continuous development: Research and development focuses on improving filtration efficiency, reducing energy consumption and developing new materials or technologies in order to remain competitive on the market. More than 25 percent of the filter solutions are exported to Japan – Kawasaki Heavy Industries, for example, has been an important customer of BOLL & KIRCH for decades. The filter solutions are used in many areas of the Japanese conglomerate, including in shipbuilding and in the production of their renowned high-performance motorcycles such as the Ninja.
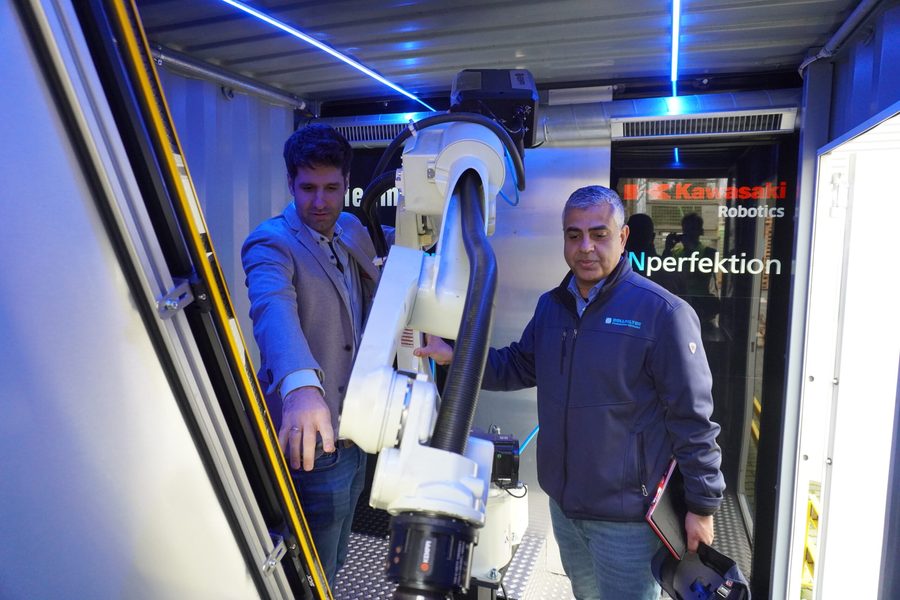
The Journey Begins: Out of the Box Automation
In this context, the topic of automation using industrial robots is becoming increasingly important, explains Dr. Basel Keita, Director Quality Management at BOLL & KIRCH: “We have been using older industrial robots to weld filter components for some time now – but they are clearly getting on in years and are no longer sufficient for our growing requirements.” During a visit to the “Schweißen & Schneiden” welding trade fair in Essen (Germany) in 2023, Jan Willkomm and Basel Keita saw the automation solutions from Kawasaki Robotics for themselves and spoke to Kawasaki robot experts and system partners on site.
One solution impressed the Boll & Kirch team so quickly that they purchased it directly at the trade fair: Robocon is a fully functional robotic welding cell based on the Kawasaki Robotics BA006L, which can be placed wherever it is needed. All that is needed is a power connection and the cell, which is integrated into a recycled shipping container, can be put into operation. Supported by industry experts such as Kemppi, Siegmund and Nederman, the unusual project was launched by Kawasaki Robotics and the system house INperfektion. Robocon was specially developed for the low-threshold automation of welding processes in small and medium-sized companies – intuitive to operate even without programming knowledge via manual guidance and with a fast ROI.
“Robocon immediately caught our attention as an unusual solution and after discussions with Kawasaki and INperfektion, we were convinced. The cell is already the ideal introduction to modern robotics for us in element production and other welding processes. The K-DIY manual control enables us to transfer the valuable know-how of our welders 1:1 to automation,” says Jan Willkomm. Offline programming and simulation of workpieces with the Kawasaki tool K-Virtual, based on proven CENIT technology, is the next step and the first employee training courses are already underway.
Requirements for Automation
While Robocon provided the perfect introduction to a new automation phase, the next steps were planned together with Kawasaki Robotics and partners. It quickly became clear that Boll & Kirch was focusing on three aspects when it came to automation:
Quality Assurance: Since 1950, the name Boll & Kirch has been synonymous with trust and quality. In addition to high-performance test equipment and a wide range of test procedures, the precise production of components guarantees maximum reliability. Modern robot solutions not only enable increased output, but also consistent quality at the highest level.
Agility: Boll & Kirch deliberately does not offer standard products. Each filter solution is precisely tailored and built to individual customer requirements. This customized configuration of components, materials and coatings is a key hallmark of the long-established company and requires a high degree of agility and flexibility in automation.
Shortage of Skilled Workers: The ongoing shortage of skilled workers is also noticeable at the main site in Kerpen near Cologne, although employee retention at Boll & Kirch is above average and is a focus for the company management. For this reason, the outsourcing of production capacities for welding is to be avoided as far as possible in the future. “Automation with Kawasaki robots allows us to deliver more output with the same team in the long term. Our team is our greatest strength and automated welding processes also require welding experts on site,” says Jan Willkomm.
Outlook: Tailor-made Automation for a Traditional Company
For some time now, the BOLL & KIRCH. team has been identifying elements of production where targeted automation will be essential in the coming years. After initial discussions with the Kawasaki Robotics experts and partners in September 2023, the plans quickly took shape and will be implemented step by step with a Kawasaki system partner as early as 2024. An older welding system is to be replaced by two Kawasaki robots from the BA series and RS series: While the RS series high-speed robot developed for handling tasks automatically feeds and positions components, the hollow-arm robot of the proven BA series welds the component quickly, precisely and safely. “This not only enables the highest quality, but also effectively saves a lot of time in view of the large number of individual parts and protects our employees,” explains Basel Keita.
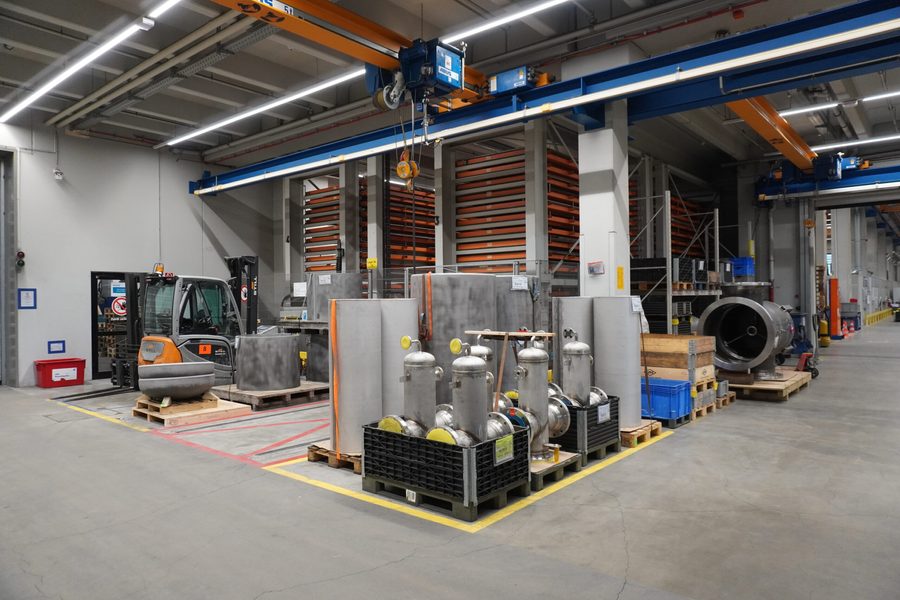
Further automation projects are already on the agenda for other joining processes too: Some products are currently joined by machine using a special adhesive. However, this process restricts the application temperature, is maintenance-intensive and makes it difficult to achieve consistent quality. The plan is to replace these products with two BA series welding robots in 2024. One highlight of the current automation phase at BOLL & KIRCH is the handling, assembly and production of the largest components and filter units: The Kawasaki Robotics MG15HL, by far the largest model in the Japanese manufacturer’s portfolio, will be used here. With a payload of up to 1.5 tons and industry-leading precision, the powerful heavy-duty robot was quickly chosen.
Alexander Ott, welding expert at Kawasaki Robotics, has been supporting customers from a wide range of industries and company sizes for years: “Long-term successful automation always requires a customized approach. The pace must be right and everything must be perfectly integrated into the existing structures. Automation at BOLL & KIRCH. therefore builds on our strengths – including the high level of quality assurance, individual solutions and the expertise of our employees.” Jan Willkomm is also certain: “It wasn’t just the technology from Kawasaki Robotics that convinced us from the outset, but in particular the open communication and advice. The resulting trust is the best possible basis for us to automate our production together and also to involve and convince all employees.”